Title: The Impact of Continuous Duty Motors on Shredder Performance and Efficiency
Introduction:
In the realm of document destruction and material reduction, shredders play a pivotal role in maintaining security, privacy, and recycling efficiency. Central to the performance of any shredding machine is the motor—the heart that drives the cutting blades to tear through materials, ranging from paper to electronic components. Among the various types of motors employed in shredder design, the continuous duty motor stands out as a critical component that greatly influences both performance and efficiency. This article delves into the nuances of continuous duty motors and their specific impact on the functionality of shredders.
When it comes to industrial shredding tasks that demand prolonged operation and consistency, the continuous duty motor becomes a key player. Unlike intermittent duty motors, which require breaks to prevent overheating, continuous duty motors are engineered to operate without interruption over extended periods. This capability ensures a constant flow of material through the shredder, leading to higher throughput and less downtime, which is crucial in settings that necessitate large volume processing.
Moreover, continuous duty motors are built with endurance and durability in mind, typically featuring robust construction and elements designed to dissipate heat effectively. The knock-on effects of these features are multifold: improved longevity of the shredder, reduced maintenance requirements, and overall cost savings. Additionally, this type of motor often displays superior performance under load, maintaining consistent speed and torque levels that are essential for the efficient and uniform shredding of materials.
Efficiency, another critical factor affected by the motor type, has a direct impact on the operational cost and environmental footprint of shredding operations. Continuous duty motors are often optimized to use energy judiciously, helping to minimize electrical consumption and supporting environmentally-conscious practices in waste management. These advantages, coupled with the promise of continuous shredding activity, position continuous duty motors as indispensable assets for high-demand shredding systems.
This comprehensive exploration will provide insights into how continuous duty motors power shredders, the technological advancements that allow these motors to sustain ongoing operations and how their integration can lead to a significant uplift in the shredders’ performance and efficiency. As businesses and individuals alike seek more reliable and cost-effective ways to manage their shredding needs, understanding the role of continuous duty motors is essential for making informed decisions about shredder selection and utilization.
Impact on Operational Throughput
The term “operational throughput” refers to the amount of material a shredder can process within a given timeframe. The operational throughput is a key performance indicator for shredders as it directly influences productivity. One of the factors that can significantly affect operational throughput is the type of motor used in the shredding device, with a continuous duty motor being an essential component for achieving high performance.
A continuous duty motor is designed to operate at a consistent performance level without overheating or requiring rest periods during its cycles. This type of motor is essential for shredders that are expected to run for extended periods or even constantly, as it can maintain a steady throughput without the interruption of cooldown periods that would be necessary for a non-continuous duty motor.
The implementation of a continuous duty motor in a shredder enhances performance in several ways. First and foremost, it enables the shredder to handle a consistent volume of material without significant fluctuations in operational speed. This can be particularly beneficial in commercial or industrial settings where large volumes of documents or materials need to be processed quickly and efficiently.
Furthermore, continuous duty motors generally come with higher quality components that are designed to withstand the rigors of non-stop operation. This results in better durability and leads to lower chances of motor failure, thus reducing potential downtime which would otherwise hinder throughput. Increased durability also minimizes maintenance requirements that may disrupt workflow and further bolster operational throughput.
In terms of efficiency, a continuous duty motor tends to be more energy-efficient compared to intermittent duty motors. Because they are designed for prolonged use, they can operate effectively at their rated load without wasting energy through frequent starts and stops which is where most of the energy surges occur.
Lastly, shredders with continuous duty motors are better suited to maintain a level of performance that is not easily affected by variable loads. Since shredding demand can fluctuate depending on the material being processed or the workload at any given time, having a motor that can consistently power through these variations is crucial to maintaining high operational throughput.
In conclusion, the integration of a continuous duty motor into the design of a shredder is a significant determinant in achieving optimal operational throughput. By ensuring steady, uninterrupted performance, minimizing maintenance and breakdowns, and maximizing energy efficiency, a continuous duty motor elevates both the performance and efficiency of a shredding machine, making it a crucial component for high-demand shredding tasks.
