Textile printing is a transformative process that brings vibrancy and creativity to fabrics, allowing for the production of diverse patterns and designs on a plethora of textile materials. The advent of wide format printers has revolutionized this art, marrying traditional craft with cutting-edge technology to produce high-quality, intricate prints on a large scale. Wide format textile printing serves various sectors, including fashion, home décor, and advertising, offering a seamless blend of flexibility, efficiency, and customization.
The process of textile printing with wide format printers involves several critical steps, each contributing to the final quality of the printed fabric. Initially, the fabric is prepared and treated to ensure ink receptivity and color vibrancy. The pre-treatment process is often tailored to the specific type of fabric and the ink used, setting the stage for optimal print output. Subsequently, advanced inkjet technology comes into play, where printers equipped with multiple color channels emit tiny droplets of ink with high precision onto the textile substrate. These inks can be reactive, acid, disperse, or pigment-based, depending on the fabric material and the intended use of the printed textile.
Modern wide format printers are also versatile, capable of handling rolls of fabric or individual pieces, and being compatible with various textile types, including cotton, polyester, silk, and blended fibers. Crucially, after printing, the fabric undergoes post-processing steps such as steaming, washing, and drying, which are essential to fix the ink onto the fabric and ensure colorfastness and durability. The integration of digital technology in wide format printers facilitates rapid prototyping, short-run production, and on-demand printing, making textile printing more accessible and sustainable than ever before.
In the subsequent sections, we will delve into the technical intricacies of the wide format textile printing process, exploring the types of printers and inks used, the importance of fabric pre-treatment, the critical role of color management, and the environmental considerations of the practice. We will also examine the impact of this technology on the textile industry and how it fosters innovation, enabling designers and manufacturers to push the boundaries of creativity and textile application.
Types of Textile Inks Used for Wide Format Printing
Wide format printing on textiles has revolutionized the way we produce printed fabrics, ranging from fashion and apparel to home decor and beyond. The type of ink used in wide format printing is critical, as it must be compatible with both the printer and the textile substrate to ensure quality, durability, and vibrancy.
There are several types of textile inks that are commonly used with wide format printers. The most prevalent ones include:
1. Reactive Inks: These inks form a chemical bond with cellulose fibers, making them ideal for natural fibers like cotton and linen. They are known for their vibrant colors and excellent wash fastness.
2. Acid Inks: Typically used for printing on silk and nylon, acid inks penetrate the fibers and, through steaming, create a permanent bond that yields rich and bright prints with high colorfastness.
3. Disperse Inks: Disperse inks are designed for printing on polyester and other synthetic fibers. They are heat-activated and become part of the fabric’s structure, resulting in strong colors with good light and wash fastness.
4. Pigment Inks: These inks lay on top of the fabric and are fixed in place through a heat process. While they can be used on a variety of textiles, pigment inks generally offer a softer color palette and do not require pre-treatment of the fabric.
5. Dye-Sublimation Inks: Often used for printing on polyester and synthetic materials, dye-sublimation inks turn into gas when heated and then bond with the fabric. This results in prints that are resistant to fading and cracking.
When it comes to performing textile printing on a wide format printer, the process typically follows a well-defined series of steps to ensure that the finished product meets the desired quality standards. Initially, a digital design is created, which is then processed by the printing software to optimize it for the textile substrate in question.
Preparation and pretreatment of the fabric are crucial to get the fibers ready to accept the ink. The fabric is then fed into the wide format printer, where the selected ink type is applied through the printheads. In the case of reactive inks, acid inks, and disperse inks, post-processing usually involves steaming the fabric to fix the ink, followed by washing to remove any unreacted ink and ensure color fastness.
For pigment and dye-sublimation inks, the fabric is typically heat-treated—either through a heat press or an oven—to cure the ink and ensure it is permanently bonded to the textile.
The wide format textile printing process is characterized by its capacity to produce highly detailed and color-rich images, transforming plain fabric into custom-designed textiles with our desired patterns or images. Due to its versatility and efficiency, wide format textile printing continues to be a popular method in various industries, catering to both small-customized batches and large-scale production runs.
Preparation and Pretreatment of Fabrics
Preparation and pretreatment of fabrics are essential steps in the printing process, particularly when using wide format printers. Before any color can be applied, the fabric must be prepared to ensure it has the proper characteristics to receive the inks. There are several key goals in fabric preparation:
1. To clean the fabric of any impurities that might affect the quality of the print. These impurities could include dust, oils, waxes, or other substances left from the manufacturing process that could interfere with the ink’s adhesion to the fabric.
