The type of media or substrate used in a wide format printer can have a major impact on the feed mechanism of the machine. This is because different types of media require different levels of force and pressure to be fed into the printer in order to ensure a quality print. If the right type of media is not used, it can lead to poor quality prints as well as damage to the printer.
Wide format printers are used in a wide variety of applications, from printing posters and banners for advertising to printing on large-scale fabrics for garments. The type of substrate used is important as it affects how the media will be fed into the printer. Different substrates require different levels of force and pressure to be fed into the printer. For example, heavier substrates may require more force than lighter substrates. Additionally, substrates with a glossy finish or other special coatings may need to be fed into the printer at a slower speed to prevent damage to the printer.
In order to ensure optimal printing results, it is important to understand how the type of media and substrate used can affect the feed mechanism in a wide format printer. By selecting the right type of media, it is possible to get the best quality prints and prevent damage to the printer.
Understanding the Role of the Printer Feed Mechanism in Different Media Types
The printer feed mechanism is an integral part of any wide format printer and is responsible for moving the media from the input tray to the print head and back. This mechanism is essential as it ensures that the media is fed correctly and that the printing process is successful. The type of media used in a printer affects the feed mechanism in multiple ways, including the speed, efficiency, and precision of the feed. The type of media is also directly correlated to the thickness of the substrate and the texture of the media, both of which can affect the functioning of the feed mechanism.
The type of media used in a wide format printer can have a significant effect on the speed and efficiency of the feed mechanism. Some media, such as paper, are lightweight and are easier to transport than other types of media. This can result in faster feed speeds and increased feed efficiency. Heavier media types, such as canvas or vinyl, may require slower feed speeds as the media is heavier and more difficult to transport. Additionally, heavier media may require more power from the feed mechanism, resulting in slower feed speeds and decreased efficiency.
The thickness of the substrate and the texture of the media can also affect the functioning of the feed mechanism. Media with thicker substrates requires more power from the feed mechanism, resulting in slower feed speeds and decreased efficiency. Additionally, media with a rougher texture may be more likely to cause paper jams or misfeeds. This can lead to decreased feed speeds and decreased printer efficiency.
In conclusion, the type of media used in a wide format printer can have a significant effect on the functioning of the feed mechanism. Different types of media require different speeds and amounts of power from the feed mechanism, resulting in different feed speeds and efficiency levels. Additionally, the thickness of the substrate and the texture of the media can also affect the functioning of the feed mechanism.
Impact of Media Type on Printer Feed Efficiency and Speed
The type of media or substrate used in a wide format printer can significantly affect the feed mechanism and its performance. Generally, the feed mechanism of a wide format printer is designed to accommodate a wide range of media types and substrates. Different media types can require different types of feed mechanisms for different levels of performance and reliability. For example, heavier substrates may require a heavier-duty feed mechanism to ensure that the media is fed into the printer without disruption. On the other hand, lighter media types may require a more lightweight feed mechanism to ensure that the media is fed into the printer quickly and efficiently.
In addition to the type of media or substrate, the thickness of the substrate can also have an effect on the feed mechanism of a wide format printer. For example, thicker substrates may require a more robust feed mechanism that is capable of handling heavy substrates without disruption. On the other hand, thinner substrates may require a more lightweight feed mechanism that can efficiently and quickly feed the substrate into the printer.
The texture of the media or substrate can also affect the feed mechanism of a wide format printer. For example, smoother media types may require a lighter feed mechanism that can accurately feed the media into the printer without disruption. On the other hand, rougher media types may require a heavier-duty feed mechanism that is capable of handling the rough media without disruption.
Finally, the material of the media or substrate can also influence the feed mechanism of a wide format printer. For example, media types that are more prone to static electricity may require a more robust feed mechanism that is capable of handling the static electricity without disruption. On the other hand, media types that are less prone to static electricity may require a more lightweight feed mechanism that can efficiently and quickly feed the media into the printer.
In summary, the type of media or substrate used in a wide format printer can have a significant impact on the feed mechanism and its performance. Different types of media may require different types of feed mechanisms, as well as different levels of performance and reliability. The thickness, texture, and material of the media or substrate can all influence the effectiveness of the feed mechanism and its overall performance.
