Title: The Impact of Warm-Up Time on Commercial Digital Laser Copiers and Multifunction Printers: Speed and Efficiency Explored
In the bustling hubs of modern business, commercial digital laser copiers and multifunction printers (MFPs) serve as pivotal tools that ensure the flow of information remains seamless and efficient. These sophisticated devices are designed to meet the high-speed demands of contemporary office environments, delivering crisp copies, prints, scans, and sometimes faxes, all from a single unit. However, one aspect that often goes overlooked, yet significantly influences the performance of these office workhorses, is warm-up time. The warm-up phase is a necessary process that brings the printer’s various components up to the appropriate operating conditions, impacting both the speed and efficiency of printing tasks.
Understanding how warm-up time affects a commercial digital laser copier or MFP is crucial for businesses aiming to maximize workflow and minimize downtime. Warm-up time can vary significantly between models and manufacturers, and can drastically change the device’s readiness and responsiveness. A printer that boasts a shorter warm-up period quickly reaches its optimal operating temperature and can start producing documents sooner, which is especially beneficial in high-paced office settings where the demand for instant printing is paramount.
Moreover, the intricacies of how warm-up time interacts with the printer’s speed and efficiency encompass not only the initial time taken for the machine to start up from an off or standby state but also how swiftly it resumes full functionality after periods of inactivity. Prolonged warm-up durations can lead to increased waiting times for employees, potentially slowing down workflows and reducing overall office productivity. Conversely, a printer with a faster warm-up capability can contribute to a more streamlined office environment where document processing is almost continuous.
In addition to the implications on speed and immediate task handling, there’s also an underlying relationship between warm-up time and a printer’s energy consumption and cost-efficiency. Devices that take longer to warm up tend to consume more power, leading to higher electricity bills and a larger carbon footprint—considerations that are increasingly important in today’s energy-conscious world.
In the following sections, we will delve deeply into the technicalities of warm-up time, examining the factors that influence it and exploring strategies that can minimize its effects. We will provide insights into the latest technological advancements that manufacturers are implementing to reduce warm-up time, ultimately enhancing the overall functionality and desirability of their laser copiers and multifunction printers. Whether you’re a business owner, office manager, or tech enthusiast, understanding the nexus between warm-up time, speed, and efficiency is key to making informed decisions about your printing solutions.
Impact of Warm-Up Time on Initial Print Speed
The impact of warm-up time on the initial print speed of a commercial digital laser copier & multifunction printer (MFP) is a significant aspect of its overall performance and efficiency. The warm-up time refers to the period required for the printer to reach its operational temperature from a cold start or standby mode. This period can vary between machines, with some requiring just a few seconds and others needing several minutes to warm up completely.
The warm-up process is necessary for laser printers because it brings the fuser assembly, the component that fuses toner onto the paper using heat and pressure, up to its correct operating temperature. Until the fuser reaches this temperature, the toner cannot be properly bonded to the paper, and as a result, the printer is unable to produce clear and accurate prints.
A printer with a shorter warm-up time can begin printing faster, which means the first page out time (FPOT) is reduced. This is particularly important for environments where printers are frequently turned on and off or woken up from sleep mode to handle sporadic printing tasks. In such settings, a longer warm-up time would lead to delays and a decrease in productivity as users wait for the machine to be ready. Additionally, in a busy office setting, these delays can accumulate, leading to a significant impact on the workflow and efficiency.
Moreover, the speed and efficiency of a commercial digital laser copier & MFP are not only affected by the time it takes for the initial print. They are also influenced by how quickly the machine can handle consecutive printing tasks. If the copier enters a standby mode between tasks to save energy, a shorter warm-up time means it can resume printing sooner, which enhances overall operational throughput.
In summary, warm-up time is a crucial factor in determining the usability and responsiveness of a commercial digital laser copier & MFP. The efficiency of the warm-up process can greatly influence the initial print speed, overall productivity, and the machine’s ability to handle a steady stream of print jobs without excessive wait times for users. Manufacturers often strive to reduce warm-up times in newer models to enhance the user experience and meet the demands of fast-paced work environments.
Warm-Up Time and Overall Operational Efficiency
Warm-up time is a crucial factor affecting the overall operational efficiency of commercial digital laser copiers and multifunction printers (MFPs). Operational efficiency in this context refers to how effectively and quickly a printer can complete a printing task from the very moment a print job is initiated. The warm-up time plays an integral role in determining how soon after being powered on or waking from a sleep mode the device can be ready to perform its first print or copy.
Commercial devices vary greatly in their warm-up times due to different technologies, designs, and energy-saving features. A shorter warm-up time means less waiting for the first printout, which can contribute to faster workflow and increased productivity, especially in office environments where printing demands can be frequent and immediate.
The warm-up process typically involves bringing various components of the printer, such as the fuser unit, to the required operating temperatures to ensure quality prints. The speed and efficiency at which this process is completed can influence the overall efficiency in several ways:
1. Time Savings: Printers with shorter warm-up times are ready sooner, allowing for quicker commencement of print jobs. This time saved can compound, especially if numerous print jobs are queued throughout a workday, leading to a more streamlined operation.
