When it comes to ensuring the longevity and optimal performance of electronic devices and machinery, understanding the concept of ‘Duty Cycle’ is of paramount importance. A duty cycle is a measure of the operational “on” time of a machine or device, expressed as a percentage of the total time within a given period. It is a critical factor that can influence decisions about how and when a device should be used, and more importantly, how it should be maintained. In this comprehensive introduction, we will explore how the duty cycle impacts device usage and the scheduling of maintenance, thereby providing insights into better management and efficient operation of equipment across different industries.
Devices with high duty cycles are often subject to more wear and tear, as they are in active use for a more significant proportion of time. Consequently, these machines require more frequent maintenance to prevent breakdowns and extend their service life. Conversely, devices with low duty cycles tend to experience less stress, indicating that maintenance can be scheduled less often. Understanding the intricacies of the duty cycle allows for the optimization of resources and enhances reliability by preventing unexpected failures.
The interplay between duty cycle, device usage, and maintenance scheduling is also critical from an operational continuity and budget efficiency standpoint. Proper planning can ensure that devices are not overused, potentially resulting in overheating or failure, which could lead to costly downtime and repairs. Similarly, regular maintenance timed according to the device’s duty cycle can forestall significant overhauls and replacements, ensuring that expenditures are kept in check. For organizations that rely heavily on machinery and devices, this triad of considerations is not just a technical concern but a business imperative.
In this article, we will delve into how organizations can best calibrate their device usage practices and maintenance schedules in response to the duty cycles of their assets. From industrial manufacturing equipment to office printers and IT servers, we will provide insights into maximizing efficiency and reliability through strategic duty cycle management. This knowledge is not only vital for the operational staff and technicians responsible for the day-to-day running of equipment but also for the decision-makers who must balance the needs of production with the costs of maintenance and equipment lifecycle management. Join us as we untangle the complexities of duty cycle considerations and provide actionable strategies for businesses seeking to optimize their operations.
Understanding Duty Cycle Specifications
Duty cycle specifications are crucial for users to understand as they indicate the expected performance parameters under which a device or machinery is designed to operate. The duty cycle is typically expressed as a percentage and represents the ratio of time a piece of equipment can run compared to the total time it should be allowed to rest within a given period. For instance, a duty cycle of 40% for a motor might mean that it can run continuously for 4 minutes and then needs to cool down for 6 minutes in a 10-minute cycle.
Understanding these specifications is vital because it prevents the overuse of equipment, which can lead to overheating, increased wear and tear, and ultimately, premature failure. When devices are run beyond their duty cycles, harmful consequences may arise, which could otherwise be avoided through adherence to specified operating limits.
How duty cycle factors into decisions about device usage and scheduling maintenance hinges on its direct relationship with the operational stress placed on the equipment. When a device is used at or near its maximum duty cycle, it is likely to experience higher levels of heat and mechanical stress. Over time, these stresses can lead to degradation of components such as bearings, motors, and drives, necessitating more frequent maintenance or replacement.
By incorporating duty cycle considerations into maintenance scheduling, potential downtime can be reduced, and device longevity can be enhanced. For example, machines operating at higher duty cycles may require more frequent lubrication, part inspections, or cooling periods to mitigate the effects of the continuous operation. Scheduling maintenance tasks based on the actual usage patterns, rather than fixed time intervals, could lead to more efficient maintenance programs that better correlate with the equipment’s operational demands.
Moreover, by respecting the duty cycle limitations, users can plan workflows to optimize the use of equipment. This includes spacing out demanding tasks to avoid continuous operation at peak duty cycle, thus minimizing strain on the machinery. For companies that run multiple shifts, understanding duty cycles is also essential for balancing workloads across different teams to evenly distribute the wear on equipment and avoid overburdening any single device.
In essence, duty cycle specifications should be an integral part of the decision-making process when it comes to device usage and the scheduling of maintenance. It enables a proactive approach to equipment management, ensuring reliability, performance consistency, and longevity of the assets within an operation.
Impact of Duty Cycle on Device Performance and Longevity
The duty cycle of a device refers to the ratio of time the device is active as opposed to the time it remains idle or off. Specifically, it indicates the percentage of time a machine or component is in operation during a specific period. The impact of the duty cycle on device performance and longevity is significant and multifaceted.
