Title: Exploring the Versatility and Limitations of Flatbed Scanners: Can They Scan Three-Dimensional Objects?
Introduction:
The technological landscape is continuously evolving, bringing into focus an array of fascinating devices that greatly augment our capacity to interact with the physical world. One such fascinating tool is the flatbed scanner, commonly known as an indispensable device for digitally capturing two-dimensional images such as documents, photos, or graphics. However, its abilities extend beyond the realm of flat images. One question that often arises among tech enthusiasts and professionals alike is: Can flatbed scanners scan three-dimensional objects? This question forms the basis of this article and demands an exploration of the abilities and limitations of flatbed scanners.
In principle, flatbed scanners are designed to handle two dimensions, width and length, which caters perfectly to regular documents and photographs. This design capitalizes on the uniform nature of these items, ensuring an even light distribution for optimal scanning. Nonetheless, the question persists regarding their adeptness at scanning items that introduce a third dimension, depth.
This introduction sets the stage to delve into the mechanics of how a flatbed scanner operates, its potential in scanning three-dimensional objects and the possible challenges or limitations inherent in this capability. We attempt to illuminate whether this common office device can venture into the less-charted terrain of 3D object scanning, and if so, to what extent.
Basic Understanding: How do Flatbed Scanners Work?
Flatbed scanners operate on a relatively straightforward principle, incorporating fundamental optics and digital conversion processes to produce digital documents and images. At the heart of a flatbed scanner is a charged coupled device (CCD) array, a collection of tiny light-sensitive diodes that convert the light they receive into an electrical charge. This charge is then converted into digital information, creating a digital representation of the scanned image.
When you place a document or other flat object on a flatbed scanner, a moving light source illuminates it. As the light source moves under the surface of the object, it reflects light into a series of mirrors, which directs the light into a lens. The lens focuses the light onto the CCD array, which captures the light as a series of electrical charges. These charges are then converted into digital data that the computer can interpret and reproduce as an image.
Turning to the question of whether flatbed scanners can scan three-dimensional objects, the answer is yes, with some limitations. While flatbed scanners are made primarily for two-dimensional objects like paper documents and photos, they can be used to scan small, flat-surfaced three-dimensional objects. However, the resulting scan is still a flat, two-dimensional image that only captures the surface details of the object.
There are some limitations to this capability. For instance, the size and shape of the three-dimensional object might present a challenge. If the object is too large or bulky, it may not fit properly on the scanner bed, leading to an incomplete or poor quality scan. Additionally, the scanner lid might not close properly over the object, allowing outside light to interfere with the scanning process.
Moreover, certain differences in texture or material could also affect the quality of the scan. For instance, reflective or dark surfaces may not scan well because they either reflect too much light into the CCD array or don’t reflect enough light, causing the final scan to be overexposed or underexposed in those areas. Similarly, objects with detailed or intricate surfaces might not be fully captured because the scanner light source only illuminates and captures the surface details from one angle.
Scanning Three-Dimensional Objects: Is It Possible with Flatbed Scanners?
Scanning three-dimensional objects is indeed possible with flatbed scanners. Flatbed scanners are typically known for scanning flat, two-dimensional objects like documents or photos. However, they can also be used to scan 3D objects, such as a book or a small trinket, with varying levels of success.
The main concept in flatbed scanners is a process called ‘reflective scanning.’ As the object rests on the scanner bed’s glass top, a light source travels beneath the glass, illuminating the object’s surface. A mirror reflects the light onto a lens, which directs the reflected light onto a CCD (Charge-Coupled Device). The CCD then converts the light into electrical signals, creating an image.
While this method does allow for a certain degree of depth perception, the results can be somewhat limited. The scanner’s light source only travels in one direction, limiting shadow and depth interpretation. As a result, the outline and texture of the scanned object may appear accurately, but the scanned image won’t capture the complete depth and dimensionality that one might achieve with a dedicated 3D scanner.
Concerning limitations, the nature of flatbed scanners limits them to three-dimensional objects of specific sizes. Flatbed scanners are typically rectangular-shaped and have a defined height under the lid. Thus, anything too bulky or too tall will not fit under the lid and won’t be suitable for scanning. Furthermore, accurate image translation requires the object to be in full contact with the scanning bed. This requirement often forces the object to be placed upside-down, which can be challenging or impossible with more fragile or intricately shaped objects.
In summary, while it is possible to scan three-dimensional objects with flatbed scanners, the services these devices provide are fundamentally intended for two-dimensional scans. As such, while they can capture a representation of a 3D object, the level of meticulous detail and depth a 3D scanner can produce is not achievable. For comprehensive scans of 3D objects, it’s in your best interest to consider a 3D scanning technology.
