Title: Coping with Copier Troubles: Recognizing the Signs for Service and Preventive Measures
Introduction:
In the bustling environment of modern offices, a copier is an indispensable asset that streamlines workflow and ensures the smooth operation of business activities. Despite being designed for frequent use and durability, copiers are complex machines that can experience wear, requiring routine attention and maintenance. Recognizing the common signs that a copier requires servicing is crucial for maintaining its functionality and preventing costly downtimes. Any delay in addressing issues can transform minor inconveniences into major breakdowns, impacting productivity and incurring significant repair costs. This article will outline the typical indicators of a copier in need of servicing, such as poor print quality, unusual noises, and error messages. We will also delve into preventive measures that can be taken to mitigate disruptions and maintain the copier’s longevity. By embracing a proactive approach to copier maintenance, organizations can ensure that this essential equipment continues to operate efficiently and reliably, minimizing interruptions to their daily operations.
Frequent Paper Jams
Frequent paper jams are one of the most common issues people encounter with office copiers. Jamming occurs when the paper feeding through the machine gets stuck, which can happen for various reasons. This not only halts productivity as employees must stop to fix the issue, but it can also lead to wasted paper and wear and tear on the machine if it happens consistently.
A typical sign that a copier needs servicing is an increase in the frequency of paper jams. While an occasional paper jam is normal, consistent issues can indicate misalignment, worn rollers, or problems with the paper tray. Sensing elements within the copier, such as paper path sensors or software that monitors the timing of the paper feed, may also malfunction and cause recurrent jamming.
Preventive measures for paper jams and other copier issues include regular cleaning and maintenance. This ensures that the interior of the copier is free from dust and debris that can cause paper to stick or misfeed. Proper usage and handling of the equipment also play a significant role in preventing jams. This includes using the correct paper type and weight, ensuring paper is loaded properly into the trays, and avoiding overfilling the feeders.
Timely replacement of consumables, such as toner and paper, is crucial. Old or poor-quality paper can absorb moisture and become sticky, leading to jams. Worn out rollers, which are responsible for feeding paper through the machine, can also cause jams and misfeeds, so they should be replaced as per the manufacturer’s maintenance schedule.
Environmental considerations for copier placement can affect the frequency of paper jams. Copiers should be placed in a clean, dust-free environment with stable temperature and humidity levels to prevent paper from absorbing moisture and swelling, which might lead to jamming.
Finally, scheduling professional servicing and inspections is a preventive measure to avoid major breakdowns. Technicians can identify and resolve minor issues before they become major, as well as ensure that all the moving parts are in good working order, which reduces the likelihood of frequent paper jams and prolongs the life of the machine. Regular professional maintenance can keep the copier running efficiently and prevent operational issues that can interrupt daily business processes.
Poor Print Quality
Poor print quality from a copier can manifest in various ways, indicating that the machine may require servicing. Some of the symptoms might include streaks or lines on the printed pages, incomplete or faint prints, smudges, or inconsistent coloring. These problems can result from different issues such as depleted toner levels, the need for replacement of the drum unit, clogged print heads, or even dirt accumulation on various internal components.
When parts such as rollers and drums approach the end of their lifecycle or become dirty, print quality is commonly jeopardized. Servicing might involve cleaning, adjusting, or replacing components, which can restore the copier to optimal functioning conditions. An expert can also recalibrate the system to ensure color accuracy and proper printing alignment.
To discuss common signs that a copier requires servicing, one should be aware of indicators such as increased frequency of paper jams, unusual noises, error messages, and misfeeds. If a copier persistently presents such symptoms, it is a clear sign that the machine needs a professional’s attention.
As for preventive measures that may help avoid major breakdowns, regular cleaning and maintenance sit at the top. Engaging in consistent upkeep of the machine can prevent dust and residue buildup, which could otherwise interfere with the copier’s mechanisms. Proper usage, like using the correct paper type and not overloading the machine, also plays a significant role in maintaining its health.
Replacing consumables, such as toner cartridges, drums, and fusers, before they are completely worn out can also extend the life of the copier. Paying attention to the manufacturer’s guidelines regarding the service life of these items is crucial.
Furthermore, the environment where the copier is situated affects its functionality. It should be kept in a location that is free from extreme temperatures, humidity, and direct sunlight, all of which can adversely affect performance.
Lastly, investing time in scheduling professional servicing and inspections can act as a proactive approach to identifying potential issues before they erupt into more significant complications. By adhering to these preventive measures, one can often avert the need for extensive and costly repairs.
Unusual Noises During Operation
Unusual noises during the operation of a copier are more than just a minor inconvenience; they are often a harbinger of potential issues that could escalate into major problems if not addressed in a timely manner. These sounds could include grinding, squeaking, clicking, or other out-of-the-ordinary noises that are not part of the copier’s regular operational sounds. Such noises may indicate a variety of underlying issues, such as mechanical wear and tear, the need for lubrication of moving parts, debris trapped in the machine, or components that are loose or out of alignment.
