Canvas printing on a wide-format printer represents a fusion of traditional artistry with modern digital technology, allowing photographers, artists, and designers to turn their digital creations into tangible works of art. This technology has democratized the art world, making it easier than ever to produce high-quality, large-scale prints that were once the province of professional print shops. As wide-format printers have become more accessible, artists and consumers alike can bring gallery-quality canvas prints into homes and businesses, showcasing stunning graphics and vibrant colors on an impressive scale.
The comprehensive process of canvas printing using a wide-format printer requires a meticulous approach, precision equipment, and an understanding of the artistic nuances that distinguish a good print from a great one. It begins with the preparation of a digital image, ensuring it has been properly edited and formatted to achieve optimal results on canvas. The printing process itself involves the use of specialized inks and a carefully selected canvas medium that together deliver a print that is not only visually impactful but also durable.
Advancements in printing technology have introduced a variety of wide-format printers, each with their unique capabilities and ink systems, such as aqueous, solvent, UV, and latex, that cater to different needs and purposes. Understanding these technologies and how they interact with different canvas materials is crucial for obtaining the desired finish, texture, and longevity of the print. Once the print is complete, additional steps such as drying, stretching, and mounting are essential to transform the freshly printed canvas into a display-ready masterpiece.
This article will delve into the detailed process involved in canvas printing with wide-format printers, from image preparation to the final touches that ready a print for exhibition, discussing the technical considerations, creative decisions, and professional techniques that contribute to the creation of a stunning canvas print. Whether for personal enjoyment, professional display, or commercial sale, mastering the art of wide-format canvas printing can unlock a world of creative potential.
Preparing the Digital Image
Preparing the digital image is a crucial first step in the process of canvas printing on a wide-format printer. The quality of the printed canvas is directly influenced by the resolution, color accuracy, and detail present in the digital image. Therefore, it is important to start with a high-resolution image, as this will ensure that the end result is sharp and clear, even when printed at a large size.
The procedure generally begins with selecting an appropriate image. This image can either be a digital photograph, a scan of a painting or artwork, or a graphic design created in a software program. Once the image is chosen, it usually undergoes editing using image editing software, such as Adobe Photoshop. During this stage, artists or technicians can adjust various parameters such as contrast, brightness, saturation, and color balance to enhance the visual appeal of the image. Additionally, any unwanted elements or imperfections can be retouched or removed to achieve the desired quality.
Ensuring the correct aspect ratio and orientation of the image is also a part of the preparation process. The digital image is often cropped or resized to fit the dimensions of the desired canvas print without losing important details or distorting the original image. When resizing, it’s crucial to maintain a high dots per inch (DPI) or pixels per inch (PPI) setting to preserve the quality of the print; usually, a minimum of 300 DPI is recommended for high-quality prints.
Sharpening may be applied to the image to enhance edge definition and detail, but this should be done conservatively to prevent the introduction of unwanted artifacts. Moreover, images are typically converted into the correct color mode—usually CMYK (Cyan, Magenta, Yellow, and Key [Black]) for printing purposes—and the correct color profile that matches the printer’s specifications is applied to ensure color accuracy during the printing process.
Once the digital image is fully prepared and optimized, it must be saved in a print-ready format, such as TIFF or PDF, to ensure that all edits are preserved and that there’s no loss in quality during the transfer of the image to the printing system.
The process of canvas printing on a wide-format printer can generally be explained as follows:
First, the chosen canvas material is loaded into the printer. Wide format printers can handle large rolls of canvas and allow for printing of high-quality, large-scale images. Before printing, the wide-format printer must be calibrated for color accuracy to ensure that the colors on the canvas match the original digital image as closely as possible. Color calibration involves adjusting the printer settings and using color profiles that take into account the type of canvas and inks being used.
Once calibrated, the printer applies ink to the canvas using one of various printing techniques. Inkjet printing is a common method, where microscopic droplets of ink are sprayed onto the canvas surface to recreate the image’s details and colors. The inks used in wide-format printers are typically aqueous (water-based), solvent, latex, or UV-curable, each with its own properties and advantages for durability and color fidelity.
After the image is printed, the canvas may need to dry or cure, depending on the type of ink used. The final step involves finishing touches, such as applying a protective coat to resist moisture and UV damage, and stretching the canvas onto a frame if necessary for display.