2. User Satisfaction: When users experience minimal delays, the perception of the device’s efficiency and reliability improves. In environments where multiple users access the printer, this can lead to higher satisfaction and reduced frustration relating to waiting times.
3. Power Management: Printers with longer warm-up times may lead to power inefficiencies, as they must maintain higher temperatures for extended periods if left on, or repeatedly undergo the warm-up cycle if they frequently enter and exit energy-saving modes.
4. Throughput: Warm-up time is often not considered as part of the print speed specifications. However, it directly impacts the time to complete the first page, which is essential in determining how quickly an entire job can be finished, particularly for short, time-sensitive print tasks.
To counteract the negative effects of long warm-up times, some manufacturers have developed technologies that allow for a quick start-up, using advanced fuser technology that can reach operational temperatures more rapidly. Others have improved their energy-saving modes to maintain a ready state with minimal power usage, balancing efficiency and energy conservation.
In summary, warm-up time significantly impacts a commercial digital laser copier and MFP’s speed and efficiency by determining how quickly it can respond to a print command following a period of inactivity. With a faster warm-up, the device can maximize its operational efficiency, thereby providing better service to the users and contributing positively to business productivity.
Relationship Between Warm-Up Time and Energy Consumption
The relationship between warm-up time and energy consumption in commercial digital laser copiers and multifunction printers is a significant aspect that affects both operational costs and environmental sustainability. Generally, warm-up time refers to the period required for a printer to reach the optimal operating temperature from a non-operational state. The importance of this phase cannot be understated, as the components within a printer, particularly fuser units, need to be at a specific temperature to properly bond toner to the paper.
Regarding energy consumption, when a device has a lengthy warm-up time, it consumes more power to reach the necessary operational temperature. The energy consumed during this time can contribute substantially to overhead costs in office environments where printers are frequently turned off and on or where they transition in and out of power-saving modes. Thus, manufacturers have been working on technologies to reduce warm-up times, promoting faster availability for printing tasks while also reducing the idle energy expenditure.
Modern laser printers and multifunction devices employ different strategies to minimize warm-up time, such as using fuser designs that heat up more quickly, or maintaining a lower base temperature in standby, which reduces the required heat-up time when a print job is initiated. These improvements help devices to become operational more rapidly, reducing the wait time before the first page prints and cutting down on the overall energy use per task.
Moreover, devices with shorter warm-up periods tend to be more energy-efficient during intermittent use. This is because the energy used to maintain standby temperatures is typically less than that required for a complete warm-up cycle from a cold state. As a consequence, devices are better able to balance readiness with energy savings.
Lastly, energy consumption relative to warm-up times is not only financially impactful but also pertinent to the environmental footprint of office operations. Devices with lower energy requirements during warm-up contribute to lower CO2 emissions, especially when drawing power from non-renewable energy sources. This dimension is increasingly critical for companies aiming to improve their sustainability and environmental stewardship. Consequently, warm-up time is a valuable factor to consider when evaluating the efficiency and ecological implications of a commercial digital laser copier or multifunction printer.
The Effect of Warm-Up Time on Component Lifespan
Warm-up time is an important factor that significantly impacts the lifespan of components within a commercial digital laser copier and multifunction printer (MFP). Generally, warm-up time refers to the duration a printer takes from being turned on, or waking up from a power-saving mode, to when it is ready to start the first print job. This period allows the printer’s internal components, especially the fuser unit that bonds the toner onto the paper, to reach the requisite operating temperatures.
Extended warm-up times can cause more wear and tear on components. This is because components such as the fuser assembly and other internal heating elements frequently undergo thermal expansion and contraction as they heat up and cool down. If a printer has a lengthy warm-up time, it may spend more time in a state of thermal cycling, thereby increasing stress on these components. Over time, this can lead to a need for more frequent maintenance and potential earlier failure of parts, thus affecting overall component lifespan.
In terms of the speed and efficiency of these devices, warm-up times can be a bottleneck for productivity, especially in commercial environments. If an MFP or laser copier requires a significant amount of time to warm up, this delay before the first page is printed can lead to a slowdown in workflow, particularly in situations where multiple small print jobs are common.
For a commercial digital laser copier or MFP, continuous operation or being kept in a ready state can minimize warm-up times; however, this method can significantly increase energy consumption, contributing to higher operating costs, and potentially adding ambient heat to the workspace. Therefore, manufacturers have been working on technologies that strike a balance, reducing warm-up times to boost component efficiency without excessively increasing energy consumption or thermal strain on components.
Modern printers often come with improved insulation for heating elements and software that intelligently schedules maintenance cycles to occur less frequently or during off-peak hours, limiting the effects on productivity. Additionally, new materials and design innovations can mitigate the impact of thermal stress and allow components to achieve their operating temperature more rapidly and maintain it more consistently.
