In an age where information security is paramount, the paper shredder stands as a sentinel against the misuse of printed materials. As essential as its forward function is for chopping up sensitive documents into confetti, the reverse function plays an equally critical role in maintaining the machine’s effectiveness and the user’s safety. The ability to reverse the cutting mechanism helps to alleviate paper jams, prolong the shredder’s life, and protect against accidents. This article delves into the mechanics and design principles behind the reverse function of a paper shredder, offering insights into how this deceptively simple feature ensures the device’s reliable operation.
At first glance, the reverse function seems straightforward—it allows the motor to change direction, backing the blades away from their relentless march forward. However, the processes and components that enable this functionality are ripe with engineering nuances. The design intricacies involve electrical circuitry, motor configuration, and the physical layout of the shredding blades themselves. We will explore how manufacturers have integrated electronic controls, sensors, and mechanical designs that work in tandem to facilitate the reverse function.
Understanding how the reverse function operates in a paper shredder not only shines a light on the ingenuity behind everyday office machinery but also informs users on best practices for proper maintenance and handling of the device. Whether it’s a simple strip-cut or a complex cross-cut shredder, the principles remain consistent. From the simple act of flipping a switch or pressing a button to the complex interaction between components, we will dissect the workings of this indispensable feature. This article aims to arm readers with knowledge, shedding light on how the reverse function in a paper shredder works—from its necessary role in operational efficiency to its critical contribution to user safety.
Mechanical Configuration of Reversing Mechanism
The mechanical configuration of the reversing mechanism is a critical component of a paper shredder’s design that ensures the device can effectively back out paper in the event of a jam or when the user activates the reverse function. This mechanism typically consists of various gears, levers, and sometimes a reversing switch, working in conjunction with the motor to change the direction of the cutters’ movement.
The cutters in a paper shredder are designed to rotate in a forward direction to draw in and cut the paper into strips or cross-cut pieces, depending on the shredder’s design. When reversing, the shredder’s motor changes rotation, which in turn causes the gears interconnected with the cutter blades to reverse their direction. This action pushes the paper back toward the user, allowing for the removal of the jammed material. The mechanical configuration must be robust enough to handle the potential strain caused by reversing the tightly compacted paper caught in the shredding mechanism.
In most shredders, this function is initiated either manually by a user or automatically by sensors that detect a jam. Manual initiation typically involves a user switching a control—usually a sliding switch or button—to the reverse setting. Once activated, the motor’s operation is inverted, causing the blades to spin in the opposite direction via the internal gear system specifically designed to handle both forward and backward rotations.
Automatic reversal, when included, is often a safety and convenience feature. In this case, the shredder senses an overload condition either through mechanical detection (where the resistance to the cutter’s motion exceeds a certain threshold) or through electrical sensing (detecting a spike in current draw which signifies a jam). This triggers the reversal process without user intervention. The aim is to clear any obstruction and protect the shredder’s motor from overheating or sustaining damage due to the stress of a jam.
The reverse function in a paper shredder works by employing a combination of electrical and mechanical elements. When the shredder detects a jam or when the user activates the reverse mode, an electrical signal is sent to the motor to reverse its direction. The motor, which is typically a universal motor in smaller shredders or an induction motor in larger, commercial-grade machines, has the ability to rotate in both directions. Once the signal to reverse is received, the motor changes the polarity of its electric fields or adjusts its phase relationships (for AC induction motors), effectively reversing its rotation.
This reversal of the motor’s direction is transferred to the shredding mechanism’s cutting blades via a gearbox or drive belt system. The gearbox consists of gears that can change the rotational movement necessary to drive the blades backward. In some models, the switching between forward and reverse is achieved through electrical relays or switches that alter the current flow, while in others, a physical swap between gear settings is used.
This bidirectional capability is essential not only for clearing out jams but also for maintaining the shredder. For example, if maintenance is required on the cutting blades, the reverse function can help in expelling any remnants of paper or debris before the unit is opened.
In conclusion, the reverse function of a paper shredder is a vital feature that significantly contributes to the usability and maintenance of these devices. By combining mechanical gears and levers with an electric motor that can change its rotational direction, shredders are equipped to effectively respond to paper jams, reduce user frustration, and extend their operational life.
