When selecting a shredder for office or personal use, various factors must be taken into account to ensure it meets the user’s needs. Among these considerations, the shredder’s duty cycle is a crucial element that can significantly impact its cost and energy consumption. A duty cycle in the context of shredders refers to the maximum amount of time a shredder can operate before it needs to cool down. This attribute determines the shredder’s capability to handle continuous or heavy loads, which is particularly important in environments with high-volume shredding demands.
Understanding the relationship between a shredder’s duty cycle and its cost is imperative for making an informed purchase. Shredders designed with longer duty cycles are typically built with more robust motors and cooling systems, which enable them to withstand extended periods of operation without overheating. Consequently, these enhancements can lead to a higher initial purchase price. On the other hand, shredders with shorter duty cycles may be less expensive upfront but could result in reduced productivity and potential downtimes that ultimately affect long-term operational costs.
In terms of energy consumption, the duty cycle also plays a pivotal role. A shredder that operates continuously for an extended period will use more power compared to one with frequent rest periods. Moreover, high-performance shredders with efficient cooling mechanisms may consume more energy to maintain optimal operating temperatures. This increased consumption can affect operational expenses and the organization’s carbon footprint.
The interplay between duty cycle, cost, and energy consumption requires a delicate balance. Organizations must assess their specific needs, taking into account the volume of shredding, the sensitivity of the materials being shredded, and overall budget constraints. In this comprehensive article, we will delve deeper into how a shredder’s duty cycle influences its cost—considering aspects such as initial investment, maintenance, and potential downtime—as well as its energy consumption patterns, offering insights into the most cost-effective and environmentally friendly shredding solutions.
Duty Cycle Duration and Shredder Efficiency
The duty cycle of a shredder refers to the amount of time a shredder can operate continuously before needing a cool-down period to avoid overheating. This is a critical factor in determining the overall efficiency and effectiveness of a paper shredder. Shredders are designed for varying levels of use – from light use in a home office to heavy use in a commercial setting. The duty cycle can range from just a few minutes up to an hour or more for highly resilient models.
Shredders with a longer duty cycle are often more expensive, as they are equipped with more robust motors and cooling systems capable of handling prolonged use without overheating. These shredders can process a larger volume of paper within their cycle, making them more suitable for environments with high shredding demands. Consequently, businesses with extensive shredding needs may find these more efficient machines worth the investment, despite the higher upfront cost.
When it comes to how a shredder’s duty cycle affects its cost and energy consumption, there are several factors to consider. A shredder that’s built to withstand long duty cycles will typically have a heftier price tag due to its more durable components and advanced technology. These components may include powerful motors, better quality blades, and sophisticated cooling mechanisms, all of which contribute to the overall cost of the shredder.
Energy consumption is also directly impacted by the duty cycle. Shredders with longer duty cycles tend to use more energy over time since they are designed to handle continuous operations. To manage heat generation during extensive use, these shredders may require additional energy to power cooling fans or to operate at a higher performance level. This increased energy usage will result in higher electricity bills, which is an important cost factor for businesses to consider.
However, it’s also essential to consider the efficiency gained from a longer duty cycle. In a busy office, a shredder with a short duty cycle may lead to downtime and reduced productivity as staff members wait for it to cool down. This could result in higher indirect costs related to employee time. In contrast, a shredder that can operate continuously may allow for a more streamlined workflow, reducing the overall time and labor costs associated with shredding documents.
In summary, when selecting a shredder, it is crucial to weigh the higher initial cost and energy consumption of models with a more extended duty cycle against the potential for increased productivity and efficiency in shredding operations. The right balance will depend on the specific needs of the user and the volume of shredding required.
Impact of Duty Cycle on Shredder Energy Usage
The impact of a shredder’s duty cycle on its energy usage is a significant factor in both operational cost and environmental footprint. Duty cycle refers to the length of time a shredder can operate continuously before it needs to cool down. This duration is generally guided by the shredder’s motor and its cooling capabilities to prevent overheating, which can harm its internal components.
