Title: The Factors that Influence the Runtime of a Paper Shredder
In an era where privacy concerns and the protection of sensitive information have become central to personal and corporate responsibility, paper shredders have emerged as an essential tool in safeguarding against data theft and ensuring compliance with data protection laws. Whether deployed in a home office or a bustling corporate setting, the effectiveness of a paper shredder is not only measured by its shredding capacity and security level but also significantly by its runtime – the continuous length of time the device can operate before needing to cool down.
The runtime of a paper shredder is a key performance metric that can have practical implications for operational efficiency and user experience. Several factors converge to define this critical aspect of shredder functionality. These factors encompass both the design elements of the shredder itself, such as the motor power, cutting mechanism, and thermal protection features, as well as the usage patterns, such as the volume of paper being shredded, the paper thickness, and the duty cycle for which the shredder is rated.
Moreover, environmental conditions such as the ambient temperature and ventilation of the space where the shredder is located can also have an impact on its runtime. In the following article, we will delve into a detailed analysis of these determinants to provide a comprehensive overview of what influences a paper shredder’s runtime. Understanding these factors is pivotal not only for making informed purchasing decisions but also for ensuring the longevity and consistent performance of your shredding equipment. Join us as we dissect the intricacies of paper shredder runtimes and explore how to optimize this key aspect for better data management and protection.
Motor Power and Duty Cycle
Motor power and duty cycle are crucial elements that determine the performance and runtime of a paper shredder. The motor power, usually measured in horsepower (HP) or watts, directly affects the capacity of the shredder to take on and process the material fed into it. A more powerful motor can usually handle a greater throughput — in other words, it can shred more sheets of paper simultaneously and can manage thicker materials or even staples and credit cards depending on the model.
The duty cycle refers to the amount of time a paper shredder can operate continuously before it needs to cool down. This is a critical factor because shredders are not built to run non-stop; they need intermittent periods of rest to prevent overheating. Manufacturers typically specify the maximum runtime and the necessary cooldown period for their models. For example, a shredder may have a duty cycle that allows it to run for 20 minutes continuously before requiring a 40-minute cool-down period. The ratio of these times is directly linked to the capacity and intended use of the shredder — with heavy-duty shredders offering longer run-times and shorter cool downs, catering to high-volume, more demanding environments.
Several factors can impact the runtime of a paper shredder, interconnected with the machine’s motor power and duty cycle:
– **Heat Generation and Dissipation:** All shredders generate heat during operation. A powerful motor may heat up quickly, but it should be paired with an efficient cooling mechanism to prolong the shredder’s runtime. Overheating protection, such as thermal cutoffs and fans, can also play a significant role.
– **Shredder Capacity and Load:** The number of sheets a shredder can handle at once (its capacity) will impact run time since overloading the shredder can cause it to work harder and heat up faster, resulting in a need for a longer cool-down.
– **Type of Material Being Shredded:** Tougher materials require more power to shred, leading to shorter runs and more stress on the motor.
– **Maintenance:** Well-maintained shredders with sharp blades and clean sensors are likely to have longer run times. Accumulated dust and paper debris can put additional strain on the motor.
– **Ambient Conditions:** The environmental temperature can affect the motor’s heat dissipation. Cooler environments can potentially extend runtime, while a warmer environment might reduce it.
Considering these factors, it becomes evident that to maximize the runtime of a paper shredder, it’s not just the power of the motor and the specified duty cycle that are important. It is also critical to operate the machine within the recommended capacity, provide proper maintenance, and understand the impact of the environment in which the shredder is used. The balance and interaction of these factors ensure efficient operation and longevity of the equipment.
Shredder Capacity and Paper Load
Shredder capacity and paper load refer to the amount of paper that a shredder can process at once without jamming or compromising its performance. The capacity is typically measured in sheets of paper and indicates the maximum number a shredder can handle in a single pass. Shredders with a higher capacity can shred more sheets at once, leading to faster document destruction and increased efficiency for users with larger volumes of paper to dispose of.
Shredder capacity is influenced by several factors including the physical dimensions of the shredding blades or teeth, the power of the motor, and the design of the shredder’s feed entry. For example, a shredder intended for personal use in a home office may only be able to shred 5-10 sheets per pass, while a commercial-grade shredder might handle 20 sheets or more at once.
