When it comes to maintaining the high-quality output of your copier, one of the critical components you will periodically need to replace is the drum unit. The drum unit is a crucial part of a copier’s imaging process; it is responsible for transferring the toner to the paper to create a crisp, clear image. However, not all drum units are created equal, and choosing the wrong one can lead to subpar performance, increased costs, and even damage to your copier. As such, it’s imperative to consider several key factors when selecting a drum unit replacement for your specific copier model. This introduction aims to outline the essential considerations to ensure you make an informed decision that maintains the reliability and efficiency of your copying equipment.
First and foremost, compatibility is paramount when choosing a drum unit. Each copier is designed to work with a specific drum unit that matches its specifications. Using an incompatible drum can lead to frequent paper jams, diminished print quality, and could potentially harm the inner workings of your copier. Therefore, understanding your copier’s model and its requisite drum type is the starting point for any replacement process.
In addition to compatibility, it is also crucial to consider the quality and longevity of the drum unit. A high-quality replacement may come at a higher initial cost but could save money in the long run by reducing the frequency of replacements and avoiding operational issues. The yield of the drum unit – or the number of pages it can print before needing a replacement – is another integral aspect to look at, as it impacts the overall cost-per-page and downtime of the copier.
Thirdly, while evaluating options, one must contemplate whether to choose OEM (Original Equipment Manufacturer) drum units or look for compatible or remanufactured units from third-party vendors. Each choice carries its own set of pros and cons related to cost, print quality, and warranty implications for your copier. Furthermore, the environmental impact of the drum unit, through factors such as recyclability and the manufacturer’s sustainable practices, may also influence a decision in light of corporate social responsibility.
The following article will delve into each of these considerations in detail to provide you with comprehensive guidance on choosing the ideal drum unit replacement for your specific copier model. Whether you are maintaining an office copier or managing a fleet of printing devices, being well-informed will help ensure continuous efficiency and exceptional print quality in your workplace.
Compatibility with Printer Model
When it comes to maintaining the functionality and operational efficiency of copiers and printers, choosing the right drum unit is crucial. The drum unit is a critical component in laser printers, as it works closely with the toner cartridge to create crisp images and text on the page. Understanding the importance of item 1 from the numbered list, “Compatibility with Printer Model,” is key to preventing printing issues and ensuring seamless operation.
The essential considerations when choosing a drum unit replacement for a specific copier model start with compatibility. Compatibility is fundamental because each printer model is designed to work with specific drum units that are matched to its operational parameters and requirements. Using an incompatible drum can lead to a host of issues ranging from poor print quality to potential damage to the printer.
Firstly, it’s necessary to check the printer’s manufacturer specifications to determine the exact model number of the drum unit. This information is typically found in the printer’s manual or on the manufacturer’s website. The model number is the surest way to match the drum unit to the printer because it takes into account the unique design and technological aspects of that specific printer model.
Secondly, the physical dimensions and design of the drum unit must align with those of the printer. Printers are built with precise internal layouts, and even slight variations in the shape or size of a drum unit can prevent it from fitting into the printer correctly or functioning as intended.
The printer firmware is another consideration. The firmware may only recognize drum units with specific chips or identifiers. Using an incompatible drum unit can result in errors or warnings that prevent printing entirely.
Additionally, the electrical connections between the drum unit and the printer must be considered. The printer relies on these connections to send and receive signals. An improper fit or incorrect electrical contacts can lead to communication errors and degraded performance.
Finally, compatibility impacts the overall longevity and maintenance cycle of the printer. An incompatible drum unit might wear out more quickly or cause undue wear and tear on other components, leading to increased maintenance costs and downtime.
In summary, ensuring that a replacement drum unit is compatible with a specific copier model is paramount. It requires attention to model numbers, physical dimensions, firmware specifications, electrical connections, and the broader impact on printer maintenance and longevity. Overlooking these considerations can lead to inefficiencies, increased costs, and even damage to the printer, emphasizing the critical nature of choosing the right drum unit.
Page Yield and Drum Life
When it comes to printer maintenance and replacements, particularly for the drum unit, one important aspect to consider is page yield and drum life. Page yield refers to the approximate number of pages that can be printed with a single drum unit before it must be replaced. Typically, drum units are designed to last longer than toner cartridges, capable of supporting several toner replacements over their lifetime. Drum life, on the other hand, is the expected lifespan of the drum unit itself, which is measured in the number of pages it can effectively contribute to before its performance declines.
It’s crucial to evaluate the page yield in terms of your specific printing needs. A higher page yield is generally more cost-effective for users with high-volume printing demands as it reduces the frequency of replacements, minimizes downtime, and can offer better value over time. For consumers or businesses with lower print volumes, a drum with a standard yield might suffice.
When choosing a drum unit replacement for a specific copier model, understanding the relationship between the drum life and the toner cartridges used can help in optimizing print costs and ensuring seamless printing operations. Each copier and printer model will have its own specifications for page yield and drum life, which is often provided by the manufacturer.
