In the world of document shredding and printing, the distinction between auto feed and manual feed mechanisms can significantly impact efficiency and ease of use in both office and industrial settings. Auto feed technology, which allows a stack of papers to be processed automatically without the need for individual sheet feeding, contrasts sharply with the more hands-on approach required by manual feed machines. This difference raises important questions about the comparative advantages and disadvantages of each method in terms of time management, user workload, and overall workflow productivity.
Auto feed systems offer a clear advantage in efficiency for users who need to shred or print large volumes of documents regularly. By enabling the user to load a significant quantity of paper into the machine at once, there’s a reduction in the time spent standing by the equipment, feeding it sheet by sheet. This can translate into sizable time savings and a smoother, more streamlined operation especially beneficial in environments where time is a critical factor. Furthermore, this technology often integrates with features that reduce paper jams and handle various paper weights, making the process even more efficient.
On the other hand, manual feed machines typically require the constant presence of an operator to insert documents individually, which could lead to a slower overall process. However, they can offer more precise control over each print or shred job and may be seen as an advantage when dealing with sensitive documents, special media types, or when only a small quantity of documents need to be processed. Manual feeds can also be less expensive and more suitable for smaller businesses or personal use where the volume of documents doesn’t justify the investment in auto feed technology.
Therefore, understanding the nuances of auto feed and manual feed, from speed to user interaction and beyond, is crucial for businesses and individuals looking to optimize their document management practices. This article will delve into the specifics of auto feed and manual feed mechanisms, comparing their efficiency and ease of use, and examining scenarios where each might be the best fit. Whether for a home office or a corporate environment, selecting the right feeding mechanism can make a profound difference in productivity and operational efficiency.
Comparison of time efficiency between auto feed and manual feed systems
The comparison of time efficiency between auto feed and manual feed systems is a critical consideration in various industries that rely on processing materials, parts, or documents. The difference in time efficiency can significantly influence overall productivity, costs, and the ability to meet production deadlines.
Auto feed systems are designed to automate the process of feeding materials into a machine for processing. This feature allows continuous operation without the need for human intervention, reducing the time between successive operations. Because of automation, auto feed systems can ensure that the material feed rate is consistent and optimized for the machine’s processing speed. Consequently, the seamless integration between material feeding and processing can dramatically improve time efficiency, especially in high-volume production settings.
In contrast, manual feed systems require an operator to physically handle materials and feed them into the machine. This process tends to be slower and subject to variability, as operators may have different speeds and efficiencies. Furthermore, factors such as fatigue, attention lapses, and human error can introduce delays and inconsistencies, impacting the overall time efficiency. The requirement for manual intervention also means that the machine may sit idle between feeds, waiting for the operator to prepare and position the next batch of material.
When comparing the two methods in terms of efficiency, auto feed systems typically come out ahead. They are generally faster, more consistent, and can operate for extended periods without rest, aligning closely with the demands of high-throughput environments. They also reduce the likelihood of bottlenecks that can occur in manual feed operations where the operator is not keeping up with the machine’s capacity, which can cause downtime and disrupt workflow.
In terms of ease of use, operators may find auto feed systems more comfortable to work with over long periods, as these systems minimize the need for constant physical interaction. Manual feed systems, while simpler in design and perhaps requiring a lower initial investment, demand more physical effort and attention from the operator, which can lead to fatigue and reduce efficiency over time.
In summary, auto feed systems have a distinct advantage over manual feed systems regarding time efficiency and ease of use. Their automated nature allows for continuous operation without the pauses and variability introduced by human operators. This leads to faster processing times and less potential for human-induced errors, making auto feed systems the preferred choice for operations looking to maximize efficiency and throughput.
Differences in user effort and physical strain
The differences in user effort and physical strain between auto feed and manual feed systems are significant and have implications for workplace efficiency and employee well-being. Auto feed systems are designed to automatically supply material to a machine or processing line with minimal human intervention, which dramatically reduces the amount of physical effort required from the worker. This automation allows employees to focus on supervisory tasks instead of repetitive and physically demanding labor.