When a device has a high duty cycle, it is in use for a predominant portion of the time, which can lead to increased wear and tear on its components. This heightened usage level can result in the generation of heat and mechanical stress, both of which are critical factors that contribute to the wear of parts and potential failure. As materials are subjected to continual or intense cycles of heating and cooling, or start-stop operations, their performance can degrade more quickly over time. For example, a motor running at near its maximum duty cycle continuously may have a much shorter lifespan than one running at a moderate duty cycle, simply due to the increased physical demands placed on the system.
On the other hand, a device with a low duty cycle will have more periods of rest or lower operational intensity, potentially allowing for better recovery and less strain on its components. This can result in fewer maintenance needs and a longer life expectancy, assuming that the device is used within its intended specifications.
The duty cycle should be a central factor in decisions regarding both the usage and the scheduling of maintenance for devices. When planning the use of a device, one should consider whether the intended use falls within the recommended duty cycle limitations to avoid premature equipment failure. Consistently operating equipment beyond its duty cycle can lead to more frequent breakdowns and a decrease in operational efficiency.
Additionally, a proactive approach to scheduling maintenance based on the duty cycle can significantly improve a device’s performance and longevity. Understanding the stress that the duty cycle imposes on a device helps in determining the timing of preventive maintenance. Components subject to high duty cycle operation may need to be inspected, serviced, or replaced at shorter intervals to prevent unexpected downtime and the potential damage that could result from component failure.
In conclusion, the duty cycle is an essential factor to consider for anyone responsible for managing the usage and maintenance of devices. By respecting the duty cycle specifications and by planning maintenance activities in accordance with the operational stresses it imposes on devices, one can enhance both performance and longevity, ensuring more reliable operation and greater efficiency over the life of the equipment.
Duty Cycle Considerations in Preventive Maintenance Scheduling
Duty cycle considerations play a significant role in preventive maintenance scheduling for various types of equipment and machinery. The duty cycle of a device refers to the amount of time the device is expected to operate compared to the time it is designed to be in use within a certain period. In simpler terms, it’s the ratio of operating time to the total time, often expressed as a percentage. By understanding the duty cycle of a device, maintenance teams can predict when wear and tear will occur, allowing them to schedule maintenance activities proactively to avoid unexpected downtime and extend the life of the equipment.
When scheduling preventive maintenance, it is vital to factor in the duty cycle since different machines will experience stress and wear depending on their usage patterns. For example, a motor that operates continuously at full capacity (100% duty cycle) will require more frequent maintenance checks and parts replacement than one running at 50% duty cycle, which would have periods of rest and less overall stress on its components.
Maintenance schedules can be optimized by analyzing the equipment usage patterns and the environmental conditions under which they operate. Equipment running under more demanding conditions (e.g., higher loads, temperatures, or in corrosive environments) albeit for the same duty cycle, may degrade faster and subsequently require more frequent maintenance. Furthermore, duty cycle irregularities, such as periods of overuse, can accelerate equipment wear and failure, highlighting the need for maintenance scheduling that takes into account not just the average duty cycle, but peak usage periods as well.
Considering the duty cycle when planning preventive maintenance also involves assessing the criticality of the equipment within the operation. Essential machinery that would cause significant interruptions in workflow if it failed would necessitate more conservative maintenance intervals. On the other hand, less critical equipment may follow a more lenient schedule, balancing maintenance costs with the risks of downtime.
Moreover, duty cycle considerations in maintenance scheduling are not only about ensuring the functionality and reliability of equipment but also about safety. Machines that are overused or not properly maintained can pose serious risks to operators and the facility. Implementing a preventive maintenance schedule that respects the designed duty cycle of the equipment helps mitigate these risks by ensuring that machines operate within their safe operating conditions.
In conclusion, the duty cycle is a fundamental factor that should be integrated into the decision-making process for preventive maintenance scheduling. It informs the maintenance intervals, the expected wear on components, and helps in balancing the operational demands with the longevity and reliability of the equipment. By tailoring maintenance protocols around the duty cycle, facilities can achieve efficient operations, prolong the life of their assets, and uphold safety standards.