For instance, a grinding sound may be indicative of worn-out gears or rollers, which are integral components for moving paper through the machine. Squeaking may suggest that there is a need for lubrication on various parts of the equipment. Clicking sounds could be related to a problem with the machine’s electric components or a sign that certain parts are not correctly engaging as they should.
When these noises arise, it’s crucial to address them promptly. Ignoring them could lead to a worsening of the problem, where a simple fix could have sufficed if caught early. For example, a misaligned component left unattended could lead to improper wear and eventually a breakdown of not just the one part, but potentially others in a domino effect of mechanical failure.
In terms of common signs that a copier requires servicing aside from unusual noises, there are several indicators to look out for. Frequent paper jams not solved by simple troubleshooting could point to deeper problems such as misalignment or worn rollers. Poor print quality, such as streaks, blurs, or inconsistent toner distribution, could suggest issues with print heads or toner cartridges. Error messages and codes often signal specific malfunctions that require professional attention. Slow performance and frequent misfeeds might indicate a need for a thorough cleaning or replacement of certain components.
Preventive measures can significantly reduce the need for emergency servicing and help in avoiding disruptive breakdowns. Regular cleaning and maintenance are essential; this includes removing paper dust, cleaning rollers, and ensuring that there are no residues left on the glass or internal pathways. Proper usage and handling of the equipment are also crucial – following the manufacturer’s instructions on loading paper, replacing toner cartridges, and other routine tasks can help prevent many common issues.
Timely replacement of consumables, such as toner and ink, before they run dry is important, as running a copier on low toner can lead to poor print quality and additional strain on the device. Considering environmental factors, like humidity and temperature, for copier placement can also help in preserving its condition, as extreme conditions can impact performance and the longevity of the equipment.
Finally, scheduling professional servicing and inspections can be an effective measure for sustaining the copier’s optimal functionality. Technicians can provide a comprehensive check-up of the copier to identify and rectify issues that may not be obvious to the untrained eye. By adhering to a regular servicing and maintenance schedule, many of the common issues requiring repair can be avoided, thereby ensuring that the copier operates efficiently and has a lengthy service life.
Error Messages and Codes
Error messages and codes displayed on a copier are often indicators of specific issues that the machine is encountering. These messages and codes are part of the copier’s self-diagnosis system, designed to alert users to faults or the need for maintenance. Their appearance can range from simple alerts, such as indicating an open cover or an empty paper tray, to more complex codes that signal internal mechanical or electrical problems.
One of the most common reasons for seeing error messages and codes is due to hardware malfunction within the copier. This can include issues with the internal circuitry, failures in mechanical components like feeders and fusers, or problems with sensors not functioning correctly. Software glitches can also lead to error codes when the copier’s firmware becomes outdated or if there is a conflict within the machine’s internal processing.
Regular servicing is crucial to not only address these issues when they arise but also to prevent them from occurring. Preventive measures can play a significant role in reducing the frequency and severity of copier malfunctions. One of the most basic preventive steps is regular cleaning and maintenance, which can help avoid a buildup of dust and debris that can interfere with the machine’s components. Proper usage and handling of the equipment are equally important; for instance, loading paper correctly and using the right type of supplies can minimize the risk of jams and related errors.
The timely replacement of consumables like toner, drums, and even paper, when it’s of poor quality, helps maintain optimal functioning and reduces the strain on the copier’s mechanical parts. Placing the copier in an appropriate environment where temperature and humidity are controlled can prevent parts from expanding, contracting, or corroding, which can lead to errors. Finally, scheduling professional servicing and regular inspections can ensure that potential issues are identified and rectified before they manifest as error messages and codes, ultimately leading to a more reliable and efficient copier.