These specifications are not just random figures—manufacturers usually calculate them based on standardized testing methods, such as under specific conditions or using a certain percentage of page coverage, commonly at a 5% coverage per page. However, in real-world usage, these figures can vary due to factors like type of documents printed (text, images, mixed), print settings (draft, standard, high quality), and environmental conditions (temperature, humidity).
It is essential to find a drum unit that matches or exceeds the manufacturer’s specifications for the best results. Moreover, users should keep in mind that when the drum life is nearing its end, print quality issues may become apparent, such as streaks, spots, or faded areas on printed documents. Watching for these signs can help in preemptively scheduling maintenance and avoiding print quality degradation.
Overall, understanding and choosing the appropriate drum unit based on its page yield and life expectancy is a critical factor in maintaining the productivity and cost-effectiveness of a copier or printer. Regularly assessing print volume, document type, and quality requirements are important steps in ensuring that the chosen drum unit will meet or exceed the user’s expectations and demands.
Print Quality Requirements
When selecting a drum unit replacement for a specific copier model, one critical factor that comes into play is understanding and considering the print quality requirements of your tasks. The drum unit is a central component of laser printers and copiers that transfers toner powder onto paper, creating text and images through a complex electrostatic process.
High-quality printouts are essential for businesses that frequently produce printed materials for clients, such as marketing agencies, design firms, and legal offices. These organizations typically rely on exceptionally clear, crisp texts with fine details and gradients. Color accuracy might be equally crucial for those that print high-resolution images or graphics. In these scenarios, selecting a drum unit that can deliver high-resolution printing capabilities is imperative.
In contrast, environments like schools or casual home offices with less stringent requirements might prioritize cost over absolute print quality. They may opt for drum units that still produce readable texts but might not reproduce the highest level of detail or the widest color gamut. This trade-off often comes at a lower cost, which may better fit such users’ needs.
When evaluating print quality, one should also consider the drum unit’s durability and its potential to maintain a certain quality level over time. Some drum units may produce excellent initial prints but could quickly degrade in quality with usage. It is always vital to check user reviews and product longevity reports to ensure consistent performance throughout the drum unit’s lifespan.
In summary, the essential considerations for print quality when choosing a drum unit replacement include the clarity and precision of text and images, the accuracy of color reproduction, and the consistency of printouts over the unit’s lifespan. Aligning these aspects of print quality with the intended use and expectations will contribute to maintaining efficiency and satisfaction with the printed materials produced by the specific copier model.
Manufacturer vs. Third-Party Options
When considering a drum unit replacement for a specific copier model, one of the critical decisions you’ll face is choosing between manufacturer (OEM) and third-party (compatible or remanufactured) options. OEM stands for Original Equipment Manufacturer and signifies that the drum unit is made by the same company that manufactured the copier. Third-party units, on the other hand, are made by other companies and may be compatible or remanufactured versions designed to work with various printer models.
OEM drum units are often recommended by the copier manufacturer because they are specifically designed to work seamlessly with your model. This means they are typically reliable, come with a warranty, and theoretically should not cause any issues that would void your copier’s warranty. However, this peace of mind often comes at a higher cost, which can be a significant factor for businesses trying to manage their expenses.
Third-party drum units can offer considerable cost savings and are often much cheaper than OEM versions. Companies specializing in compatible or remanufactured drum units aim to provide products that meet or sometimes exceed the quality and performance of original units. However, it’s essential to proceed with caution. Not all third-party units are created equal, and some might even damage your printer or produce inferior print quality, which could result in additional costs down the line.
To ensure that you are making the right choice, it’s important to:
1. Assess the reputation and reviews of the third-party manufacturer.
2. Verify that the third-party drum unit is fully compatible with your copier model.
3. Check if using a third-party drum unit will affect your copier’s warranty.
4. Compare the page yield and overall cost per page between OEM and third-party options.
5. Consider the environmental impact of the drum unit, as remanufactured options can be more eco-friendly.
6. Ensure that there is a warranty or guarantee from the third-party supplier, offering some level of protection should the product not meet your expectations or malfunction.
Regardless of whether you choose an OEM or third-party drum unit, it is crucial to consider these aspects beforehand to avoid unnecessary printing issues and to ensure that your printed materials consistently meet the quality standards required by your business or personal needs.