2. To ensure uniformity across the entire fabric surface. This involves making sure that the fabric is smooth and has consistent absorbency so that the ink spreads evenly without blotching or bleeding.
The pretreatment process includes several steps designed to prime the fabric. Pretreatment solutions or coatings are applied to fabrics to enhance print quality, color yield, sharpness, and wash fastness. This treatment creates a chemical bond between the fabric and the ink, improving durability and the vibrancy of the print.
Depending on the type of fabric and ink being used, the pretreatment might involve heat or steaming to activate chemicals, or a coating might be applied to help the ink adhere better. The fabric is generally rolled out flat, and the pretreatment is applied either through padding, spraying, or immersion. After the pretreatment has been applied, the fabric is typically dried to remove any excess moisture, which could affect the printing process.
When it comes to textile printing on a wide format printer, the pretreatment is also designed to stop the ink from spreading too far into the fabric, which can blur the design and reduce the sharpness of printed images. For example, in dye-sublimation printing (common for synthetic fabrics like polyester), pretreatment is key for ensuring crisp and vibrant transfer of the image.
With the continuing advancements in digital textile printing, new pretreatment mixtures and methods are being developed for various types of inks and fabrics to optimize the printing results. It’s an area of significant innovation in the sector, with the ultimate goal of achieving high-quality, durable prints with good hand feel and minimal environmental impact.
Printing Technologies and Techniques
Printing technologies and techniques are central to the process of applying designs to textiles, particularly when it comes to wide format printing. Wide format printers are made to handle large-scale print jobs that go beyond the capability of standard printing devices. In textile printing, these printers are specifically designed to accommodate various fabric types and use special inks that are appropriate for textiles.
When it comes to wide format textile printing, there are a few commonly used technologies and techniques that stand out.
**Direct-to-Garment (DTG) Printing:**
This method of printing is quite similar to how a traditional inkjet paper printer works, but it is specifically designed for fabrics. Small droplets of ink are sprayed directly onto the textile from the print head. DTG allows for intricate designs and a wide spectrum of colors, making it suitable for high-quality, detailed images.
**Dye-Sublimation Printing:**
In this technique, heat-sensitive inks are used to print onto a transfer paper. The printed image is then transferred onto the textile using a heat press. The heat converts the ink into a gas that permeates the fabric fibers, creating a durable and vibrant print. Dye-sublimation is commonly used for printing on polyester and other synthetic fabrics.
**Screen Printing:**
While this is a more traditional technique, it can also be used in conjunction with wide format printing for textiles. Screen printing involves creating a stencil (the screen), and then using that to apply layers of ink on the printing surface. Each color is applied using a different stencil, one at a time. Although it is not as efficient for highly detailed images or prints with many colors, screen printing is economical for large-run orders.
Wide format printers for textile printing usually operate with either piezoelectric or thermal inkjet print heads. The piezoelectric print heads use vibration to push ink out of the nozzle, which allows for more precise control over the drop size and print resolution. Thermal inkjet heads, on the other hand, use heat to create a bubble in the ink chamber that forces a droplet of ink from the nozzle.
Given the textile nature of the medium, special considerations in the printing process need to be accounted for, such as fabric feeding mechanisms to ensure the material passes evenly through the printer, and ink curing methods to ensure color fastness and durability.
Additionally, the inks used for wide format textile printing are specifically formulated to ensure proper adhesion to fabrics, color accuracy, and print longevity. These inks include reactive inks, acid inks, disperse inks, and textile pigment inks, each suitable for different types of fabric and application requirements.
The process of textile printing on a wide format printer involves more than just selecting the right technology; it necessitates an understanding of the fabric’s properties, the desired outcome, and the operational aspects of the machinery. Mastery in these areas results in printed textiles that are both stunning in appearance and durable in function.
Post-Processing and Finishing Steps
After the textile has been printed on a wide format printer, the post-processing and finishing steps are crucial to set the ink and ensure the durability and quality of the print. These steps are essential to enhance the visual appeal and to meet the required standards for various applications, whether it’s for fashion, home decor, or industrial purposes.
