Large format printing stands tall in the visual communication landscape, offering businesses and creatives the capacity to produce eye-catching graphics and high-impact imagery on a grand scale. Within this realm, dye-sublimation printing is a cutting-edge technique, revered for its versatility and vibrant results. As it becomes more accessible and cost-effective, it is essential to understand the intricacies of how dye-sublimation works and the unique benefits it brings to large-format applications.
At its core, dye-sublimation is a digital printing technology that allows for the transfer of full-color, photographic-quality images onto a variety of substrates. Unlike traditional printing methods that lay ink on top of a surface, dye-sublimation involves a chemical process that transforms solid dye particles into a gaseous state, allowing them to permeate and bond with the chosen printing medium. This results in graphics that are not only stunning in their color richness and clarity but also durable and resistant to the elements.
To appreciate the process, one must delve into the foundations of dye-sublimation. It starts with a digital design that is printed onto a special transfer paper using sublimation inks. When heat and pressure are applied via a heat press, the inks vaporize and infuse directly into the material’s fibers; if the medium is a polymer-based substrate, the ink becomes part of its structure. Hence, once the transfer is complete, the image is as integral to the material as the material itself.
This remarkable printing technique opens up a world of possibilities for large format applications—from banners and flags to trade show displays and interior decor—providing creators with the tools to produce sharp, long-lasting, and engaging visual content. This comprehensive article will delve into the science behind dye-sublimation, the various stages of the printing process, and its application in large format printing scenarios, to enlighten both novices and seasoned print professionals about the transformative potential of this innovative printing technology.
Sublimation Ink Characteristics
Sublimation inks are a unique kind of ink that is used primarily in dye-sublimation printing, a popular method for printing high-quality images onto various substrates. Dye-sublimation ink comprises solid dye particles that are ground into a fine powder and suspended in a liquid carrier. The distinguishing characteristic of sublimation ink is its ability to transition from a solid to a gas without going through a liquid phase, a process known as sublimation. This characteristic is crucial for the transfer process used in dye-sublimation printing.
Upon heating to a high temperature, the sublimation ink transforms into a gaseous state. This gas is then able to penetrate the surface of the substrate being printed on, which is typically a polyester or polymer-coated material. As the ink cools and returns to a solid state, it becomes a part of the substrate itself, unlike in traditional inkjet printing where the ink merely sits on top of the substrate. This results in a high-resolution print with vibrant colors that resist fading and are durable against washes and handling.
The sublimation ink is not only recognized for its vibrant and long-lasting colors but also for its ability to perform without blocking the print heads of printers, an issue common with other types of inks. Printers equipped for dye-sublimation use, typically feature a piezo-electric print head that vibrates to release precise amounts of the ink onto a transfer paper. This transfer paper then serves as the medium to carry the image onto the substrate.
Now, in the context of large-format printing, dye-sublimation plays an integral role, predominantly within industries that produce banners, flags, signage, trade show graphics, and custom fabric prints, among others. Large-format dye-sublimation printers are capable of producing wide graphics that can be several feet in both width and length. To achieve this, the printers use rolls of transfer paper and larger amounts of ink.
In the large-format dye-sublimation printing process, after the image is printed onto the transfer paper, it is taken to a heat press where both the transfer paper and the substrate are subjected to high temperatures, usually around 400°F (204°C). The heat causes the sublimation ink to transform into a gas, and under the pressure of the press, the ink permeates the fibers of the substrate. When the temperature drops, the ink re-solidifies within the substrate, ensuring a long-lasting and vivid print.
The advantages of using dye-sublimation for large-format printing are numerous. It allows for continuous tone printing, where colors shade into each other with seamless transitions and without visible dots or rasterization, which is particularly important in large graphics where viewers may be in close proximity to the image. Additionally, as the sublimation process actually dyes the fabric, the print is less prone to scratching and fading compared to other printing methods. The results are especially prominent in custom apparel and sportswear, where elasticity is important and the print will not crack when the fabric is stretched.
Dye-sublimation is a versatile and powerful printing technique that has revolutionized the way high-quality images are transferred onto a variety of large-format substrates, delivering durability and outstanding color accuracy in the final products.
Transfer Process and Heat Press Technology
The transfer process and heat press technology are at the heart of dye-sublimation printing, which is pivotal to creating high-quality prints for various applications, including large-format designs found in banners, flags, and other display graphics.