Canvas printing on a wide-format printer enables artists, photographers, and businesses to produce gallery-quality prints suitable for a wide range of applications, including fine art reproductions, interior design, and commercial signage.
Choosing the Right Canvas Material
Choosing the right canvas material is a pivotal step in the process of canvas printing, especially when dealing with wide format printers. The canvas material, often referred to as the substrate, can significantly influence the appearance, durability, and overall quality of the final print.
There are several types of canvas materials available, each with its own set of characteristics. Cotton canvases, for instance, are favored for their traditional look and feel, and they are capable of rendering a high level of detail, making them ideal for fine art reproductions. Cotton canvases are known for their ability to absorb inks deeply, which contributes to rich, vibrant color reproductions.
Alternatively, polyester canvases may be chosen for their strength and resistance to environmental factors such as moisture and sunlight. Polyester canvases often provide a bright white point that serves to enhance the vibrancy and dynamic range of the print. Additionally, they tend to be more affordable than their cotton counterparts, making them a cost-effective option for high-volume or commercial applications.
Recently, there has been an upsurge in the use of poly-cotton blends, which aim to combine the best attributes of both materials. These blends offer the durability and consistency of polyester while maintaining a part of the texture aesthetic associated with cotton.
When using a wide format printer, it’s essential to pick a canvas that is compatible with the inks and printer technology to ensure reliable adhesion and ink coverage without bleeding or smudging. Printers are often intended to work with specific materials, and their settings can be adjusted to match the thickness, absorbency, and texture of the canvas. Not paying enough attention to this match-up can lead to disappointing print results.
Wide format canvas printing is a process that begins with the printer interpreting the digital image file, which is formatted for printing using specific color profiles. As the printing begins, microdroplets of ink are sprayed onto the surface of the canvas material by the printer’s printhead. The actual technique may vary, with some printers using dye-based inks for their wide color gamut and others using pigment-based inks for enhanced archival properties and UV resistance.
The ink must then dry and subsequently cure so that it is set into the fibers of the canvas material. Depending on the printer, drying systems such as heaters may be used to accelerate this process. High-resolution print heads enable intricate details to be reproduced on a larger scale, maintaining image clarity even on expansive canvas sizes typical for wide format printing.
After printing, the canvas needs to be trimmed to size if it wasn’t pre-cut and may be treated with a protective coating to extend its longevity and protect against UV light, moisture, and scratches. The final step is the finishing process where the canvas is stretched over a wooden frame, gallery-wrapped, or mounted as desired. Each of these steps is critical in ensuring the final piece of art or photographic work is presented with maximum impact and enduring quality.
Calibration and Color Management
Calibration and color management are essential components in the canvas printing process, particularly when using wide-format printers. The goal of calibration is to ensure consistent and accurate color reproduction across different devices – such as scanners, monitors, and printers – so that the final print accurately reflects the original digital image. This process involves adjusting the printer settings so that they align with a recognized standard. This way, the printer’s output can be predicted and matched to the on-screen image.
Color management, on the other hand, involves a series of controlled processes to maintain color consistency and fidelity throughout the workflow. It often begins in the photo editing phase, continues through the software used to process the print job, and is maintained in the printer’s settings and its management of ink distribution onto the canvas. A color-managed workflow utilizes color profiles, which are mathematical models that describe the color attributes of a particular device or viewing condition. These are usually in the form of International Color Consortium (ICC) profiles. By using ICC profiles, the colors in the digital image file are interpreted consistently across different devices.
In the context of wide-format canvas printing, the printer must be periodically calibrated, and its color profiles updated to account for ink density, color range (gamut), and the specific type of canvas material being used, as all these factors affect the appearance of printed colors. Printers come with software that can assist in the calibration process and profile creation, often through the use of a spectrophotometer, which measures the printed colors and compares them to the intended colors.
Efficient calibration and color management are vital because the texture and color of the canvas material can influence how colors print and are perceived. Higher-quality materials and inks will generally provide a wider color gamut and better fidelity, but without proper calibration and color management, the results can still be unpredictable.
Through diligent application of these processes, printmakers can achieve prints that are both vibrant and faithful to the original artwork or photograph. This is crucial for artists and photographers who sell their prints, as well as for customers who expect the colors of their purchased canvas to match what they saw on their computer screen or in a gallery.