Post-processing varies significantly based on the type of ink used and the fabric. For instance, textiles printed with reactive dyes need to be steamed to fix the color, which involves exposing the fabric to high-temperature steam. This process allows the ink to react chemically with the fiber, resulting in vibrant colors that are wash-fast and resistant to fading.
Once steaming is completed, the fabric often undergoes washing to remove any unfixed ink, thickening agents, and other chemicals used during the printing process. Washing is a critical step, as it influences the softness of the hand and the final appearance of the print.
Furthermore, a series of finishing treatments may be applied to the textile. These can include softening agents to improve the feel of the fabric, flame retardants for safety, or water repellents for outdoor applications. Each of these treatments is applied with the end-use of the fabric in mind.
For textiles printed using UV-curable inks, post-processing might include exposure to ultraviolet light to cure the ink, a process that solidifies the ink and creates a bond with the fabric. This step makes the print durable and resistant to environmental factors such as sunlight and moisture.
Different wide format printers may require specific post-processing steps. Optimizing these steps is critical to ensure the best possible result for the printed textile. Careful attention to the post-processing and finishing steps is what differentiates high-quality textile products from those of lower quality and it’s pivotal for producers to maintain high standards throughout this phase.
As for textile printing performed on a wide format printer, the process involves applying ink directly onto the fabric using inkjet technology. Wide format printers are designed to accommodate larger print jobs and can handle a variety of textile substrates. The printer applies the ink in a precise and controlled manner, which is ideal for creating detailed patterns and images.
Before printing, the textile may need to be pre-treated with a primer or a fixation agent to ensure the ink adheres well to the fabric and to improve the color yield. During the printing process, the fabric is typically fed through the printer, where the heads deposit tiny droplets of ink onto the textile in the desired pattern.
After printing, as mentioned above, post-processing steps such as steaming, curing, washing, or applying specific chemical treatments are crucial to ensure longevity, color fastness, and the desired texture of the printed fabric.
Wide format textile printing has revolutionized the industry by allowing short runs, customization, and complex design reproduction with high precision and relatively low setup costs compared to traditional screen-printing methods. With ongoing advancements in technology, the capabilities and applications of wide format textile printers continue to expand.
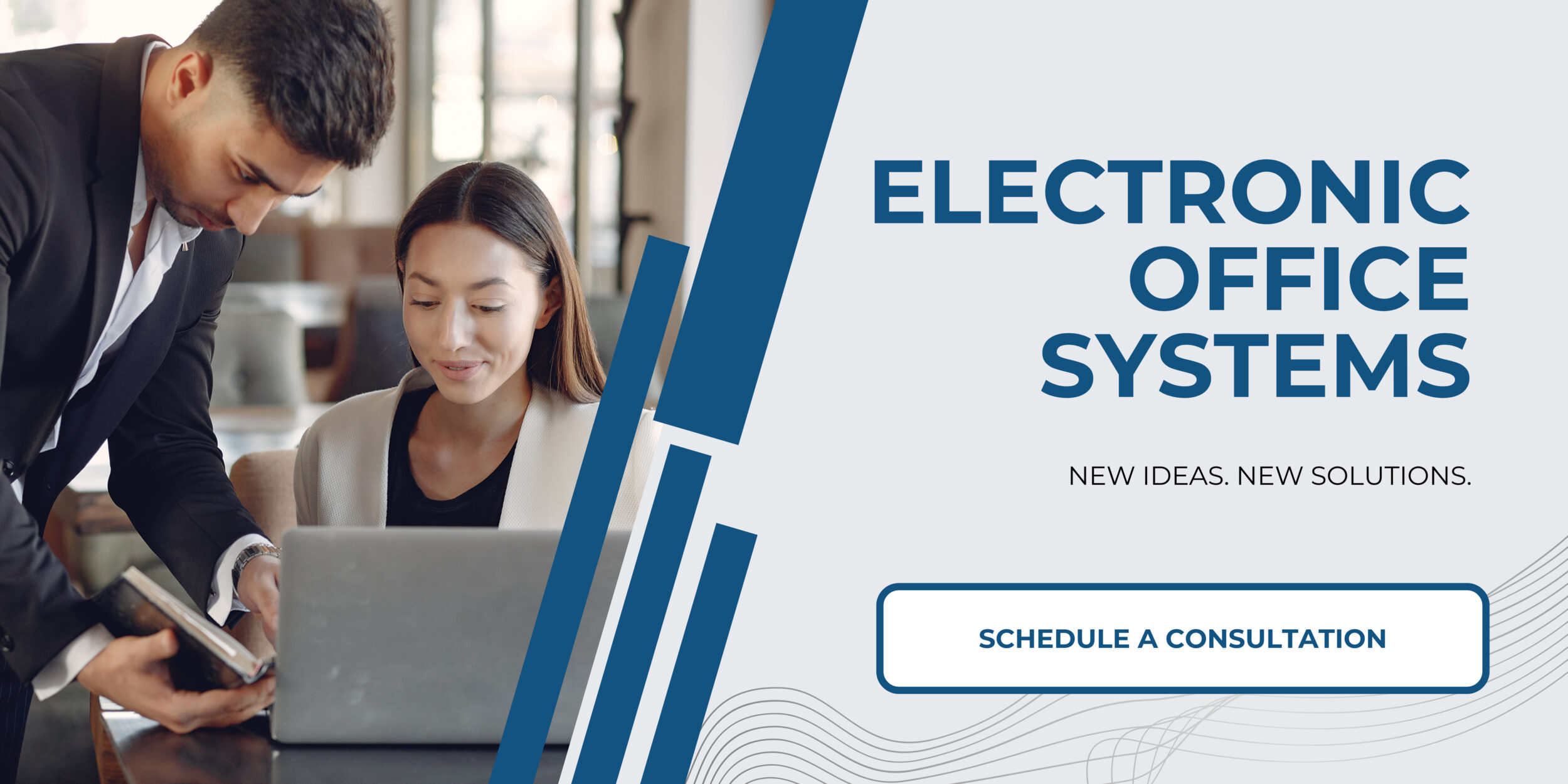
Quality Control and Testing Methods
Quality control and testing methods are critical components in the textile printing industry, especially with wide format printing. They help ensure that the printed fabrics meet specific standards and customer requirements, both in terms of aesthetics and performance. These methods encompass a variety of procedures and checks conducted at different stages of the printing process to verify the quality of the textile materials being produced.
