Title: The Art of Wide Format Vinyl Printing: Techniques and Technologies
Introduction:
In the ever-evolving world of digital printing, the ability to create striking and durable prints on vinyl has bolstered the printing industry with a versatile medium known for its resilience and vibrancy. Wide format vinyl printing, in particular, stands out for its capacity to produce large-scale graphics that capture eyes from a distance—be it for vehicle wraps, outdoor banners, or storefront signage. This process harnesses the power of wide format printers, complex machinery that marries the intricacy of digital art with the robust nature of vinyl material.
The implementation of vinyl printing on such a grand scale demands a blend of precision, technical know-how, and artistic skill. Initially, this process begins with a careful design phase, where graphic designers tailor their creations to the expansive canvas that wide format printers offer. The printers themselves are technological marvels, equipped to handle and flawlessly print onto vinyl sheets that can span several feet in both width and length. The choice of vinyl type, from cast to calendared, hinges on the application’s needs and expected longevity, balancing cost and functionality.
As we delve deeper into the process of vinyl printing on wide format printers, it is paramount to chart the course from digital designs to tangible, eye-catching displays. This includes detailing the intricacies of the printing technique—whether it’s solvent, eco-solvent, UV, or latex ink being utilized. Each ink type brings with it distinct characteristics and use cases, affecting durability, environmental impact, and image quality. Moreover, understanding the specifics of print-and-cut systems, color profiling, and finishing processes highlights the comprehensive nature of vinyl printing that ensures a professional outcome.
By examining the sophisticated orchestration of state-of-the-art printers, cutting-edge inks, and premium materials, this article will provide a comprehensive introduction to the dynamic world of wide format vinyl printing. We will explore how this printing method has become integral to the advertising, branding, and custom signage industries, and why it remains a coveted choice for producing high-impact visual communication.
Preparing the Design File
Preparing the design file is the initial and arguably one of the most crucial steps in the process of vinyl printing using a wide format printer. This essential first item involves the creation or obtaining of a digital design that will be printed onto the vinyl material. As the foundation for the finished product, the design file needs to be carefully considered and optimized for the printing process.
To start, the design is typically created using graphic design software such as Adobe Illustrator, Photoshop, or CorelDRAW. These programs allow designers to create complex graphics with multiple layers, colors, and intricate details. For a design to be print-ready, it must meet several criteria:
1. Resolution: The image or graphic must be of high resolution, usually 300 dots per inch (DPI) or higher, to ensure clarity and sharpness when printed, especially at large sizes.
2. Color Mode: While on-screen designs are created in RGB color mode, a design file for printing should be converted to CMYK mode, which is what printers use to create the full spectrum of print colors.
3. File Format: The finalized design should be saved in a format that is compatible with the printing software. Common formats include .pdf, .ai, .eps, and .tiff files.
4. Cut Lines: If the design will be cut after printing (for decals or stickers, for instance), cut lines or contours must be added to the design file to guide the cutting equipment.
5. Bleed: An additional margin around the design (typically about 0.25 inches) ensures that no unprinted edges occur if there is any misalignment while cutting the vinyl.
Once the design file is ready, it should be thoroughly checked for any errors or issues that could affect print quality. It’s a good practice to proofread all text, check color consistency, and ensure that all elements are positioned correctly within the file. This attention to detail in the preparation phase can save time, resources, and prevent the need for costly reprints due to design errors.
### How Vinyl Printing is Performed on a Wide Format Printer
Vinyl printing on a wide format printer involves multiple steps and precise execution to achieve high-quality results. A wide format printer, distinctly larger than standard printers, is capable of handling various types of media including sheets and rolls of vinyl up to a certain width, which could range from 18 inches up to 100 inches or more. Here is how the vinyl printing process is generally performed:
1. **Setup of the Printer**: Before starting the printing process, the printer must be set up correctly. This involves loading the vinyl material into the printer and ensuring it is properly aligned. The rollers must apply the right amount of pressure to feed the vinyl through the printer without any skew or slip.
2. **Ink Selection and Configuration**: Depending on the printer model and the requirements of the print job, different types of inks can be used, such as solvent, eco-solvent, UV, or latex inks. These have various properties concerning durability, drying time, and color vibrancy. The settings for color density, drying time, and print speed need to be adjusted according to the type of ink being used.
3. **Printing the Design**: Using the prepared design file, printing can commence. The printer interprets the digital design and begins to apply ink to the vinyl substrate. Wide format printers typically use a method called inkjet printing, which is a non-contact process that involves spraying tiny droplets of ink onto the vinyl to form the image.
