Title: Maintaining and Troubleshooting Standalone Cutting Plotters in Wide Format Printing
Introduction:
In the world of wide format printing, standalone cutting plotters are invaluable tools for professionals who require precise and efficient cutting for their vinyl and other materials. These specialized pieces of equipment are pivotal in producing everything from large-scale advertising banners to intricate vehicle wraps. While cutting plotters are designed to offer high levels of performance and reliability, maintaining their optimal functionality requires a proactive approach and an understanding of common troubleshooting practices.
This comprehensive article aims to serve as a fundamental guide for users of standalone cutting plotters, providing essential insights into the maintenance routines and troubleshooting techniques necessary to ensure these machines continue to operate at their best. We will delve into key maintenance actions such as regular cleaning, blade inspection and replacement, and establishing an optimal working environment for your cutter. Additionally, we will explore common issues encountered with cutting plotters, such as misalignment, incorrect cutting depth, and software connectivity problems, and provide step-by-step solutions to get your plotter back on track.
By the end of this article, owners and operators of cutting plotters will be equipped with the knowledge to not only perform regular maintenance but also to identify and resolve common technical issues swiftly, minimizing downtime and maintaining productivity in demanding wide-format printing tasks. Whether you are a seasoned professional or new to the world of cutting plotters, these guidelines will ensure that your equipment remains a reliable asset in your printing arsenal.
Regular Maintenance and Cleaning Procedures
Regular maintenance and cleaning are crucial for the optimal functioning of a standalone cutting plotter used for wide format printing. These cutting plotters operate by moving a blade to cut shapes out of vinyl or other materials, and thus are prone to collecting debris and dust which can impact the quality and precision of the cuts.
Maintaining a cutting plotter involves a series of routine procedures. Firstly, it’s essential to keep the plotter clean. Dust and material offcuts can accumulate in the machine, leading to potential misalignment or even damage to the mechanical parts. At a minimum, the plotter should be cleaned after each major project or at the end of a day’s work. Use a soft, dry cloth to wipe the surface of the machine and remove any particles or residues on the cutting mat or around the cutting strip. Compressed air can be used to blow away finer particles from hard-to-reach areas.
Lubrication is also a key part of regular maintenance. Some plotters have moving parts that may require occasional lubrication to ensure smooth operation and to prevent wear and tear. Check the manufacturer’s manual for specific guidance on lubricating mechanisms like the blade holder or carriage rails.
Regarding the cutting blade, it should be checked regularly for signs of dullness or damage since a sharp and well-maintained blade is crucial for achieving accurate cuts. Blades should be replaced as needed, depending on the frequency of use and the materials being cut.
Maintenance also extends to the software that controls the cutting plotter. Regular updates can fix bugs, improve functionality, and ensure compatibility with other programs. Ensure that your firmware and software are always up to date to minimize operational issues.
Moreover, record-keeping of maintenance schedules, issues, and any repairs can be quite beneficial. Keeping logs helps to predict when parts may need service or replacement and can aid in diagnosing issues when they arise.
Troubleshooting a cutting plotter may require a systematic approach to identifying and solving problems. Common issues include misaligned cuts, incomplete cuts, or error messages from the plotter’s software. When troubleshooting, start by checking the simplest factors such as making sure the machine is clean, the blade is sharp and properly seated, and the machine is calibrated correctly. Verify that the material being cut is suitable for the plotter and that it’s secured firmly. Additionally, confirm that the software settings match the job that’s being sent to the plotter. If error messages occur, refer to the user manual for specific troubleshooting steps or contact the manufacturer’s technical support team.
By regularly following maintenance and cleaning procedures, and applying systematic troubleshooting methods, you can ensure that your standalone cutting plotter remains reliable and continues to produce high-quality results for all your wide format printing needs. Regular upkeep not only maximizes the lifespan of the plotter but also helps to maintain efficiency and accuracy in the cutting process.
