FPOT, or First Piece On-Time, is a metric crucial for businesses across various industries, reflecting the prompt initiation of production or service delivery. In an increasingly competitive and fast-paced market, the efficiency and reliability represented by FPOT can significantly impact a company’s reputation, customer satisfaction, and bottom line. In the introduction to an article discussing how different business scenarios and needs might be influenced by FPOT, one might explore several key considerations.
To begin with, the concept of FPOT could be introduced in the context of supply chain management and operational excellence. It is often a benchmark for manufacturing companies that need to evaluate the performance of their production lines. However, FPOT’s significance is not limited to the manufacturing sector alone; it extends to service providers and retailers who also strive for timely offerings to their clientele.
An overview of the multifaceted benefits of maintaining a high FPOT rate would be provided, highlighting not only the direct advantages to customer satisfaction and retention but also the ripple effects on inventory management, forecasting, and overall agility of the business to respond to market demands. Conversely, the drawbacks of a low FPOT rate could be introduced, such as increased costs due to rush orders, excess inventory, or impaired trust with customers and partners.
The introduction would also outline a variety of business scenarios, from the launch of a new product, scaling operations to meet increased demand, or entering a new market. In each case, FPOT can serve as a litmus test for the business’s ability to meet expectations and deliver value. For instance, in a new product launch, a strong FPOT indicates that the supply chain is effectively aligned with the product development cycle, ensuring that the product is available to customers as promised.
Furthermore, the article would suggest that assessing the implications of FPOT requires a nuanced understanding of each business’s unique needs and challenges. It would set the stage to delve into how FPOT is more than just a measure of punctuality; it is a reflection of a company’s operational efficiency, capacity for planning, and commitment to excellence. By considering different business scenarios, the article would promise to provide insights on how organizations can leverage FPOT as a key performance indicator to optimize their operations and maintain a competitive edge.
### Inventory Management and Stock Optimization
Inventory management and stock optimization are essential components of a successful business operation. They encompass a variety of processes designed to monitor and control the amount, location, and timing of stock. The primary goal is to maintain an optimal balance – having enough inventory to meet customer demand without accumulating excess that incurs additional holding costs or risks obsolescence.
Effective inventory management allows businesses to reduce costs and improve cash flow. By keeping stock at optimal levels, companies can prevent overinvestment in inventory while minimizing the risk of stockouts, thus ensuring that capital isn’t tied up unnecessarily in unsold products. Stock optimization, on the other hand, involves using predictive analytics and forecasting tools to accurately anticipate customer demand, thereby enabling a business to make informed purchasing decisions. This can help in maintaining a lean inventory, reduce carrying costs, and improve turnover rates.
In various business scenarios, Fast Pick Order Time (FPOT) can have a significant impact on inventory management and stock optimization. FPOT generally refers to the speed at which an order is picked, packed, and ready for shipment. A faster FPOT contributes to shorter lead times, which means customers receive their products sooner. In a retail environment, for example, a quick turnaround time on orders can lead to higher customer satisfaction and repeat business, as well as enable more accurate and dynamic inventory management.
For businesses with perishable goods or fast-moving consumer goods, FPOT is crucial. Efficient pick and pack processes reduce the time these products spend in storage, minimizing spoilage and waste. This is particularly important for food items, pharmaceuticals, and high-fashion garments, where product life cycles are particularly short.
Likewise, in a manufacturing context, components need to be available just in time to meet production schedules—neither too early, to avoid unnecessary storage costs, nor too late, to prevent costly production delays. Here, FPOT plays a pivotal role in ensuring that inventory levels are sufficiently synchronized with production needs.
However, an excessive focus on improving FPOT without considering the broader context of inventory management and stock optimization can lead to problems. For instance, it might lead to overstocking to ensure fast picking processes, which in turn can result in higher inventory carrying costs and potential waste through obsolescence.
In summary, inventory management and stock optimization significantly benefit from a well-managed FPOT. Fast and efficient order processing can enhance customer satisfaction and contribute to a lean and responsive inventory system. However, businesses need to balance the pursuit of a fast FPOT with the overall principles of stock optimization to ensure that the outcomes align with broader business goals, such as cost reduction and improved cash flow.
Supply Chain Efficiency and Vendor Relationships
The concept of Supply Chain Efficiency and Vendor Relationships plays a crucial role in ensuring that businesses can meet their operational goals, adapt to market changes, and maintain competitive advantage. This concept revolves around optimizing the various processes involved in the movement of goods and services from the point of origin to the point of consumption. To achieve this, companies strive to reduce waste, increase velocity, and manage inventories effectively in their supply chains.
