Contour cutting is a pivotal process in the wide-format printing industry that takes the capabilities of printed graphics beyond the standard sheets or rolls of material. When it comes to personalization and crafting intricate designs, contour cutting stands out as the technique that enables businesses and hobbyists alike to push the envelope of creativity. In essence, contour cutting refers to the process of cutting along the edge of an image with precision, thereby creating customized shapes and designs that fit exact specifications. This innovative procedure bridges the gap between digital printing and precise physical cuts, offering limitless possibilities for stickers, decals, custom signage, vehicle wraps, and much more.
The process utilizes advanced digital cutting machines that align themselves with printed graphics through various detection methods such as optical eyes or alignment marks known as registration marks. Once the print job is complete, these machines read the marks or detect the edges of the graphic to determine the exact path for the blade to follow. The precision of contour cutting means that even the most complex of shapes can be accurately trimmed, lending a professional finish to the final product.
Contour cutting is not solely about cutting out shapes, but also about enhancing the functionality and aesthetic appeal of the prints. The ability to create custom die-cuts transforms ordinary printed materials into dynamic marketing tools that can catch the eye and engage potential customers. Whether used for promotional materials, instructional signage, or decorative pieces, the technique adds a layer of sophistication and bespoke quality unattainable with standard cutting methods.
In this introduction, we will delve into the intricacies of contour cutting within the wide-format printing realm, discuss its technical aspects, and explore the various applications that benefit from this technology. We will also examine the implications of contour cutting on the production workflow and highlight how it fosters innovation in the field of wide-format graphics. Join us as we uncover the multifaceted world of contour cutting and its role in elevating printed materials to new heights of customizability and impact.
Definition and Process of Contour Cutting
Contour cutting refers to the method in printing and sign-making industries where a machine cuts around the edges of a printed image. This technique allows for the creation of stickers, decals, or any graphic with a custom shape, rather than being limited to simple geometric shapes like squares or rectangles.
The process of contour cutting begins with the design phase. The desired graphic is created in a vector-based graphic design software, which is often equipped with specific tools for outlining the precise cut lines that will define the graphic’s borders. These cut lines, often called “cut contours,” “cut paths,” or “vector paths,” act as guides for the cutting machine.
Once the graphic has been printed onto a suitable material, such as vinyl, the printed substrate is fed into a contour cutter. This machine utilizes a small blade to follow the vector paths created earlier, precisely cutting around the printed graphic. Modern contour cutting equipment can automatically align the cutting to the printed image using various methods, like reading registration marks that are printed along with the design. These marks are essential for ensuring the cuts align perfectly with the printed image, even if the material has shifted or stretched slightly during the printing process.
This technique is especially popular in wide format printing, where large graphics are produced for signs, vehicle wraps, window graphics, and other applications where custom shapes and precise cutting add a professional touch to the end product. Contour cutting enables the production of sophisticated, eye-catching designs that can be applied effortlessly to various surfaces, giving businesses and individuals a higher level of customization and branding opportunities.
In wide format printing, contour cutting has revolutionized how vinyl graphics are created. The ability to precisely trim around complex shapes means that installers no longer need to hand-trim with scissors or utility knives, reducing labor time and the potential for human error. This precision-cutting technique makes it possible to produce large quantities of consistent, accurately cut graphics, which is crucial for maintaining brand consistency and image quality across various applications.
Equipment and Technology Required for Contour Cutting
Contour cutting refers to the process of cutting around the edges of a printed image following its specific shape and contours. To achieve precision contour cuts in wide format printing, specific equipment and advanced technology are required. Let’s delve into the equipment and technology integral to the process:
### Cutting Machines
The core equipment for contour cutting is a cutting plotter or cutter. These are specialized machines that can range from small desktop cutters suitable for small vinyl decals to large format cutting plotters capable of handling large printed graphics. The cutting plotter must have an accurate tracking mechanism to ensure that long print jobs are cut consistently and precisely along the desired path.
### Software
Software is essential for contour cutting because it controls the cutting plotter. It includes designing and cutting programs that allow for the creation of graphics, layout of cut lines, and sending the precise cutting instructions to the machine. The cutting software is often compatible with various file formats and allows for setting of the cutting speed, pressure, and blade depth.