When considering paper load, it’s worth noting that shredders are calibrated to shred standard office paper. If you’re shredding thicker paper, glossy paper, envelopes with plastic windows, or other non-standard forms of paper, the effective capacity of the shredder may be reduced. Consistently overloading the shredder with more paper than it is designed to handle can lead to jams and wear out the motor more quickly, potentially reducing the shredder’s lifespan.
Factors determining the run time of a paper shredder include:
1. Motor Power and Duty Cycle: The motor power affects how effectively the shredder breaks down materials and how long it can operate before needing to cool down. The duty cycle refers to how long the shredder can run before it needs a rest period.
2. Shredder Capacity and Paper Load: As mentioned above, the number of sheets a shredder can handle at one time will influence the time it takes to complete a shredding job. Larger capacity shredders can run continuously for longer periods if not overloaded, yet may still require breaks depending on their cooling mechanisms and motor capabilities.
3. Type of Cut: Different types of cuts, such as strip-cut, cross-cut, and micro-cut, require different amounts of energy and time to process the paper. For instance, micro-cut shredders provide a higher security level by cutting paper into smaller pieces but usually have shorter run times due to the increased power needed.
4. Cooling-Down Period and Overheating Protection: All shredders need to cool down after a certain amount of use to prevent overheating. The length and frequency of these cool-down periods can considerably affect a shredder’s run time. Models with advanced cooling features or overheating protection may have longer run times.
5. Maintenance and Usage Frequency: Regular maintenance, such as oiling the blades and removing paper dust, helps maintain optimal performance, which, in turn, affects run time. High usage frequency might also demand more frequent cool-down periods to protect the motor from damage.
To maximize a shredder’s run time, it is important to choose the right shredder based on the volume of shredding needed and to follow the manufacturer’s guidelines for proper use and maintenance.
Type of Cut (Strip-Cut, Cross-Cut, Micro-Cut)
The type of cut refers to the way a paper shredder slices the paper and is one of the crucial features that determine a shredder machine’s performance. The three most common cuts include strip-cut, cross-cut, and micro-cut, each differing in the level of security they offer and the resulting run time.
A strip-cut shredder is the most basic type, cutting documents into long, vertical strips. This cut is faster and less complex, allowing the machine to shred more sheets at a time and usually have longer run times since the cutting mechanism is less strenuous on the motor. Strip-cut shredders are typically used for general document disposal and can handle more extensive periods of usage without overheating as quickly as other types.
Cross-cut shredders offer more security by cutting paper both vertically and horizontally into small particles. Because the cutting process is more intricate, cross-cut shredders can handle fewer sheets per pass compared to strip-cut shredders, and the run time can be affected since the motor works harder to perform the additional cuts. These shredders balance between security and efficiency, making them popular for office environments where sensitive information is frequently handled.
For the highest level of paper-cutting security, micro-cut shredders pulverize documents into confetti-like pieces. This method delivers superior protection because the particles are so tiny that reconstructing the original document is nearly impossible. However, this fine level of cutting requires more energy, which can reduce the shredder’s run time. The shredder needs to put in more effort and time to process even a small number of sheets, which in turn generates more heat and can lead to more frequent cool-down periods.
Several factors determine the run time of a paper shredder, with the type of cut being a significant one. The run time of a shredder is also affected by the motor’s power and duty cycle, which dictates how long the shredder can operate before it needs a cool-down period. Additionally, the shredder capacity and paper load influence run time; a higher capacity usually means more continuous run time. The machine’s cooling-down period and overheating protection are built-in features that prevent damage from extended use, which ultimately affects how long a shredder can operate continuously. Furthermore, regular maintenance and usage frequency will impact the overall lifespan and functionality of the shredder, including its run time and efficiency. Proper care, such as cleaning and oiling the blades, can help maintain the shredder’s run time and ensure it performs optimally.
Cooling-Down Period and Overheating Protection
The cooling-down period and overheating protection are critical factors that contribute to the efficiency and longevity of a paper shredder. The cooling-down period refers to the necessary downtime that a shredder requires after operating for a continuous period. This downtime allows the motor to cool down and prevents overheating. Paper shredders are generally designed with a specific maximum run time in mind, which can vary significantly from model to model. Once a shredder reaches its maximum run time, it will need to enter into a cooling-down period to avoid damage and reduce wear on the motor.