The Correlation Between Substrate Thickness and the Feed Mechanism Functioning
The feed mechanism is a critical component of wide format printers. It is responsible for pulling in the media and feeding it through the printer. One of the key factors that affects the functioning of the feed mechanism is the thickness of the substrate. Generally, thicker substrates require a higher degree of pressure to be feed through the printer, while thinner substrates may require less pressure. In addition, wider substrates may require more power and a wider feeder mechanism.
The substrate thickness can also affect the accuracy of the feed mechanism. If the substrate is too thick, the feed mechanism may not be able to pull it in correctly and the print job may be inaccurate. The substrate must be the correct thickness to ensure that the feed mechanism can accurately and precisely feed the media through the printer. This will help to ensure that the prints are accurately printed.
The feed mechanism also affects the speed of the printing process. Thicker substrates require more pressure to be feed through the printer, which can slow down the printing process. Conversely, thinner substrates may require less pressure, which can lead to faster printing speeds. Therefore, it is important to select the right substrate for the job in order to maximize the efficiency and speed of the printing process.
In conclusion, the substrate thickness is a key factor that affects the functioning of the feed mechanism in wide format printers. The substrate must be the correct thickness to ensure that the feed mechanism can accurately and precisely feed the media through the printer. The substrate thickness can also affect the speed of the printing process, with thicker substrates requiring more pressure and slower printing speeds, while thinner substrates may require less pressure and faster printing speeds. Therefore, it is important to select the right substrate for the job to ensure that the prints are accurately printed and the printing process is as efficient and fast as possible.
The Effect of Media Texture on Wide Format Printer Feed Mechanism
The texture of the media used in wide format printers can have a major effect on the printer feed mechanism. This is because the texture of the media can affect how the mechanisms interact with the paper, as well as the speed, accuracy and reliability of the feed process. Different textures can also affect how the media is held in place during printing, which can have a direct impact on the quality of the final product.
Different types of media textures can be used to achieve different printing results. For example, a smooth texture is ideal for producing high-quality, vibrant images, whereas a rougher texture is better suited for producing sharp text. In addition, some media textures can also help to reduce jams and other feed issues.
The texture of the media can also have an effect on the accuracy of the feed mechanism. If the media is too smooth, it can cause the feed mechanism to slip or become misaligned, resulting in inaccuracies in the final output. On the other hand, a rougher texture can help to keep the feed mechanism in place and reduce the risk of misalignment.
Finally, the texture of the media can also affect the speed of the printer feed mechanism. If the media is too smooth, it can cause the feed mechanism to move too quickly, resulting in a lower print speed and potentially lower quality results. Conversely, a rougher texture can help to slow down the feed mechanism, allowing for higher quality prints at a faster speed.
In conclusion, the texture of the media used in wide format printers can have a major impact on the feed mechanism. Different textures can be used to achieve different printing results, while also affecting the accuracy, speed and reliability of the feed process. Understanding the effects that the texture of the media can have on the feed mechanism is important for achieving the best possible results.