Blade and Cutting Strip Inspection and Replacement
Blade and cutting strip inspection and replacement are critical maintenance tasks for ensuring the optimal performance of standalone cutting plotters used for wide format printing. The blade is the component directly responsible for cutting through the material, whether it’s paper, vinyl, or any other medium. Over time, the blade can become dull or damaged, leading to inaccurate cuts and potentially damaged materials. That’s why regular inspection is necessary to determine if the blade is sharp enough and free of nicks or other imperfections. If signs of wear or damage are detected, it is imperative that the blade is replaced with a new one to maintain the quality and precision of the cuts.
Alongside the blade, the cutting strip, which is the surface the blade cuts against, is also prone to wear and should be regularly inspected. A worn-out cutting strip can affect cut quality and even cause damage to the blade. It’s marked by visible cuts and grooves that accumulate from repetitive use. When it becomes too grooved, it can interfere with the plotter’s ability to make precise cuts. Replacing the cutting strip when it shows signs of excessive wear is equally important to ensure that the cutting plotter functions effectively.
To maintain and troubleshoot a standalone cutting plotter, it’s crucial to adhere to the manufacturer’s recommended maintenance schedule and procedures. Regularly cleaning the plotter to keep it free of dust and debris can prevent many issues. Keeping the firmware and software updated ensures compatibility and can sometimes improve the performance or add new features. Calibration and realignment should be performed as instructed to ensure that cuts are accurate and align correctly.
In case of problems, referring to the cutting plotter’s manual for common issues and error messages is beneficial. Many plotters come with self-diagnostic tools that can guide you through troubleshooting steps. It’s also advisable to seek professional help if the problem persists or is beyond one’s technical expertise. Proper maintenance and timely troubleshooting are essential to extend the life of the cutting plotter and guarantee consistent output quality.
Firmware and Software Updates and Configuration
Keeping a standalone cutting plotter functioning at its best often requires maintaining its firmware and software up-to-date. Firmware is a specialized software that is ingrained directly into the hardware of the plotter. It controls the basic functions of the device and allows it to communicate effectively with the computers running design software. Manufacturers release firmware updates periodically to enhance performance, add new features, and fix known bugs. Regularly checking for and installing these updates ensures that the cutting plotter operates efficiently and remains compatible with the latest software and operating systems.
Software, on the other hand, is the application that runs on a computer and sends instructions to the plotter. Design and cutting programs need to be current for optimal communication and functionality. Manufacturers may release software updates to introduce new functionalities, improve user experience, and provide fixes for any software-related issues that may interfere with the plotter’s performance.
To maintain and troubleshoot a cutting plotter, it is crucial to follow a systematic approach. First, always refer to the user manual provided by the manufacturer for specific maintenance guidelines and procedures. For firmware updates, it is typically necessary to connect the plotter to a computer with internet access or to download the update onto a USB drive, depending on the model. Consistently checking the manufacturer’s website for updates will keep the firmware current.
For software issues, ensure that the cutting program is compatible with the operating system on your computer. It’s also important to check for updates or patches that resolve known issues. When encountering problems, restarting the software or computer and ensuring that the connection between the plotter and the computer is secure can often resolve the issue.
Ensure that the configuration settings on both the software and the firmware are correctly set. Incorrect settings can lead to poor cutting quality or the plotter not recognizing commands properly. Calibration of the cutting blade’s pressure and alignment in relation to the material being cut is also essential for accurate and efficient operation.
If the plotter is experiencing consistent issues despite software and firmware updates, consulting the manufacturer’s support team can provide guidance and potentially necessary repairs if the problem is hardware-related. Additionally, online forums and user groups can be a valuable resource for troubleshooting common issues that other users may have experienced and resolved.
Regularly updating the firmware and software and correctly configuring them is a proactive step towards maintaining the longevity and efficiency of a standalone cutting plotter. It ensures the device is up-to-date with technological advancements, helping to prevent many issues before they arise and simplifying the troubleshooting process when they do occur.
Calibration and Alignment Techniques
Calibration and alignment are critical techniques for ensuring the accuracy and quality of outputs from a standalone cutting plotter used for wide format printing. A well-calibrated cutting plotter can produce clean cuts and precise graphics which are essential for professional-looking designs. The process of calibration generally involves adjusting the machine to ensure that it is cutting at the right depth and pressure. Alignment, on the other hand, ensures that the cutting blade is moving correctly over the material, preventing skewing and misalignments of graphics and designs.
