Title: The Impact of Ink Selection on the Final Quality of Vinyl Printing
Introduction:
In the dynamic realm of vinyl printing, the success of the final product is not only a testament to the design prowess but also hinges heavily on the technical decisions made during the production process. One such critical decision is the choice of ink, which plays a pivotal role in determining the quality, durability, longevity, and visual impact of the printed vinyl materials. Whether it’s for vibrant advertising banners, eye-catching vehicle wraps, or custom apparel, the ink selection requires careful consideration to ensure it aligns with the intended application’s demands and client expectations.
The intricacies of ink selection for vinyl printing encompass a range of factors, including the type of vinyl substrate, the intended use of the final print, the printing technology itself, and the environmental conditions to which the product will be exposed. Each of these elements must be meticulously assessed to make an informed choice. The inks used in vinyl printing vary broadly, from solvent and eco-solvent inks to latex and UV-curable options, each offering a distinct set of properties that influence the print’s outcome.
This article aims to delve into the fundamental ways in which the choice of ink can affect the final result of vinyl printing projects. Through an exploration of the different types of inks available, their compositional characteristics, and the resultant print quality on vinyl substrates, we will examine how each ink type interacts with the vinyl surfaces to produce varying degrees of color vibrancy, resolution, and durability. We will also discuss how the environmental sustainability of inks affects their selection and the growing importance of environmentally conscious printing practices. Ultimately, understanding the multifaceted relationship between ink selection and vinyl print quality is essential for achieving excellent results that meet both aesthetic and functional requirements in the wide-ranging applications of vinyl graphics and signage.
Types of Inks Used for Vinyl Printing
Vinyl printing is a popular method for producing banners, signage, decals, and various forms of advertising and graphic displays. The choice of ink used in vinyl printing is crucial, as it impacts the color quality, durability, and application potential of the printed material. There are several types of inks that can be used for vinyl printing, each with its own advantages and limitations.
The most commonly used inks in the industry include solvent inks, eco-solvent inks, UV-curable inks, and latex inks. Solvent inks are known for their ability to adhere well to vinyl and other non-porous materials, making them highly durable and resistant to weather elements. However, the solvent inks release volatile organic compounds (VOCs), which are harmful to the environment and require ventilation during printing.
Eco-solvent inks are an environmentally friendlier alternative to traditional solvent inks, producing fewer VOCs and requiring less ventilation. While eco-solvent inks are gentler on the environment, they may not be as robust as their stronger solvent counterparts, which could compromise the longevity of the print when exposed to harsh outdoor conditions.
UV-curable inks are increasingly popular due to their fast curing times and ability to create vibrant prints that are immediately dry and ready for use. The inks are cured using ultraviolet light, which quickly turns them from a liquid to a solid on the vinyl surface. This swift drying process reduces the risk of smearing and allows for greater detail in the printed design. UV-curable inks also boast excellent durability and resistance to fading.
Latex inks are water-based and offer benefits similar to eco-solvent inks—fewer emissions and an eco-friendly profile. They produce high-quality prints that are odorless and safe for indoor applications, such as in healthcare settings or schools. The prints created with latex inks are also scratch-resistant and can withstand outdoor conditions to a reasonable extent.
The choice of ink affects the final result of vinyl printing in several ways. Durability, as previously mentioned, is a key factor, especially for applications that will be exposed to outdoor environments. Environmental considerations also play a role, as businesses become more conscious of their ecological footprint. In terms of print quality, the ink composition affects the vibrancy of the colors and the sharpness of the printed details. Each type of ink has a different color gamut and optical density, which can influence how vivid and accurate the print colors are.
Moreover, ink choice influences the compatibility with various vinyl substrates. Certain inks may not adhere well to particular types of vinyl film or may require specific preparation and finishing processes. Finally, the curing and drying process related to the type of ink used can affect production speed and turnaround time for print jobs, which is an important consideration for businesses and their customers.
In summary, the selection of ink in vinyl printing significantly impacts several aspects of the final product, including durability, environmental impact, color quality, compatibility with materials, and production efficiency. Each type of ink offers a balance of these traits, and the best choice for a particular print job will depend on the specific requirements and intended use of the printed vinyl.