### Registration Marks
The use of registration marks (also known as crop marks or alignment marks) is crucial in contour cutting. They are printed along with the design and serve as guides for the cutting machine to follow the contour accurately. After printing, the cutter reads these marks to align the cutting blade with the printed image.
### Optical Eye
The optical eye is a feature in advanced cutting plotters. It scans the registration marks to determine the cut line relative to the printed design. This automatic alignment is critical for achieving precision cutting, especially for complex shapes or when the material has shifted slightly during the printing or loading process.
### Print and Cut Devices
Some wide format systems integrate both printing and cutting capabilities in a single machine. These print and cut devices streamline the workflow by printing the image and then cutting it in one seamless operation, ensuring perfect registration between the print and cut.
### Material Handling
For wide format printing, material handling systems are vital to manage the larger and often more unwieldy materials. Roll feeders, vacuum hold-down systems, and flatbed cutters are examples of equipment designed to handle materials efficiently during the contour cutting process.
### Blades and Tools
Lastly, a range of blades and cutting tools are necessary for different materials and cuts. The choice of blade depends on the type of material (vinyl, film, paper, etc.), the thickness, and the complexity of the design. Some systems also offer additional tools for scoring or perforating, expanding the capabilities of what can be achieved with contour cutting.
In terms of contour cutting in relation to wide format printing, it is an invaluable technique that allows for custom-shaped decals, stickers, graphics, and signs. This process can elevate a simple print into a visually appealing and custom-shaped product that stands out from standard rectangular or square prints. The ability to accurately cut around complex shapes provides significant versatility in product offerings for businesses that utilize wide format printing.
Applications of Contour Cutting in Wide Format Printing
Contour cutting has grown to be an integral part of wide format printing, enabling a higher level of creativity and flexibility in the production of printed materials. This technique refers to the process of cutting along the edges of printed images, shapes, or designs that are not restricted to basic geometric patterns such as squares or circles. As such, this capability extends the potential applications of printed materials in numerous industries.
In the realm of advertising and marketing, contour cutting is used to produce customized stickers, decals, vinyl lettering, and signage that effortlessly conform to the branding requirements of businesses. These custom cut-outs can be applied on windows, walls, vehicles, and floors, offering a vibrant and engaging way to showcase logos, marketing messages, or decorative elements that capture the attention of potential customers.
Furthermore, contour cutting in wide format printing gives way to personalization and decoration in spaces like retail stores, restaurants, and event venues. It allows for the production of wall graphics and floor decals that fit specific areas, adhering to the dimensions and contours of the space. This customization makes it possible for businesses to immerse their clients in a particular theme or ambiance, enhancing their overall experience.
Within the packaging industry, contour cutting is also highly valuable. It allows for the creation of prototypes and short-run custom packaging that stand out on the shelves. This technology enables brands to swiftly bring to market products in unique shapes without the high costs and long lead times associated with traditional die-cutting processes.
In addition to these, wide format printing with contour cutting has a significant role in the textile and fashion industries. It is used to cut printed fabrics into intricate designs for apparel, accessories, or even upholstery, giving designers the freedom to execute their visions without the constraints imposed by standard cutting techniques.
Overall, contour cutting opens up a new dimension in the production of printed materials, as it allows for greater customization, detailed craftsmanship, and the ability to distinguish products and services in a competitive market.
Regarding your inquiry on “What is contour cutting in relation to wide format printing?”:
Contour cutting in the context of wide format printing is an advanced finishing technique used to cut printed materials into custom shapes and sizes. Rather than printing on predetermined cut blanks or using straight cuts that yield rectangular or square shapes, wide format printers equipped with contour cutting ability can produce an array of complex and non-standard shapes directly from a digital design file.
This process typically involves printing a design onto a large substrate—the ‘wide format’ part of the printing process—which can include materials such as vinyl, paper, cardboard, fabric, or other specialty media. Once printed, the same machine or a separate cutting device reads the contour lines or cut paths that have been defined in the design file. Guided by these paths, a blade or laser then precisely trims the printed material to the exact shape of the design.