Overheating protection is a related feature that is often integrated into modern paper shredders. This is a safety mechanism that automatically shuts off the shredder if the motor reaches a temperature that is too high. Overheating protection is essential because it not only prevents potential fire hazards but also guards the internal components of the shredder against heat-related damage. It can extend the life of the shredder and reduce the need for maintenance or repairs due to overheating.
When selecting a paper shredder, it is vital to consider the length of both the maximum run time and the cooling-down period, especially for those who need to shred large amounts of paper regularly. In an office setting, for example, a shredder with a short cooling-down period may cause delays, which can impact productivity. In contrast, a shredder with a longer run time and effective overheating protection is better suited for heavy-duty use.
Overall, the cooling-down period and overheating protection features are integral to the design of a paper shredder because they directly impact runtime, operational safety, and the service life of the machine. It’s essential to choose a shredder with these features properly calibrated to the expected volume and frequency of shredding tasks to maintain efficiency and safety standards.
Factors Determining the Run Time of a Paper Shredder:
1. **Motor Power and Duty Cycle**: The motor’s power dictates the shredder’s ability to operate continuously. A more powerful motor can handle longer run times, while a less powerful motor might overheat more quickly. The duty cycle is the recommended on/off pattern of usage that prevents overheating.
2. **Shredder Capacity and Paper Load**: Shredders designed to handle more sheets of paper per pass can shred more quickly, reducing overall run time for large jobs. However, consistently pushing the shredder to its maximum capacity can lead to faster overheating.
3. **Type of Cut**: Different shredding styles (strip-cut, cross-cut, micro-cut) require different amounts of power and exert various levels of strain on the shredder’s motor. Micro-cut shredders, for instance, produce tiny particles and may overheat quicker than strip-cut shredders due to the more intensive shredding process.
4. **Cooling-Down Period and Overheating Protection**: As discussed, the cooling-down period is the rest phase required to prevent overheating, while overheating protection automatically powers down the shredder if it gets too hot. A unit with a shorter cooling-down period can be run more frequently, while one with longer cool-down needs might have a longer overall run time for large shredding tasks.
5. **Maintenance and Usage Frequency**: Regular maintenance can prevent excessive stress on the shredder and improve its run time. A well-oiled and cleaned shredder will run more efficiently than one that is not properly maintained. Additionally, shredders that are used frequently may have a shorter run time due to accumulated wear and tear.