4. **Quality Checks**: Throughout the printing process, quality checks are often performed to ensure that the colors are correctly reproduced and that there are no issues such as streaking, banding, or other imperfections.
5. **Drying/Curing**: After the printing is complete, the ink must thoroughly dry or cure. Some printers have built-in dryers or UV lights to cure the ink instantly. However, some inks may still require an additional period to dry completely, which is crucial before moving on to any finishing processes.
6. **Finishing**: The final steps of the printing process may include lamination to protect the print and add durability, as well as cutting to the desired shape and size. The finishing process can significantly enhance the longevity and professional look of the printed vinyl.
Wide format vinyl printing requires a combination of technical knowledge, attention to detail, and an eye for design. Each step, from preparing the design file to the finishing touches, contributes to the overall quality and effectiveness of the final printed media.
Loading and Setting Up the Vinyl Material
Loading and setting up the vinyl material is a crucial step in the process of creating high-quality vinyl prints using a wide format printer. Before one can start the printing, the correct type of vinyl must be chosen. Vinyl comes in various types, weights, and finishes, and each is suited for different applications. For outdoor signage, a more durable, weather-resistant vinyl would be appropriate, while for indoor decorations, a lighter, more flexible vinyl could be preferred.
Once the right vinyl material is selected, it must be properly loaded into the wide format printer. This involves making sure the vinyl is free of any dust or particles that might interfere with the print quality. The material is then aligned and fed into the printer’s media feed path to ensure that it moves smoothly without any skewing or wrinkling during the printing process. This is imperative because any misalignment can lead to wastage of material and poor-quality prints.
In addition, tension on the vinyl must be adjusted correctly. Too much tension can cause the vinyl to stretch or distort the image, while too little tension might lead to the material bunching up and potentially causing a printer jam. Ensuring that the vinyl is perfectly taut will help in achieving a high-quality print.
Wide format printers are capable of printing on vinyl by dispersing ink onto the vinyl surface in precise patterns and colors to replicate the desired design. The process begins with the creation of the design in a digital format, after which the design file is sent to the printer. In the case of vinyl, special inkjet inks are used, which are specially formulated to adhere to the vinyl surface and are durable enough to withstand exposure without fading or scratching easily.
The printer applies ink to the vinyl in swathes, much like a traditional paper printer, but on a larger scale. This technology allows for high-resolution graphics and vibrant full-color images. Depending on the setup and the printer model, printing on vinyl may require specific print heads suitable for the type of ink used and the print material. Most wide format printers are equipped with technology that ensures droplets of ink are piezoelectrically or thermally jetted onto the vinyl in precise locations.
Once the print has begun, it is essential to monitor the process to ensure there are no issues with ink distribution or vinyl movement. After printing is complete, the vinyl often needs to dry before it can be handled or further processed. The drying time can vary depending on the type of ink and vinyl used, as well as on environmental factors such as temperature and humidity.
Overall, the careful preparation and loading of vinyl material help ensure the efficient and high-quality output of wide format printers. Technological advancements continue to refine the process, making it more accessible and preferable for various applications due to its durability and versatility.
Configuring the Wide Format Printer Settings
When addressing the third step of the printing process, Configuring the Wide Format Printer Settings, it is essential to understand the intricacies involved to ensure a high-quality print. This stage is crucial because the settings will determine how accurately the design is transferred onto the vinyl material.
Wide format printers typically accommodate a variety of media types and sizes, which requires precise calibration for each specific job. Printer settings must be adjusted according to the type of vinyl being used (e.g., cast, calendared, clear, or colored) and the required level of print quality. Key settings include the resolution, which may be measured in dots per inch (DPI), and the printing mode, such as standard, high-quality, or draft, each offering a balance between print quality and speed.
Moreover, color management is an integral part of this process. Printers often use CMYK color models for vinyl printing, and ensuring the correct configuration is essential for color accuracy. Printer profiles should be selected or created that match the printer, ink, and vinyl combination to achieve the desired results. Additionally, the ink saturation and drying times may need adjustments depending on the material and environmental conditions.
Print speed and the heating or curing settings should also be configured correctly. Some wide format printers utilize heated beds or pre-heating options to ensure the vinyl is at an optimum temperature for receiving the ink. This reduces the likelihood of smudging and aids in the immediate curing of the ink, ensuring that the print is resilient and the colors are vibrant upon completion.
Now, addressing the specific process of vinyl printing on a wide format printer, the technique revolves around transferring a digital image onto the vinyl substrate. The process begins by loading the vinyl roll into the printer. Once the material is set up and the design file is prepared, the printer’s settings are configured to suit the vinyl type and the desired quality of the print.