Printing Technology and Ink Types
The fourth item on the numbered list, “Printing Technology and Ink Types,” plays a crucial role in the canvas printing process, particularly when using a wide format printer. The printing technology employed in wide format printers is typically either inkjet or dye-sublimation. Inkjet printers are the most common for canvas printing and work by spraying tiny droplets of ink onto the canvas surface. This technology has evolved significantly over the years and can now produce high-quality, detailed prints that can last for many years, especially when using pigment-based inks.
Pigment-based inks are preferred for canvas printing due to their excellent color performance and durability. These inks contain fine particles of colored pigment suspended in a liquid carrier. When they are applied to the canvas, the carrier liquid evaporates, leaving the color pigment fixed to the fibers of the canvas. This results in prints with exceptional color vibrancy and fade resistance, making them suitable for fine art reproductions and long-lasting displays.
Dye-sublimation printing is another technique, although less common for canvas. It involves transferring dye onto the canvas using heat. This type of printing is not typically used for traditional canvas materials; however, it can be employed for printing on polyester canvases and is renowned for its color saturation and smooth gradations.
The process of canvas printing on a wide format printer begins once the digital image has been properly prepared, the right canvas material has been selected, and the color management is calibrated. The prepared image file is sent to the printer, where it begins its transformation into a physical work of art. The wide format printer will interpret the digital file using a RIP (Raster Image Processor) software to efficiently manage color output and layering of the ink.
The canvas, which is usually in roll form, is fed into the printer, where it passes under the print heads. The heads move back and forth with extreme precision, depositing inks onto the surface. Modern printers are capable of using multiple shades of each color to produce a rich and accurate representation of the original image. They can print on larger canvases, which allows for producing artwork on a grand scale suitable for galleries or large interior spaces.
After printing, the canvas must be left to dry sufficiently. In the case of pigment inks, this may also involve a curing period during which the ink undergoes a chemical reaction to bond firmly to the canvas material. This step is crucial for the durability and longevity of the canvas print, ensuring that it remains resistant to environmental factors such as moisture and UV light.
Overall, the technology and types of inks used are essential components of canvas printing. They determine not only how the final print will look but also its archival quality and suitability for different displays or purposes.
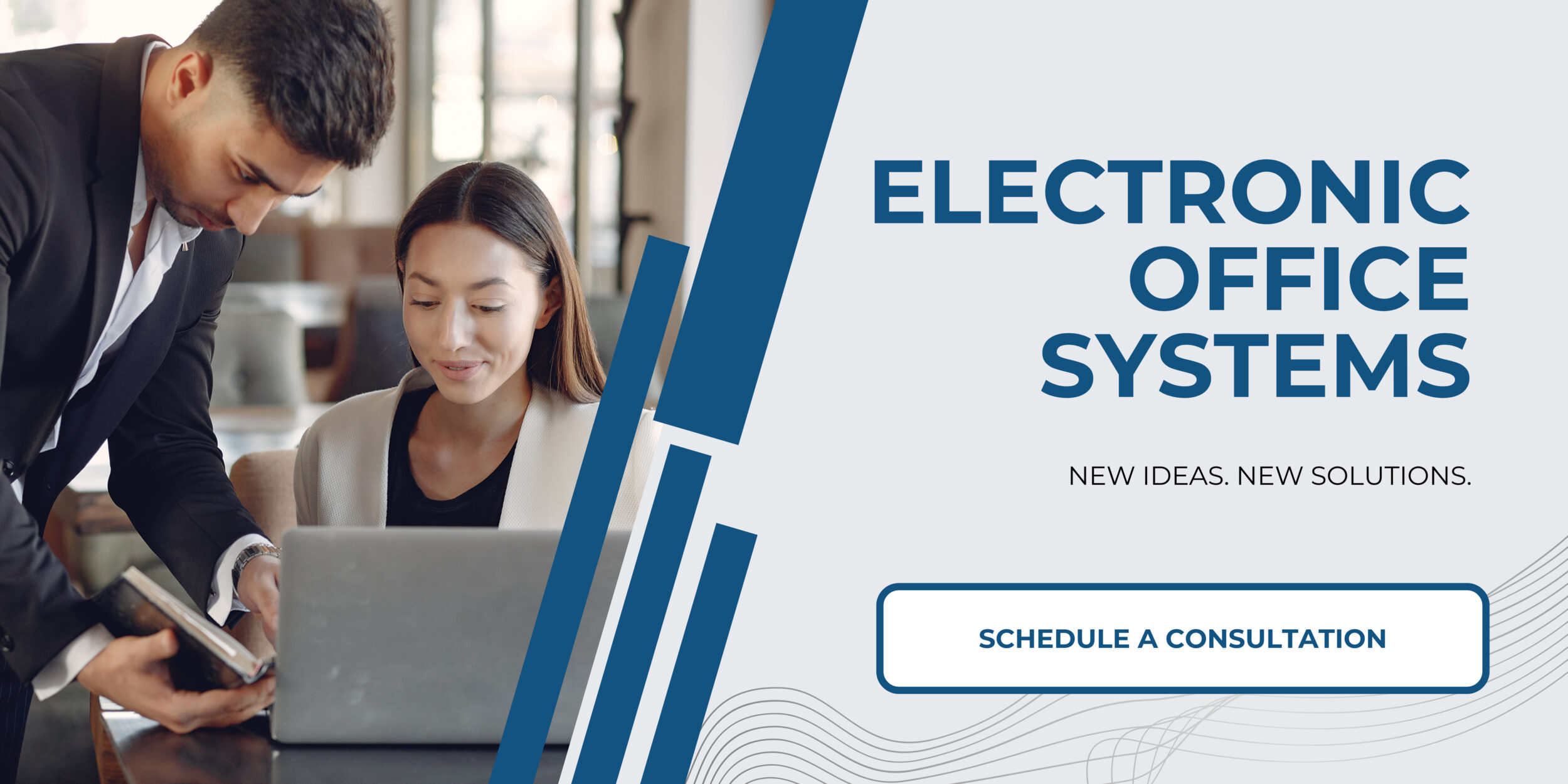
Finishing and Stretching the Canvas
