Shredders equipped with standby modes represent a confluence of convenience and energy efficiency in the modern office environment. These devices remain poised to resume full operation at a moment’s notice, yet they consume minimal power when not actively in use. However, this added functionality brings with it a unique set of maintenance considerations to ensure their longevity and optimal performance. The introduction of standby modes necessitates a reevaluation of traditional equipment maintenance protocols, with an emphasis on both the mechanical and electronic components that enable this feature.
A shredder in standby mode might appear inert, but behind the scenes, its components are in a state of ready suspension. Such a state can introduce specific stresses on electrical systems that differ from those experienced during either full operation or complete shutdown. Given this, it becomes crucial for users and maintenance personnel to understand how periods of inactivity can affect the shredder’s operation over time. For instance, ensuring that internal components do not succumb to the potential buildup of heat or experience condensation due to environmental factors becomes a more prominent concern.
Furthermore, developing a maintenance schedule that accounts for the unique needs of a shredder with standby mode is pivotal. This includes routine inspections, cleaning to prevent the accumulation of dust and debris, lubrication of moving parts, and verification of software or firmware updates for the electronic control systems. The maintenance program should also consider usage patterns – as the shredder might cycle between standby and active modes frequently – which can exert different forms of wear on its components compared to shredders operating without a standby feature.
In this article, we will delve deep into the maintenance considerations for shredding equipment with standby capabilities. We’ll explore the small, yet significant, adjustments required in preventive care routines, the potential impact of neglecting such adjustments, and the best practices for keeping these complex machines in prime working condition. Whether dealing with the cutting blades, motors, sensors, or electronic circuitry, understanding these considerations will not only maximize the effective lifespan of the shredder but also ensure that it functions safely and efficiently, ready to spring into action at the press of a button.
Power Consumption Management
Power consumption management refers to the strategies and practices that are implemented to manage and reduce the amount of electrical energy used by a device – in this case, a paper shredder with a standby mode. Efficient power management is crucial, not only for cost savings but also for reducing the environmental impact resulting from excessive energy use.
When considering a shredder with a standby mode, one of the key maintenance considerations is to ensure that the standby mode is functioning correctly. The standby mode is designed to reduce the shredder’s power usage when it is not actively shredding documents. However, if the mechanism or sensor that activates the standby mode is faulty, the shredder may continue to consume power at a higher rate than necessary, leading to increased costs and unnecessary energy waste.
Regular maintenance checks should be conducted to verify that the sensor or mechanism responsible for transitioning the shredder to standby mode is clean and free of obstructions. Dust, paper particles, and other debris can sometimes interfere with the proper operation of these sensors. If a sensor failure is detected, it should be addressed promptly to ensure that the power management benefits of the standby mode are realized.
Another maintenance consideration is to check the power settings if available. Some shredders may allow settings to be adjusted so that the time before entering standby mode can be customized. A shorter duration before entering standby can result in greater energy savings, provided it doesn’t interfere with the typical usage patterns of the shredder.
Additionally, it’s important to stay informed about the actual power consumption of the shredder during its different modes of operation. Monitoring and reviewing the power usage data can help identify any inconsistencies or usage patterns that could indicate a problem or an opportunity for further optimization of power management.
Lastly, for shredders equipped with power-saving features beyond standby mode, such as energy-efficient power supplies or auto-shutdown features, it is critical that these features are fully functional. Annual inspections or following the service recommendations provided by the manufacturer will ensure the long-term sustainability of these features and promote overall energy savings.
By paying attention to these maintenance considerations, organizations can ensure the efficient operation of their shredder, minimize operational costs, and contribute to energy conservation efforts.
Component Wear and Lubrication
Component wear and lubrication are critical factors in the longevity and efficient operation of any mechanical device, including shredders. For shredders equipped with a standby mode, maintenance considerations concerning component wear and lubrication are both proactive and preventive in nature.
