Bi-directional printing stands as a pivotal technology in the realm of wide format printers, fundamentally impacting print quality, efficiency, and overall output. At its core, bi-directional printing refers to the ability of a printer to apply ink to the substrate in both the left-to-right and right-to-left directions as the print head moves across the material. This method contrasts with uni-directional printing, where the print head only deposits ink in a single direction, usually requiring a return to the starting position before laying down more ink.
The implications of bi-directional printing on print quality are multifaceted and deeply intertwined with the technical prowess of the wide format printer in use. It promises enhanced productivity by effectively halving the time taken for each print pass, which is particularly beneficial for large-scale outputs that are typical in wide format printing applications. However, the true impact on print quality is a matter of intricate calibration and precision engineering. This technique hinges on the precision alignment of the print heads and the synchronization of the ink droplets, both of which must be finely tuned to avoid any discrepancies in the pattern that can arise from the bidirectional movement.
Moreover, the influence of bi-directional printing on quality is also tied to the intricate dance between the print head technology (be it piezoelectric or thermal inkjet), the viscosity and formulation of the inks, and the characteristics of the substrate. Striking the right balance can lead to sharp, vivid, and consistent prints that rival or exceed unidirectional results. On the flip side, if the printer is not properly calibrated or if the substrates do not accommodate this back-and-forth motion well, the result can be ghosting, color misregistration, banding, or other print defects that detract from the final product’s aesthetic and professional appeal.
In the context of wide format printing, which often involves a vast array of applications including banners, posters, wall graphics, and more, maintaining impeccable print quality is paramount. The sheer size of the prints means that any imperfection is magnified, making the precise execution of bi-directional printing not just advantageous for productivity, but also a critical component for maintaining the integrity of the printed image or text.
This comprehensive article will delve into the technical aspects of bi-directional printing and its effects on print quality. We will explore how wide format printers leverage this technology, the challenges involved in its implementation, and the solutions adopted by manufacturers and operators to ensure that high-speed bi-directional printing does not compromise the caliber of the printed product. Whether you are a print professional, a vendor of wide-format equipment, or simply a curious enthusiast, understanding the dynamic between bi-directional printing and print quality is key to appreciating the complex art and science behind large-scale, high-impact visual communications.
Alignment and Registration Accuracy
Alignment and registration accuracy in printing refer to the precise placement of images or text on a printed page. This aspect is crucial for all types of printing but becomes even more important for wide format printers that often produce large graphics, signage, or banners where any misalignment can be easily noticed and may greatly affect the professional look of the final product.
For wide format printers, maintaining high alignment and registration accuracy involves several factors, including the precision of the printer’s mechanical system, the stability of the media on which printing is performed, and the performance of the printer’s software that controls the print head movements.
In a wide format printer, bi-directional printing can have implications on print quality, especially in terms of alignment and registration accuracy. Bi-directional printing is a technology that allows the print head to deliver ink on the substrate in both directions as it moves across the media, expecting to improve speed and efficiency. However, potential challenges may arise if the printer is not properly calibrated and the motion of the print head is not precisely controlled.
If a wide format printer is not well-calibrated for bi-directional printing, discrepancies can occur during the switch from one direction to another. These discrepancies can lead to slight misalignments of the print passes, producing visible banding or color misregistration in the final output. To minimize these effects on print quality, advanced printers use sophisticated algorithms to adjust the ink droplet placement with high precision, ensuring a seamless blend between passes.
Moreover, maintaining consistent tension on the media, accurate stepper motors, and high-resolution encoders also plays a vital role in achieving the desired alignment and registration. This is because the accurate advancement of the media after each print pass is crucial to maintain quality, particularly when the print head works in both directions.
In conclusion, while bi-directional printing offers the advantage of increased productivity for wide format printers, it requires a well-tuned system of hardware and software to maintain high print quality. Manufacturers often invest in developing printers that can handle the complexities of bi-directional printing without compromising on the critical aspect of alignment and registration accuracy.
