In contemporary offices and homes, paper shredders serve as critical tools to securely dispose of sensitive documents, thus safeguarding against identity theft and maintaining confidentiality. However, alongside their utility, paper shredders can introduce noise, which may disrupt the tranquility of the environment. The noise level of a paper shredder can be influenced by a myriad of factors, ranging from the design of the shredder itself to the manner and frequency of its use. Understanding these factors is key for consumers and businesses alike who seek to balance the need for security with the desire for a quiet workspace.
First and foremost, the design of the paper shredder plays a pivotal role in determining its noise output. The build materials, the engineering of the cutting blades, the insulation within the machine, and even the type of motor used can all dramatically influence the acoustics of shredding. Higher-end models often incorporate noise-dampening features such as specialized gears or mounts, while budget models may lack such refinements, leading to louder operation.
Moreover, the capacity and speed of the paper shredder are also significant contributors to its noise level. Models designed for higher volume shredding and those that shred more rapidly tend to produce more noise due to the increased energy exerted by the shredder’s motor and the rapid movement of cutting components. This is not only associated with the mechanical sounds of paper being cut but also with the strains placed on the motor.
In addition to design and capacity, the maintenance of a paper shredder can impact its noise production. Shredders that are not regularly cleaned or lubricated may operate less smoothly, generating additional noise as paper passes through. Furthermore, using the shredder for materials it is not designed to handle, such as thicker papers, plastic cards, or metal clips, can cause strain on the machine, leading to heightened sound levels during operation.
Finally, the acoustic characteristics of the environment where the paper shredder is operated can either amplify or dampen the noise produced. Hard surfaces can cause sound to bounce and increase the din in a room, while carpeting and other soft furnishings can help absorb sounds. Consequently, the placement of the shredder can be as crucial as the design of the shredder itself.
In the following article, we will delve deeper into the various factors that contribute to the noise level of a paper shredder, exploring how each aspect affects the overall sound output and what can be done to minimize disruptions in a work or home setting. Whether you are in the market for a new paper shredder or seeking to reduce the noise level of your existing unit, understanding these elements will be instrumental in achieving an effective and peaceful shredding experience.
Shredding Mechanism Design
The shredding mechanism design is one of the primary factors that contributes to the noise level of a paper shredder. This aspect of the shredder pertains to its internal configuration, including the cutting blades’ shape, size, arrangement, and movement, which together dictate how paper is cut and processed through the machine.
Shredders typically come in two main types of cutting designs: strip-cut and cross-cut. Strip-cut shredders use rotating blades to cut paper into long, vertical strips, whereas cross-cut shredders use two contra-rotating drums to cut paper into small particles. Micro-cut shredders, a subset of cross-cut shredders, create even finer particles for more secure shredding. The more complex the cutting design, such as that of cross-cut shredders, the more mechanical action is required, which can, in turn, generate more noise.
Several factors within the shredding mechanism influence the noise level:
– **Blade Sharpness and Material:** Dull blades can cause increased resistance and friction when shredding paper, thus generating more noise. Also, the hardness and durability of the materials from which the blades are made can affect sound, with harder materials often producing more noise upon contact with paper.
– **Cutting Action:** The method by which the blades intersect and cut the paper can contribute to operational noise. For instance, a micro-cut shredder may require more frequent and fine cutting actions compared to a strip-cut shredder, potentially leading to higher noise levels.
– **Gear and Drive Train:** The gears and other mechanical aspects that transfer motion from the motor to the cutting blades can be sources of noise, especially if there is metal-on-metal contact, lack of lubrication, or if the gears are worn out.
– **Motor-to-Cutter Transfer:** How the power from the motor is transferred to the cutting blades affects noise levels. Direct drive systems may be quieter compared to belt-driven systems, which can introduce additional vibration and noise.
– **Paper Entry Design:** The design of the paper entry slot or throat might also play a small role. A well-designed entry can guide the paper smoothly into the blades, minimizing the paper’s resistance and the noise generated from crumpling or uneven shredding.
In summary, the shredding mechanism’s design, including the type of cutting action, quality, and configuration of the blades, as well as the efficiency of the gear and drive systems, significantly affects how much noise is produced by a paper shredder. A carefully constructed mechanism that minimizes resistance and unnecessary vibration will generally be quieter, thus contributing to a less noisy shredding experience.