The dye-sublimation transfer process involves printing a design with sublimation inks onto a special transfer paper. This step is the preliminary phase where the inks are still in their solid form. The real magic happens during the heat press phase. When the printed transfer paper is subjected to heat and pressure in the heat press, the sublimation inks undergo a phase change directly from solid to gas, a process known as sublimation.
In large format printing, specially-designed heat presses are used to accommodate larger print sizes, while ensuring consistent heat and pressure are applied across the entire surface. It is critical for the heat press to maintain precise temperature control since the sublimation process is initiated at around 200°C (392°F). During this change, the ink gaseous particles penetrate the fibers of the polyester or polymer-coated substrate, assuring a durable bond.
Once the heat is removed, the gaseous dye cools down and solidifies again, embedding the dye into the substrate and locking in the color. As a result, the printed image becomes a part of the substrate itself. Unlike conventional printing techniques that simply lay ink on top of a material, dye-sublimation creates a vivid, permanent image that is less prone to fading or cracking.
This process is particularly well-suited for large format printing as it can produce seamless images over large expanses of material. The dye-sublimation technique allows for the reproduction of high-quality images that have continuous tone prints and rich colors, which are ideal for wide visual graphics where close-up viewing is probable.
This technology also offers great versatility as it can work with a variety of heat-sensitive substrates suitable for different applications. Materials typically used in large format sublimation printing include textiles, ceramics, metal, and plastic materials that are coated with a special polymer layer designed to accept the sublimation inks.
In sum, the transfer process and heat press technology of dye-sublimation allow for high-quality print reproduction in large format applications, where the depth of color and durability are paramount. This method is chosen for its ability to produce long-lasting vibrant images that can withstand external elements, making it a top selection for outdoor banners, apparel, and decor items.
The Role of Substrates in Dye-Sublimation
Substrates play a vital role in the process of dye-sublimation, particularly in large-format printing. Dye-sublimation is a printing process that uses heat to transfer dye onto different materials, often fabrics. In the context of large-format printing, substrates typically refer to the large rolls of fabric or material onto which designs and images are printed.
The primary attribute that separates suitable substrates for dye-sublimation from unsuitable ones is the ability to accept and retain the dye when it’s sublimated. Sublimation printing is usually done on polyester or polymer-coated substrates because the dye-sublimation process requires a substrate that can withstand high temperatures since the sublimation transition occurs at around 180 to 210 degrees Celsius. At these temperatures, the solid dye particles turn directly into gas and permeate the fibers of the polyester material, creating a high-resolution, long-lasting print. This process ensures that the print doesn’t fade easily over time and is resistant to scratches and washes, making it ideal for applications where durability is desired, like banners, flags, sportswear, and other merchandise.
Another significant aspect to consider with substrates in dye-sublimation printing is the tightness of the weave or knit if the substrate is a textile. A tighter weave will have more fibers for the dye to bond with, which can result in a more vivid and sharp image. Additionally, the color and brightness of the substrate itself can influence the vibrancy of the final print: a substrate with a bright white color is typically preferred as it reflects the most light and therefore allows for the purest color rendition.
Beyond textiles, dye-sublimation can also be used on rigid substrates that have been coated with a special polymer layer. This expands the possibilities for creating vibrant prints on surfaces like metal, ceramic, glass, and plastic products, which are often used in the creation of decorative panels, promotional items, and other specialized products.
Dye-sublimation technology in large-format printing offers a broad spectrum of application possibilities due to its versatility with different substrates. Its ability to produce durable, vivid images on a variety of materials makes it a popular choice for both indoor and outdoor applications. As technology progresses and the demand for customized large-format items grows, the role of substrates in the success of dye-sublimation printing remains paramount. It’s worth noting that the choice of substrate is dependent not only on the technical compatibility with the dye-sublimation process but also on the desired finish of the final product, whether that’s a stretchy fabric for activewear or a rigid panel for high-quality photo prints.
Color Management and Profiling in Dye-Sublimation Printing
Color management and profiling are critical aspects of dye-sublimation printing, especially when it comes to large-format outputs. The objective of color management is to achieve consistent and predictable color reproduction across different devices—a challenge considering the varying color reproduction capabilities of printers, monitors, cameras, and other devices.
