Title: Understanding the Link Between Run Time and Overheating Risk in Paper Shredders
As the demand for secure disposal of confidential documents has risen, paper shredders have become an indispensable tool in offices and homes alike. However, with increased usage comes the potential risk of overheating, which not only poses a safety hazard but can also diminish the longevity and efficiency of the shredding machine. A common question posed by users is: Does a longer run time correlate with a higher risk of the shredder overheating? This article will delve into the intricacies of shredder operation, the impact of prolonged usage on the machine’s temperature, and what manufacturers and experts say about the correlation between run time and overheating risk.
In the quest to understand this link, we must first consider the design and functionality of a shredder. Shredders are built with varying capacities and duty cycles that dictate how long they can operate before needing a rest period to cool down. These specifications are not just random numbers; they are carefully calculated based on the motor’s capabilities and the heat dissipation features of the device. Furthermore, factors such as the quality of the shredder, the thickness of the material being shredded, and the ambient temperature of the environment can also influence the likelihood of overheating.
While manufacturers provide guidelines on the recommended run time to prevent overheating, real-world usage does not always align with these recommendations. Consequently, a deeper exploration into the consequences of ignoring these guidelines is essential. Not only can this lead to a temporary malfunction due to thermal cutoffs, but it can also cause irreparable damage to the internal components, resulting in costly repairs or replacements.
Therefore, in this comprehensive analysis, we will evaluate whether a longer run time truly correlates with a higher risk of a shredder overheating. We will examine empirical evidence, expert opinions, and anecdotal accounts to offer a nuanced understanding of the relationship between shredder use and overheating. Join us as we navigate through the nuances of shredder maintenance, operational best practices, and the steps you can take to ensure your shredder functions optimally while mitigating the risk of overheating.
Shredder Motor Specifications and Duty Cycle
The motor specifications of a shredder are crucial in determining its performance, endurance, and suitability for different shredding tasks. At the heart of these specifications is the duty cycle, which represents the recommended amount of time a shredder can operate continuously without needing a rest period to cool down. This is directly influenced by the motor’s power, rated in watts or horsepower, and the efficiency of the motor itself.
A typical duty cycle may specify that a shredder can run for a certain number of minutes, followed by a longer cooling-down period. For example, a light-duty shredder may have a duty cycle of 2 minutes on and 25 minutes off, while a commercial-grade shredder might operate continuously for 30 minutes or more before requiring a cooling period.
The duty cycle directly links to the motor’s quality and thermal protection mechanisms. High-performance shredders come equipped with motors that can handle larger volumes of material and have better endurance for maintaining operation without overheating. Some models feature sophisticated motor technologies, like thermal overload protection, which automatically shuts off the shredder to prevent damage from excess heat.
As for the relationship between a longer run time and the risk of shredder overheating, it is often directly proportional. The longer a shredder runs, the more heat it generates. Without adequate cooling periods, the motor’s temperature can rise to a point where it may cause the shredder to malfunction or incur permanent damage. This is why adhering to the recommended duty cycle is essential. It balances work and rest periods in a way that prevents overheating while allowing the users to complete their shredding tasks efficiently.
Furthermore, some shredders are equipped with features designed to manage heat accumulation. This might include fans or heat sinks that dissipate heat more effectively, allowing for longer run times without an increased risk of overheating. This underscores the importance of understanding a shredder’s motor specifications and duty cycle for optimal operation and longevity of the equipment. Users should look for a shredder that matches their volume needs with an appropriate balance of run time and rest time to reduce the risk of heating issues.
Heat Dissipation and Cooling Systems in Paper Shredders
Heat dissipation is a crucial aspect of the design and operation of paper shredders, especially for units that are intended for heavy or continuous use. When a paper shredder operates, the motor and cutting mechanisms generate heat as a byproduct of the mechanical action and friction involved in shredding paper. This heat must be managed effectively to prevent the machine from experiencing excessive temperatures that could lead to malfunction, reduced lifespan, and safety hazards.
The cooling systems in paper shredders are designed to manage and dissipate this heat. They often include vents and fans that help circulate air around the motor and cutting blades. In some more advanced or industrial models, there may be additional heat sinks or cooling components that effectively transfer the heat away from critical parts of the shredder to prevent overheating. The design and materials used in the shredder also have an impact on heat dissipation; for example, metal components can help to distribute and dissipate heat more effectively than plastic components.
Does a longer run time correlate with a higher risk of the shredder overheating? Generally, yes, the longer a shredder runs, the more heat it generates, increasing the risk of overheating. However, this is not the only factor at play. The risk of overheating also depends on the shredder’s design, such as its motor specifications, the presence and efficacy of its cooling systems, and its recommended duty cycle—the period the shredder can operate continuously before needing to rest. Manufacturers usually specify a maximum recommended run time and a necessary cool-down period to prevent the motor’s temperature from reaching critical levels.