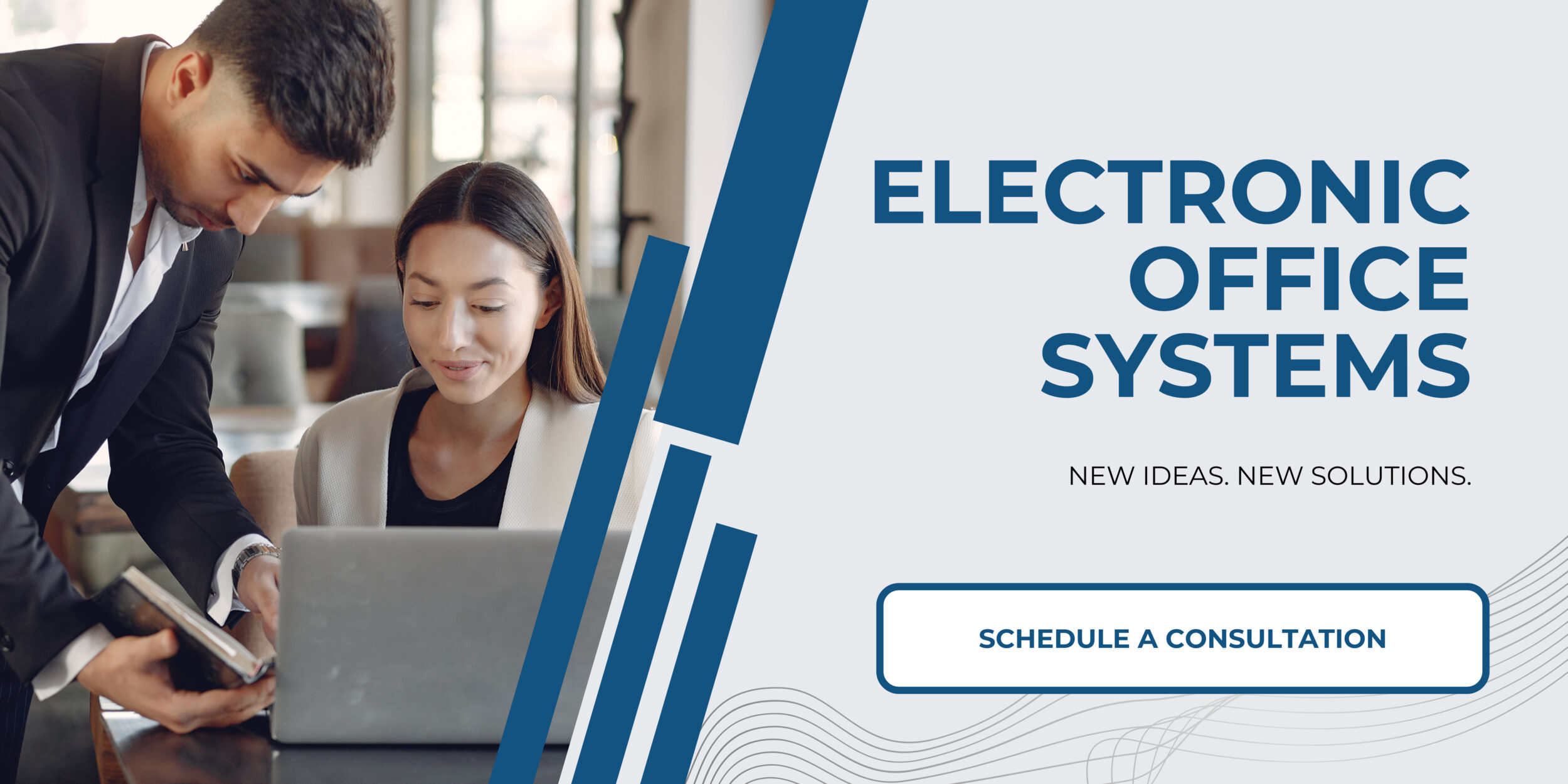
Cost and Budget Constraints
Cost and budget constraints are critical factors to consider when selecting a drum unit replacement for a specific copier model. The drum unit is an essential component of a printer or copier and is responsible for transferring the toner onto the paper to create the final print. Hence, its replacement has a direct impact on the printing process and the maintenance budget for printing devices.
Firstly, drum units can vary considerably in price, depending on the brand and whether the unit is manufactured by the original equipment manufacturer (OEM) or a third-party provider. Typically, OEM drum units are more expensive due to their guaranteed compatibility and reliability, but this isn’t to say that third-party units don’t have their place in the market. Many third-party drum units offer comparable quality at a lower cost; however, it is crucial to ensure they are compatible with the specific printer or copier model and won’t harm the machine’s longevity.
When considering budget, the initial purchase price of the drum unit is only part of the overall cost of ownership. It is also essential to look at the long-term costs, such as the unit’s lifespan (drum life), the cost per page, and the potential for reduced print quality or increased printer wear if the drum unit performs poorly. The drum life, usually measured in the number of pages it can print before being replaced, is crucial because a higher page yield can offset a higher initial cost, leading to savings over time.
Furthermore, the cost considerations might also include any warranties or guarantees provided by the manufacturer or vendor. These can offer peace of mind and potentially save money in the event of a malfunction or early wear out. However, using third-party drum units may void the warranty on the printer, which is another cost-related factor that users must be mindful of.
Lastly, buyers should consider their printing volume and frequency. Higher volume users may prioritize page yield and long-term costs over upfront savings, while lower volume users might be more concerned with upfront costs due to their less frequent need for replacements.
In conclusion, cost and budget constraints are often the defining factors in the decision-making process for drum unit replacements. It’s not only about the upfront purchase price but considering the total cost of ownership, which includes compatibility, print quality, page yield, long-term maintenance costs, and warranty implications, to make an informed, economical decision that matches the specific needs and usage patterns of the organization or individual.