To understand this better, it is important to consider that devices interpret colors differently. For instance, a monitor uses the RGB color model (Red, Green, and Blue), while printers typically use the CMYK color model (Cyan, Magenta, Yellow, and Black). During dye-sublimation, a printer must convert the RGB images that are often created on computers to the CMYK color space, accounting for the fact that the sublimation inks will interact differently with various substrates.
Color profiling is a process that involves the creation of ICC (International Color Consortium) profiles. These profiles provide a color management system with the information needed to convert colors accurately between different devices. To create a profile for a dye-sublimation printer, a color chart is printed, and then measured with a spectrophotometer or a colorimeter. The measurements are then compared to the original values, and the profile is adjusted to correct any discrepancies.
Another aspect to consider in dye-sublimation printing is the substrate onto which the ink is being transferred. Different materials react differently to the heat and pressure of the transfer process, as well as to the sublimation inks themselves. This means that the color output can vary significantly from one substrate to another. Therefore, creating a separate ICC profile for each substrate is often necessary to ensure color accuracy.
In large format dye-sublimation printing, managing colors becomes even more complex due to the larger surface area. Uniformity in color across the entire print job is harder to maintain, and any issues with color profiling become more pronounced. Profiling for large format printers must account for more variables, such as the consistency of the ink over a large print area and the potential for greater variation in temperature and pressure across the print bed.
Now, let’s dive into how dye-sublimation works in large-format printing. Dye-sublimation is a printing technique that uses heat to transfer dye onto different materials like fabric, paper, or plastic. In large-format printing, sublimation printers use a roll of transfer paper which is printed with sublimation inks in a mirror image of the final design.
The printed transfer paper is then placed into a heat press along with the substrate. When the press is activated, it applies heat and pressure. The heat turns the solid dye particles directly into a gas, skipping the liquid phase—a process known as sublimation. The high temperature and pressure cause the gaseous dyes to penetrate the surface of the substrate, where they condense and solidify, embedding the color within the material. This results in a high-resolution print that is durable and has vibrant colors.
For large format items, such as banners or apparel, the dye-sublimation process ensures that the finished product can withstand bending and folding without cracking the print, and can also endure washing without loss of image quality. Moreover, because the dye bonds with the material at a molecular level, it doesn’t create a layer on top of the substrate, which means the final product retains the original texture and drape of the material.
