Title: Mastering the Art of Large Format Vinyl Printing: Key Considerations for Flawless Results
Introduction:
Large format vinyl printing stands at the intercession of high-resolution graphic art and industrial design, offering unparalleled opportunities for advertisers, artists, and businesses to broadcast their messages with visual impact. The canvas of choice, vinyl, provides a durable and flexible medium ideal for banners, signage, wall decals, vehicle wraps, and more. However, transitioning from digital designs to large-scale physical representations is not without its challenges. To achieve the flawless execution of a printed piece, meticulous planning must precede the roar of the printer.
Understanding the scope of considerations necessary when printing on vinyl with a large format printer is crucial for professionals in the printing industry or for those looking to bring their grand-scale vision to life. The process begins by selecting the right type of vinyl substrate, balancing cost with performance while considering factors such as the intended use, location, and longevity of the print. After material selection, digital artwork must be carefully prepared, with attentiveness to resolution, color fidelity, and scaling to ensure that what appears on the screen translates perfectly to the expansive vinyl surface.
Printer calibration and ink choice then become the focus, involving nuanced adjustments to ensure that the drop placement and color rendering are optimized for the vinyl’s unique texture and absorption characteristics. This step is critical for avoiding common pitfalls such as banding, color shifts, and blotchiness, which can mar an otherwise stunning visual display. Additionally, environmental variables like temperature and humidity can affect the printing process, and these must be controlled to guarantee consistent quality.
With technological advancements in printing equipment, methods, and materials, the ambitious realm of large format vinyl printing demands a comprehensive understanding of the printing dynamics. This article dives into the multitude of considerations essential to master this craft—spanning material properties, design considerations, technical settings, and finishing techniques—to render high-quality prints that stand out both in dimension and detail. Whether you’re a seasoned print shop veteran or a newcomer to the world of oversize graphics, the high stakes of large format printing underscore the importance of strategic planning and technical proficiency for achieving superior outcomes in every run.
Vinyl Material Selection
When choosing a vinyl material for printing using a large format printer, it’s important to consider a variety of factors to ensure the final product meets the desired quality and durability. Vinyl is a popular choice for large format prints due to its flexibility and ability to withstand various environmental conditions, making it suitable for both indoor and outdoor applications.
The first consideration in vinyl material selection is the intended use of the print. Different vinyl types are designed for different applications, such as banners, vehicle wraps, wall graphics, or window decals. For instance, cast vinyl is typically used for vehicle wraps because of its ability to conform to curved surfaces and long-term durability, while calendared vinyl is often selected for flat surface applications like signs and banners due to its shorter lifespan and lower cost.
The properties of the vinyl should match the end-use requirements in terms of durability, adhesion, and finish. For outdoor use, UV resistance is crucial to prevent fading, and waterproofing is essential for weather resistance. For indoor use, one might consider the finish of the vinyl, whether it is matte, gloss, or satin, to match the desired aesthetic effect.
The compatibility of the vinyl with the inks used by the large format printer is another key consideration. There might be specific vinyl materials that are better suited to particular ink types such as solvent, eco-solvent, latex, or UV-curable inks. Each ink type interacts differently with vinyl, affecting not only adhesion and drying time but also the vibrancy and longevity of the print. For example, solvent inks penetrate vinyl deeply, ensuring a durable print, while UV-curable inks cure on top of the vinyl and are less susceptible to smudging.
Additionally, the quality of the adhesive backing on the vinyl is vital. Some vinyl comes with a permanent adhesive, which is strong and long-lasting, while others have a removable adhesive that allows for repositioning during installation but may not endure as long. Selection between permanent and removable adhesives depends on whether the vinyl needs to be movable or if it’s intended as a permanent fixture.
Lastly, the printer’s specifications also play a role in selecting vinyl. Large format printers have maximum and minimum thicknesses and widths they can handle, so checking the printer’s capability in relation to the vinyl’s specifications is necessary to avoid printer jams or poor-quality prints.
Overall, when printing on vinyl with a large format printer, thorough research and understanding of the project requirements are essential. Considering environmental factors, matching the material properties with the application, ensuring ink compatibility, and adhering to printer specifications will contribute to a successful print job.