Vendor relationships complement supply chain efficiency by fostering collaborative partnerships with suppliers. Strong vendor relationships can lead to better pricing, priority service, improved quality, and more innovation due to a more open exchange of information and trust. By working closely with their vendors, businesses can achieve better alignment with their supply chain goals and ensure that both parties are working towards mutual benefits.
First Pass Yield (FPOT), a metric that measures the percentage of products that are made correctly and to specification the first time without any scrap, rework, or repairs, can have substantial impacts on different business scenarios and needs. In Supply Chain Management, high FPOT rates can dramatically improve efficiency by significantly reducing lead times, decreasing costs associated with reworking defective products, and minimizing waste and overproduction. Increased FPOT rates will generally lead to a more streamlined and responsive supply chain, which is crucial in high-velocity industries.
In terms of vendor relationships, FPOT is an essential measure of supplier quality. Suppliers with high FPOT rates are considered more reliable and are likely to be more integral to business processes. When suppliers consistently deliver high-quality products, businesses can reduce their inspection and quality assurance costs. This reliability can lead to developing long-term strategic partnerships that benefit both the vendor and the purchasing company. Moreover, suppliers with high FPOT scores help in maintaining a company’s brand reputation by reducing the risk of defects reaching the end customer.
For companies operating in environments with fluctuating demand or those with just-in-time delivery systems, FPOT is particularly significant. In these scenarios, being able to depend on the first pass of products being of saleable quality can mean the difference between meeting consumer demand or facing backorders and lost sales. FPOT can also play a significant role in industries where the cost of errors is high, such as pharmaceuticals or aerospace. In these sectors, high FPOT rates are not just a matter of efficiency, but also of compliance and safety.
Overall, FPOT is a vital metric for any business concerned with enhancing supply chain efficiency and nurturing strong vendor relationships. The ability to produce goods correctly the first time directly impacts the bottom line and can drive significant improvements in overall business performance.
Cost Management and Budgeting
Cost management and budgeting are fundamental aspects of any business’s financial strategy. This involves the process of planning, controlling, and analyzing costs with the goal of meeting a company’s strategic goals. In the context of business operations, cost management and budgeting require scrutinizing all expenses and revenue streams to ensure that resources are allocated effectively and that spending aligns with company objectives.
An essential component of cost management is the ability to predict costs and formulate a budget that reflects the company’s financial reality and ambitions. Through budgeting, a company can set financial targets and limits for different departments, projects, or business segments, ensuring that there are controls in place to prevent overspending. By monitoring actual spend against these budgets, companies are able to make informed decisions and can take corrective actions if necessary. This could include identifying areas where costs can be cut without compromising quality or service, renegotiating contracts with suppliers, or adjusting product prices to ensure profitability.
Effective cost management and budgeting also provide valuable insights into cost drivers and can help companies optimize their spending by eliminating waste, improving efficiency, and prioritizing expenditures that offer the greatest returns or strategic advantage. Good budgeting practices can furthermore aid in forecasting and planning for future financial needs, helping businesses manage cash flow and prepare for investment or expansion opportunities.
The First Printout Time (FPOT) metric could influence different business scenarios and needs significantly. FPOT essentially refers to the time it takes for a printer or copier to deliver its first printed page after receiving a command. In many business environments where document handling is a regular undertaking, a rapid FPOT can help maintain productivity and efficiency.
For instance, in a high-paced legal office where time-sensitive documents are frequently needed, a higher FPOT can create bottlenecks, potentially affecting case preparation and client responsiveness. In fast-paced retail scenarios, where inventory reports or sales receipts are constantly being produced, a slow FPOT could impair staff’s ability to serve customers efficiently, thereby impacting customer satisfaction and sales performance.
Conversely, in a less demanding office environment where printing requirements are minimal and not time-sensitive, FPOT might not be a critical factor. Here, the focus may be more on cost savings for which devices with lower operational costs but slower FPOT might be preferred.
In manufacturing or logistics operations, where the printout of shipping labels, packing slips, or process documentation is frequent, a printer with a low FPOT could reduce wait times and potentially improve the flow of goods through a facility. Consequently, increasing operational efficiency might lead to reduced costs and better utilization of resources.