Durability and Longevity of Printed Inks
Durability and longevity are critical factors when it comes to printed inks on vinyl materials. These attributes determine how well the printed design will stand up to various environmental conditions over time. When considering durability, we need to think about the ink’s resistance to factors such as UV radiation, moisture, abrasion, and chemicals. Longevity, on the other hand, refers to the overall lifespan of the print before it starts to fade, discolor, or degrade in quality.
The choice of ink plays a significant role in the final result of vinyl printing, especially concerning durability and longevity. There are different types of inks used in vinyl printing, such as solvent, eco-solvent, UV, and latex inks. Each type has properties that affect the print’s resilience and durability.
Solvent inks penetrate the vinyl surface and dry quickly, making them durable once cured. They are highly resistant to environmental elements but contain more volatile organic compounds (VOCs) and require proper ventilation during the printing process. Eco-solvent inks are a more environmentally friendly alternative, emitting fewer VOCs. They offer similar durability to solvent inks but may have a slightly shorter lifespan and usually cost more.
UV-curable inks are cured by exposure to ultraviolet light, which instantly dries and adheres them to the vinyl. These inks are highly durable, resistant to scratches, and can withstand exposure to the outdoor elements effectively. They also have the advantage of being more environmentally friendly due to the lack of solvent in the ink. However, they may be more costly and require specific printing equipment with UV curing capabilities.
Latex inks are water-based and use heat during the curing process. These inks are less harmful to the environment and are considered to have excellent durability with good scratch resistance. They work well on a variety of vinyl materials and are suitable for both indoor and outdoor applications.
To ensure maximum durability and longevity of vinyl prints, it’s crucial to select the right ink for the specific application. Factors like exposure to sunlight and weather conditions, the need for flexibility of the vinyl after printing, and the intended use of the printed material (indoor or outdoor) should all be considered when choosing the ink type.
Ultimately, the interplay between the ink composition, the vinyl substrate, and the curing process determines how long the final print will last and how well it will resist fading, peeling, or cracking over time. The right choice of ink can lead to a high-quality print that maintains its visual impact for years, while the wrong choice can result in a print that rapidly deteriorates and loses its appeal.
Color Vibrancy and Accuracy
In the context of vinyl printing, color vibrancy and accuracy play critical roles in determining the overall quality and appeal of the printed product. These two factors are influenced by various elements including the type of inks used, the printing technology, and the substrate material.
Color vibrancy refers to how vivid and intense the colors appear on the printed vinyl. High vibrancy is often desired in advertisements and decorative pieces, where eye-catching graphics are paramount. In contrast, color accuracy is about the fidelity of the printed colors to the original design or the colors intended by the designer. Accuracy ensures that the hues match the specified Pantone or color codes, a crucial aspect for brand consistency and recognition.
The choice of ink significantly affects both vibrancy and accuracy. In the realm of vinyl printing, there are primarily two types of inks that are commonly used: solvent-based inks and UV-curable inks.
Solvent-based inks penetrate the vinyl surface and adhere strongly to it, resulting in vivid colors with high contrast. They contain pigments that are suspended in a volatile organic compound (VOC) solvent, which evaporates to leave the pigment behind. The solvent also helps to etch into the vinyl which can enhance color saturation, thus providing bright and vibrant prints. However, solvent inks can be less precise when it comes to color matching due to their tendency to spread slightly on the vinyl surface before drying.
UV-curable inks, on the other hand, are cured by exposure to ultraviolet light immediately after being printed. This quick curing process allows for greater color accuracy because the inks do not have time to spread or mix on the substrate. UV inks also offer excellent vibrancy with the benefit of being environmentally friendlier than solvent inks because they do not release VOCs during the curing process.
Moreover, the ink’s formulation, which includes the quality and type of pigments used, as well as the printer’s color management system, can dramatically affect color fidelity. In addition, proper calibration and profiling of the printer ensure the colors produced are as close as possible to what is seen on the screen or in a color swatch.