Contour cutting technology often requires additional hardware, such as an optical eye or camera, to recognize registration marks printed along with the design. These marks help the equipment align the cut perfectly with the printed image, resulting in clean, accurate edges that follow the contours of the design without errors or misalignment. This technique is integral to producing stickers, custom-shaped labels, vehicle wraps, point-of-purchase displays, and other items where custom shapes are a critical aspect of the product’s design and functionality.
Advantages of Using Contour Cutting in Printing Projects
Contour cutting refers to the process in which a cutting machine, such as a plotter, is used to cut around the edges of printed graphics, stickers, labels, or decals, according to a predefined contour line. This technique is especially significant in the realm of wide format printing where it enables precise cutting of large printed materials. It’s an integral part of the production process that adds versatility and immense value to printing projects.
One of the primary advantages of using contour cutting in printing projects is the professional finish it provides. Contour cutting allows for a more refined product, where the labels or graphics can be cut to any shape or size, thus removing any excess background and creating a sleek, eye-catching presentation. This technique is crucial for creating custom-shaped stickers and decals that stand out, enhancing the visual appeal of the product or marketing material.
Moreover, contour cutting increases the flexibility of design options. Designers are not limited to standard shapes, like circles or squares; they can create intricate designs that can be cut accurately, enabling a new level of creativity and custom branding opportunities. This flexibility can be particularly advantageous for marketing materials, as unique shapes are more likely to capture the attention of potential customers and make the brand more memorable.
Another significant benefit of contour cutting is the efficiency it brings to the production process. With the aid of computer-controlled machines, the cutting is precise and consistent, reducing the likelihood of human error and the need for manual trimming. This automation speeds up the production time and ultimately leads to quicker turnaround times for completing projects, which is critical in meeting client deadlines and maintaining a competitive edge.
Additionally, contour cutting provides material optimization. By allowing for a tighter nesting of shapes within a printing sheet, it minimizes waste. This improved material use is not only cost-effective but also more environmentally friendly, as it reduces the amount of leftover material that would otherwise go unused.
Contour cutting also offers a competitive advantage by enabling small-run or one-off printing projects to be economically viable. Traditionally, creating custom shapes required expensive dies and tooling, which was only cost-effective in large runs. With contour cutting, each piece can be cut individually without the need for dedicated tools, making it a great option for custom projects or small quantities.