The primary purpose of lubrication in shredders is to ensure that moving parts within the machine operate smoothly without excess friction, which can lead to wear and eventual failure. Appropriate lubrication reduces the resistance between these moving parts, which in turn conserves energy and extends the lifespan of the components. In shredders, the cutting blades are a primary area of focus. Regularly applying the correct type of oil or lubricant can help keep the blades sharp and prevent the accumulation of paper dust and other debris that might cause the blades to dull or jam more quickly.
For shredders with a standby mode, maintenance must also specifically consider the intervals during which the machine is not in active use. Although standby mode implies reduced mechanical activity, it does not completely eliminate the need for vigilance regarding lubrication. Over time, the lubricant can degrade or become contaminated, which underscores the importance of clean and adequate lubrication when the shredder transitions back to active use from standby mode.
Furthermore, even while in standby, components can be prone to wear due to environmental factors such as moisture or temperature changes which could affect the viscosity and effectiveness of the lubricant. Regular checks and replenishments of lubricant can help mitigate these effects.
Maintenance for shredders with a standby mode should also include scheduled inspections to identify any signs of wear or potential issues early on. This includes not only checking the lubricant levels but also inspecting the cutting blades, gears, bearings, and other moving parts for wear or damage. Keeping a log of maintenance activities and component replacements can be helpful for tracking wear patterns and anticipating future maintenance needs.
Understanding the shredder’s operating manual is essential as it often details the manufacturer-recommended lubrication type and schedule specific to the model. The type of material being shredded and the frequency of use will influence maintenance frequency and procedures. A practice of scheduling regular maintenance, rather than waiting for signs of wear or failure, will help ensure that a shredder equipped with a standby mode remains reliable and efficient over the long term.
Operational Readiness and Compliance
Operational readiness and compliance in the context of a shredder equipped with a standby mode primarily involve ensuring that the shredder is always ready for use while meeting the necessary safety and operational standards set by industry regulations and company policies.
Starting with compliance, shredders must adhere to various regulations that could include safety standards to prevent accidents and data protection laws to ensure the proper destruction of sensitive information. It is vital for organizations to regularly review these regulations and confirm that their shredder is not only compliant but also that staff are trained on how to operate the machine within these guidelines. For example, some shredders are designed to destroy specific materials or data to a particular standard, such as the DIN 66399 standard for paper shredders, dictating the size and shape of the particles after shredding. Failure to comply can lead to significant legal repercussions, especially concerning data protection and privacy laws.
Operational readiness refers to the shredder’s ability to function efficiently and effectively when needed. This involves routine checks on the shredder’s functionality and condition, preferably each time before use, especially if it is not used frequently. Standby mode can be helpful in maintaining operational readiness by reducing the initial start-up time, ensuring that the shredder can begin operating quickly when activated. However, even in standby mode, components can deteriorate over time, so inspections are critical to detect potential issues before they escalate into more significant problems.
Maintenance considerations for a shredder with standby mode:
1. **Electrical Components Check:** Regularly test and ensure that the electrical components, especially those involved in the standby mode, are functioning correctly. Over time, standby circuits can fail, which may prevent the shredder from becoming operational when needed.
2. **Mechanical Inspection:** Even in standby mode, mechanical components may encounter issues due to prolonged inactivity. Periodically run the shredder to ensure gears, cutting blades, and other moving parts are moving freely and not seizing up.
3. **Software Integrity:** For shredders that include software components, it’s important to ensure that these systems are up-to-date and functioning correctly. Software faults can cause a shredder to malfunction, including failure to wake from standby mode.
4. **Ready-to-Use Checks:** Regularly ensure the shredder is not only in standby mode but also is stocked with supplies (such as shredder oil or bags) as needed and is clear of any jams or remnants from the last use.
5. **Security Protocols:** Ensure that the standby mode does not compromise any of the security features of the shredder. Sensitive information should not be at risk due to the machine being readily accessible or not fully shutting down after use.
6. **Energy Consumption Monitoring:** While standby modes often save power, they do still consume energy. Organizations should monitor electricity usage to ensure that the cost of operating in standby mode does not offset the benefits of operational readiness.
By considering these maintenance factors, organizations can ensure that their shredders remain both compliant and operationally ready, offering a balance between energy efficiency, usability, and adherence to regulatory standards. Regular assessments and servicing of shredders guarantee their reliability whenever they are needed, whether they have been inactive or in standby mode.