First, a shredder with a longer duty cycle can process more material in a single go, which tends to increase energy efficiency. When a shredder is activated, it consumes power to start the motor and initiate the shredding process; if it can run longer without breaks, the relative energy consumed during startup is distributed over more sheets of shredded material, reducing the energy usage per sheet.
On the other hand, a longer duty cycle also means that the shredder is consuming power continuously over a longer period. High-performance shredders capable of extended duty cycles typically need more robust and thus more power-hungry motors, which can lead to increased energy consumption overall. Such models, designed for heavy-duty operations, often come with a higher upfront cost but are necessary for environments with large volumes of documents to shred, like offices or document management services.
The duty cycle affects cost in several ways. The initial cost of a shredder with a high-duty cycle is generally higher due to the need for more durable components capable of withstanding prolonged use. This is an investment that could pay off in commercial settings, where the time saved by employees not having to wait for the shredder to cool down can be significant.
However, energy consumption should also be considered in the total cost of operation. If a shredder is used frequently and near its maximum duty cycle, it will consume more electricity, increasing operational costs. In contrast, a shredder used intermittently may rarely reach the limits of its duty cycle, hence the added cost of a high-duty cycle shredder, in this case, may not be justified.
In summary, when considering energy usage and cost, the shredder’s duty cycle plays a pivotal role. A longer duty cycle improves efficiency in terms of sheets shredded per energy unit consumed, but it may also imply a more powerful motor, leading to higher overall energy use and costs. For organizations that require high-volume shredding with minimal downtime, the investment in a durable shredder with a long duty cycle makes sense. However, for more sporadic use, a lower-duty-cycle shredder could be more cost-effective and energy-conserving. It’s a balance between the initial investment, the expected volume of shredding, and the operational costs associated with the energy used during the shredder’s lifetime.
Duty Cycle Limitations and Overhead Costs
Duty cycle limitations play a critical role in both the upfront cost and the ongoing overhead costs of a paper shredder. The duty cycle refers to the length of time a shredder can operate continuously before it needs to cool down to prevent overheating. This limitation directly affects a shredder’s efficiency; if a shredder has a short duty cycle, it will need regular breaks, which can be a significant hindrance in environments where large volumes of documents need to be shredded regularly.
From a cost perspective, shredders with a more extended duty cycle are typically more expensive. They are engineered with more robust motors, better cooling systems, and higher-quality components that can handle extended periods of activity without overheating. This means that the initial investment is higher for these machines. However, it’s also true that with a longer duty cycle, employees can spend less time waiting for the machine to cool down and more time shredding, which can improve office productivity.
In terms of energy consumption, a shredder with a short duty cycle may seem to use less energy because it operates for less time before needing a break. However, the start-stop nature of its usage pattern might actually lead to higher energy use in the long run. Starting up a shredder requires a surge of power, which can be inefficient if repeated frequently. In contrast, a shredder with an extended duty cycle operates more consistently, which can be more energy-efficient over time.
Additionally, a shredder with a short duty cycle that is frequently operated beyond its limits may have higher maintenance costs due to the strain on its components. This will further affect the overhead costs because the shredder will need parts replaced or repairs done more often, contributing to increased operational costs. In the worst-case scenario, it could even mean the early retirement of the shredder and the need to purchase a new one, which would be an additional expense.
In summary, the duty cycle of a shredder directly impacts both the initial purchase price and the ongoing expenses related to energy consumption and maintenance. Investing in a shredder with the right duty cycle for your needs can save money and energy in the long-term, even if the initial cost is higher. It’s essential to consider both the immediate and long-term financial implications of the shredder’s duty cycle when making a purchasing decision.
Maintenance and Replacement Costs Related to Duty Cycle
The duty cycle of a shredder refers to the maximum amount of time it can operate without needing a cool-down period. This aspect of a shredder’s operation significantly influences maintenance and replacement costs. A shredder with a longer duty cycle is typically designed to handle more continuous usage, which implies that it has more robust internal components capable of withstanding the heat and wear that come with prolonged activity. As a result, shredders with longer duty cycles tend to have higher upfront costs due to their more durable construction.