Heat Generation and Dissipation
Heat generation and dissipation is a critical aspect when it comes to the performance and efficiency of a shredder, especially one equipped with a continuous duty motor.
Shredders with continuous duty motors are designed to operate for extended periods without overheating or requiring cool-down breaks. This is particularly beneficial for industrial or office settings where the shredding demand is high. These motors are typically built with a higher quality of materials and engineering, focusing on handling the thermal load efficiently.
The performance of a shredder with such a motor is directly affected by how effectively it can manage heat generation. The continuous operation means more friction and energy conversion, which inevitably leads to heat. The design of the shredder must, therefore, facilitate heat dissipation. This usually involves some combination of heat sinks, cooling fans, and sometimes even coolant systems. The better a shredder can manage heat, the less likely it is that it will suffer from thermal overload, which could lead to motor failure.
In terms of efficiency, heat generation and dissipation play a vital role as well. If a shredder cannot efficiently dissipate heat, the excess temperature could lower the viscosity of lubricants, which in turn increases friction and may lead to more power being required for the same amount of work. This inefficiency not only wastes energy but can also accelerate wear and tear on the shredder’s components, leading to more frequent maintenance or part replacements and potentially shortening the overall lifespan of the equipment.
In addition to the physical design considerations, some shredders with continuous duty motors might have intelligent control systems that monitor heat generation and adjust operational parameters to ensure that the machine stays within safe temperature limits. This could include reducing the speed at which the shredding happens or temporarily halting the shredding process until the temperature drops to an acceptable level.
Therefore, for shredders with continuous duty motors, it is essential to have an effective system for heat generation and dissipation to maintain high performance and efficiency while ensuring the shredder’s longevity.
Durability and Maintenance Requirements
Durability and maintenance requirements are crucial factors in the performance and efficiency of machinery, including shredders. Durability pertains to the ability of the shredder to sustain its performance over time with minimal depreciation or failure. It is influenced by the quality of materials used in its construction, the engineering design, and the tolerances to which it was manufactured. Typically, components such as the cutting blades, drive gears, and motors must withstand constant use and resist wear and deterioration caused by the shredding of materials, which could include paper, plastic, metal, or electronic components.
Maintenance requirements refer to the level of upkeep necessary to keep the shredder operating at optimal levels. Proper maintenance ensures that the equipment remains reliable and extends its lifespan. Routine checks allow for the timely replacement or repair of worn-out parts and the lubrication of moving components to reduce friction. In shredders, maintenance tasks might include cleaning, sharpening or replacing blades, ensuring proper alignment of parts, and possibly updating software for models that incorporate automation technologies.
In the context of a continuous duty motor in a shredder, both durability and maintenance requirements are significantly impacted. A continuous duty motor is designed to operate for extended periods without overheating or requiring cool-down intervals. This type of motor can enhance the performance and efficiency of a shredder in several ways.
Firstly, with a continuous duty motor, a shredder can run for more prolonged periods without interruption, improving operational throughput and productivity. As the motor is less prone to overheating, the risk of thermal damage to the motor and other shredder components is reduced, enhancing the overall durability of the system.
Secondly, the reduced need for start-stop operation minimizes mechanical stress on the shredder components. This steady operation typically results in less wear and tear and, thus, longer intervals between maintenance. The less frequent need for repairs and part replacement contributes to a lower total cost of ownership and reduced downtime for the equipment.
Furthermore, because continuous duty motors are built for non-stop use, they are often more efficiently engineered and of higher quality. They are better able to withstand the demands of shredding materials constantly, which translates to an investment in long-term reliability. Users can avoid the inefficiencies related to overworking a motor not designed for continuous operation, such as power surges and energy waste.
In conclusion, the integration of a continuous duty motor into the design of a shredder has the dual effect of enhancing the shredder’s durability by ensuring its components are under less strain during operation, and reducing maintenance requirements by allowing steady, consistent performance with fewer interruptions for servicing. This increase in reliability and efficiency typically leads to a reduction in the total cost of operation and maximizes the return on investment for businesses that rely heavily on shredding equipment.