Software and Firmware Updates
Software and Firmware Updates are critical aspects of maintaining a shredder with a standby mode. The software and firmware in a shredder control how the device operates, including how it enters and exits standby mode. Manufacturers regularly release updates to this software, which can enhance the shredder’s functionality, fix known bugs, and provide improved security measures. Staying up-to-date with the latest versions is essential for ensuring that the equipment operates efficiently and securely.
Maintenance considerations for a shredder equipped with a standby mode should include routine checks for software updates. Owners should follow the manufacturer’s instructions for updating the system, as this process can vary between different models and brands. Ignoring software updates can leave the shredder vulnerable to emerging threats, expose it to potential malfunctions, and may even reduce its overall lifespan.
Moreover, firmware updates may also include improvements in power management, which can enhance how the shredder handles standby mode, possibly leading to energy savings. Since the shredder is designed to switch to a low-power state when not actively shredding documents, proper software functioning is vital to ensure that this transition is smooth and effective in preserving energy.
Another essential consideration is compatibility. Sometimes, updates in software and firmware can also ensure compatibility with newer hardware components if replacements or upgrades are necessary. Therefore, maintaining current software and firmware versions can ensure that if components within the shredder need to be serviced or upgraded, they will operate correctly with the rest of the system.
Regular upkeep and review of update logs are advisable, ensuring that the shredder’s software is not only current but also that past updates were successful and didn’t introduce new issues. In many cases, software and firmware updates can be scheduled outside of normal business hours to minimize disruption, a luxury allowed by advanced planning and awareness of the shredder’s maintenance schedule.
Finally, while updating software and firmware, it’s crucial to keep records of the updates applied. Documentation of the updates can provide a maintenance history that can be useful for troubleshooting future issues and ensuring that all systems are running on compatible and up-to-date versions of their operating software.
In summary, staying current with software and firmware updates is an integral part of maintaining a shredder with standby mode. It ensures that the shredder functions efficiently, remains secure, and operates in an energy-conscious manner. Regular maintenance and a proactive approach to managing these updates can save time, reduce costs, and prolong the lifecycle of the shredding equipment.