Cost management and budgeting must therefore consider the FPOT for printers and copiers in the context of the business’s operational needs. Investing in technology with faster FPOT can be justified if it aligns with the strategic objective of enhancing productivity and customer satisfaction, and if the increased cost fits within the organization’s budget constraints.
Customer Satisfaction and Delivery Performance
Customer satisfaction and delivery performance are paramount for the success of any modern business. They represent the culmination of the numerous processes and strategies that companies put in place, from the initial order to the final delivery of a product or service.
Effective delivery performance can significantly enhance customer satisfaction. In today’s fast-paced market, customers expect quick, reliable, and accurate deliveries. When a company consistently meets delivery timelines and provides high-quality products or services, trust is built, which can lead to increased customer loyalty and repeat business. Conversely, poor delivery performance can result in complaints, returns, and negative reviews, which can damage the business’s reputation and bottom line.
Firstly, let’s consider how FPOT, or First Pass On Time delivery, impacts customer satisfaction and delivery performance. FPOT refers to the percentage of orders delivered on-time and in full on the first attempt. Improving FPOT is crucial as it directly correlates to how customers perceive the reliability and efficiency of a company. In today’s marketplace, where consumers have ample choice and high expectations for rapid service, a high FPOT score can be a significant differentiator.
Different business scenarios and needs impacted by FPOT might include:
1. E-commerce: An online retailer relies heavily on their delivery performance to satisfy customers, as there is no physical store experience to compensate for logistical failures. A high FPOT rate in e-commerce would mean that customers receive their orders promptly, which can improve customer satisfaction and encourage repeat purchases.
2. Manufacturing: In a manufacturing scenario, just-in-time delivery is often essential. The manufacturer must have parts delivered reliably to keep production lines running without interruption. Here, FPOT directly affects production efficiency and customer commitments for product delivery times.
3. Service Industry: For services like internet or cable installation, FPOT would impact scheduling efficiency and customer satisfaction. A high FPOT means that service providers show up and successfully deliver the service on the scheduled date and time, which is crucial for maintaining a positive customer relationship.
4. Healthcare: In healthcare, timely delivery of medical supplies can be critical. FPOT here impacts patient care and overall healthcare facility operations. A high FPOT score ensures that healthcare providers have the necessary tools and medications to treat patients without delay.
FPOT is influenced by various factors, including inventory management, supply chain coordination, and production planning—all of which must be carefully monitored and managed to ensure high delivery performance. In conclusion, FPOT serves as a benchmark for operational efficiency and customer satisfaction, and businesses in any sector can benefit from focusing on improving their FPOT scores to stay competitive and keep their customers content.
