Title: Recognizing the Need for Maintenance: Common Signs That Your Scanner Requires Servicing
In the era of digital documentation, scanners play a critical role in seamlessly transitioning from paper to pixels. A well-maintained scanner can swiftly digitize and archive documents with high accuracy and efficiency. However, over time, scanners, like all electronic devices, may exhibit signs of wear or experience issues that hinder their performance. Recognizing the common signs that a scanner requires maintenance or servicing is crucial to maintain workflow continuity and ensure the integrity of digitized data.
The first indicator that suggests a scanner may need attention is a noticeable decline in image quality. This can manifest as streaks, spots, or lines on the images that were not present in the original document. Inconsistent color, poor resolution, and unexpected artifacts in scanned documents can also point to potential problems. Such issues could stem from a dirty scan glass or sensors, hardware malfunctions, or outdated software drivers.
Another apparent sign is frequent paper jams or misfeeds, which can be both frustrating and time-consuming. These can indicate that the scanner’s paper handling mechanisms may be compromised, requiring a professional look at rollers, feeders, or adjustments in the scanning settings. Additionally, strange noises or vibrations emanating from the scanner during its operation can signal mechanical problems that need to be addressed to prevent further damages.
Slower scan speeds and unresponsive behavior may also suggest that the scanner is due for servicing. This can be due to a variety of reasons, ranging from aging internal components to software issues. Finally, error messages or flashing indicator lights on the scanner serve as a direct communication from the device that it is experiencing an issue that may require professional servicing to resolve.
In conclusion, maintaining awareness of these common signs is pivotal in optimizing the performance of your scanner and ensuring longevity. Prompt attention to maintenance needs can not only prevent more significant issues down the line but also maintain the quality and trustworthiness of the digital data being processed. Regular servicing schedules, aligned with the manufacturer’s recommendations, can help mitigate the risks of unexpected scanner failures, keeping your digitization processes smooth and reliable.
Decreased Scan Quality
Decreased scan quality is typically the most noticeable sign that a scanner may require maintenance or servicing. When the output images or documents exhibit unusually low resolution or clarity compared to the past performance, users become aware that there’s an issue. There are several potential causes for this drop in quality: the scanner’s optical components, such as lenses or sensors, may be dirty or scratched; the internal lighting sources could be failing, providing inconsistent illumination; or the scanner’s calibration might be off, leading to color inaccuracies or poor contrast.
Dirt, dust, and other contaminants are common culprits when it comes to affecting the optics of the scanner. Over time, these can accumulate on the glass surface where documents are placed or on the internal components themselves. Regular cleaning as part of preventative maintenance can help to avoid such issues, but if left unchecked, these can lead to a noticeable degradation in scan quality.
Scratches on the scanning surface can also be problematic, as they can cause distortions or lines to appear on the digital copies. This physical damage often occurs from mishandling, the presence of staples and paper clips during scanning, or general wear and tear. Depending on the severity, the glass might need to be replaced to restore the scanner to its full functionality.
Another issue that affects quality is scanner calibration. Over time and with repeated use, the calibration settings of a scanner can drift, leading to poor color reproduction or images that are too dark or too light. Re-calibrating the scanner ensures that it produces accurate and consistent results.
Failing hardware components such as sensors, light sources, or even the mechanical elements responsible for feeding and transporting the documents can all diminish the quality of scanned images. In cases where these components are failing, swift maintenance or servicing is required to replace them before they corrupt scan quality further or cause additional damage to the device.
In summary, consistent and high-quality scanning is crucial for operations that rely on digitizing documents. Recognizing the signs of decreased scan quality is an important step in maintaining the functionality and longevity of scanner equipment. Regular service and maintenance checks can help prevent the degradation of quality and ensure that the scanner continues to perform at its best.
Unusual Noises During Operation
Unusual noises during scanner operation can be indicative of a variety of potential issues that may require maintenance or servicing. These sounds are often the first sign that something abnormal is occurring with the hardware components. A well-maintained and properly functioning scanner typically operates with minimal noise, allowing for a quiet work environment. Therefore, when a scanner begins to emit strange or loud noises, it could point to mechanical issues or the need for internal cleaning.