Before initiating a full-scale print run, pre-printing tests may be conducted on the inks and fabrics to assess their compatibility. This involves colorfastness testing, which checks how well a fabric retains its color when subjected to conditions such as light exposure, washing, and rubbing. Additionally, tension testing is done to ensure the textile can withstand the stress of going through the printer without distortion.
Once the printing process begins, in-line inspections are often used to detect any defects as early as possible. High-resolution cameras and sensors can be utilized to monitor the print in real time. This helps identify issues such as nozzle clogging, misalignment, or streaking, which can be corrected immediately to mitigate waste and reduce the incidence of printing faults.
After printing, the textiles are usually subjected to post-processing treatments such as steaming, washing, and heat setting to ensure the durability and permanence of the prints. Following these treatments, further quality checks are executed. For instance, a rub test might be carried out to verify the resistance of the printed design against wear and abrasion.
Other tests include inspecting for uniformity and repeatability of prints, particularly important for patterned fabrics where continuous design alignment is crucial. The sharpness of edges, color consistency across the batch, and the textile’s general appearance are all scrutinized to ensure they meet quality standards. Metamerism checks could also be performed to guarantee that colors appear consistent under different lighting conditions.
The final approval often includes a detailed evaluation against a control sample or specification sheet to ascertain that the final product meets all the established criteria. Only after passing all these tests and inspections is the fabric cleared for dispatch to customers.
Regarding how textile printing is performed on a wide format printer, the process involves several steps. First, the proper type of textile ink needs to be selected based on the fabric composition and desired outcome. The fabric itself has to be pretreated if necessary to accept the ink. The pretreatment often includes applying a special coating that helps the ink bond with the fabric fibers, particularly for synthetic fabrics.
Then the textile is loaded onto the printer, which is equipped to handle large widths of fabric. Wide format printers use different inkjet printing technologies, such as sublimation (where ink is transferred and bonded to the fabric via heat), reactive dye printing, or direct disperse printing, depending on the application. The designs are then printed onto the fabric, with special attention to ensure consistent color and pattern accuracy.
After printing, the fabric is typically finished with heat or steam to fix the dyes into the fibers and to remove any excess ink, ensuring color permanence and washfastness. The fabric can undergo additional finishing processes, including brushing, cutting, or coating, depending on the end-use requirements.
Throughout the entire wide format textile printing process, quality control and testing methods are integral to maintain standards and to ensure the final product performs as expected.