Energy Consumption and Efficiency
Energy consumption and efficiency are critical factors in the performance and functionality of any shredder that uses a continuous duty motor. The term “continuous duty” refers to motors designed to operate at a constant load for an indefinite period without overheating or suffering degradation in performance. When it comes to shredders, this means that the motor is capable of running continuously as it processes materials without needing to pause for cool-down periods like an intermittent duty motor would require.
The efficiency of a continuous duty motor can significantly affect a shredder’s energy consumption. Efficient motors use less power to perform the same amount of work compared to less efficient ones. This reduction in power requirement translates to lower electrical bills, less heat generation, and potentially a smaller carbon footprint if the energy source is fossil-fuel-based.
Several factors influence the efficiency of these motors. For example, well-designed motors with high-quality components, such as precision bearings and better windings, have lower internal friction and electrical resistance, which in turn reduces electrical losses. Additionally, variable-frequency drives (VFDs) can be employed to adjust the motor speed to the optimum level for the load being processed, which further improves energy efficiency.
In shredders, a continuous duty motor’s ability to work relentlessly without a break makes the process more seamless and eliminates the downtime required for motor cooling. This constant operation can help ensure a uniform and consistent shredding process, which is often necessary for industrial applications where throughput and reliability are of the utmost importance.
However, it is important for a shredder to be appropriately matched with its motor regarding power and size to maintain high efficiency. A motor that is too small may be overworked, which can lead to excessive energy consumption and potential motor failure. Conversely, a motor that is too powerful for the shredder can lead to wasted energy and higher operational costs.
To conclude, continuous duty motors are advantageous in shredding operations since they improve performance by allowing for ongoing operation without the need for intermittent breaks that can disrupt workflow. When these motors are optimized for efficiency, they contribute significantly to reducing energy consumption, which not only lowers operational costs but also supports sustainability initiatives. It is essential to pair the right motor with the shredding application for both optimal performance and energy efficiency.