Print Head Technology and Nozzle Configuration
Print head technology and nozzle configuration are critical aspects of any wide format printer as they directly influence the print quality, resolution, and the overall reliability of the printing process. The print head is the component of the printer that applies ink onto the substrate, and modern print heads typically use micro-electromechanical systems (MEMS) to precisely control the ejection of ink droplets.
Nozzle configuration refers to the arrangement and number of nozzles in the print head. The denser the nozzle configuration, the higher the potential resolution of the print, allowing for more detailed and sharper images. Nozzles are also designed to produce droplets of varying sizes, which can be essential for producing smooth gradations and color transitions in an image. Additionally, multiple nozzles are often assigned to each color in the ink system, which helps maintain consistent color density and uniformity across prints.
The technology behind the print head is also important – for instance, piezoelectric and thermal are two common types of inkjet print head technologies. Piezoelectric print heads use piezoelectric material, which changes shape when an electric current is applied, to force droplets out of the nozzle. On the other hand, thermal print heads use heat to create a bubble that ejects a droplet. Each technology has its own advantages and handling characteristics which can influence print quality.
Now, considering the impact of bi-directional printing on print quality: Bi-directional printing is when the print head deposits ink on the substrate in both the left-right and right-left directions as it moves across the media. This can significantly increase printing speed, as it allows the printer to lay down ink on every pass of the print head, effectively halving the time it takes to print. However, this speed comes with potential trade-offs in quality.
For bi-directional printing to not adversely affect print quality, the printer must have high precision in the movement of the print head and media. If there’s even a slight misalignment when the print direction changes, it could result in banding, where lines are visible on the print, or color misregistration, where colors don’t line up correctly. To mitigate these effects, wide format printers with bi-directional printing capabilities are typically equipped with sophisticated sensor technologies and firmware algorithms that can compensate for the minute shifts between passes, ensuring high-quality output that is consistent with what unidirectional printing would achieve.
These sophisticated systems must accurately align the droplets from line to line and pass to pass, regardless of the direction of the print head movement. Maintaining a high level of precision is therefore crucial, and the printer’s system must be calibrated correctly. Some high-end printers also allow fine adjustments to be made to the bi-directional printing settings so the operators can tweak the performance for optimal quality.
In conclusion, while bi-directional printing can potentially introduce quality issues due to misalignment and timing variances between passes, advanced print head technology, nozzle configurations, and precise printer control algorithms have gone a long way in minimizing these issues allowing printers to benefit from the speed advantages without significantly compromising on the quality.
Ink Distribution and Droplet Placement
Ink distribution and droplet placement play crucial roles in the overall print quality of a wide format printer. The precise distribution of ink and the accuracy of each droplet’s placement on the media determine the sharpness, color fidelity, and detail of the printed image or text. In wide format printing, where large-scale graphics and high-resolution images are common, even minute errors in droplet placement can lead to visible defects and quality degradation.
Ink distribution refers to how the printer manages and controls the flow of ink from the cartridges to the printhead nozzles. A consistent ink distribution ensures that the right amount of ink is available for each droplet that is ejected onto the substrate. The distribution system must be robust enough to maintain uniformity across all colors and shades, which is particularly challenging when working with large swathes of printed material that require consistent color across the entire print job.
Droplet placement is about the accuracy with which the printer can position each tiny droplet of ink onto the media. Modern wide format printers often use advanced technologies like variable droplet size, which can produce smaller droplets for fine detail and larger ones for filling in solid colors quickly. The precision in droplet placement is essential for delivering crisp edges, detailed graphics, and smooth color transitions.
Now, regarding how bi-directional printing affects print quality in a wide format printer, it’s essential to understand what bi-directional printing is. Bidirectional printing refers to the method where the print head deposits ink on the substrate in both directions as it moves across the media—on the pass from left to right and on the return from right to left. This method can substantially increase print speeds compared to unidirectional printing, where the print head only deposits ink in one direction and often stops briefly at the ends of each pass.
However, bidirectional printing can introduce alignment issues, where the droplets placed during the different direction passes might not perfectly align. This misalignment can cause banding or streaking, which are lines across the printed media where the droplets didn’t align correctly, negatively affecting the print quality. The printer must meticulously manage the timing and synchronization of the print heads with the media feed to minimize these issues. The precision of ink droplet placement is critical, and any variation can become more pronounced when switching between directions.