However, the maintenance costs associated with these shredders are often lower per cycle of usage because the components don’t need to be serviced or replaced as frequently. High-duty cycle shredders are designed with the expectation of intensive use, so manufacturers might provide longer warranties and use better-quality materials to ensure longevity. For organizations with high volume shredding needs, the extra upfront cost might actually lead to savings over the long term as the machine endures less wear and tear for each unit of shredded material.
On the other hand, shredders with shorter duty cycles are generally less expensive to purchase but may require more frequent maintenance or replacement. The internal components might not be as resilient, and the heat generated from the motor can cause faster degradation of the machine. Consequently, these shredders are more likely to face mechanical issues or breakdowns with extensive use, leading to additional costs in maintenance, downtime, and potential replacement if the damage is extensive enough.
The energy consumption of a shredder is indirectly affected by its duty cycle. Shredders designed for longer duty cycles use energy more efficiently over their lifespan. Usually, they are equipped with more powerful motors that shred more paper per pass and thus function more effectively, which can contribute to energy savings. On the other hand, a shredder with a short duty cycle might have to run more frequently or longer to complete the same amount of work, which could increase energy consumption over time.
Finally, how a shredder’s duty cycle affects its cost and energy consumption hinges on the balance between initial investment and operational efficiency. Shredders with longer duty cycles may have higher upfront costs but will likely offer reduced long-term expenses both in maintenance and in energy usage, due to their efficient design and more durable construction. Conversely, a cheaper shredder with a shorter duty cycle might look attractive on the purchase price but could lead to higher overall costs in maintenance, replacement, and energy usage, particularly in settings where shredding needs are intensive and continuous.
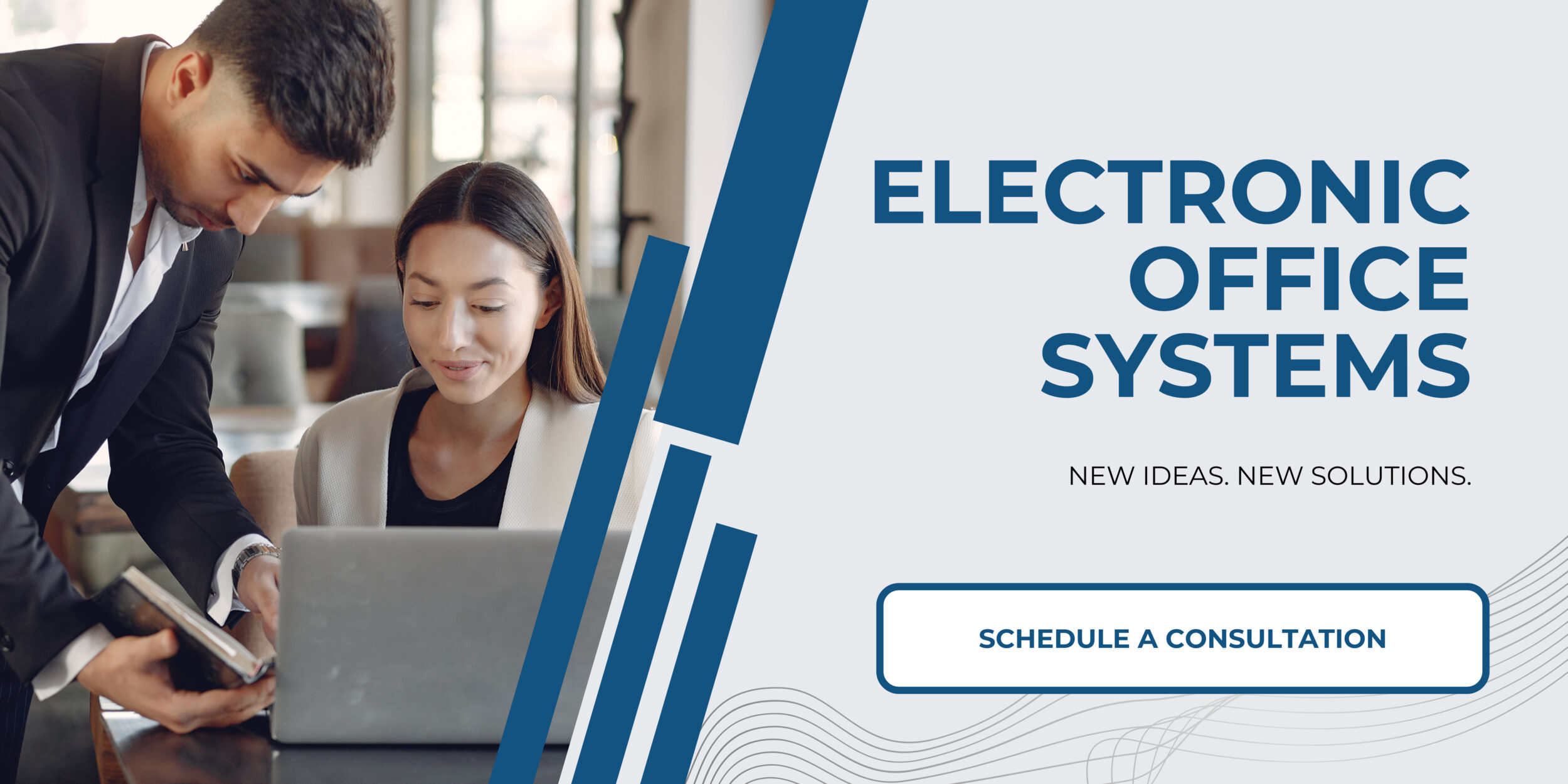
Influence of Duty Cycle on Cost per Sheet Shredded
The duty cycle of a shredder refers to the maximum amount of time a shredder can operate continuously before it needs to cool down to avoid overheating. This specification is important because it influences how quickly a shredder can handle a given volume of paper, thus affecting the overall cost efficiency when shredding large quantities of documents.