Electrical Circuitry and Control for Reversal
Item 2 from the numbered list, Electrical Circuitry and Control for Reversal, plays a critical role in the functionality of a paper shredder, especially when it comes to dealing with paper jams or operational errors. This system encompasses the selection of appropriate electrical components, the design of the circuit, and the integration of control mechanisms to manage the reversal of the shredder blades.
The electrical circuitry in a shredder is designed to allow the motor to run in both forward and reverse directions. The control for reversal is frequently managed by a switch or a button that the user can press, prompting the electric motor to change direction. In some more advanced models, this process may be automated.
The switch to reverse the motor is connected through the circuit to the motor’s power supply. When activated, it causes a change in the polarity of the voltage applied to the motor, which in turn reverses the motor’s rotational direction. This ability to reverse is integral in dislodging jams from the cutting mechanism. The motor needs to have the proper torque and reversal capabilities to handle the various loads it encounters during operation. Also, safety elements are often built into the circuitry to prevent the shredder from overheating or drawing too much current.
The control system might be as simple as a user-interface with a basic switch, or it might involve more complex electronics that can automatically sense when a jam is about to occur and initiate the reverse function. The latter systems are particularly beneficial; they often include sensors that detect an impending jam due to an overload of paper, prompting the system to automatically reverse the motor’s direction to prevent the jam from occurring, or to clear the jam if it has already begun.
The reverse function in a paper shredder is crucial not only for maintaining the device’s functionality and prolonging its lifespan but also for user convenience. By allowing users to quickly and effectively address jams without disassembling the shredder or manually removing the stuck paper, the electrical circuitry and control for reversal provide an indispensable feature in modern shredding devices. Additionally, by integrating this feature into the electrical circuitry, shredders can offer a seamless operation experience and enhanced safety measures, reducing the risk of injury or damage to the shredder.
Sensor and Detection Systems for Jam and Overload
Sensor and detection systems play a critical role in the operation of a paper shredder, especially when it comes to preventing and managing paper jams and overloading. These systems are designed to detect when too much paper has been fed into the shredder or when a jam is about to occur, which could potentially damage the machine or cause it to malfunction.
At the heart of these detection systems are sensors that monitor the workload on the shredder’s motor and the paper feed’s resistance. The most common types of sensors used in paper shredders are mechanical and optical sensors. Mechanical sensors may include tactile switches or levers that are triggered when the paper exceeds a certain thickness or when pressure builds up due to a jam. Optical sensors, on the other hand, can detect the presence of paper passing through the entry slot and determine if the stack is too thick or if paper is entering unevenly, which could signal a potential jam.
These sensors continuously send data back to the shredder’s control system. In the event that an irregularity is detected, such as excessive paper thickness or a noticeable increase in motor strain, the control system can then automatically initiate the reverse function. This reverse function is designed to roll back the cutting blades and eject the paper that is causing the issue, thus preventing a jam or damage from occurring.
When discussing the reverse function in a paper shredder, it’s important to understand that this mechanism is employed to both protect the shredder’s internal components and ensure user safety. When the detection system signals that a jam is imminent or has occurred, the electrical control system triggers the motor to reverse its rotation. This change in motor direction causes the cutting blades or rollers, which usually move in a forward direction to shred paper, to rotate backward. By doing so, the blades push the jammed paper back out toward the user, making it easier to remove and clear any obstruction.
Moreover, the reversibility feature allows for easy maintenance and troubleshooting of the shredder. In case of a jam, instead of forcing the paper out, which can further damage the shredder, the user can simply rely on the reverse function to gently eject the problematic material. This not only helps in maintaining the longevity of the shredder but also reduces the risk of injury to the user who might otherwise attempt to manually remove a jammed paper.
In summary, the sensor and detection systems in paper shredders are integral to preventing overloads and managing paper jams by detecting anomalies during operation and activating the reverse function to keep the shredder functioning efficiently and safely. This combination of smart technology and mechanical design ensures that paper shredders remain useful and durable office tools while minimizing potential safety hazards.
Manual and Automatic Reversal Features
Regarding paper shredders, the manual and automatic reversal features are critical aspects that enhance the functionality and user experience of these devices. These features are designed to address potential paper jams and overloads that can occur during the shredding process.