Wide format printers intended for vinyl printing often use eco-solvent, solvent, UV, or latex inks because of their durability and resistance to outdoor elements. During the printing, the printer head moves back and forth across the material, dispensing tiny droplets of ink that form the image. The precision of the printer head movements and the droplet sizes are determined by the printer’s resolution settings, which can be quite high to achieve sharp and detailed prints.
After the printing is done, depending on the type of ink used, the vinyl may go through a drying or curing phase. Solvent inks will need time to outgas, while UV-cured inks will be exposed to ultraviolet light to set the ink immediately. Latex inks, on the other hand, are dried and cured within the printer using internal heaters.
In conclusion, configuring the wide format printer settings is a complex task that significantly impacts the final quality of the vinyl print. Every adjustment made during this stage can influence the detail, color fidelity, and durability of the printed material. It’s a step that requires proficiency with the specific printer model being used and a deep understanding of how changes to these settings affect the vinyl printing process.
Printing Process and Ink Application
The printing process and ink application is a crucial step in the production of vinyl graphics using a wide-format printer. This is item 4 on your provided numbered list, which comes after the design file has been prepared, the vinyl material has been loaded and set up, and the printer settings have been configured.
Once the design file is ready and the vinyl material is properly positioned in the wide-format printer, the actual printing can begin. The printer uses a particular type of ink that is suitable for the vinyl material to ensure good adhesion, durability, and color quality. Most wide-format printers used for vinyl printing feature either solvent, eco-solvent, latex, or UV-curable inks, each with specific characteristics that make them ideal for outdoor signage, banners, vehicle wraps, and more.
During the printing process, the wide-format printer applies ink to the vinyl surface in a controlled manner. The print heads move back and forth across the material, releasing tiny droplets of ink in a precise pattern defined by the digital design file. The inks are formulated to spread slightly upon contact with the vinyl, merging with adjacent droplets to form a continuous, high-resolution image.
In terms of the operation, the printer is typically governed by RIP (Raster Image Processor) software. This software interprets the digital design and translates it into a language the printer can understand, adjusting the color management, print resolution, and media feed rate for optimal results.
For solvent and eco-solvent inks, the printed vinyl needs to outgas for a certain period, which allows the solvents to evaporate before the material can be laminated or applied. For latex and UV-curable inks, outgassing is not required or much reduced, allowing for faster handling and turnaround.
After the printing process is complete, the ink must be cured. Solvent and eco-solvent inks often dry over time or with the help of heaters. Latex inks are typically cured using heat, which causes them to ‘set’ and adhere to the vinyl. UV-curable inks are unique in that they are cured almost instantly when exposed to ultraviolet light during the printing process. This immediate curing makes UV prints durable and resistant to fading and scratching.