Manual feed systems, on the other hand, require the user to physically handle materials and feed them into the machine. This process can be labor-intensive and may involve lifting, reaching, bending, and other movements that can lead to physical strain over time. Workers engaged with manual feeding tasks are at a higher risk of suffering from musculoskeletal disorders, fatigue, and other work-related injuries.
In terms of efficiency, auto feed systems are generally more consistent and faster than manual feeding. Once an auto feed system is set up and calibrated, it can feed materials at a constant rate without the variations in speed and accuracy that might occur with a human operator. This consistency can lead to higher throughput and reduced chances of errors or jams, which can be common in manual operations where focus and performance might fluctuate.
On the ease of use front, auto feed systems may require a more significant initial setup and adjustment to function correctly, but once operational, they are straightforward to use and can often be managed with simple controls or even a computer interface. In contrast, manual feed systems are inherently straightforward in concept, as they require human judgment and action, but this simplicity comes at the cost of ongoing physical labor and the potential for human error.
Overall, auto feed systems tend to be more efficient and easier on the user than manual feed systems, especially in long-term application scenarios. However, the choice between an auto feed and a manual feed system may depend on various factors, including the scale of operations, the type of materials being processed, and the desired levels of productivity and worker safety.
Accuracy and consistency in processing materials
Accuracy and consistency are critical factors in the processing of materials, and they often help to determine the quality of the final product. These factors become even more significant when considering the differences between auto feed and manual feed systems.
Auto feed systems are typically designed to be highly precise. They utilize advanced sensors, software, and mechanical components to ensure that materials are fed into a machine or process at consistent intervals, with consistent force, and in precise quantities. This level of control can greatly enhance the accuracy of the operation, reducing the variability that is commonly associated with human error.
For instance, in manufacturing contexts where materials need to be cut, shaped, or assembled, auto feed systems can maintain a level of consistency that is difficult to achieve manually. The repeatability of the system ensures that each part is processed in exactly the same way, leading to uniform quality across all products. This is particularly valuable in high-volume production settings, where even small inconsistencies can add up to significant product defects or rework requirements.
In contrast, manual feed systems depend heavily on the skill and attention of the operator. While an experienced operator can achieve a high level of accuracy, fatigue, distractions, or even slight variations in technique can introduce inconsistencies. Manual processes are also typically slower since they depend on human speed and reaction time, which can fluctuate throughout the day or be impacted by various factors such as operator health or morale.
From an efficiency standpoint, auto feed systems often surpass manual feeds because they can operate continuously at a set speed, without breaks, and with minimal supervision. This can lead to a higher throughput and reduced time spent on quality control and error correction. Additionally, because auto feed systems are less reliant on human intervention, they can often be used in conjunction with other automated systems to create a more streamlined and integrated workflow.
Ease of use, however, can vary. Auto feed systems can be more complex to set up and may require specialized training to operate effectively. Once configured, they tend to be user-friendly, often performing the majority of tasks with minimal human interaction. On the other hand, manual feed systems typically require more hands-on operation, which can be physically taxing and require more skill to maintain accuracy.
In conclusion, when it comes to accuracy and consistency, auto feed systems generally offer superior performance to manual feed systems. They help to minimize human error, ensure uniform product quality, and increase overall operational efficiency. Nevertheless, the best choice between an auto feed and a manual feed system can depend on several factors, including the specific application, available budget for machinery and training, and the desired volume of output.
Impact on productivity for various operational scales
The impact of auto feed versus manual feed on productivity can be significant, and this tends to be closely related to the operational scale of the task or project at hand. For smaller operations, the difference in productivity may not be as noticeable because the volume of material to be processed might not be sufficient to justify the investment in auto feed technology. Manual feeding in such scenarios can be quite efficient and cost-effective, as the incremental gains in productivity from an auto feed system would not offset the initial costs and ongoing maintenance expenses.