Overall, when choosing inks for vinyl printing, it’s important to consider the end use of the product. For outdoor applications where the vinyl will be exposed to elements, one might prioritize durability along with vibrancy, potentially opting for solvent inks. For indoor, detail-oriented graphics, UV-curable inks could be the better choice due to their finer color precision and lower environmental impact. Ultimately, the balance between color vibrancy, accuracy, and other factors like durability and material compatibility will determine the final result and suitability for the intended application.
Compatibility with Vinyl Materials
The compatibility between the ink used for vinyl printing and the vinyl material itself is of paramount importance. Each type of vinyl has unique chemical and physical properties that dictate which inks will adhere best and which will not. This is crucial since an improper match can lead to ink not sticking, peeling off, or even degrading the vinyl material itself.
Different vinyl materials may require different kinds of inks. For example, cast vinyl, which is typically used for more flexible and conformable applications, such as vehicle wraps, often pairs best with solvent or eco-solvent inks. These inks have chemical properties that allow them to penetrate slightly into the vinyl and create a strong bond. For rigid or less flexible vinyl, UV-curable inks may be ideal because they adhere well to the surface and cure instantly when exposed to ultraviolet light, reducing the risk of smudging or spreading.
The choice of ink is not only about adhesion; it also affects the durability of the print. Some inks are more resistant to environmental factors such as UV light, harsh weather conditions, and frequent handling or cleaning. For instance, using UV-curable inks on outdoor signage can extend the lifespan of the print. Ink flexibility is another consideration, especially for vinyl that needs to be stretched or applied over curves and edges, as in the case of vehicle graphics or skins for electronic devices.
Moreover, the choice of ink interacts with the color vibrancy and accuracy of the printed vinyl. Certain inks, like eco-solvent, are known for their broad color gamut, producing vivid and accurate colors. To ensure the best final result in vinyl printing, professionals often pretest the ink and vinyl combination for compatibility, and they take into account the intended use scenario of the printed material, whether it might be for indoor or outdoor use, subjected to heat, cold, or mechanical stress.
The chemical composition of the ink also has implications for the health and safety of the workers and the environmental impact of the printing process. For instance, some solvent inks contain volatile organic compounds (VOCs), which can be harmful if proper ventilation and safety measures are not in place.