Print Quality and Resolution Settings
Print Quality and Resolution Settings are critically important when it comes to large format printing on vinyl. First, understanding the concept of print quality and resolution is key. Print quality can encompass various factors, including the sharpness of the image, color accuracy and depth, as well as the overall smoothness of the prints. Resolution, typically measured in dots per inch (DPI), is a direct measure of how many individual dots a printer can produce within a linear inch. The higher the DPI, the more detailed and finely granulated the printed image can be.
When printing on vinyl, several considerations need to be made about these quality and resolution settings. A higher resolution is particularly important for large format prints where viewers may be inspecting the print from a close distance. This can include graphics for tradeshow banners, retail signage, or vehicle wraps. A lower resolution might be accepted if the viewing distance is greater, such as with billboards.
Moreover, print quality is influenced by the printer’s capabilities, the type of ink used, and how the ink interacts with the vinyl material. Large format printers typically use either solvent, eco-solvent, latex, or UV-curable inks, all of which have different adhesion properties and interactions with the vinyl. Choosing the correct ink and resolution settings can greatly affect the durability and visual impact of the final product.
The resolution settings must match the intended use of the vinyl print. High-detail graphics require higher resolution settings to maintain the sharpness and intricacy of the image. However, using excessively high resolution for all projects isn’t cost-effective and can increase production time unnecessarily. Thus, striking the right balance between quality and efficient resource use is crucial.
Environmental factors, such as ambient temperature and humidity, can also affect print quality. These factors can cause the vinyl to expand or contract, leading to potential distortions if not accounted for. Therefore, calibrating the printer and adjusting resolution settings for the specific environmental conditions is important.
Finally, vinyl is a somewhat stretchable material and is often applied to irregular surfaces. The material’s stretchability needs to be considered, as stretching can affect the final appearance of the print. Adequate resolution settings should be chosen to ensure the image maintains its clarity and sharpness after the vinyl is applied and stretched onto its final surface.
In conclusion, when printing on vinyl with a large format printer, one needs to carefully consider print quality and resolution settings to ensure the end product meets the aesthetic and durability requirements. This includes selecting appropriate resolution to match the viewing distance, choosing the right ink for the vinyl, balancing quality with production efficiency, adjusting for environmental conditions, and accommodating the material’s stretching properties.
Color Calibration and Management
Color calibration and management are critical aspects in the printing industry, particularly when printing on vinyl using a large format printer. This process ensures that the colors represented on the final printed vinyl match as closely as possible to the original design seen on the monitor or color proofs. Proper color calibration and management affect the accuracy and consistency of colors across different print jobs and substrates.
Before delving into large format printing on vinyl, several considerations must be taken into account concerning color calibration and management. Firstly, the calibration of the printer is fundamental. Large format printers must be calibrated regularly to ensure that they produce accurate colors. This involves adjusting the printer’s settings to match a known color standard. Calibration is necessary over time as the color output can drift due to various factors such as changes in temperature, humidity, or the age of the printer.
Secondly, the color profile of the vinyl material being used is critical. Different materials can have different white points and may absorb or reflect ink differently. This variability means that a color profile specific to the vinyl is essential to ensure color accuracy. Using generic profiles can result in colors that are off, especially with complex images or when brand colors need to be replicated with precision.
Additionally, the inks used in the printer play a crucial role. Different inks have varying color gamuts and may respond differently to the vinyl material. Quality third-party inks often require their own color management strategies, which might differ from the original equipment manufacturer’s (OEM) inks.
Another factor is the viewing conditions under which the final print will be observed. Viewing conditions can dramatically affect the perception of color, so it’s important to calibrate colors not just to the printer and material but also to the lighting under which the vinyl will be displayed. For instance, prints that will be displayed outdoors will be viewed in daylight, while indoor prints may be viewed under fluorescent or LED lighting.
Environmental conditions can also influence the printing process. Temperature and humidity can cause vinyl to expand or contract, affecting how the ink sets and ultimately how the colors look. Maintaining a consistent environment when printing can help mitigate these issues.
Lastly, a consistent workflow is crucial. All devices in the color workflow, such as cameras, monitors, printers, and cutting equipment, should be calibrated and profiled to ensure color consistency from design to the final print.
In summary, color calibration and management are pivotal in large format vinyl printing for ensuring that the end product meets the expected color accuracy and quality. Proper attention to printer calibration, material profiles, ink types, viewing conditions, environmental stability, and an integrated color workflow will yield the best results, maintaining the integrity and professionalism of the final printed pieces.