The most common types of unusual noises from a scanner may include grinding, clicking, or whirring sounds. Grinding noises often suggest that there is a problem with the gears or moving parts within the scanner. Over time, gears can wear down or become misaligned, potentially leading to a failure to operate as intended. Clicking sounds might indicate an issue with the scanner’s internal components not engaging properly, such as a loose roller or a misaligned feed mechanism. Whirring sounds, on the other hand, could mean that the scanner’s motor is strained or obstructed.
Regular maintenance is critical to prevent the wear and tear that can lead to these noises. Dust, paper debris, and other particulates can accumulate inside the scanner, causing friction and possibly obstructing the movement of rollers, gears, or other components. Regularly cleaning the interior and exterior of the scanner can help prevent buildup and prolong the life of the device.
In addition to unusual noises, other common signs that a scanner may require maintenance or servicing include the following:
1. **Decreased Scan Quality**: A decline in the clarity, sharpness, or color accuracy of scanned documents can signal that the scanner’s calibration is off, or its sensors and lenses could be dirty or damaged.
2. **Slow Scanning Speeds**: If a scanner’s processing time lengthens substantially, it might be due to software issues, failing hardware, or the need for updates or optimizations.
3. **Frequent Error Messages**: Consistent error messages often indicate a failure in the scanner’s communication with the computer system, or other internal errors that software updates or hardware adjustments might resolve.
4. **Physical Wear and Tear**: Visible signs of damage, such as cracks, broken parts, or loose connections, are clear indicators that the scanner is in need of repair or replacement.
When you observe any of these signs, it’s advisable to consult the user manual or reach out to a professional service technician who can undertake a full diagnostic and carry out the necessary repairs or adjustments. It’s best to address these issues promptly to prevent further damage and to ensure the scanner remains reliable for continued use.
Slow Scanning Speeds
When dealing with slow scanning speeds, it’s crucial to understand the probable causes and consider the contexts that can lead to such a decline in performance. Slow scanning speeds can stem from a variety of issues, ranging from hardware malfunctions to software glitches, or even due to the use of high-resolution settings which naturally take longer to process.
Hardware-related causes may include an aging scanner with components that are no longer functioning optimally. For instance, the moving parts within the scanner, such as the belts and rollers, could be worn out, leading to slower operation. Dust and debris accumulation on the scanner’s glass or the internal sensors could also impede the device’s ability to quickly process documents.
On the software side, outdated drivers or software that has not been optimized for the scanner’s operation can contribute to reduced speeds. Compatibility issues between the scanner and the operating system could also be a factor, especially after system updates that aren’t accompanied by corresponding scanner software updates. Moreover, the settings chosen by the user play a huge role—if the resolution is set very high for fine detail, the scanner will naturally take more time to capture all the information.
In more complex scanning environments like networked office scanners, slow speeds could be a symptom of network congestion or a sign that the scanner’s network connection is not properly configured or is functioning below its potential bandwidth.
Common indicators that a scanner may require maintenance or servicing include:
1. **Decreased Scan Quality:** Blurry images, streaks, or lines on the scanned documents are telltale signs that the scanner’s optical system may need cleaning or servicing.
2. **Unusual Noises During Operation:** Grinding, clicking, or other strange sounds can hint at mechanical issues within the scanner, suggesting that parts might be loose, misaligned, or need lubrication.
3. **Slow Scanning Speeds:** As discussed earlier, a noticeable decrease in the scanning throughput might imply that the hardware is facing mechanical issues or that software/firmware updates are necessary.
4. **Frequent Error Messages:** Persistent software errors or messages indicating hardware malfunctions often precede the need for professional servicing.
5. **Physical Wear and Tear:** Signs of physical damage or excessive wear on the scanner’s body, buttons, or the glass surface can indicate that the scanner has been heavily used and might need parts to be replaced or the unit to be serviced.
Routine maintenance and servicing of a scanner can alleviate many of these issues, extending the device’s lifespan and ensuring that it operates at peak efficiency. Keeping the scanner clean, updating its software, and following the manufacturer’s maintenance guidelines will go a long way in preventing slow scanning speeds and other related problems.