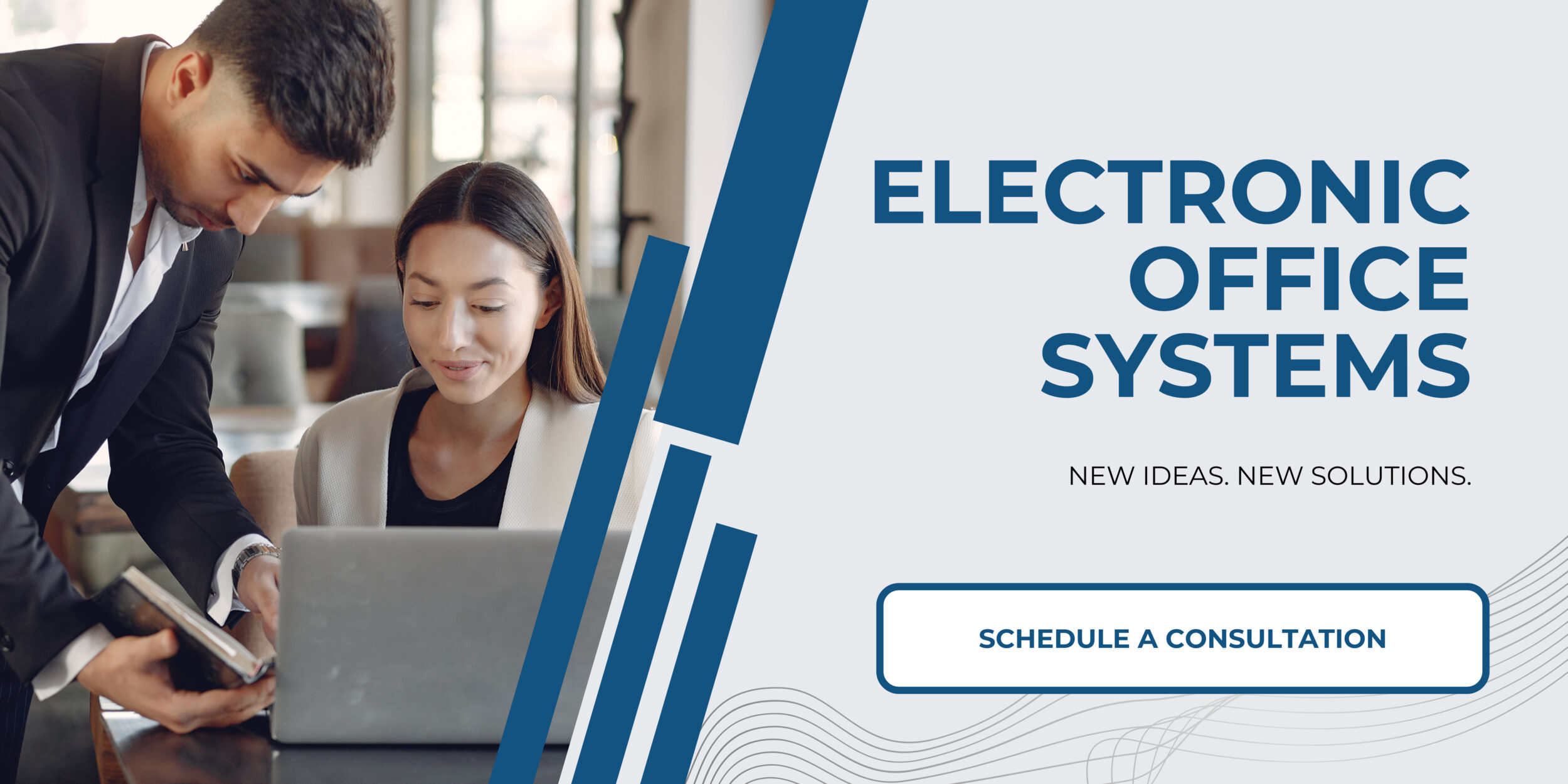
Torque and Speed Characteristics
Torque and speed characteristics are critical factors that determine the performance of a paper shredder. Torque refers to the twisting force that the motor of the shredder exerts on the cutting blades. It is this force that enables the blades to cut through paper, staples, credit cards, and other materials that are fed into the shredder. Higher torque implies a stronger cutting capacity, allowing the shredder to process thicker stacks of paper or tougher materials without jamming or stalling.
Speed, on the other hand, is the rate at which the shredder’s blades spin. It influences how quickly the material is processed. A higher speed means more cuts per minute, which translates to faster shredding operations. It is essential to strike the right balance between torque and speed to ensure that the shredder operates efficiently. If a shredder runs at a very high speed but has insufficient torque, it may stall when attempting to cut through thick materials. Similarly, if the shredder has a high torque but operates at a very low speed, the shredding process may become inefficient.
A continuous duty motor in a shredder enhances both performance and efficiency in several ways. Unlike a standard motor, a continuous duty motor is designed to run without interruptions over an extended period. This continuous operation is crucial for heavy-duty shredding tasks where the shredder needs to operate for several hours without overheating or requiring a cool-down period.
The continuous duty motor ensures that the shredder maintains consistent torque and speed levels throughout prolonged use. This reliability prevents the motor from overheating and reduces the likelihood of thermal shutdowns, which could interrupt work and reduce operational throughput. Moreover, such motors are generally built to higher durability standards to withstand the stress of constant use, which translates to less maintenance and longer service life.
In terms of efficiency, continuous duty motors are often more energy-efficient. They are designed to provide maximum power using the least amount of energy possible. This efficient conversion of electrical energy to mechanical energy translates to lower operating costs over time, particularly in commercial or industrial environments where shredders are used frequently. Overall, the integration of a continuous duty motor in a shredder presents a beneficial combination to meet the demands of heavy-duty shredding with robust, reliable, and efficient performance.