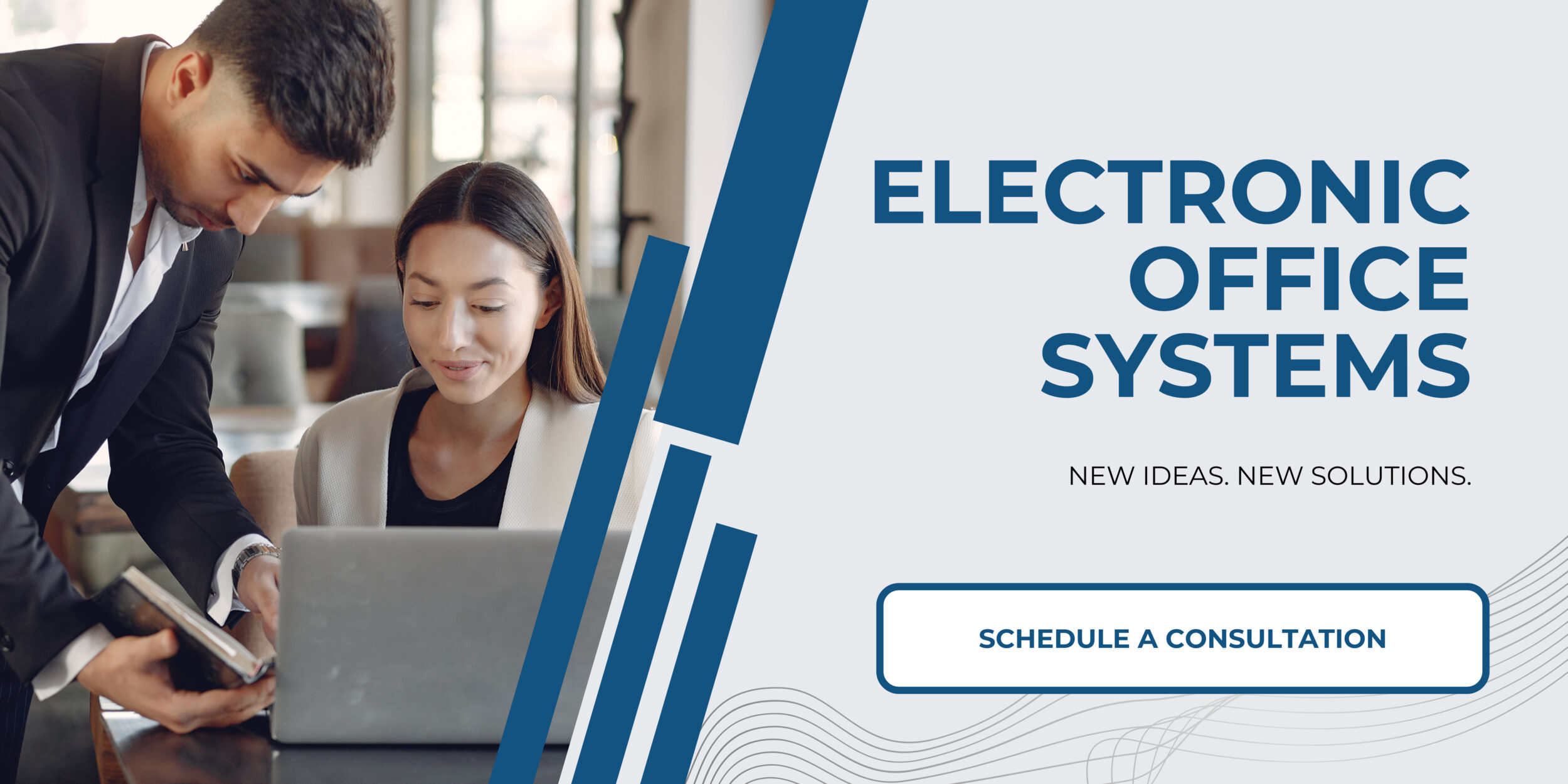
Debris Management and Cleaning Procedures
Debris management and cleaning procedures are crucial aspects of maintaining a shredder to ensure its efficient operation and longevity. When a shredder is used regularly, it tends to accumulate small bits of paper, paper dust, and other materials that can interfere with its functionality. Over time, this debris can build up and cause jams, reduce the efficiency of the shredding mechanism, and even lead to the premature wear of shredder components.
Implementing proper cleaning procedures can prevent these issues. It typically involves routinely unplugging the shredder, removing any excess paper or debris from the cutting blades, and using specialized cleaning sheets or solutions designed for shredders. This could also entail oiling the cutting blades to keep them moving smoothly—especially for cross-cut shredders which cut paper into smaller pieces and can be more susceptible to jamming and wear.
In addition to the mechanical cleaning, the waste bin of the shredder needs to be regularly emptied to prevent overflow, which can cause jams at the entry point of the shredder. More advanced shredders with automatic cleaning cycles and anti-jamming technologies still require periodic checks as these features do not eliminate the need for maintenance altogether.
For shredders with standby modes, maintenance considerations also include managing the shredder when it is not actively in use but still powered on. Standby mode is a power-saving feature that allows the shredder to remain on without running its motor, ready to activate when needed. While this mode is advantageous in terms of energy conservation and ease of use, it is important to ensure that the shredder does not remain in standby mode for extended, unnecessary periods, which can still contribute to power consumption.
Moreover, because standby mode indicates that the shredder is still on, users should ensure that the shredder’s cutting heads are clean and free from debris before it goes into standby. This prevents any remaining material from hardening on the blades, which could cause operational issues when the shredder is next used. Additionally, it’s also advisable to disconnect the shredder from power after cleaning and when not in use for extended periods to reduce wear on electronic components and to save energy.
Overall, maintaining a shredder in good working condition involves not just addressing debris management and cleaning procedures, but also understanding how features like standby mode contribute to ongoing maintenance needs. This can help extend the lifespan of the shredder and maintain its effectiveness.