Frequent Error Messages
Frequent error messages are a clear indicator that a scanner may be facing issues that need to be addressed. These error messages typically appear on the scanner’s display or on your computer screen during the scanning process. They come in various forms, indicating different types of problems, which can range from something as simple as a paper jam to more complex issues like communication errors between the scanner and the software or outdated drivers.
One of the most common reasons for frequent error messages is due to software-related problems. This might mean that the scanner’s drivers are outdated or incompatible with your system’s operating system. Driver updates are important as they can fix bugs, add new features, and enhance the compatibility and performance of the scanner. Similarly, the scanning software itself might be outdated or configured incorrectly, leading to recurrent error messages.
Hardware problems can also be a cause of frequent error messages. Over time, scanners can accumulate dust and debris on the internal sensors and the scanning surface, which can interfere with the accuracy and functionality, resulting in errors. Continuous use can lead to the wearing out of mechanical parts such as rollers, gears, and feeder trays, which can cause the scanner to malfunction.
Regular maintenance is essential to prevent and address these issues. Dust and debris should be cleaned from the scanning surface and internal components carefully, according to the manufacturer’s instructions. If there are software issues, ensuring that the latest drivers and scanning software are installed can prevent many errors. For hardware concerns, parts that are subject to wear and tear might need to be replaced periodically.
In summary, the common signs that a scanner may require maintenance or servicing include:
– Poor scan quality, such as lines or spots on the images, color issues, or blurry text.
– Unusual sounds during scanning, which could indicate a problem with the scanner’s internal components.
– Slower than usual scanning speeds can be a sign of software issues or a failing hardware component.
– Frequent error messages are a significant indicator that something is not functioning correctly and should be addressed promptly.
– Signs of physical damage or excessive wear and tear signify that the scanner may need repairs or replacements for certain parts.
Addressing these signs quickly can extend the life of the scanner, maintain the quality of scanned documents, and save time and resources in the long run. If you’re unsure how to resolve the issues you’re facing with your scanner, consulting the user manual or contacting professional technical support would be advisable.
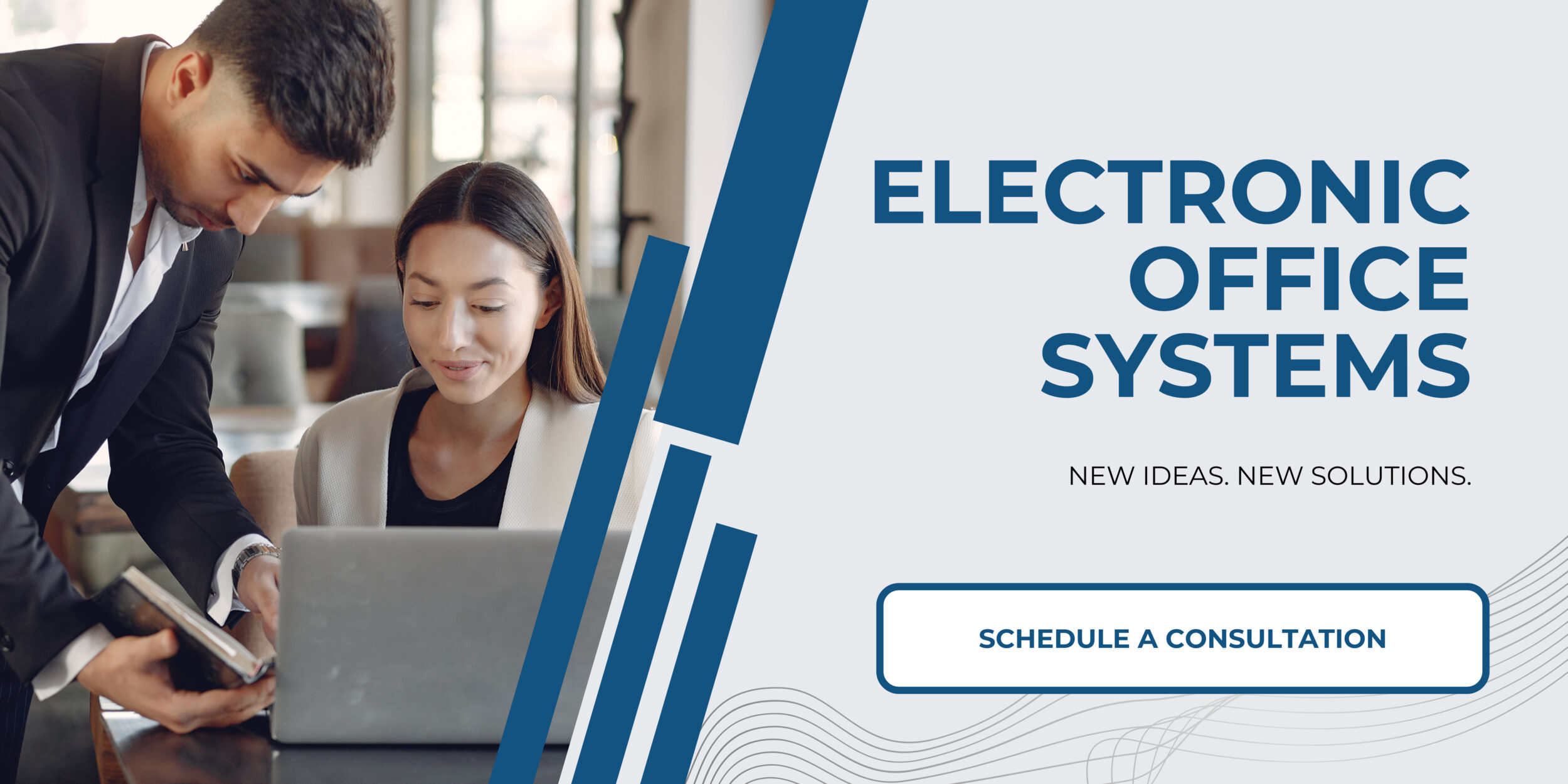