Role of Duty Cycle in Predictive Maintenance and Condition Monitoring
The duty cycle of a device refers to the ratio of its operational time to the total time under consideration, often expressed as a percentage. It represents how intensively a device is being used. In terms of predictive maintenance and condition monitoring, the duty cycle plays a crucial and multifaceted role. Predictive maintenance is a strategy that relies on the real-time monitoring of equipment conditions to predict when maintenance should be performed. Condition monitoring, which is a key component of predictive maintenance, involves the continuous assessment of machine states to identify any changes that may indicate a decline in performance or an impending failure.
Understanding the duty cycle is essential in predictive maintenance because it directly affects the wear and degradation rate of components. For example, a motor with a high duty cycle is in operation for a longer portion of the cycle and, thus, accumulates wear and tear faster than a motor with a lower duty cycle. This means maintenance activities such as lubrication, parts inspection, or replacement may need to be scheduled more frequently for higher duty cycle equipment to prevent unexpected breakdowns and maintain optimal functioning.
The analysis of duty cycle data, often in conjunction with other variables such as temperature, vibration, and noise levels, allows maintenance teams to develop a more accurate prediction of equipment lifespan and failure points. By tracking these parameters, they can catch issues before they become significant problems and can plan maintenance activities during scheduled downtimes, thus minimizing the impact on production.
Furthermore, integrating the duty cycle into scheduling maintenance ensures that the recommendations provided by predictive analytics tools are contextually accurate. This integration leads to smarter decision-making regarding when and how to service equipment. Without considering the duty cycle, there could be a disconnect between the predicted maintenance schedule and the actual usage pattern of the machine, possibly leading to over- or under-maintenance.
In summary, the duty cycle is an integral part of the data set required for effective predictive maintenance and condition monitoring. By accommodating the specific usage patterns of equipment within these strategies, organizations can not only anticipate potential failures and plan maintenance to avert downtime but also optimize the life expectancy of their assets and ensure safe, efficient, and uninterrupted operation. Consequently, when deciding on device usage patterns and scheduling maintenance, duty cycle considerations help to avoid unnecessary costs and preserve the health of equipment.
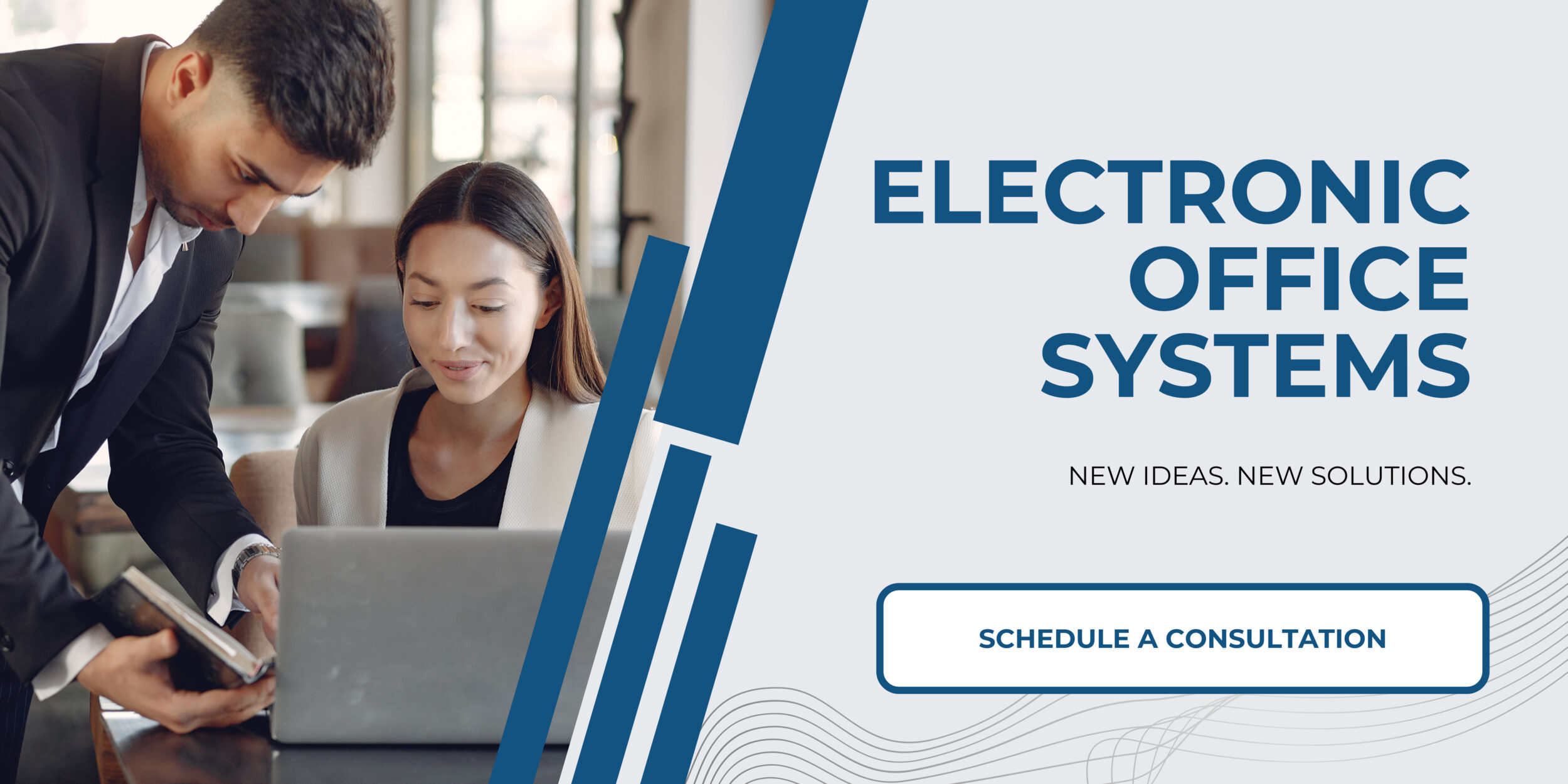
Duty Cycle Implications for Energy Efficiency and Operational Costs