Maintenance and troubleshooting of a standalone cutting plotter for wide format printing are key to the machine’s longevity and performance. To maintain such a device, it’s important to follow a comprehensive plan that includes regular calibration to ensure the accuracy of cuts. Users should refer to the manufacturer’s guidelines for calibration procedures, which typically involve using test patterns to adjust and correct the blade force, offset, and other settings.
Alignment is equally important and can often involve making sure the material is being fed straight into the plotter and that the print and cut marks are being accurately read by the device’s optical sensors or laser pointers, which help in aligning the cutting blade with the printed images. Regular checks and adjustments might be needed to keep the plotter operating within its specifications.
Troubleshooting such plotters involves a systematic approach to diagnosing issues like misaligned cuts, incomplete cuts, or poor tracking. Regular checks for software updates and keeping firmware current can prevent many issues. When a problem arises, checking the error messages provided by the cutter can be the first step toward diagnosis. Typical issues could include updating or reverifying settings for blade pressure and offset after replacing a cutting strip or blade, ensuring the material is properly loaded and that no debris or obstructions are affecting the cutting path or media sensors.
Keeping the plotter clean, including the blade and the area around the cutting strip, helps maintain the equipment and prevents debris-related issues. Operators should also check for mechanical wear and tear regularly and consult the manual or customer support for specific issues that cannot be resolved through initial troubleshooting steps.
Overall, maintaining and troubleshooting a cutting plotter requires attention to detail, a comprehensive understanding of the equipment, and adherence to recommended maintenance schedules to minimize downtime and extend the life of the machine. Operators should be well-versed in the machine’s operation to quickly identify and correct small issues before they lead to significant problems.
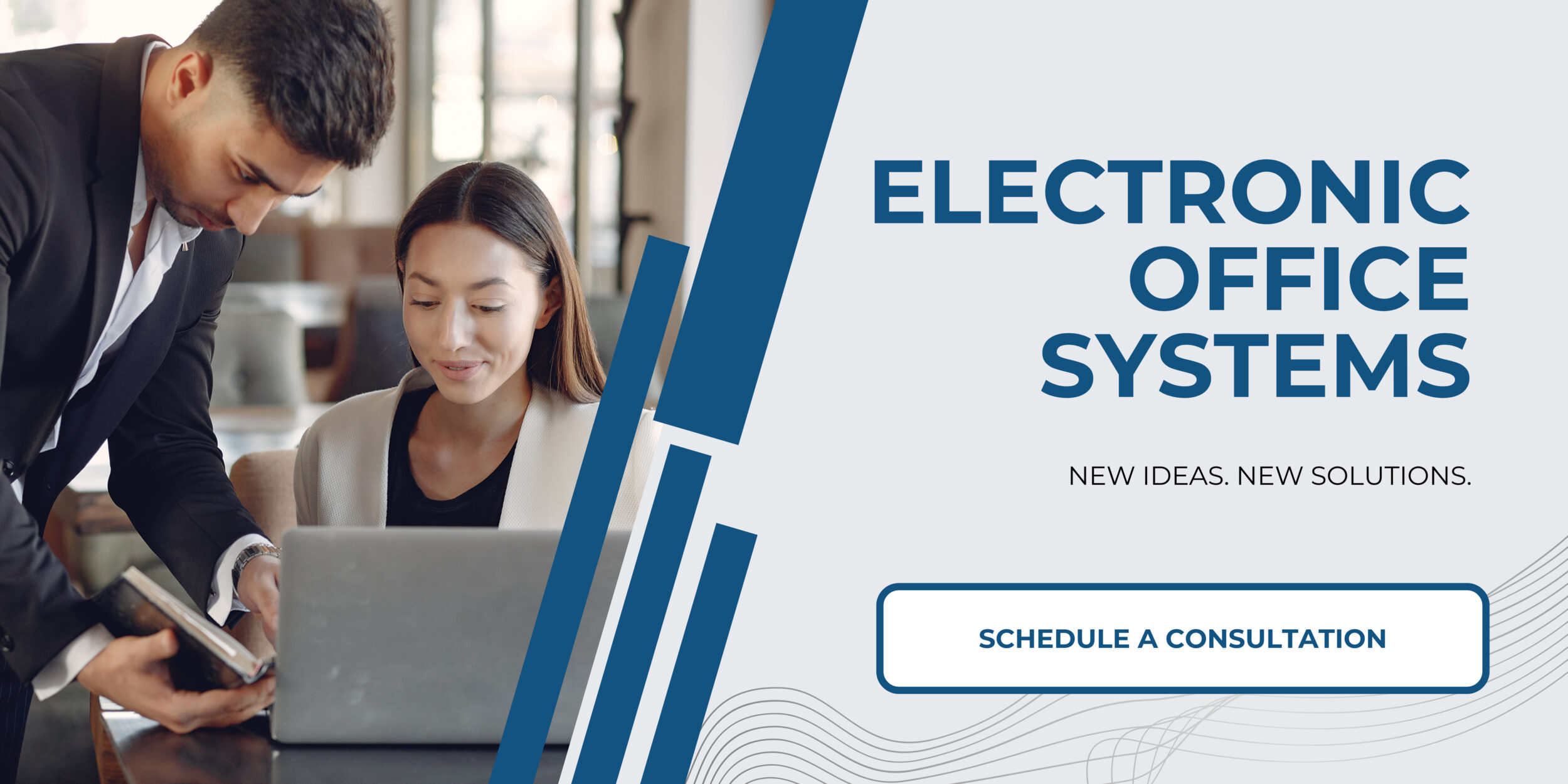
Troubleshooting Common Issues and Error Messages
Maintaining and troubleshooting a standalone cutting plotter is essential for ensuring consistent operation and longevity. Standalone cutting plotters, which are often used for wide format printing such as for signage, vinyl decals, and heat transfer materials, can experience various common issues that can impede performance. Troubleshooting these problems often starts with understanding the error messages displayed by the device.