Consequently, users should be mindful of the shredder’s duty cycle and adhere to the recommended balance between run time and rest time. Failing to do so can lead to overheating, and frequent overheating can permanently damage the shredder’s motor and other critical components, leading to a reduction in its overall lifespan and performance. It is also important to note that high-volume shredding demands robust cooling systems and a more extended duty cycle to mitigate the risk of overheating. Regular maintenance and ensuring the shredder is not tasked with more than its designed capacity are also key to preventing overheating.
Run Time vs. Rest Time Ratios
The concept of run time versus rest time ratios is critical in the context of paper shredders. The ‘run time’ refers to how long the shredder can operate continuously before it needs to stop to cool down, while ‘rest time’ pertains to the cooldown period required before the shredder can safely resume operation. This ratio is typically provided by the manufacturer and is an important specification when considering the durability and operational efficiency of a shredder.
Longer continuous run times may offer convenience for shredding large batches of documents; however, this may indeed carry a higher risk of the shredder overheating. Here’s why: shredders generate a significant amount of friction and heat as they cut through paper, especially in high-volume or heavy-duty shredding tasks. The motor within a shredder is designed to tolerate heat to a certain extent, but beyond its thermal threshold, there is a risk of overheating.
Overheating can threaten the longevity of the shredder, potentially damaging the motor and other components. It is a result of the motor’s working beyond its capacity, leading to the breakdown of lubricating oils, deformation of parts, and eventual motor burnout. The risk is pronounced in shredders with poor heat dissipation mechanisms or those without sufficient time allocated for cooling down.
To ensure that a shredder operates within safe temperatures, manufacturers may recommend a specific run time to rest time ratio. For example, a common ratio may be 30 minutes of run time followed by 40 minutes of rest. Adhering to these guidelines is vital to prevent overheating and maintain the shredder’s performance and longevity.
In conclusion, a longer run time does correlate with a higher risk of the shredder overheating, especially if the manufacturer’s recommended run time to rest time ratio is not strictly followed. However, the correlation must be weighed against the shredder’s design specifications such as quality of build, the presence of effective cooling systems, and the anticipation of the user’s needs in the designing phase. It is the responsibility of the user to understand and adhere to recommended operational protocols to ensure the shredder functions safely and efficiently over an extended period.
Types of Materials Being Shredded and Their Impact on Overheating
The fourth item on the list, “Types of Materials Being Shredded and Their Impact on Overheating,” is an important aspect of how shredders operate and their longevity. Different shredders are designed to handle various materials, ranging from light paper to heavy-duty items like credit cards, CDs, and thick stacks of paper. The type of material being shredded can have a significant impact on the potential for a shredder to overheat.
When a shredder is designed for light use, such as shredding standard office paper, it features a less robust motor and heat dissipation system. However, if thicker materials or non-paper items are frequently processed, the shredder’s motor has to work harder, which generates more heat. This excess heat, if not dissipated effectively, can lead to the shredder’s motor overheating, which not only temporarily stops the device from operating but might also shorten its lifespan.
Moreover, shredders that are fed materials they are not designed for could encounter increased resistance that strains the motor. For instance, shredding cardboard, heavier paper stocks, or multiple items at once generates additional friction and heat. The cutting blades can become jammed, causing the motor to overwork and overheat as it tries to power through the jam.
In addition to the type of materials, the size and the feed rate at which items are shredded can also contribute to overheating. A high volume of materials or feeding items too quickly into the shredder does not allow the motor to cool down between tasks, exacerbating the accumulation of heat within the system.
Addressing the question of whether a longer run time correlates with a higher risk of the shredder overheating, the answer is generally yes. Most shredders have a maximum recommended run time, referred to as the “duty cycle,” which indicates how long they can operate before they need a cool-down period. When a shredder is used for longer than the recommended duration, it does not get a chance to dissipate the heat efficiently, causing the temperature of the motor to rise and increasing the risk of overheating.
It’s essential to adhere to the manufacturer’s guidelines regarding both the types of materials suitable for shredding and the duration of use. This ensures that the shredder functions correctly and has a longer useful life. Regular breaks during prolonged shredding tasks can prevent the machine from reaching excessive temperature thresholds, which could lead to a thermal shutdown or permanent damage. Shredders that are better equipped with advanced cooling systems or higher specifications may tolerate longer run times but will still have practical limits to prevent overheating.