Once the canvas has been printed, the next significant step in the production process is finishing and stretching the canvas. Finishing refers to the various treatments applied to the printed surface of the canvas to protect it, enhance its appearance, and prepare it for stretching or mounting. Stretching is the process of securing the finished canvas to a frame, also known as a stretcher bar, to give it the traditional canvas art look and make it ready for display.
In the finishing phase, a clear protective coating might be applied to the canvas. This coating serves multiple functions: it can protect against UV light, reduce fading, provide a water-resistant layer, and help prevent scratches and other physical damage. The finish can be matte, satin, or glossy, depending on the desired visual effect and the application of the piece. After the coating dries, the canvas is inspected for any imperfections before proceeding to the next step.
Stretching the canvas is a craft that requires precision and care. The canvas must be pulled taut and evenly over a wooden frame, usually made from stretcher bars, ensuring that the image is aligned correctly and that no distortion occurs. The canvas is attached to the stretcher bars using staples or tacks and is often folded neatly at the corners for a professional look. Gallery wrapping is a popular method where the image extends around the edges of the frame, allowing for a frameless presentation when hung.
For fine art reproductions or high-end displays, additional touches like a bracing system might be added to the back of the stretcher frame to provide extra support and prevent warping over time. Some stretched canvases may also be further framed with decorative moldings, similar to traditional paintings.
Now let’s discuss what the process of canvas printing on a wide format printer entails:
The process starts with preparing the digital image to ensure it is of high resolution and color-corrected for print. Once the image is ready, the appropriate canvas material is selected based on texture, weight, and finish preference. A wide format printer is calibrated for color accuracy and loaded with the selected ink type, be it dye-based, pigment-based, or UV-curable inks, which each have their own benefits and uses.
Printing on a wide format printer involves feeding the roll of canvas material into the machine. The printer then sprays the ink onto the canvas surface in a series of passes, building up the image layer by layer. Precision is vital, as the printer’s head movement and ink application must be meticulously controlled to ensure a high-quality print without banding or other artifacts.
Once the printing is complete and the ink is dry, the canvas may be trimmed to size and then undergoes the finishing and stretching processes as described above, culminating in a piece of art ready for wall mounting or display in a gallery or home setting. The combination of modern printing technology and traditional finishing techniques allows for the production of high-quality canvas prints that can replicate the look and feel of original works of art.