Motor Type and Power
The motor type and power of a paper shredder are critical components that directly influence its performance and noise level. Typically, paper shredders use either a universal motor or an induction motor. Universal motors, being lightweight and compact, can operate at high speeds and tend to be louder due to their brushed design, which creates more friction and noise. Induction motors, on the other hand, are often heavier and more substantial but operate more quietly and efficiently, with lower maintenance requirements since they have fewer moving parts and do not incorporate brushes.
When considering the power of the motor, shredders with higher horsepower may shred more sheets of paper simultaneously and handle tougher jobs like shredding credit cards or CDs. However, more powerful motors can also generate more noise, especially under heavy load. The design and precision with which the motor integrates into the shredder can also affect the noise level; a well-engineered system that minimizes vibrations can lead to quieter operation.
Several factors contribute to the noise level of a paper shredder. Some of the primary factors include:
1. **Motor Specifications:** As mentioned, the kind of motor and its horsepower have a significant impact on noise emission. Universal motors are typically noisier than induction motors. Additionally, a powerful motor might produce more noise when shredding through thick stacks of paper or tougher materials.
2. **Cutting Blades and Mechanism:** The design of the blades and cutting mechanism is another contributing factor. Some blades are designed to cut more quietly, while others might make more noise as they tear through sheets of paper. If the shredding mechanism becomes dull or encounters materials that are difficult to cut, it will often make more noise due to the added strain on the motor and gears.
3. **Shredder Construction:** The overall construction of the shredder, including how well the components fit together, can influence how much noise it produces. Loose parts or poor assembly can lead to excessive vibration, which tends to increase noise levels.
4. **Gear and Transmission Quality:** The quality and design of the gear system transferring the motor’s power to the cutting mechanism also impact the noise level. Better quality gears operate more smoothly and quietly, while a shredder with cheap or worn-out gears will produce more sound.
5. **Insulation and Dampening:** The presence and quality of insulation and vibration dampening materials within the shredder’s housing contribute significantly to sound reduction. Some shredders are designed with specialized sound-dampening materials around the motor and shredding compartment to reduce the noise detected by the user.
By taking into account these factors and carefully choosing a shredder that balances performance with noise reduction features, users can find a shredding solution that meets their needs without causing excessive disturbance. Regular maintenance, such as oiling the shredder and sharpening or replacing blades as necessary, can also help keep the noise level down over the shredder’s lifespan.
Materials and Build Quality
The materials and build quality of a paper shredder play a critical role in determining both its durability and noise level. High-quality materials such as reinforced steel blades can withstand the stress of shredding better than lower-quality materials. This not only makes the shredder more robust and long-lasting but also contributes to smoother operation, which can result in reduced noise output. The precision with which a shredder is built can affect how much noise it generates as well. Tight tolerances and well-fitted parts are less likely to produce rattling or extra friction, both of which can amplify the sound during operation.
Moreover, the overall construction of the shredder can influence its acoustic characteristics. For example, units with heavy-duty metal casings might dampen sound more effectively than those with lightweight plastic housings. The build quality also extends to components such as the gears and bearings. High-quality gears that mesh precisely and bearings that allow for smooth rotation typically generate less noise compared to their lower-quality counterparts.
When manufacturers focus on the noise level as a design factor, they might integrate noise-reducing elements within the build of the shredder itself. This can include using special types of bushings or washers that cushion the movement of parts and absorb vibrations which would otherwise contribute to the noise level. Additionally, the design of the feed entry can be such to minimize the sound at the point of insertion where paper shredding begins.
In measuring the noise level of a paper shredder, several factors need to be considered:
1. **Shredding Mechanism Design**: The cutting mechanism itself, whether it is strip-cut, cross-cut, or micro-cut, will impact the noise level. Different designs may require different amounts of force and may operate at different speeds, resulting in varying sound levels.
2. **Motor Type and Power**: The type of motor (induction vs. universal) and its horsepower can affect how loudly the shredder operates. A more powerful motor might be louder but could also complete shredding tasks more quickly, reducing the time during which it generates noise.
3. **Materials and Build Quality**: As discussed, high-quality materials and construction help minimize noise by reducing vibration and ensuring smooth operation.
4. **Shredding Capacity and Speed**: Shredders designed to handle a higher volume of paper at once or at faster speeds can be noisier. The increased workload can cause louder operational sounds.
5. **Insulation and Sound Dampening Features**: The presence of insulation materials and other sound-dampening technologies can significantly reduce the amount of noise that escapes from the machine. This can include strategically placed foam or rubber, enclosed casings, and other vibration-absorbing design elements.