The duty cycle of a device, which is the ratio of time the device is active compared to the total time it could be in operation, has significant implications for both energy efficiency and operational costs. It is a critical factor to consider in order to optimize the performance and cost-effectiveness of equipment in various industries, including manufacturing, transportation, and utilities.
When a device is operating with a high duty cycle, it means the equipment is active for a larger percentage of the time. This can lead to increased energy consumption as the device is drawing power more frequently. On the other hand, a low duty cycle indicates that the device spends more time in idle or off state, which might suggest better energy saving potentials. However, the start-up and shut-down processes can also be energy-intensive, and cyclic loading can lead to thermal stress and other forms of wear and tear, potentially impacting energy efficiency negatively and increasing maintenance requirements.
Understanding the optimal duty cycle for a specific piece of equipment is important because it can help to strike a balance between energy consumption and the device’s operational performance. For example, a motor that operates continuously at full capacity (100% duty cycle) may consume more energy and require more frequent maintenance compared to one that operates at a lower duty cycle. By optimizing the duty cycle, one can reduce operational costs by saving on energy expenses and prolonging the lifespan of the device through reduced mechanical stress.
The duty cycle also factors into decisions about device usage and the scheduling of maintenance. Equipment that is expected to have a high duty cycle will need more robust maintenance schedules to address the wear and tear that comes from frequent use. Predictive maintenance strategies, which use data and analytics to predict when maintenance should be performed, can be particularly valuable in these situations. By anticipating when a device is likely to fail or require service, maintenance can be scheduled proactively, reducing downtime and minimizing unexpected operational costs.
Low duty cycle operations may not demand as frequent maintenance, but when the equipment is used, it must be ready to perform reliably. Therefore, the maintenance schedule should ensure that even infrequently used devices are inspected and serviced appropriately to guarantee operational readiness when needed.
In conclusion, the duty cycle is a vital consideration for managing both the energy efficiency of a device and its related operational costs. By understanding and optimizing the duty cycle, organizations can save money on energy bills, extend the life of their equipment, reduce the environmental impact, and ensure that maintenance is carried out in a timely, cost-effective manner. Decision-makers should integrate duty cycle data into their strategic planning to achieve a balance between equipment performance, maintenance needs, and total operating expenses.