On the other hand, for larger operations, the productivity gains from an auto feeding system can be substantial. In high-volume scenarios, auto feed systems can dramatically enhance the speed and efficiency of the production process. These systems are designed to continuously and consistently feed materials into a machine without the need for operator intervention, reducing downtime between feedings. The constant supply of material ensures that machines operate at peak capacity, which can lead to a significant increase in output. This increase is often necessary for larger operations to meet higher demand and to benefit from economies of scale.
Auto feeders also tend to provide a more consistent and uninterrupted workflow compared to manual feed systems. In manual feeding, the human operator’s pace can vary, and fatigue or distraction can lead to stoppages or a slowdown in the workflow. This inconsistency can directly impact productivity, especially over long periods or during high-intensity work periods. For a large operation, these inconsistencies can result in a significant decrease in overall productivity.
In terms of efficiency and ease of use, auto feed systems excel because they minimize the manual labor required and can be programmed to operate with precision and autonomy. Operators can focus on monitoring the system and conducting quality checks, rather than carrying out repetitive and potentially straining manual feeding tasks. This can reduce physical strain on workers and lower the risk of injuries associated with repetitive motions or lifting heavy loads, which is an aspect of manual feeding that can negatively affect efficiency and productivity.
Overall, while each method of feeding has its place, the larger and more complex an operation becomes, the more beneficial an auto feed system tends to be in terms of productivity. Investments in such technology should, however, be weighed against the operational needs, scale, and long-term strategic goals of the business to determine the most advantageous approach.
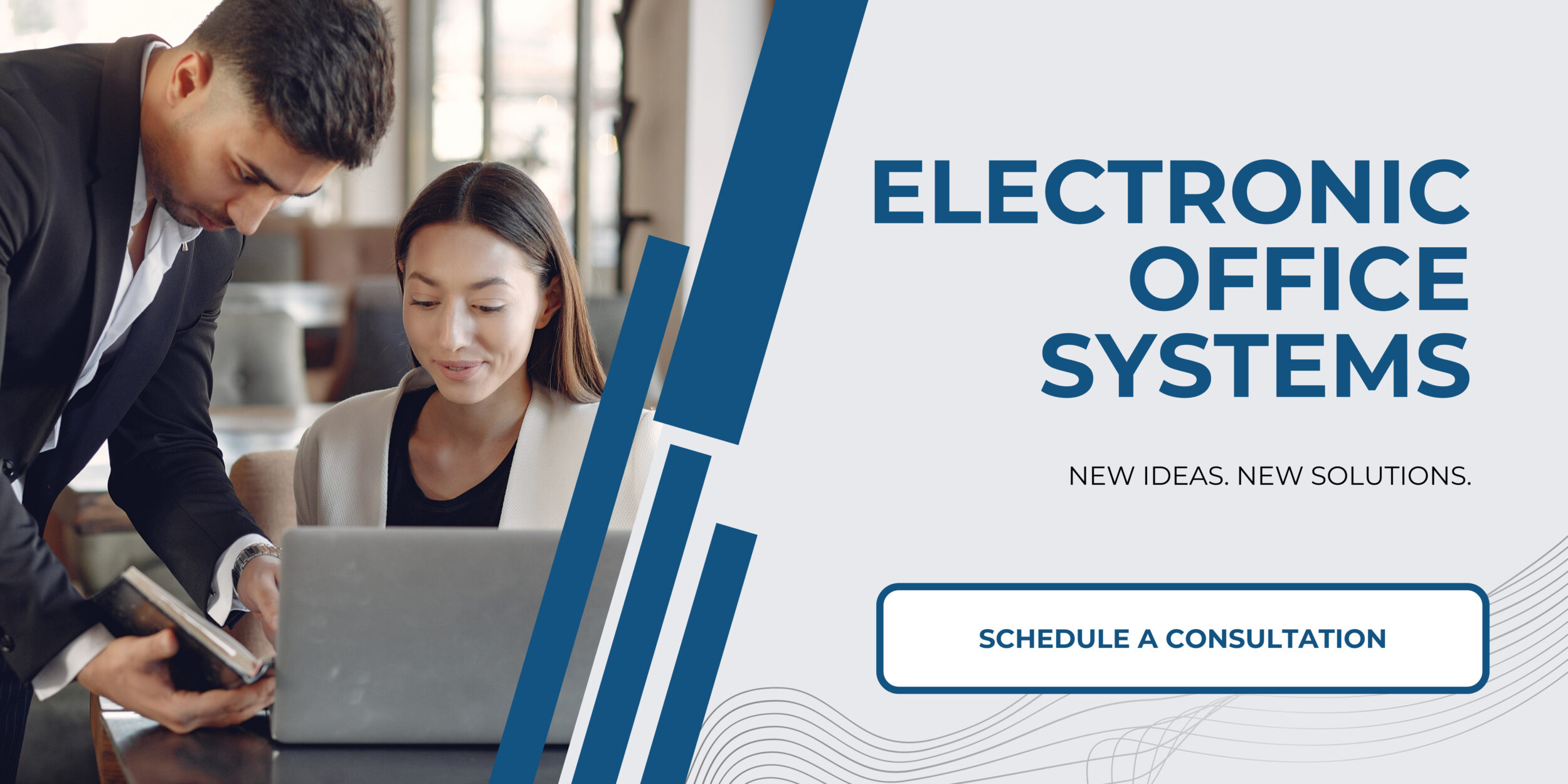
Maintenance and reliability concerns for auto feed vs. manual feed
When comparing maintenance and reliability concerns between auto feed and manual feed systems, several factors must be taken into account. Auto feed systems are often touted for their ability to streamline the feeding process, typically in industrial settings such as manufacturing or production lines. These systems are designed to automatically supply material to a machine or processing area, reducing the need for constant human intervention.