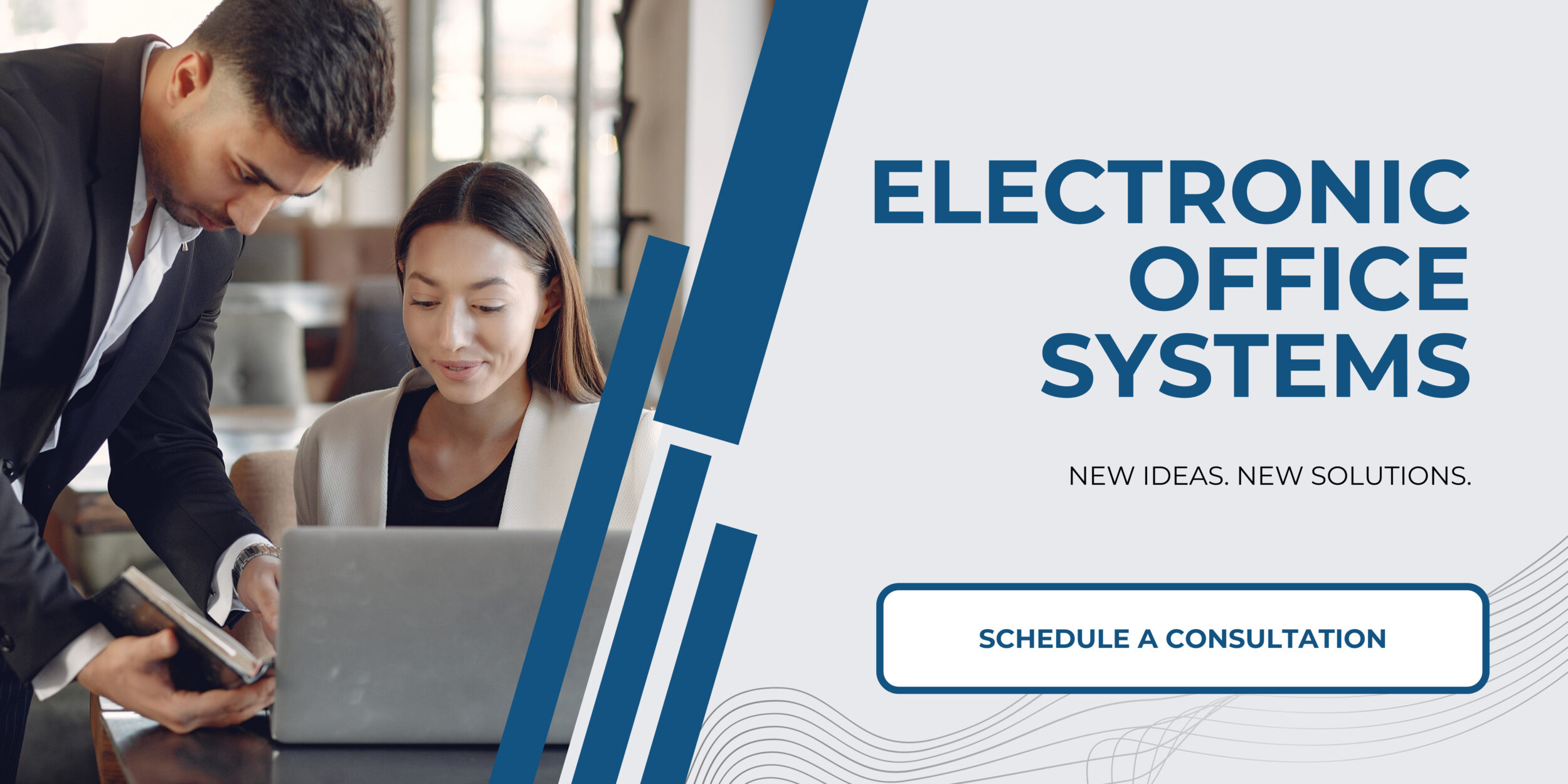
Maintenance and Care Practices for Shredders to Prevent Overheating
Regular maintenance and proper care are critical for keeping paper shredders operating efficiently and for preventing overheating. Overheating can be a significant issue because it not only reduces the lifespan of the shredder but also poses safety hazards. Effective maintenance and care practices for shredders involve several steps:
First, it’s essential to clean the shredder blades regularly. Paper dust and other materials can accumulate between the blades, which can cause increased friction during operation and lead to overheating. Compressed air can be used to blow out particles from the blades, or a vacuum with a nozzle attachment can remove the accumulated debris.
Second, lubricating the shredder is a significant preventative measure. Special shredder oil or a manufacturer-recommended lubricant should be applied as directed, typically after a specified number of uses or when the shredder starts to make unusual noises or run slower than usual. The lubrication helps to reduce blade friction, which not only minimizes the risk of overheating but also ensures smoother operation and prolongs the shredder’s life.
Third, it is crucial to avoid overfeeding the shredder with more paper than it can handle at one time. Shredders have specific sheet capacity limits that should not be exceeded. Overfeeding can strain the motor, increase the amount of heat generated, and cause faster wear and tear.
Lastly, respecting the shredder’s duty cycle by alternating between periods of usage and cool-down is vital. Continuous use beyond the recommended runtime can rapidly increase internal temperatures, risking motor damage and overheating. Adhering to the manufacturer’s guidance on run time versus rest time ratios helps prevent these issues.
In regards to whether a longer run time correlates with a higher risk of the shredder overheating: yes, it does. The longer a shredder runs continuously, the more heat is generated by its motor. Most shredders are designed to operate for a certain period – known as the duty cycle – after which they require a cool-down period. This is because prolonged use generates heat buildup that cannot be dissipated quickly enough, potentially resulting in an automatic shut-off to prevent damage (if the shredder has a thermal protection feature) or, in extreme cases, a more serious malfunction or fire hazard. It’s critical for users to adhere to the recommended run time to rest time ratio to ensure the longevity and safety of their shredding equipment. Proper rest periods allow the motor to cool down, ultimately reducing the risk of overheating and maintaining shredder performance and durability.