Physical Wear and Tear
Physical wear and tear on a scanner are indicative of its regular use and age. This deterioration can manifest in various ways, often as cosmetic changes, such as scratches or dents on its surface. However, the implications of wear and tear are beyond superficial blemishes. Internally, components such as the scanning bed, rollers, and hinges may degrade over time due to repeated use. This can result in misalignment or uneven movement during scans, causing image distortions or incomplete scans.
One of the critical parts susceptible to wear and tear is the scanning glass, which can accumulate scratches and scuffs. These imperfections can lead to poor scan quality by creating shadows or lines that interfere with the scanned image’s integrity. In automatic document feeders (ADF), rollers and feeder mechanisms can wear out, leading to paper jams or multiple sheets being pulled in at once, resulting in misfeeds and potentially damaged documents or equipment.
In addition to the functional components, the connectivity cables can also undergo physical wear. Fraying or loosening of the connection can result in intermittent scanning failures or the inability for the scanner to communicate effectively with the computer. Moreover, the wear on buttons or touch panels may lead to unresponsive controls, making it challenging to operate the scanner correctly.
Now, regarding the common signs or indicators that a scanner may require maintenance or servicing:
1. Decreased Scan Quality: If scanned images appear with streaks, spots, or are consistently poor in quality, this might indicate that the scanning glass, sensor, or internals require cleaning or the components need replacing.
2. Unusual Noises During Operation: Scanners should operate relatively quietly. Grinding, clicking, or whirring sounds could suggest that internal parts are malfunctioning or that there is debris inside the machine.
3. Slow Scanning Speeds: If a scanner is taking longer than usual to complete scans, this can indicate an issue with the scanner’s hardware, software, or an overfilled storage space which requires cleaning out.
4. Frequent Error Messages: Consistent errors when trying to scan could point to a software issue or failing internal components that need to be diagnosed and addressed by a professional.
Maintenance and servicing at regular intervals or when these signs present themselves can help extend the scanner’s life, ensure good scan quality, and avoid interruptions to the system’s availability and productivity. Regular cleaning and calibration may mitigate some of these issues, but it is essential to consult the scanner’s manual or a professional for proper maintenance procedures and when to seek servicing.