One of the primary considerations for an auto feed system is its complexity. Because these systems are often sophisticated, with numerous mechanical and electrical components, they can require a more rigorous maintenance schedule to ensure all parts are functioning correctly. Regular preventive maintenance is essential to avoid downtime and costly repairs. The automated nature of these systems usually indicates that when they do fail, they may require specialist attention, which can sometimes result in longer periods of inactivity if the required expertise is not immediately available.
On the other hand, manual feed systems tend to be simpler. With fewer moving parts and less dependence on automated mechanisms, there is often less that can go wrong. However, the simplicity comes with its trade-offs; increased physical labor and time are needed to manually feed materials into the system, which can lead to inconsistent feed rates and potentially lower productivity. Additionally, the manual aspect introduces human error and variability, factors absent in well-calibrated automated systems.
From an efficiency standpoint, automated systems usually outperform manual feeding methods due to their continuous and consistent operation. They are specially designed to feed materials at an optimal rate, ensuring a steady workflow. This efficiency often translates into increased production rates and can significantly impact the bottom line for larger-scale operations. However, when the auto feed systems fail, they can bring the entire production to a halt until repairs are made, which can be a critical concern.
Ease of use is markedly different between the two systems. While the initial learning curve may be steeper for workers to operate and troubleshoot automated systems, the reduced physical strain and the lessened need for constant manual intervention can make auto feed systems more user-friendly in the long run. Conversely, manual systems are generally straightforward to use from the outset but may become burdensome over time due to the repetitive and physical nature of the task.
In summary, auto feed systems can offer superior efficiency and ease of use, particularly in high-volume environments where their continuous operation can significantly improve production rates. However, they come with added complexity and potentially higher costs for maintenance and repair. Manual feed systems, with their simplicity, can offer a reliable alternative for smaller operations or where the expense of automation can’t be justified. Maintenance and reliability concerns must always be balanced against operational needs and resources available.