Environmental Conditions and Handling
Environmental conditions and handling are critical factors to consider when printing on vinyl using a large format printer. Large format printing often involves producing outdoor signs, banners, vehicle wraps, and various types of displays that must endure diverse environmental conditions. Therefore, understanding how environmental factors such as temperature, humidity, and exposure to sunlight impact the quality and durability of a vinyl print is essential.
Temperature plays a significant role in how the vinyl behaves during printing and after installation. High temperatures can cause vinyl to soften and stretch, which can be beneficial during the application to complex curves but detrimental during printing, potentially leading to misregistration and distortion of the image. Conversely, low temperatures can make vinyl brittle and prone to cracking, particularly when applying the vinyl to a surface. It’s important to print and install vinyl within the temperature ranges specified by the manufacturer to ensure optimal adhesion and performance.
Humidity levels are another consideration. High humidity can affect the drying time of inks, potentially causing smudging or color bleeding. Moreover, if the vinyl is not properly dried before being rolled up or stacked, the prints may stick together or transfer ink onto the reverse side. Low humidity can also be problematic, as it might lead to static electricity build-up that attracts dust and dirt to the vinyl, contaminating the print surface and causing defects in the printed image.
Exposure to sunlight, specifically ultraviolet (UV) light, can influence the longevity of a vinyl print. Many inks are UV-sensitive and will fade over time if not properly formulated for outdoor use or shielded by a UV laminate. This is a significant consideration when producing graphics intended for long-term exterior application. Lamination can extend the life of a print by protecting it against UV light, scratches, and abrasions.
Additionally, the way the vinyl is handled before, during, and after printing can affect the quality of the finished product. It is essential to handle vinyl with care, avoiding creases and fingerprints that can degrade print quality. Using clean gloves can help prevent oils and dirt from contaminating the vinyl surface. Proper storage is integral as well; vinyl should be kept in a clean, dry environment, away from direct sunlight and at a consistent temperature recommended by the manufacturer.
In summary, when printing on vinyl with a large format printer, it is crucial to consider environmental conditions such as temperature and humidity and to understand how they affect the materials and printing process. Proper handling and storage are also necessary to protect the print’s aesthetic and structural integrity. By taking these factors into account, print providers can ensure high-quality, durable vinyl prints for their clients.
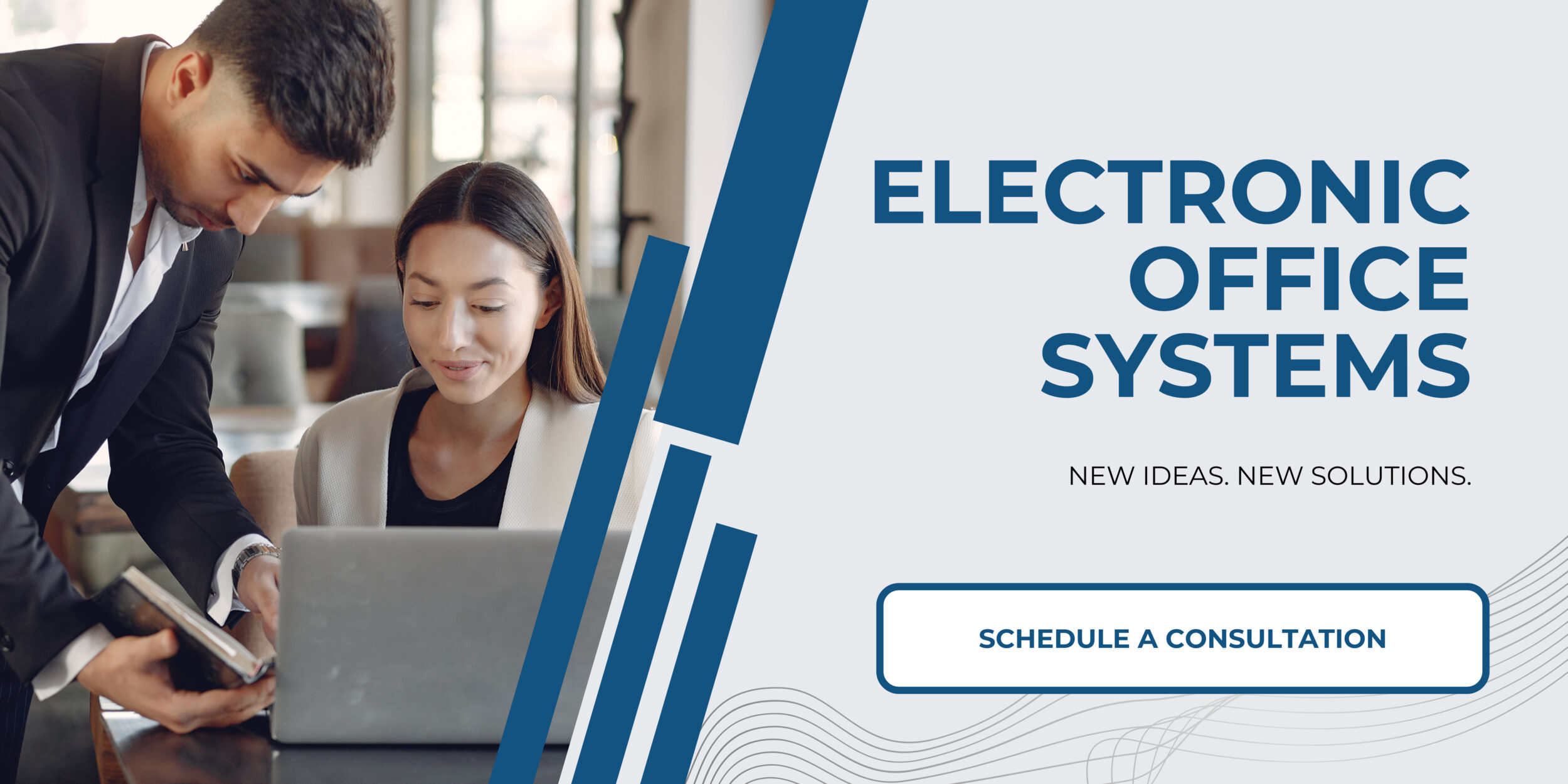
Post-Printing Processes and Finishing Techniques