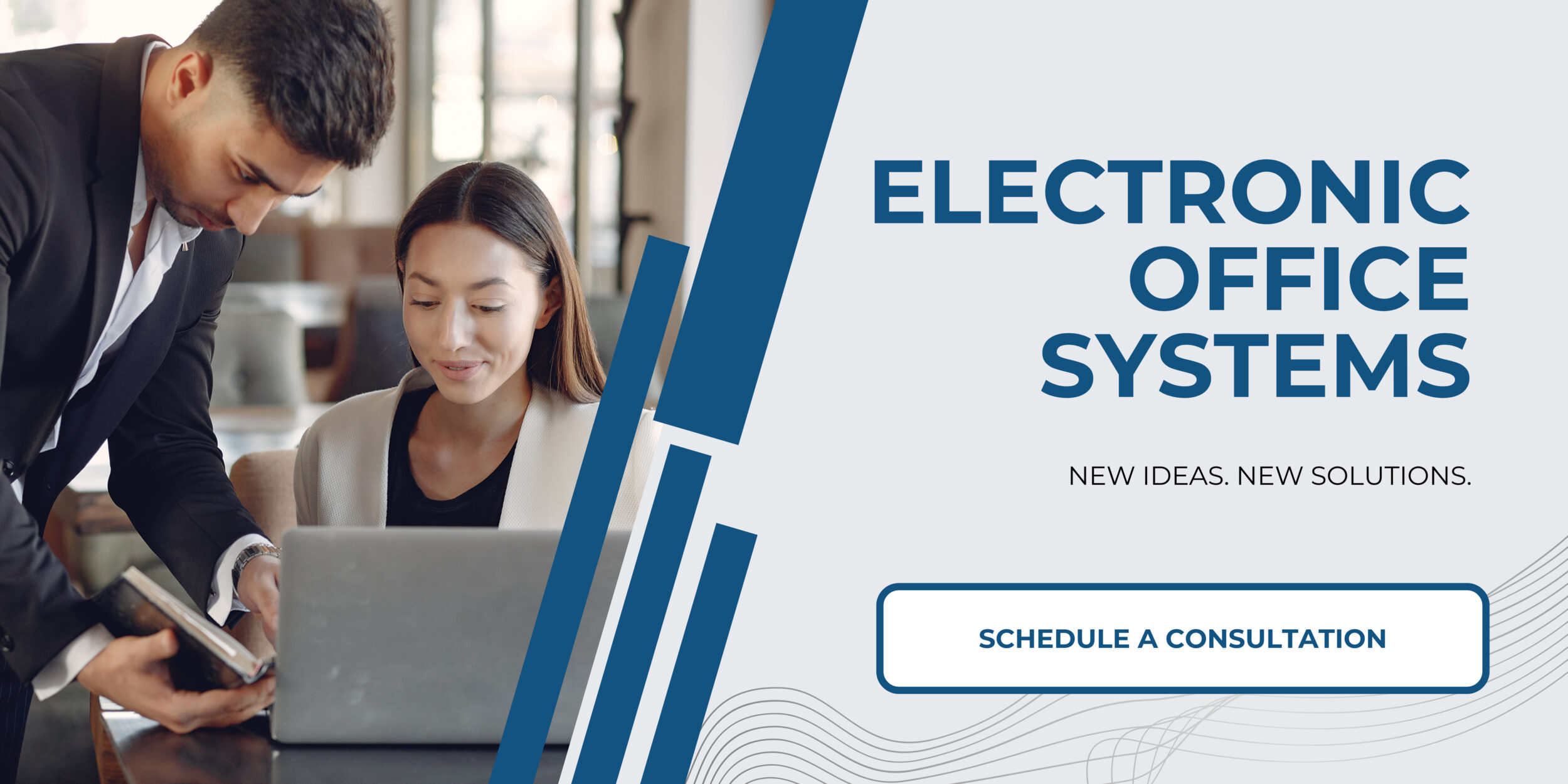
Influence of Media Material on the Precision and Alignment of the Feed Mechanism
The type of media or substrate used can have a significant impact on the feed mechanism in a wide format printer. This is due to the fact that different materials have different properties that can affect the functionality of the feed mechanism. For example, certain materials may be more prone to sticking or clogging, while others may be more slippery. This can lead to problems with the feed mechanism, such as jams, misalignment, or even damage to the printer itself. Furthermore, some materials may be more difficult to feed due to their size or thickness, which can lead to delays in the printing process.
In addition, the material used for printing can also affect the precision and alignment of the feed mechanism. Certain materials, such as thick cardstock or coated paper, may require more precise alignment of the feed mechanism in order to ensure that the printer can properly handle the material. If the alignment is not correct, the printer may experience issues such as misprints or uneven printing. This is especially true for wide format printers, which typically require a higher level of precision in order to properly handle the larger material.
Finally, the type of media or substrate used can also impact the overall quality of the final product. Different materials may absorb ink differently, which can lead to variations in the color or clarity of the final product. Additionally, certain materials may be more prone to fading or discoloration over time, which can lead to a lower quality product. Therefore, it is important to consider the type of substrate used when selecting a wide format printer, as this can have a significant impact on the overall quality of the final product.