Limitations of Flatbed Scanners in Scanning Three-Dimensional Objects
Flatbed scanners, commonly used to scan two-dimensional items such as documents and photos, do possess some capability to scan three-dimensional objects. However, inherent limitations exist based on the design and operational principles of these devices.
The key constraint is the fixed focus of flatbed scanners. These devices are designed to scan items placed directly on the glass plate; the scan head moves beneath this plate, capturing data within a very narrow focal range. As such, when a three-dimensional object is placed on the scanner, parts of the object that are not in direct contact with the scan glass may appear blurred or not be captured at all. The nature of this flat surface scanning technology inherently limits depth perception, which is critical for accurately representing three-dimensional objects.
Also, the way a flatbed scanner illuminates the object being scanned can further limit the quality of a scan of a three-dimensional object. Flatbed scanners typically use a light source that moves across the object in a single pass, and this is most effective for illuminating flat objects uniformly. With three-dimensional objects, this type of illumination may fail to properly light all surfaces, leading to poor image quality in the scanned representation.
Moreover, the size of the object to be scanned is another limitation of flatbed scanners. Overly large or heavy objects may not fit within the confines of the scanner or could even cause damage.
In summary, while it is theoretically possible to scan a three-dimensional object using a flatbed scanner, the results may be of poor quality due to limitations intrinsic to the design and operation of these devices. These limitations include a fixed focal range that is optimized for two-dimensional objects, inadequate illumination of three-dimensional surfaces, and physical constraints regarding the size and weight of objects that can be reasonably scanned.
Alternative Technologies: 3D Scanners vs Flatbed Scanners
There are diverse methods of capturing digital images of physical objects available. A couple of them include flatbed scanners and 3D scanners which are alternative technologies utilized for different objectives.
Flatbed scanners are essentially utilized for two-dimensional scanning. They work in a way that involves emitting light onto the object that is being scanned. The reflected light is then detected by the scanner’s sensor, which subsequently converts it into a digital signal. This is predominantly excellent for materials such as documents, photos or artwork among others. However, it has its limitations when it comes to scanning three-dimensional objects as it may not be able to capture the depth and sides of the objects accurately.
3D scanners, on the other hand, have been introduced to overcome the limitations of the flatbed scanners. These provide more advanced technology that’s able to accurately capture three-dimensional objects in more detail. They function on the principle of capturing the depth, texture, and size of the objects which flatbed scanners are unable to. They accomplish this by sending out a laser or structured light onto the object and then capturing and processing the reflection. Therefore, for a comprehensive and accurate scan of three-dimensional objects, the usage of 3D scanners is highly suggested although they may be more expensive than the flatbed scanners.
Flatbed scanners indeed can scan three-dimensional objects but with notable limitations. These limitations stem from the fact that flatbed scanners are structured to capture flat, two-dimensional objects. Consequently, when asked to capture a 3D object, they can only effectively scan the part of the object that directly contacts the scanner bed, leaving out the depth and the sides of the object. Moreover, objects that are not perfectly flat may appear distorted or blurred due to their inability to focus at different levels of an object’s depth. Despite the limitations, they can be used for basic and quick scans of objects that don’t require too much precision or details.