In conclusion, the choice of ink for vinyl printing directly influences the effectiveness of the adhesion, the appearance, and durability of the print, as well as the safety and environmental impact of its production. Achieving optimal results requires a careful selection of ink that is tailored to the specific type of vinyl and the intended application of the printed product.
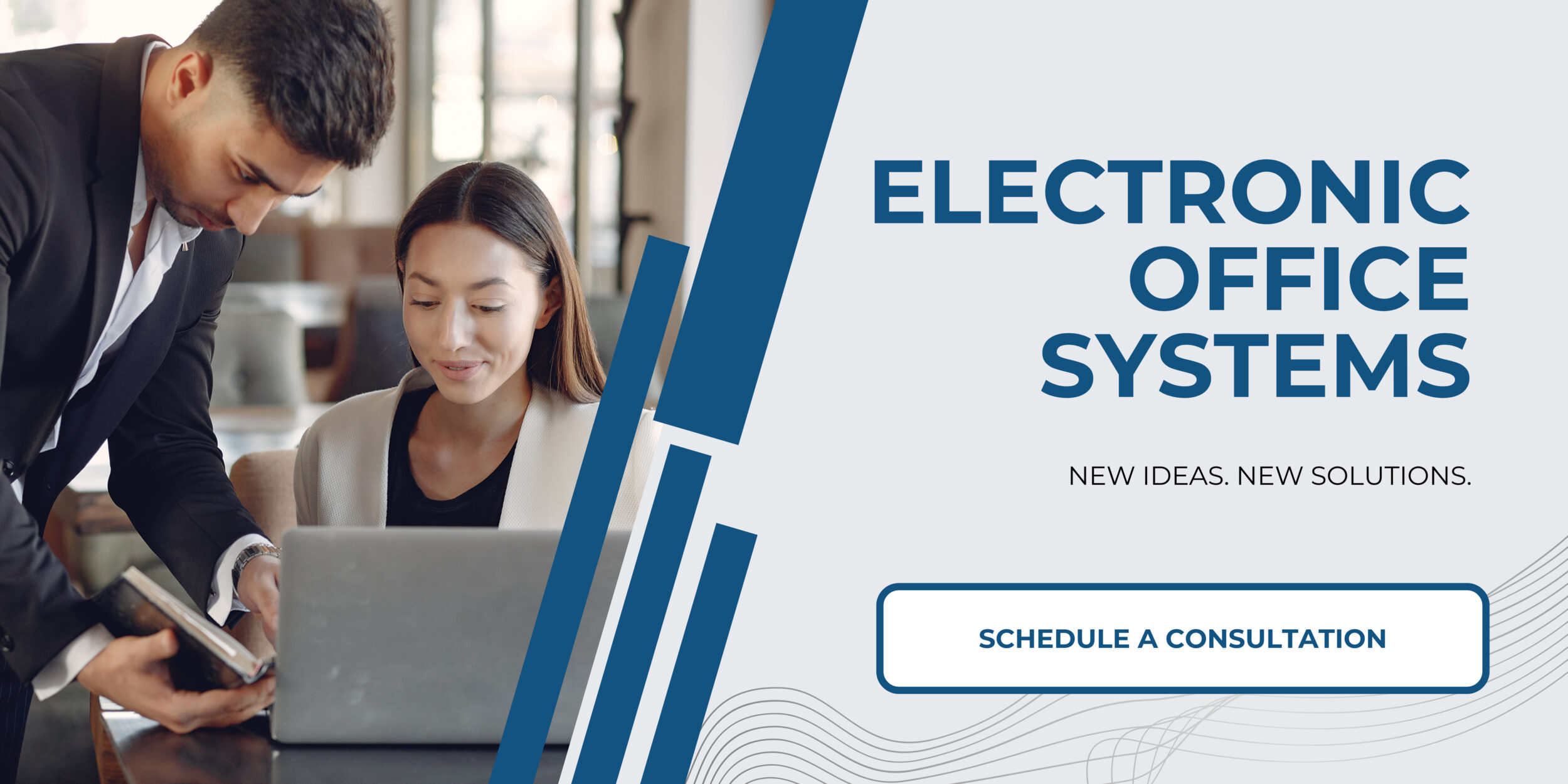
Ink Curing and Drying Processes
In vinyl printing, the ink curing and drying processes are critical steps that can significantly affect the quality, durability, and appearance of the printed product. The curing process involves the drying and hardening of the ink once it has been applied to the vinyl material, ensuring that the ink adheres properly and remains fixed to the substrate.
There are several methods used to cure inks on vinyl, and the choice of method largely depends on the type of ink used. For instance, solvent-based inks dry through evaporation of the solvents, leaving behind the pigment on the vinyl’s surface. Eco-solvent inks follow a similar process but are usually slower to dry and require less ventilation due to their reduced volatile organic compound (VOC) content.
UV-cured inks, on the other hand, are dried using ultraviolet light which quickly cures and sets the ink, making it durable and resistant to fading. UV curing is highly efficient as it typically results in an almost instantaneous drying process. This method not only reduces production times but also allows for the use of more vibrant colors, as UV-cured inks are often more resistant to fading and have a wider color gamut.
Latex inks are another option, which cure by being heated after printing. The heat causes the water-based latex inks to evaporate, leaving the pigments to bond with the vinyl surface, resulting in a print that is both durable and scratch-resistant.
The choice of curing technique impacts the final outcome significantly. If the ink is not properly cured, it can smear, crack, or peel, compromising the print’s overall durability and appearance. Proper curing is especially important for outdoor applications where prints are exposed to sunlight and weather conditions that can speed up degradation if the ink is not cured and adhered properly. Additionally, well-cured inks maintain their color brightness and provide a better resistance to environmental factors such as UV light and moisture.
In summary, the ink curing and drying processes are essential in achieving a high-quality, long-lasting vinyl print. The methodology employed not only affects the immediate handling of the printed material but also its longevity and how it will withstand various conditions over time. The choice and application of the curing process must thus be carefully considered based on the desired outcome, the specific ink used, and the intended use of the printed vinyl.