To counteract potential quality issues, many modern wide format printers come with sophisticated print head alignment technologies and calibration processes that adjust the timing and compensate for any misalignment, ensuring that the print quality remains high even in faster, bidirectional modes. So, while bi-directional printing can indeed affect print quality if not carefully controlled, advancements in printer technology and software algorithms have made it possible to enjoy both high print speeds and high-quality output.
Paper Feed and Media Handling System
The paper feed and media handling system play a pivotal role in ensuring high-quality output from wide format printers. This system is responsible for the movement and positioning of the print medium—whether paper, film, vinyl, or canvas—during the printing process. The precision of the system directly impacts print alignment, color consistency, and the overall sharpness of the printed image. If the paper feed and media handling mechanisms are not finely tuned, the printer may experience media feed errors, resulting in misalignment, which can lead to smudging, ink wastage, and uneven print quality.
Advanced media handling systems accommodate various media types and thicknesses, ensuring consistent media tension and proper alignment. They also feature guides and rollers that precisely advance the media through the printer. Some systems include vacuum or suction features to keep the media flat and avoid any wrinkles or slips during printing. The precise control of media reduces the risk of head strikes (when the print head comes into contact with the media), which can damage the print heads and affect print quality.
Bi-directional printing is a method where the print head prints in both the left-to-right and right-to-left directions. Regarding how it affects print quality in a wide format printer, it has both positive and negative implications.
On the positive side, bi-directional printing can significantly increase print speeds because the printer utilizes both directions of the print head’s movement. By maximizing the printing during each pass of the print head, overall productivity increases without leaving idle time for the print head to return to a start position. This can be especially beneficial when dealing with large format prints that can take a considerable amount of time to produce.
However, bi-directional printing can also introduce print quality issues. If the paper feed and media handling system are not perfectly synchronized with the print head movement, there may be slight variances in print drop placement between the two directions. This can manifest as banding or a noticeable difference in print quality between the swathes laid down in opposite directions. To minimize these effects, most high-quality wide format printers include sophisticated calibration procedures that compensate for any slight misalignments during bi-directional printing. Properly maintained printers with precise paper feed and media handling systems should be able to engage in bi-directional printing with minimal impact on print quality, assuming that the printer’s firmware and software are optimized for such a printing technique.