In summary, color management and profiling in dye-sublimation printing are essential for producing accurate and consistent colors, particularly in large format printing where any variation is magnified. The dye-sublimation process allows for durable and vivid prints on a variety of materials, fitting a wide range of applications in the industry.
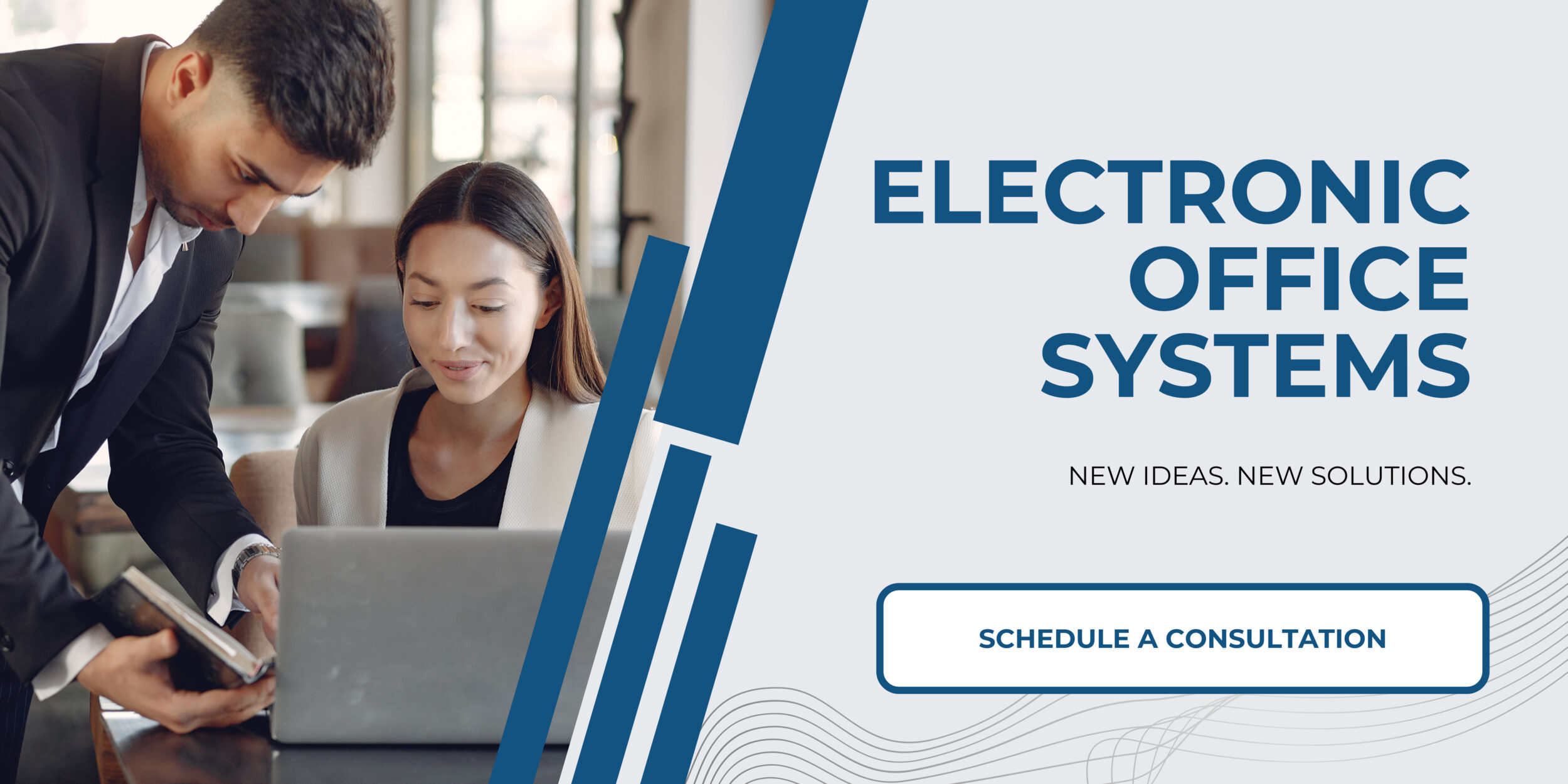
Applications and Limitations of Large-Format Dye-Sublimation
Large-format dye-sublimation printing is widely recognized for its versatility and vibrant, high-quality results. This printing technique is especially popular for producing large-scale visual displays and promotional materials, including flags, banners, backdrops for trade shows, soft signage, and even home decor such as custom-printed curtains and furniture. The dye-sublimation process allows for intricate and colorful designs that are well-suited for textiles and other substrates that can withstand the heat required for sublimation.
Applications for this technology are diverse due to its ability to produce long-lasting, vividly colored images that are impervious to water and UV light damage, making them suitable for both indoor and outdoor use. Additionally, sports apparel and high-fashion items often utilize large-format dye-sublimation for complex, multicolor patterns that do not hinder the breathability or comfort of the fabric.
While dye-sublimation provides numerous benefits, it also comes with specific limitations. For instance, it typically requires polymers to bond with the ink, limiting the choice of materials to those that are polymer-coated or contain polyester. This can be a constraint when considering cotton or other natural fibers that might not be compatible with the process. Another limitation is the sometimes higher cost of production compared to other methods, due to the specialized inks and equipment needed. Furthermore, dye-sublimation printers often have slower printing speeds, which can be a bottleneck for high-volume orders.
In terms of how dye-sublimation works in large-format printing, the process is quite fascinating. Special sublimation inks are printed onto a transfer paper, and this printed paper is then positioned onto the substrate that is to be printed. Once the paper is in place, a heat press is applied—the combination of heat and pressure causes the sublimation ink to transition from a solid to a gaseous state (skipping the liquid phase) and permeate the fibers of the substrate. The high temperature opens up the pores of the polymer-based material, allowing the gas to enter. Once the heat is removed and the material cools, the pores close, trapping the ink inside the substrate.
This process effectively dyes the substrate, so the ink becomes a part of the material rather than lying on top. As a result, the images do not crack, fade, or peel under normal conditions, ensuring the longevity of the product. Additionally, the sublimation process does not affect the texture or flexibility of the substrate, maintaining the original feel of the material. This level of quality and durability is what makes dye-sublimation a preferred choice for many large-format applications.