Post-printing processes and finishing techniques are critical stages in the production of vinyl prints, especially when using a large format printer. These processes involve various steps that are necessary to ensure the final product is durable, aesthetically pleasing, and meets customer specifications. Some of these post-printing steps include lamination, cutting, weeding, and mounting or installation.
Lamination is crucial for protecting the print from environmental damage such as UV rays, moisture, and scratches. It can also enhance the vibrancy of the colors and extend the lifespan of the print. In this process, a clear protective film is applied on top of the vinyl graphic. There are different types of laminates, including gloss, matte, and textured finishes, and the choice depends on the desired aesthetic effect and the conditions in which the vinyl will be used.
Cutting is the next step and involves trimming or contour cutting the vinyl to achieve the desired shape and size. Precision cutting is important to ensure that the final product fits the application area perfectly. Large format printers often use automated cutting machines that can read registration marks printed along with the graphic, resulting in accurate cuts.
Weeding is necessary when dealing with vinyl decals or lettering. It involves removing excess vinyl material that is not part of the final design. This step is usually done by hand, requiring careful attention to detail to avoid damaging the actual graphics.
Finally, mounting or installation can be the last stage. This process refers to how the vinyl is attached to its end surface, whether it’s a wall, a vehicle, a signboard, or any other substrate. Proper installation is key to avoid bubbles, wrinkles, or peeling, ensuring that the graphic adheres smoothly to the surface.
When printing on vinyl with a large format printer, specific considerations need to be taken into account to ensure quality and durability of the final product:
1. **Material Compatibility**: Ensure that the vinyl and ink are compatible with each other and suitable for the intended use, whether it’s for indoor or outdoor applications.
2. **Ink Curing**: Inks should be fully cured before any post-printing processes are conducted. Uncured inks may smear or not adhere properly, which would be detrimental to the final product.
3. **Cutting Precision**: The cutting step must be precise and match the design specifications accurately. Errors in cutting can compromise the integrity and appearance of the print.
4. **Lamination Needs**: Determine if lamination is necessary based on the use case of the printed vinyl. If so, consider timing because some inks require a period to outgas before applying the laminate.
5. **Environmental Adjustments**: The post-printing environment should have controlled temperature and humidity levels to prevent the material from expanding or contracting before finishing procedures.
6. **Cleanliness**: The work environment must be clean to avoid dust and debris from getting trapped under or onto the vinyl during finishing processes, as these can cause imperfections.
These considerations are crucial when working with vinyl prints produced by large format printers to ensure the final product is of high quality, maintains its integrity over time, and satisfies the client’s requirements.