Understanding these factors will help in selecting a shredder that best fits one’s needs and ensure that the machine operates within its capacity without incurring damage or experiencing premature failure.
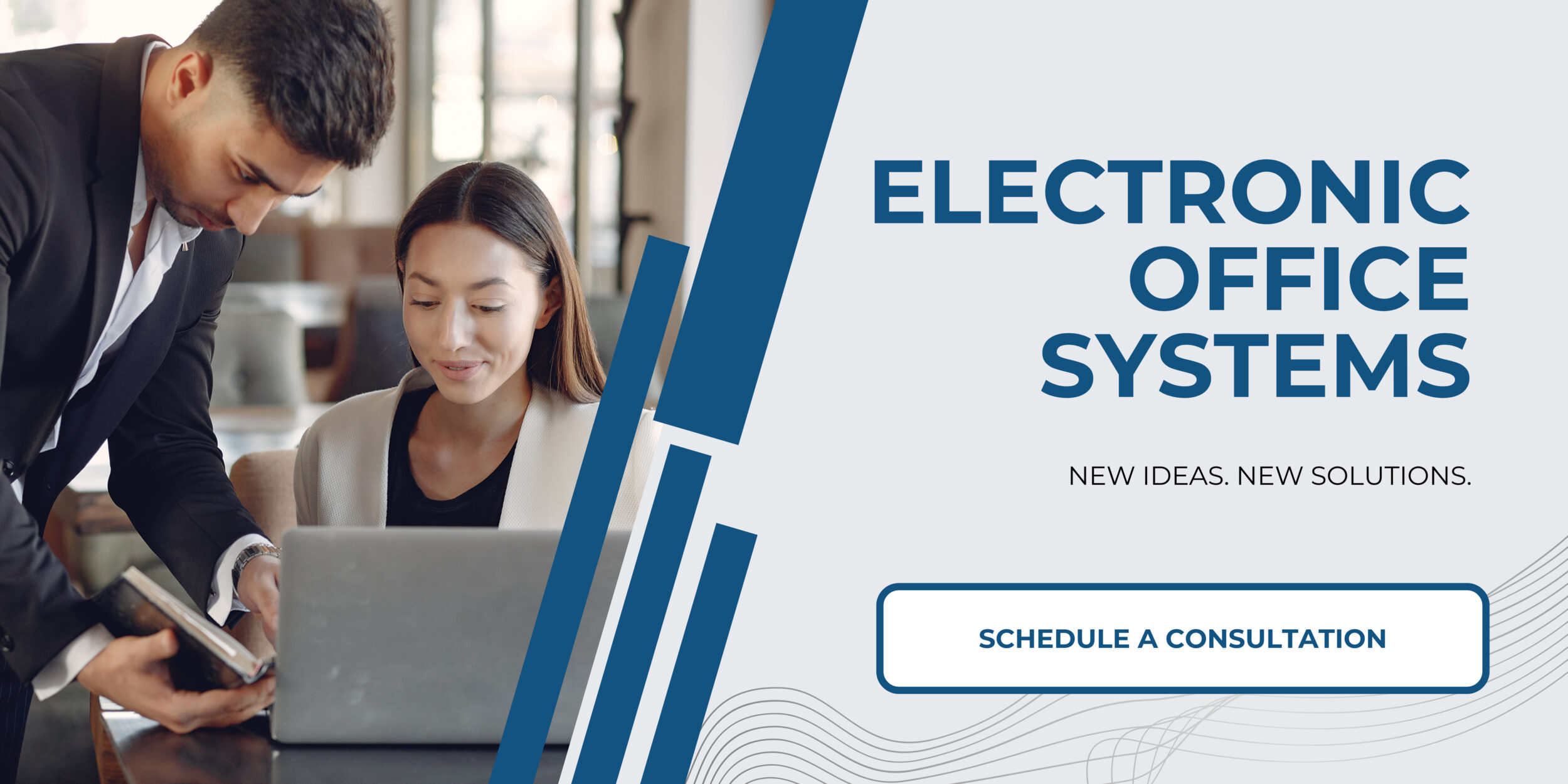
Maintenance and Usage Frequency
Maintenance and usage frequency are critical factors that determine the runtime of a paper shredder. The more frequently a shredder is used and the less maintenance it receives, the shorter its overall lifespan and efficiency during operation are likely to be. There are several considerations under this category:
**Regular Cleaning:** Paper shredders require regular cleaning to remove paper dust and debris that accumulate over time. This debris can clog the cutting blades, leading to increased wear and tear and potential overheating. By cleaning the blades according to the manufacturer’s instructions, users can ensure smoother operation and extend the shredder’s runtime.
**Oiling the Blades:** Many shredders need their cutting blades oiled periodically. Oiling helps to maintain the blades’ sharpness and prevents rusting, which keeps the shredder running efficiently. It’s important to use the correct type of oil as recommended by the manufacturer, as the wrong type could damage the blades or cause other issues.
**Removing Paper Jams:** Paper jams are not only a nuisance but can also harm your paper shredder if not addressed promptly. Users should carefully remove any jammed paper according to the manufacturer’s instructions to prevent damage to the motor or the cutting mechanism. Preventative measures like not exceeding the shredder’s maximum capacity can help minimize the occurrence of paper jams.
**Usage Habits:** The runtime of a paper shredder is also affected by how it is used. For example, consistently shredding materials at or near the shredder’s maximum capacity can lead to increased wear on the motor and overheat the device. In contrast, using the shredder well below its capacity and giving it ample rest between large shredding jobs can prolong its life.
**Frequency of Use:** Shredders designed for occasional, light use are not engineered to handle the same workload as commercial-grade shredders. Running a small office shredder continuously for extended periods can cause it to overheat and lead to motor burnout. Conversely, using a heavy-duty shredder for regular short sessions should pose no significant issue. It’s crucial to select a shredder that is appropriate for your expected usage frequency to prevent premature failure.
By adhering to proper maintenance practices and usage guidelines, users can maximize the runtime and lifespan of their paper shredders. It is always beneficial to refer to the manufacturer’s recommendations and ensure that any users of the shredder are trained on proper operation and care protocols.