In conclusion, while the shredding mechanism’s design, motor type, capacity, and speed certainly contribute to the noise level, it is the materials and build quality that serve as a foundational determinant of how much noise a shredder will produce. High-quality and well-engineered shredders are typically quieter due to improved manufacturing techniques that focus on reducing vibration and ensuring the shredder operates as smoothly as possible.
Shredding Capacity and Speed
Shredding capacity and speed are significant factors that contribute to the performance and efficiency of a paper shredder. The shredding capacity refers to the maximum number of sheets of paper that a shredder can process at one time. A higher shredding capacity usually means that you can dispose of larger amounts of documents more quickly, streamlining the shredding process for office environments or individuals with heavy shredding needs. Speed, on the other hand, refers to how fast the shredder can process the papers. This is typically measured in feet per minute (FPM) and indicates how swiftly the shredder can turn a page into confetti or strips.
Now, while a higher capacity and speed can increase the convenience and efficiency of shredding tasks, these factors can also influence the noise level of the shredder. Here are a few factors that affect the noise created during the shredding process:
1. **Motor Load**: Higher capacity shredders require more powerful motors to pull in and cut through larger volumes of paper. As the motor works harder to shred more sheets at once or to maintain a faster speed, it generates more noise. The sound can further increase if the motor is straining because of continuous use or shredding materials that are at the upper limit of the shredder’s capacity.
2. **Cutting Mechanism Stress**: As the capacity and speed increase, the cutting blades experience more wear and tear. The heavier workload can lead to more mechanical noise as the cutters slice through multiple layers of paper, especially if the shredder is also dealing with staples, clips, or credit cards, which are common in high-capacity shredders.
3. **Vibration**: Higher shredding capacities and speeds may result in increased vibrations. The physical movement of the shredder’s components, particularly when the device is operating at full capacity, can amplify the sound output. This vibration can transfer to the surface the shredder is placed on, which can act like a sounding board, further increasing the volume of noise.
4. **Type of Cut**: The noise level can also vary depending on whether the machine is a strip-cut, cross-cut, or micro-cut shredder. Generally, machines that produce smaller particles (like cross-cut and micro-cut shredders) must work harder and thus might be noisier at higher capacities and speeds when compared to strip-cut shredders.
5. **Device Design and Maintenance**: The design of the shredding unit and how well it’s maintained play roles in noise production as well. Shredders that lack proper noise insulation or are not regularly maintained (with blades lubricated and cleaned, for instance) can become noisier over time as components degrade or malfunction.