Error messages can range from communication errors, which might involve incorrect settings or faulty connections between the plotter and the computer, to mechanical issues such as paper jams, misalignment, and errors related to the cutting blade or strip.
To maintain your cutting plotter, it is imperative to follow a routine maintenance schedule. This includes regularly cleaning the device to prevent build-up of debris and dust that can interfere with the sensors or get into the mechanical parts. The cutting strip and the blade should be inspected frequently for signs of wear and tear, as they are crucial for precise cutting results. If any part of the blade or cutting strip appears to be damaged or dull, it should be replaced immediately to avoid poor quality cuts or further damage to the machine.
It’s also important to ensure that the firmware and software associated with the cutting plotter are up to date. Manufacturers often release updates to correct known bugs, improve performance, and ensure compatibility with newer operating systems and design software.
Calibrating and aligning your cutting plotter are critical steps to ensure accuracy. The alignment process adjusts the sensors and cutting path, while calibration ensures that cuts are made at the correct force and position. Skipping these steps can lead to inaccuracies in cut quality and may result in wasted material.
When an error message appears, consult the user manual for specific troubleshooting steps or error codes explanations. Many issues can be resolved by following the provided instructions, such as resetting the device, checking cable connections, or cleaning sensor areas. If the problem persists, or if you encounter a mechanical issue such as a strange noise or an unexpected stop during operation, it may be time to engage a professional service technician.
One crucial part of maintaining the cutter is keeping backups of configurations and settings. In the event of a system reset or firmware update, having these backups will make it easier to restore the plotter to its previously optimized state without the need to recalibrate from scratch.
Lastly, proper training for the operator is also beneficial. Knowing how to operate the cutting plotter, which includes loading the material correctly and selecting the right cutting parameters, not only improves the efficiency of the machine but also reduces the likelihood of errors that could lead to the need for troubleshooting.
Consistent maintenance and being proactive about potential issues can drastically reduce the need for intensive troubleshooting. However, when common issues do arise, a systematic approach to understanding error messages and consulting the manual can help quickly identify and address the problem.