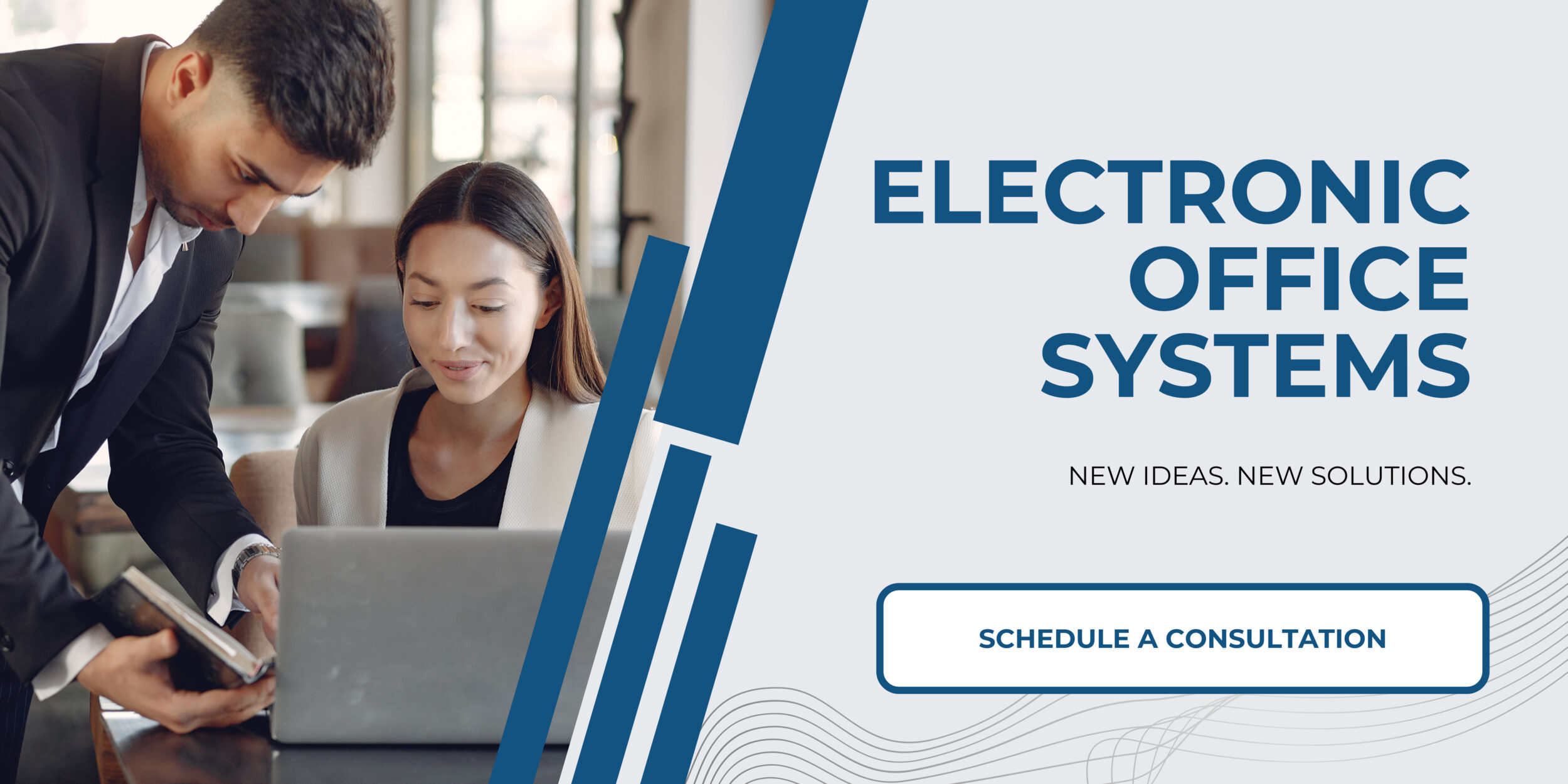
Slow Performance and Frequent Misfeeds
Slow performance and frequent misfeeds in a copier can be particularly troublesome for any office setting. These issues impact productivity and can cause significant annoyance and delay. When a copier begins to slow down, it suggests that it is struggling to process the tasks at its normal pace, which could be due to a variety of factors, including but not limited to the machine’s age, outdated firmware, or internal component wear and tear.
Misfeeds are another common issue where the copier fails to feed the paper correctly, leading to jams and even potential damage to the machine. This can occur because of misalignment, wear on the rollers, or simply because of using the wrong type or size of paper.
One classic sign that a copier needs servicing include an increase in the frequency and consistency of jams and misfeeds, even after performing basic troubleshooting steps such as removing jammed paper according to the manufacturer’s instructions or realigning the paper tray. If these problems persist, it’s a strong signal that professional service may be necessary.
Aside from slow performance and frequent misfeeds, it’s important to recognize other indications that a copier might require servicing. Common signs can include but are not limited to:
– **Frequent Paper Jams:** While the occasional paper jam is normal, frequent jams can be a sign of deeper mechanical issues.
– **Poor Print Quality:** Blurred, streaky, or faded prints often indicate a problem that might require professional attention.
– **Unusual Noises:** Strange sounds such as grinding, clicking, or squeaking are not typical and can indicate mechanical issues.
– **Error Messages and Codes:** Persistent or recurring error messages on the copier’s display can signal specific problems that often need an expert’s eye.
Preventive measures can significantly reduce the risk of major copier breakdowns. Regular cleaning and maintenance are essential, as accumulated dirt and debris can cause issues over time. This includes cleaning the copier’s exterior and interior following the manufacturer’s guidelines. Ensuring proper usage and handling of equipment can extend the copier’s life—this means using the correct paper type and size, avoiding overloading the paper tray, and ensuring documents are free of staples and clips before copying.
Timely replacement of consumables such as toner, ink cartridges, and drums is crucial to maintain optimal performance and print quality. Neglecting to replace these in a timely fashion can lead to poor print quality and additional strain on the machine.
Environmental considerations for copier placement can have a significant impact on performance. Factors such as humidity, temperature, and exposure to direct sunlight can affect the copier’s operation. Therefore, it’s important to position the copier in a suitable environment.
Lastly, scheduling professional servicing and inspections can uncover and address issues that may not be obvious to the untrained eye. Having a professional technician service the device can ensure that components are in good working order and are replaced or repaired before causing major operational issues. Regularly scheduled servicing can significantly extend the lifespan of a copier and ensure that it performs at its peak capacity.