Manual reversal is the user-operated function that allows individuals to physically switch the shredding operation into reverse gear. If a person notices that the shredder is struggling to process the inserted paper, they can prevent a jam by manually activating the reverse function. This is typically done by toggling a switch or pressing a button on the shredder. Once activated, the shredder’s rollers or blades rotate in the opposite direction, backing the paper out towards the user for removal. This helps to clear any immediate obstruction and prevents further complications such as potential damage to the shredding mechanism or overheating due to motor strain.
Automatic reversal, on the other hand, is a sophisticated feature that employs sensors to detect when a paper jam is imminent or already occurring. These sensors monitor the stress on the shredder’s motor or the thickness of the paper being fed into the machine. Upon sensing an overload or jam, the shredder automatically triggers its reverse function, causing the rollers or blades to rotate in reverse and push the paper out. This automatic response is particularly useful as it helps to maintain the shredder’s performance and longevity by preemptively addressing issues without user intervention.
The reversal function in paper shredders, whether manual or automatic, operates by changing the direction of the motor, which in turn rotates the shredding mechanism in the opposite direction. The effectiveness of the reverse function relies on the shredder’s ability to change rotational direction quickly and with sufficient torque to overcome the resistance caused by the jammed paper. The shredder’s design usually includes a gear train that enables the change in direction without causing damage to the internal components.
High-quality shredders with reverse functions are equipped with durable and powerful motors capable of handling frequent reversals. This feature not only adds convenience for the user but also plays a significant role in preserving the shredder’s operative life.
In conclusion, the manual and automatic reversal features in paper shredders are essential for mitigating the risks of paper jams and ensuring smooth operation. The ease of clearing jams and preventing damage to the machine makes these features indispensable for both personal and professional shredding tasks. The automatic reversal feature, in particular, represents an advanced aspect of shredder design, reflecting a user-friendly approach and a commitment to hassle-free maintenance.
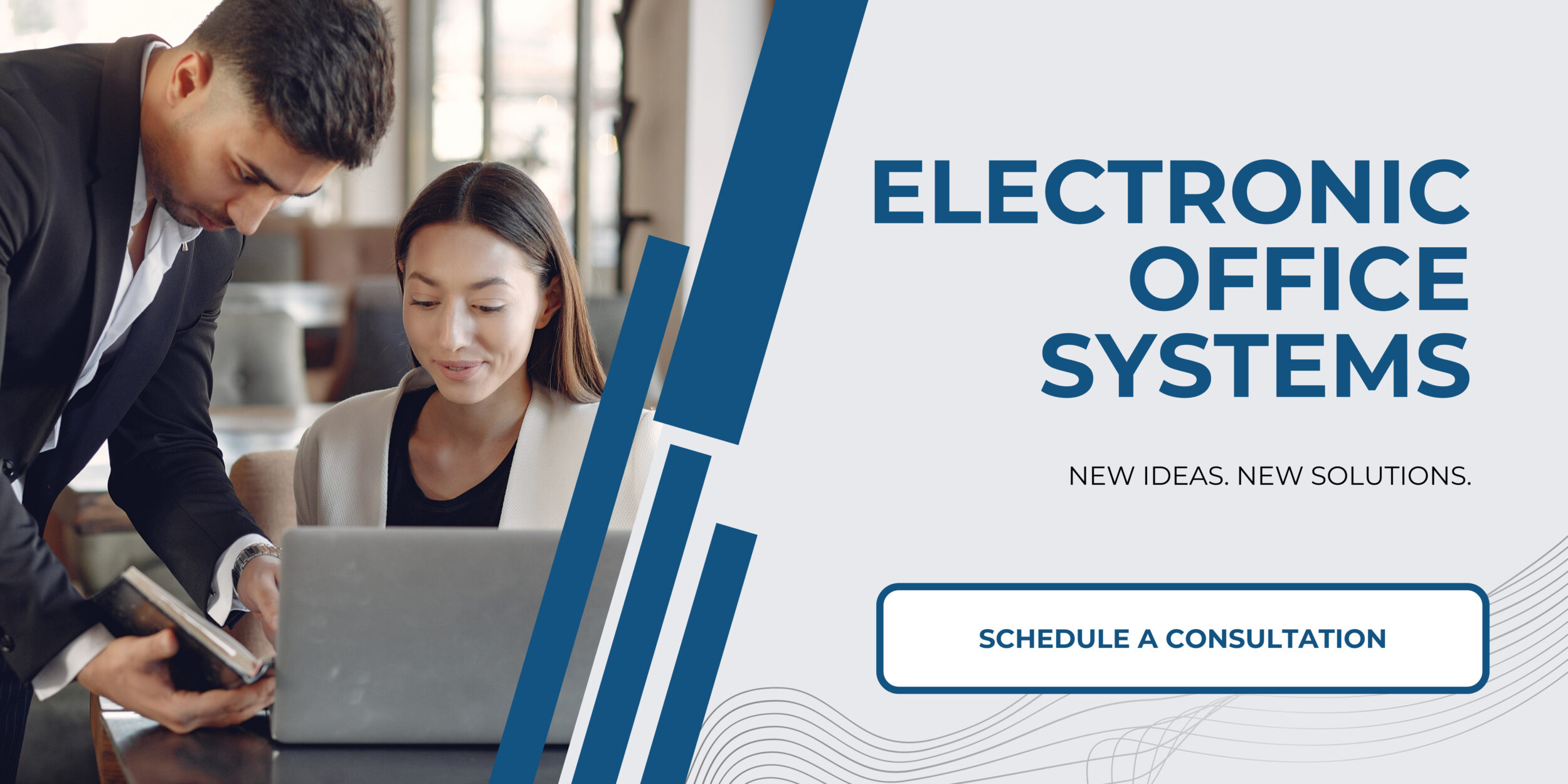
Safety Considerations for Reverse Function
Safety considerations for the reverse function in paper shredders are an essential aspect of the design and operation of these devices. Manufacturers prioritize the inclusion of various safety features to protect users and ensure a safe interaction with the shredder, particularly when the reverse function is in use.