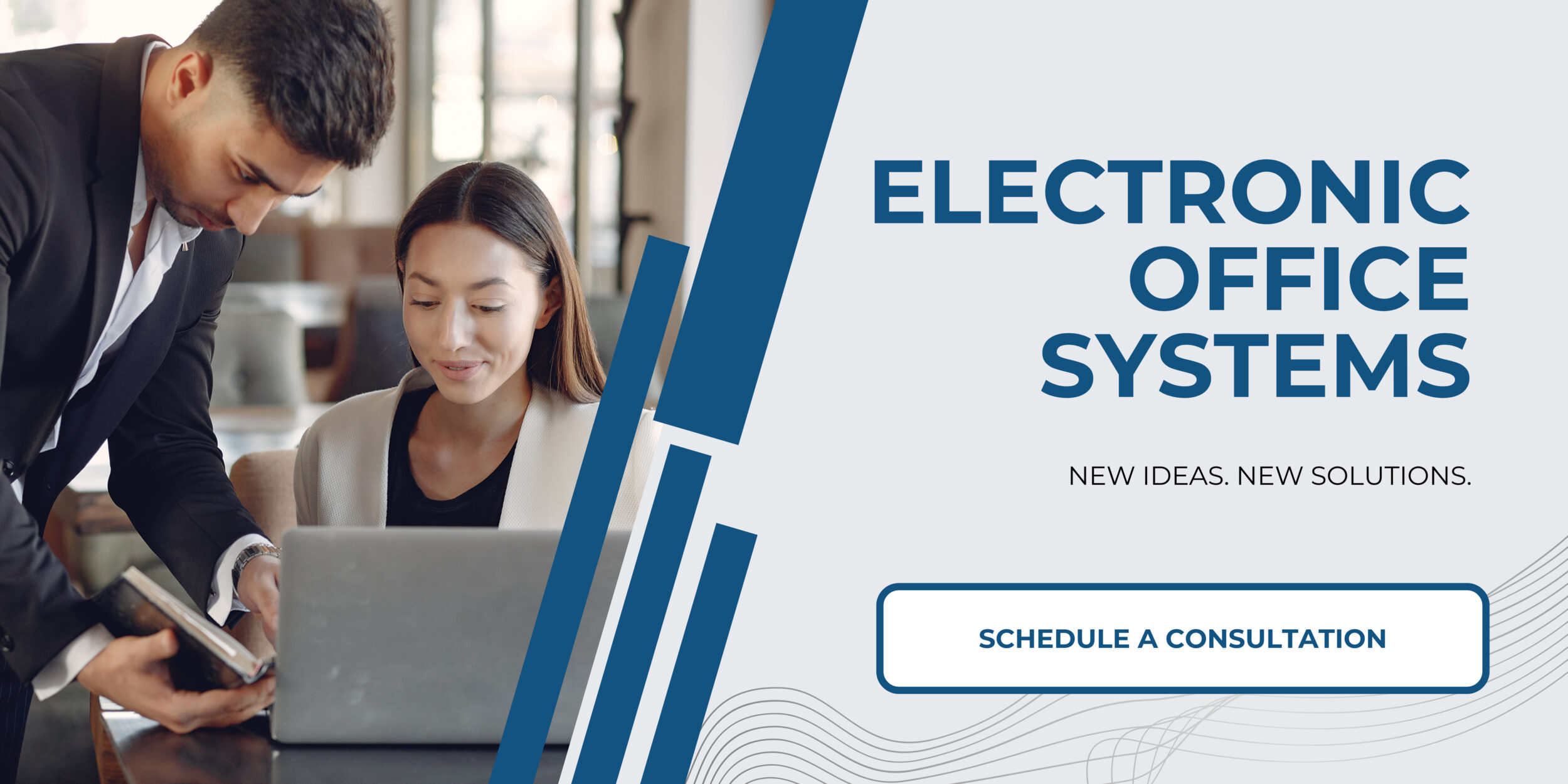
Optimizing Scans: Tips and Techniques to Scan 3D Objects on Flatbed Scanners.
Optimizing scans is an important component of using 3D objects on flatbed scanners. Though flatbed scanners are typically utilized for scanning two-dimensional objects such as documents or photos, they can also be used to scan three-dimensional objects with certain limitations.
People often need to scan 3D objects for a variety of reasons, such as archiving, digitizing for online sale, or simply for documentation. Flatbed scanners can do this job, but it requires some understanding and application of the appropriate techniques for optimizing scans.
One of the primary methods for optimizing scans of 3D objects on flatbed scanners involves the strategic placement of the object. Since the scanner captures the image based on the object’s contact with the glass, placing the side of the object that contains the most detail face down on the scanner can ensure capturing the maximum detail possible.
Lighting is a crucial factor in scanning 3D objects. The scanner uses its own light source to illuminate the object’s surface, which should be even and unimpeded to accurately capture the object’s details. Shadows or light reflections could diminish the quality of the scan, and hence objects should be carefully positioned to avoid these issues.
Finally, settings of resolution, color balance, and contrast are key factors that determine the scan’s output quality. These should be appropriately adjusted depending on the specifics of the object being scanned.
To answer the second part of your question, yes, flatbed scanners can technically scan three-dimensional objects. But there are some limitations to this ability. The most notable limitation is that flatbed scanners cannot capture the back or sides of an object, which means they only provide a two-dimensional image of a 3D object rather than a true, 360-degree 3D model. The depth of scan field is also limited, which could impact the capturing of minute details if the object is not placed correctly.
The object being scanned must also fit within the dimensions of the scanner bed. Large objects may need to be scanned in parts and then digitally stitched together, which can be complex and time-consuming. Finally, the object must be light enough to not damage the scanner glass.
In conclusion, while flatbed scanners are not the ideal tool for scanning 3D objects, with proper techniques and careful handling, they can still fulfill specific scanning needs. For more advanced or professional uses, dedicated 3D scanning devices could provide more accurate and detailed results.