In summary, while a shredder with high shredding capacity and speed can greatly improve productivity, it is important to consider that these attributes can contribute to increased noise levels. Factors such as motor load, cutting mechanism stress, vibrations, type of cut, and overall device design and maintenance need to be meticulously engineered and managed to keep noise levels within acceptable ranges for the work environment.
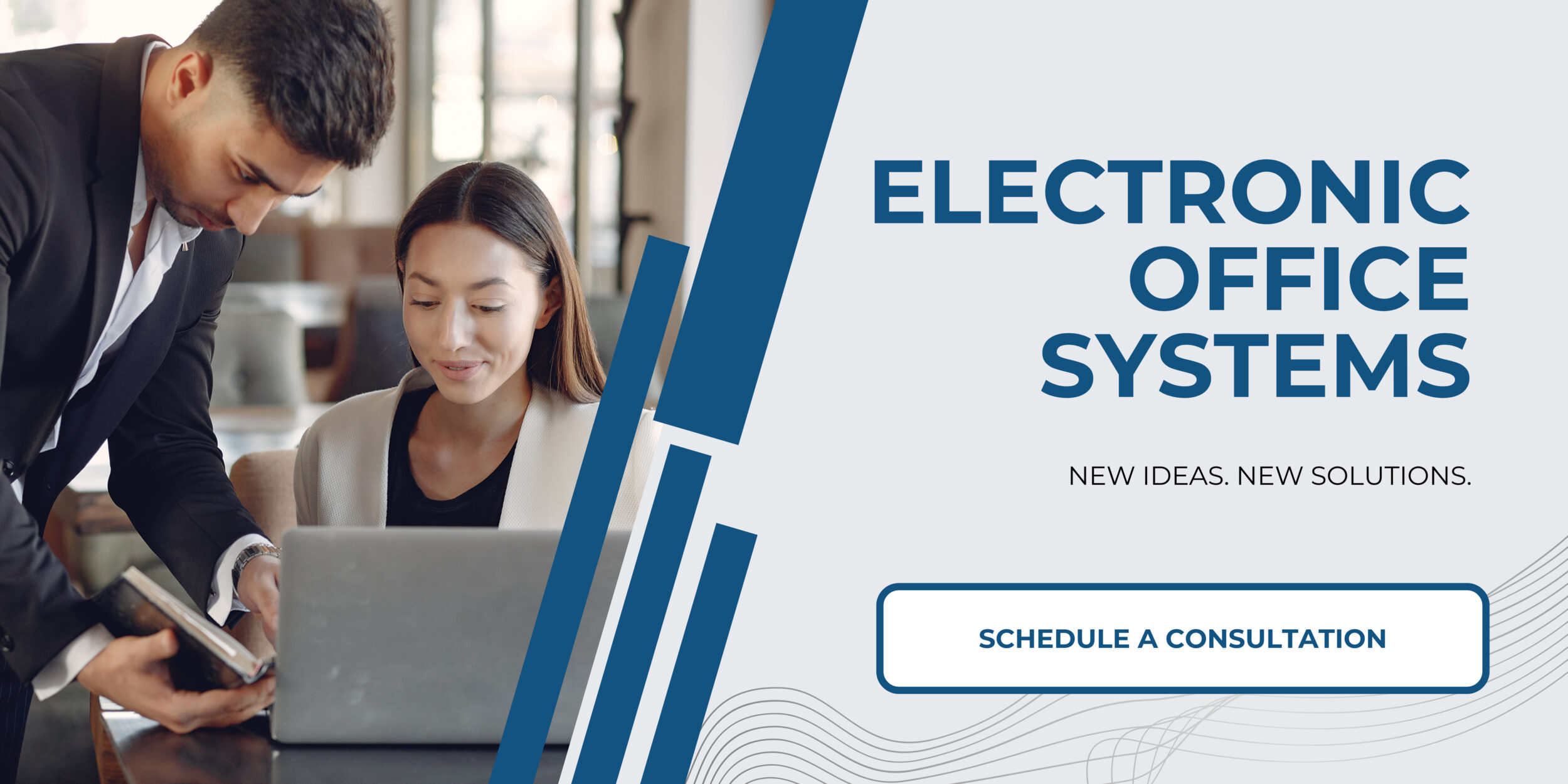
Insulation and Sound Dampening Features
Insulation and sound dampening features play an essential role in minimizing the noise levels of a paper shredder. These features are designed to absorb sound waves or reduce the vibration that causes sound, making the operation of a paper shredder significantly quieter. Sound dampening can be achieved through various methods, such as incorporating special materials into the construction of the shredder that are designed to absorb sound or by using design elements that isolate vibration.
One common approach manufacturers use to reduce noise is adding insulation around the shredding mechanism. This insulation can be made from foam or other sound-absorbing materials. By encapsulating the area where the shredding takes place, the sound emitted during the shredding process is contained and absorbed by the insulation, which prevents it from spreading widely.
Another important aspect is the use of rubber mounts or other vibration-absorbing components. These can be placed at strategic points where the shredder attaches to its housing, or between the motor and the frame of the shredder to reduce the transmission of vibrations to the external structure. This vibration is responsible for a significant amount of noise, and its reduction is key to making a quieter machine.
The design and layout of the shredder itself can also incorporate sound dampening techniques. For example, some shredders are constructed with double-walled housings, which offer an extra layer of sound insulation. Moreover, the shredder’s exterior panels can be lined with sound-dampening materials to prevent noise from escaping.
The quality of materials used in soundproofing is also a crucial factor. Higher quality materials tend to provide better sound insulation and, as a result, a quieter operational experience. As the paper shredder industry has grown, there has been an increasing demand for machines that can operate discreetly in office environments, spurring innovation in this regard.
In addition to their noise-reducing benefits, these insulation and sound dampening features also tend to correlate with overall build quality. A shredder that incorporates good sound dampening is likely to have been thoughtfully designed and constructed, leading to a better overall product.
In summary, factors that contribute to the noise level of a paper shredder include the shredding mechanism design, motor type and power, materials and build quality, shredding capacity and speed, and insulation and sound dampening features. A shredder that has been designed with consideration for reducing noise will incorporate various sound dampening and insulating elements to minimize operational decibels, thus making the shredder more suitable for use in shared workspaces or other environments where noise mitigation is important.