In conclusion, the adoption of contour cutting in printing projects brings about numerous benefits such as enhanced visual appeal, increased design versatility, precision and consistency, material optimization, and economic efficiency for custom and small-run projects. This modern technology continues to revolutionize the printing industry, offering customers and businesses alike the chance to produce highly customized printed products that effectively convey brand messages and stand out in the marketplace.
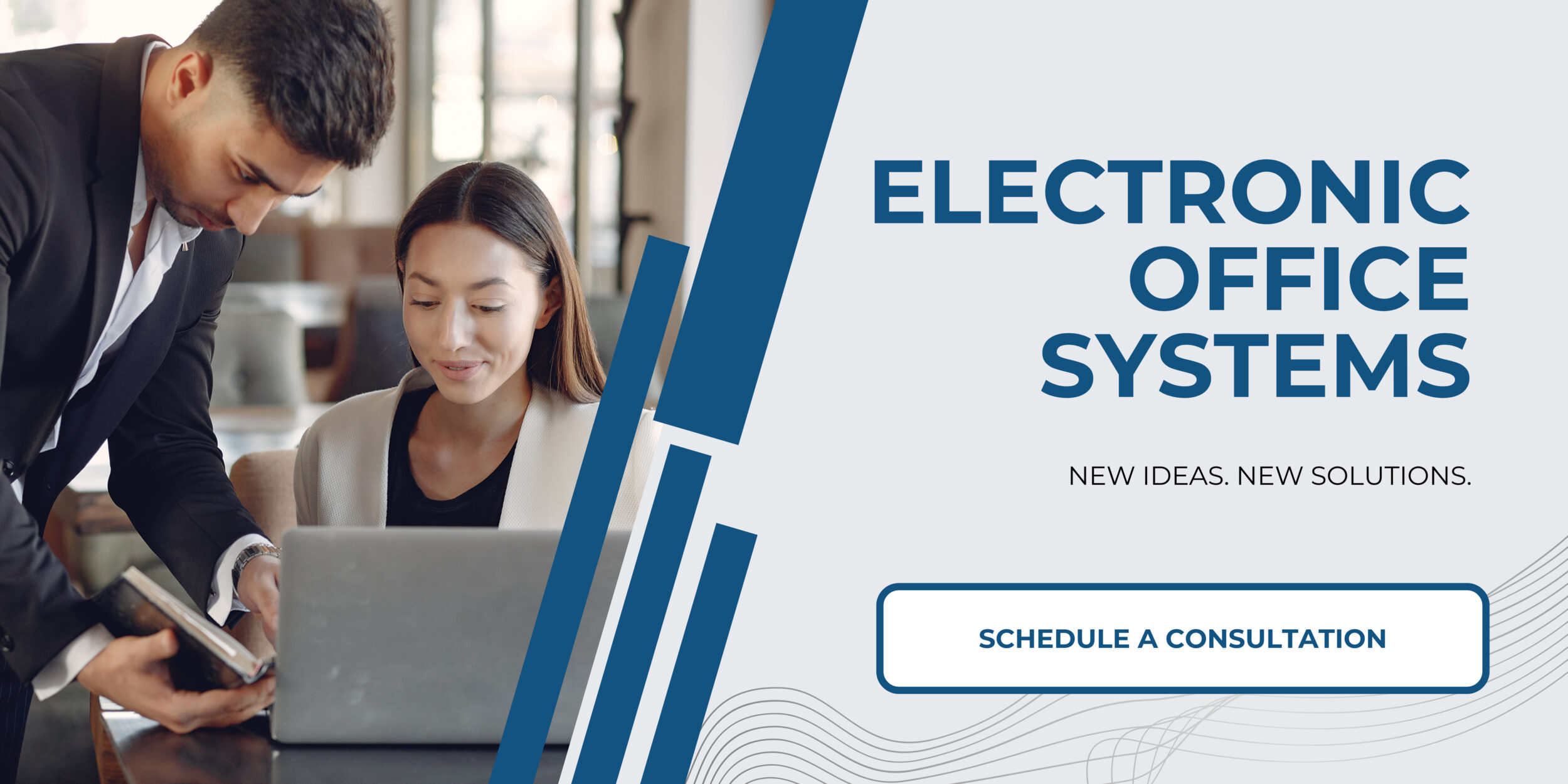
Challenges and Considerations in Contour Cutting
Contour cutting is a precision cutting method predominantly used in the wide format printing industry to cut prints into custom shapes and designs. This technique has become indispensable for creating high-quality, detailed graphics for a variety of applications such as stickers, custom labels, decals, and signs. While contour cutting offers numerous advantages including the ability to produce intricate custom shapes with ease, it also brings with it certain challenges and considerations that must be taken into account.
One major challenge of contour cutting is the need for accurate alignment. The cutting machine must align perfectly with the printed image to ensure the cuts are made at the correct locations. This often involves using optical sensors or cameras that can detect registration marks—small marks printed outside the main image area—to guide the cutter. If the system is not properly calibrated or if the registration marks are not accurately read, it can lead to misalignment, which may spoil the entire print.
Another consideration is the intricacy and complexity of the design being cut. Highly detailed designs with many sharp angles and curves require precise and smooth operation of the cutting tool to achieve the desired results. This puts pressure on the operator to correctly set up the cutter’s parameters such as blade force, speed, and cutting depth. Incorrect settings can lead to incomplete cuts, excessive wear on the cutting blade, or damage to the underlying material.
The type of material being cut also poses a challenge. Different materials, like vinyl, fabric, paper, or laminate, respond differently to the contour cutting process. Each material has its own specifications for optimum cutting, such as blade type, cut speed, and force. Materials may also stretch, distort, or fray if not properly handled during the cutting process. It is crucial to understand the properties of the material to avoid issues that could affect the quality of the final product.
Finally, maintaining the cutting equipment is important to ensure consistent quality. Regular servicing is necessary to keep the cutting blades sharp and the mechanical parts of the cutter in good working order. Wear and tear on these components can lead to inaccuracies in the cuts and overall lower quality in the finished product.
In summary, contour cutting is a technology that adds significant value to wide format printing by enabling custom cutouts and intricate designs. However, it requires careful attention to detail, understanding of materials, and proper equipment maintenance to overcome its challenges and ensure high-quality results.