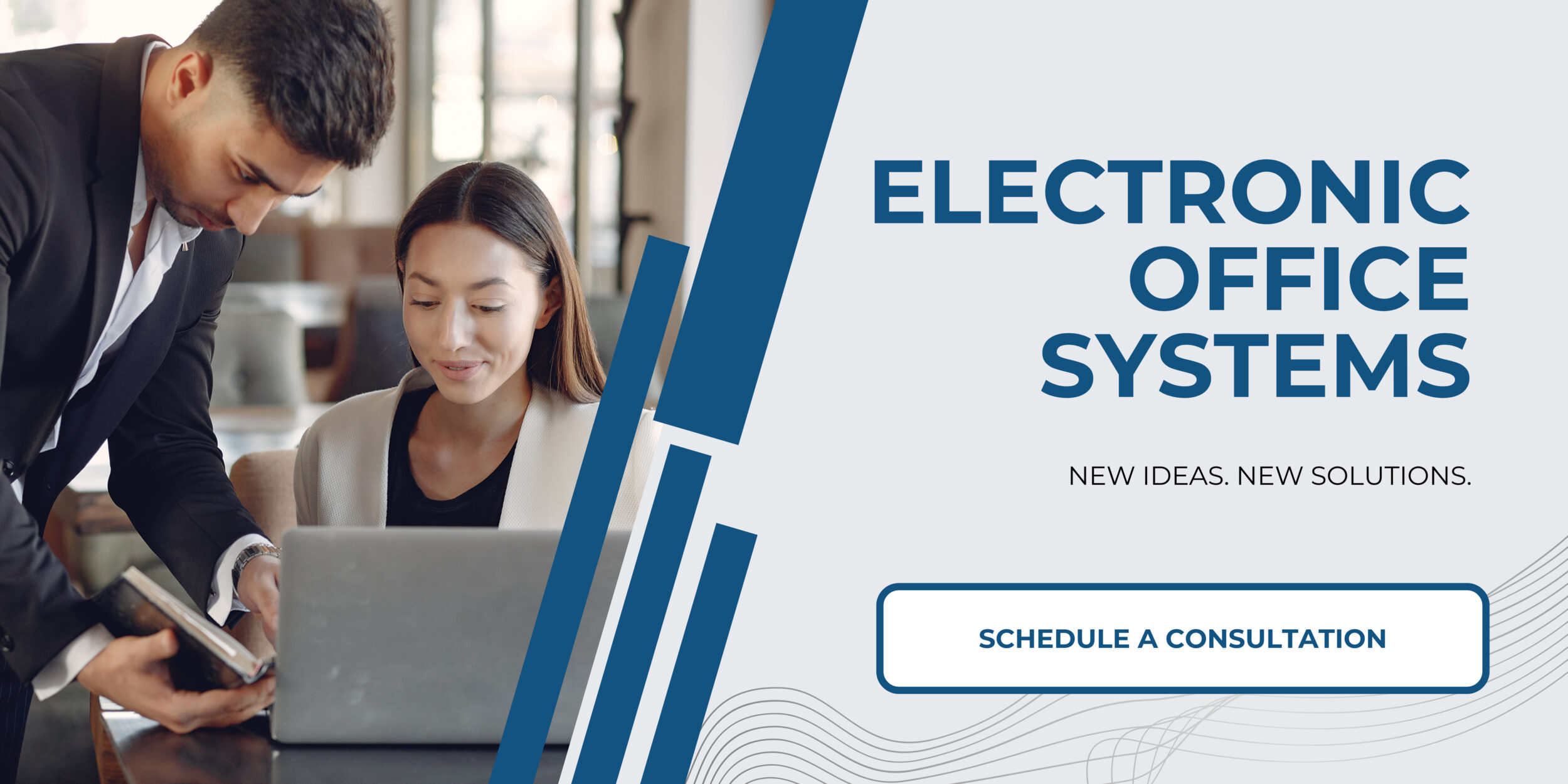
Production Planning and Capacity Utilization
Production planning and capacity utilization are critical aspects of manufacturing operations and have significant impacts on a business’s ability to meet customer demands, maintain operational efficiency, and achieve strategic goals. Production planning involves scheduling of operations, setting production goals, and determining the resources required to accomplish these goals. It ensures that the production process is in line with the company’s targets and market demands.
Capacity utilization, on the other hand, refers to the extent to which an enterprise employs its installed productive capacity. It is a measure of how well a business is using its resources to produce goods and services. An optimized capacity utilization means the company is maximizing its output without overextending its resources, which can lead to wear and tear on equipment, increased maintenance costs, or exhausted labor.
In different business scenarios and needs, First Pass Yield (FPY), or First Pass Through (FPT), and overall efficiency in the production process are highly important. FPOT (First Part Off The Tool), a critical subset of these metrics, refers to the quality and cycle time of the first item produced in a batch or run. It’s an indicator of how well the production setup is and whether the processes will run smoothly.
In a scenario where a business requires fast product delivery timelines, such as a company producing seasonal goods or one that needs to capitalize on a trend, efficient FPOT is crucial. Timely first parts mean that the rest of the production batch can proceed without delays, hence meeting market demands quickly. A delayed FPOT can result in missed opportunities and financial losses due to the short sales window or trend lifespan.
In high-precision industries like aerospace or medical devices, the importance of FPOT is elevated because it determines whether the production process can reliably meet stringent quality standards. A high FPY or FPOT suggests that the process setup is correct and can produce compliant parts, minimizing waste and rework, which are costly and time-consuming.
In high-mix, low-volume production settings, frequently encountered in custom manufacturing or job shops, FPOT is a measure of flexibility and rapid setup capability. Efficient changeovers and achieving a high-quality first part quickly are essential to meet varying customer requirements and maintaining profitability in smaller production runs.
On the contrary, in high-volume, low-mix scenarios such as mass production of consumer goods, FPOT can influence inventory levels and supply chain management. Efficient FPOT means less buffer stock is required, reducing holding costs and the risk of excess or obsolete inventory.
In conclusion, businesses must continually assess their production planning and capacity utilization strategies while considering the implications of FPOT on their operations. By doing so, they can identify areas for improvement, optimize their processes, reduce costs, and seek to exceed their customers’ expectations.