When considering cost per sheet shredded, the duty cycle is a critical factor. A shredder with a longer duty cycle can process more sheets in a single session, reducing the time needed to complete a shredding job. Consequently, this can lead to energy and cost savings because the shredder is utilized more efficiently, minimizing periods of inactivity and the associated overhead of starting and stopping the device. Conversely, a shorter duty cycle means the shredder will have to stop more frequently to cool down, which can increase the total time needed to shred the same number of pages and increase energy consumption over time due to more frequent start-up phases.
In terms of direct costs, shredders with longer duty cycles tend to have higher upfront costs because they generally incorporate more robust motors and better cooling systems that enable them to run longer. However, for high-volume shredding needs, the initial investment in a high-duty-cycle shredder can translate into savings over time, justifying the higher price point. A shredder that overheats frequently can slow down operations, causing labor costs to rise and potentially interrupting the workflow, thus indirectly affecting cost per sheet through increased labor expenses.
The influence of a shredder’s duty cycle on its energy consumption is also an important consideration. A more powerful shredder with a longer duty cycle will typically require more energy whenever it is running, but this could be offset by the reduced total operating time compared to a less powerful shredder that requires frequent breaks. As a result, the overall energy consumption must be analyzed in relation to operational efficiency and time savings, which can contribute to a lower energy cost per sheet when using shredders with adequate duty cycles for the volume of shredding required.
In summary, the duty cycle of a shredder impacts both the cost and energy consumption per sheet shredded by determining how efficiently a shredder can operate without needing a break. Balanced against the increased upfront cost of a shredder designed for a longer duty cycle, the benefits in terms of operational efficiency, energy savings, and lower labor costs can make it a cost-effective choice for businesses with large shredding requirements. However, for lower-volume needs, a more cost-effective shredder with a shorter duty cycle may be sufficient and more economical in terms of both initial investment and energy use.