In summary, the printing process and ink application involve careful manipulation of the wide-format printer and its settings to translate a digital image onto vinyl material using ink that is compatible with the vinyl’s surface and the intended use of the final product. The choice of ink and the specific process of application and curing are critical factors in the quality and longevity of the vinyl print.
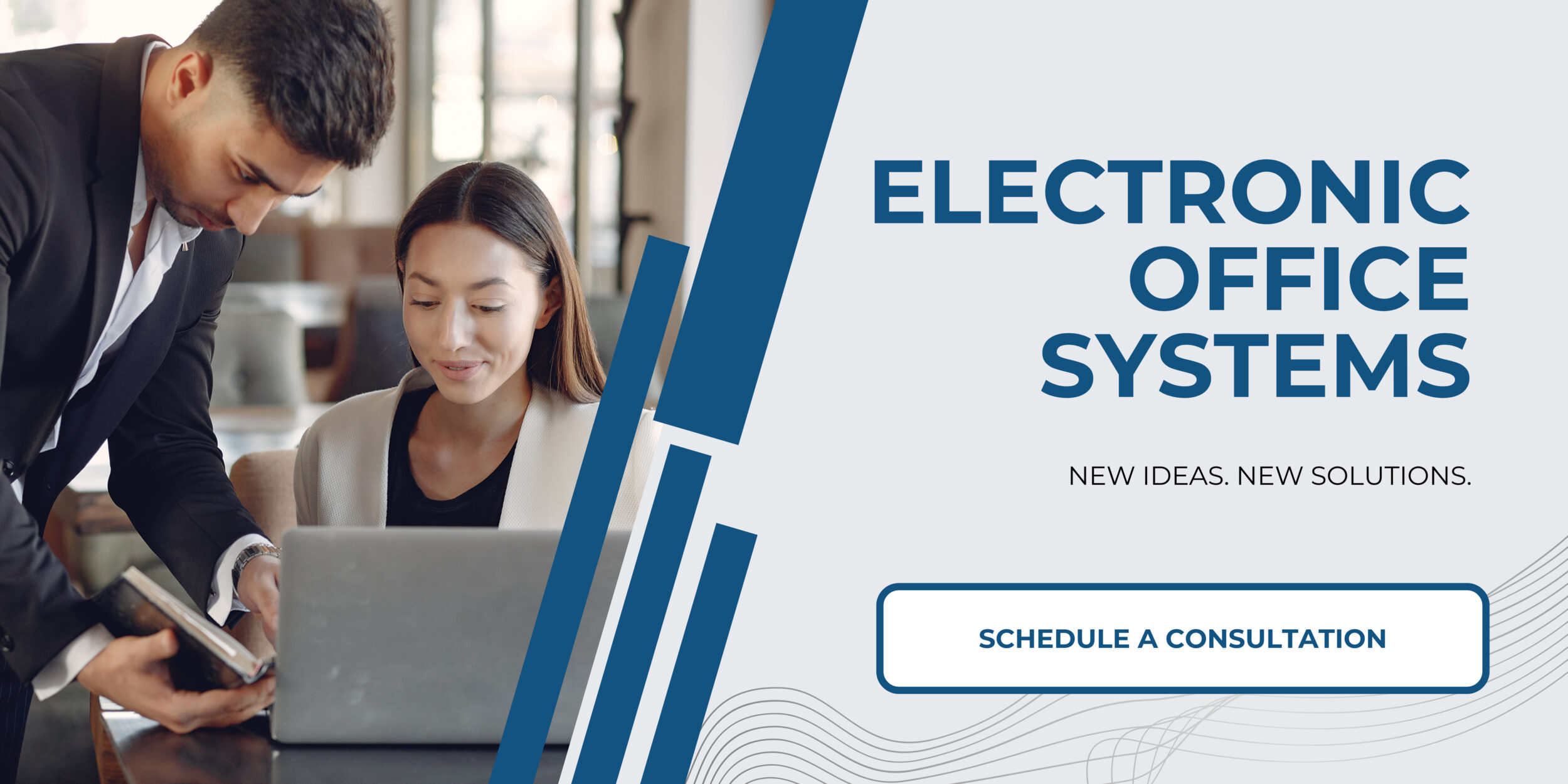
Finishing and Post-Processing Steps
Finishing and post-processing are crucial steps that come after the actual printing process in wide format vinyl printing. Once the vinyl has been printed with the desired design or image, these subsequent steps ensure the longevity, effectiveness, and visual appeal of the final product. There can be several different activities involved in finishing and post-processing, which depend on the intended use of the printed vinyl.
Firstly, after printing, the vinyl must be allowed to dry completely. Depending on the type of ink used (such as solvent, eco-solvent, UV, or latex inks), this drying time can vary. Some wide format printers have built-in dryers to expedite this process. Once the ink is dry, the vinyl is often subjected to a lamination process. Lamination provides a protective layer over the print, guarding against UV rays, scratches, and the weather, thereby extending the life of the print and maintaining the vibrancy of the colors.
Cutting is another crucial post-processing step. Printed graphics often need to be cut to size or into specific shapes, which can be achieved with a variety of tools, from manual cutters to sophisticated contour cutting machines that can follow the shape of the design with precise accuracy.
Additionally, some forms of vinyl intended for use as decals or stickers will require the application of a transfer tape, which aids in the application of the print by keeping small parts or letters in place while the adhesive side of the vinyl is exposed and applied to the desired surface.
After all of these finishing and post-processing steps are completed, the final product is inspected for quality assurance. Only after passing rigorous quality checks are the finished items packaged and dispatched for installation or delivery to the customer.
Now, how is vinyl printing performed on a wide format printer? The process starts by translating the design from a digital file to a format that the printer can interpret. The vinyl material is then carefully loaded onto the printer and properly aligned. The wide format printer is configured with the appropriate settings for the vinyl material being used and the desired quality of the print.
As the printing begins, the ink is applied to the vinyl in a series of passes. The process may vary depending on the technology of the printer; for instance, some printers require the vinyl to pass through the printer multiple times to apply different colors or to add additional layers of ink for a richer finish. Wide format printers used for vinyl often use UV, solvent, or eco-solvent inks that adhere to the vinyl and are durable for outdoor or indoor use. After the printing has concluded, the vinyl is dried, either through passive air drying or with the help of heaters built into the printer.
In conclusion, while printing is a core part of creating vinyl graphics or signage, it is the finishing and post-processing steps that turn a printed piece of vinyl into a durable and functional final product, ready for application to various surfaces or uses. These steps contribute significantly to the quality and durability of the final printed vinyl.