When a paper shredder encounters a jam or excessive load, the reverse function can be a critical tool for resolving the issue without causing harm to the user or further damage to the shredding mechanism. However, even the act of reversing the shredder can pose risks, such as the potential for ejected material that could cause injury or the risk of overheating if the motor strains to clear the jam.
To address these concerns, manufacturers incorporate key design elements and protections within the paper shredder. One of the most fundamental safety features is the inclusion of an accessible reverse switch or button that allows the user to quickly engage the function without placing their hands near the shredding blades. Additionally, sensor and detection systems can automatically trigger the reverse function when a jam is detected, preventing further entanglement and thus reducing the risk of overheating or motor damage.
To prevent accidental activation of the shredder’s reverse function, there may be safety locks or double-activation mechanisms that require the user to confirm their intention to reverse. This negates the likelihood of unintended operation, especially around children or in busy office environments where an unexpected reversal could be dangerous.
Design considerations also include creating a clear and intuitive user interface that provides instructions or warnings associated with the reverse function. Such interfaces may include color-coded controls, pictograms, or audible alerts that signal the activation or deactivation of the function, guiding users to operate the shredder safely.
An auto-stop feature can be implemented, which halts all shredder functions if certain safety criteria are not met. For example, if the shredder head is lifted or the waste bin is removed, the shredder will automatically stop running, including any ongoing reverse operation.
In more advanced shredders, electronic detection systems monitor the stress levels on the cutting mechanism and motor, preemptively engaging the reverse function before a jam becomes severe enough to pose a safety hazard or machine damage. These systems can help maintain the shredder’s longevity and user safety by avoiding the consequences of a full-blown jam.
Moreover, thermal protection measures are put into place to protect the motor from overheating. If the shredder gets too hot, perhaps from reversing multiple jams in quick succession, thermal sensors will shut down the machine to prevent any possible injury from overheating components or even fire hazards.
Safety testing and certification by recognized standards agencies ensure that the shredder meets established safety criteria. Compliance with such agencies’ guidelines reassures users that the reverse function has been designed with thoughtful consideration to prevent accidents or injuries.
In summary, the reverse function in paper shredders is accompanied by a myriad of safety considerations aimed at safeguarding users and maintaining the integrity of the shredding mechanism. These include the careful design of control elements, the implementation of automatic safety features, and adherence to rigorous safety standards to prevent injury and equipment damage.