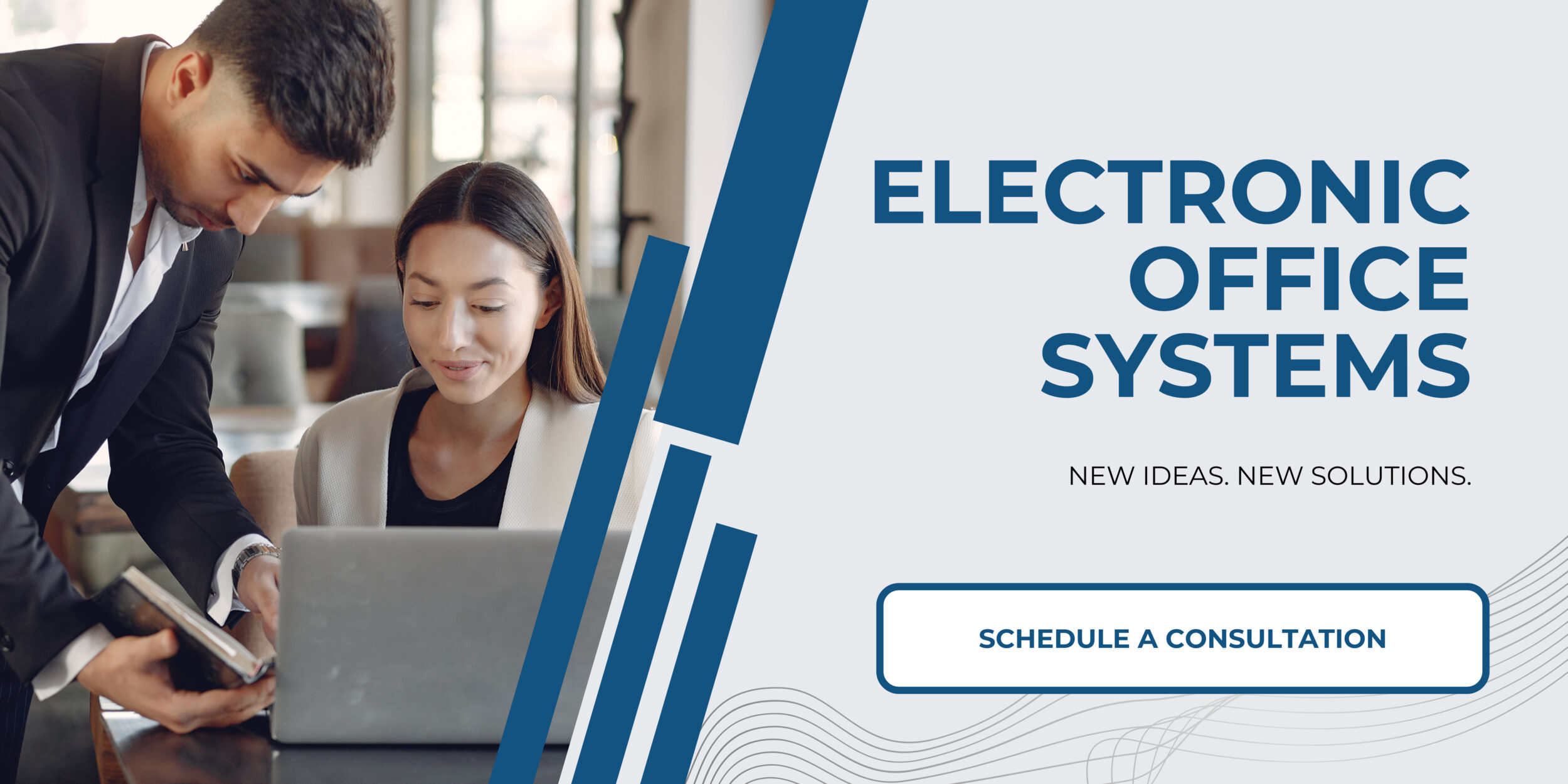
Impact of Bidirectional Printing on Print Speed and Productivity
Bidirectional printing refers to the ability of a printer to print in both directions as the print head moves across the paper or media. In other words, instead of the print head laying down ink only in a single direction before returning to the start position to begin a new line, bidirectional printing allows the print head to apply ink on the return pass as well. This can have a significant impact on print speed and overall productivity, especially for wide format printers that are often tasked with producing large prints that can be time-consuming to produce.
The main advantage of bidirectional printing is the increase in speed. Because the printer does not have to return to the starting edge after each pass to begin printing again, it can complete jobs in nearly half the time it would take to print unidirectionally. This can be particularly beneficial in high-volume printing environments where time efficiency is critical and the demand for printed material is constant and high.
Regarding print quality, bidirectional printing has its considerations. When a printer is operating in bidirectional mode, there needs to be precise synchronization between the print head movement and the ink droplet ejection. Any misalignment can result in poorer print quality, as it may lead to banding or color misregistrations. However, modern wide format printers often have advanced technologies that correct for these potential errors, ensuring high-quality prints even in bidirectional mode.
Advanced print head control algorithms and precise motor control are essential for achieving good print quality while taking advantage of bidirectional printing’s speed benefits. These technologies ensure that the droplets of ink are precisely placed on the media, regardless of the direction of the print head movement.
In practice, because of the variability of the print quality due to the bidirectional alignment challenges, operators might choose to use bidirectional printing for draft or internal prints, where speed is more important than the ultimate quality. For final or high-quality prints, they might resort to unidirectional printing to ensure the highest possible quality.
In summary, while bidirectional printing can significantly enhance the productivity of a wide format printer by reducing the time required to complete a print job, it also demands high precision and control to maintain quality. The printers that can effectively balance these demands offer a strong advantage in environments where both speed and quality are essential.