In conclusion, warm-up times are an essential consideration for maximizing the functionality, efficiency, and lifespan of commercial digital laser copiers and multifunction printers. A quicker warm-up time can improve workflow and productivity, reduce the risk of wear and tear on components, and preserve the longevity of the device. As a result, these considerations are taken into account when designing and selecting a copier or MFP for a commercial setting.
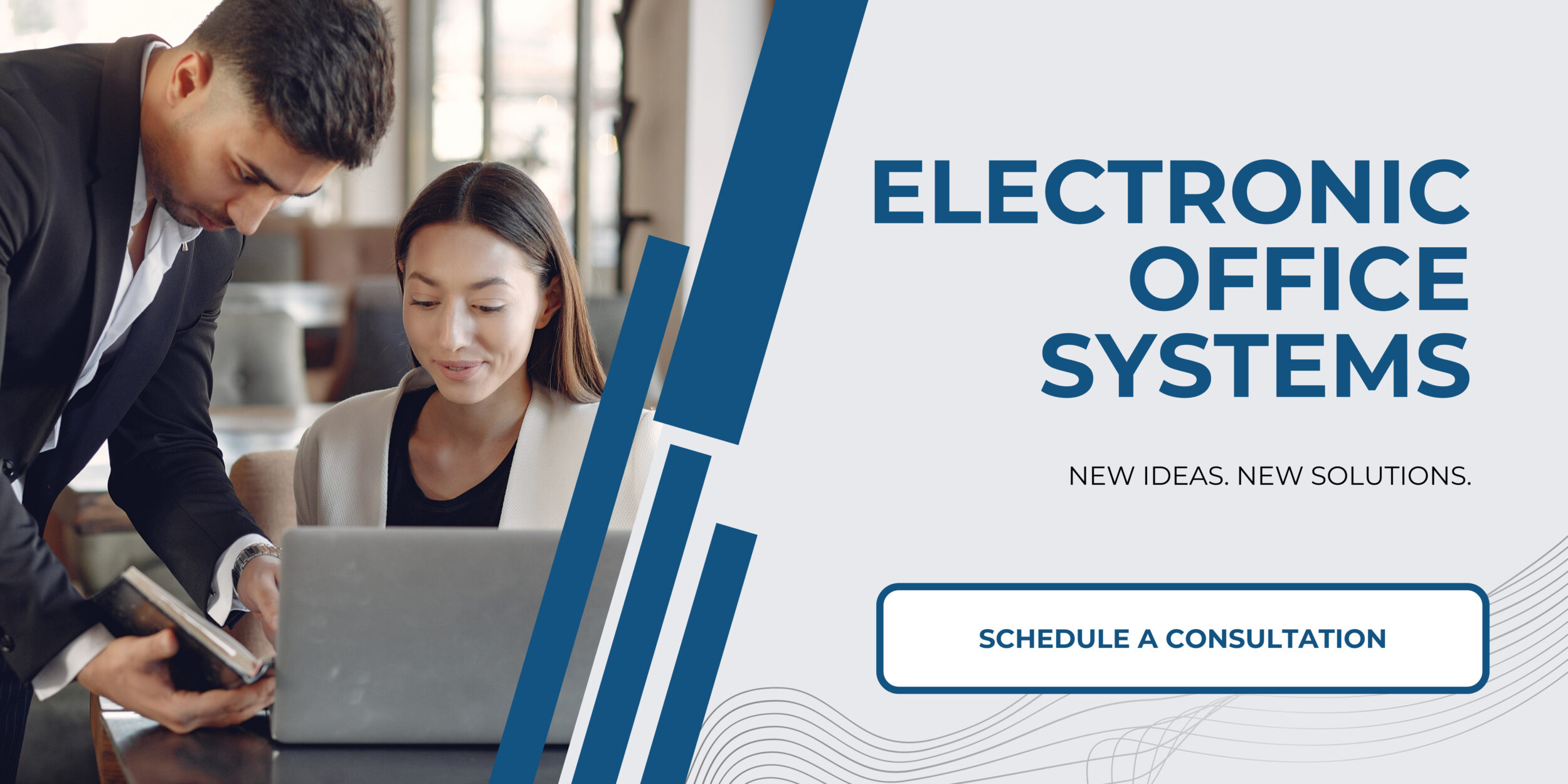
Warm-Up Times Across Different Brands and Technologies
Warm-up times for commercial digital laser copiers and multifunction printers (MFPs) can vary significantly across different brands and technologies. This variation is often due to the unique design and technology used in the heating elements of each brand’s fusing unit, which is one of the main components that require warming up.
The fusing unit in a laser printer applies heat and pressure to bond toner powder onto paper. The difference in warm-up times between technologies can often be attributed to the type of fuser being used. There are two main types of fusing technologies typically used in modern printers: conventional hot roller fusers and instant-on fusers.
Conventional hot roller fusers have a heated roller that must come up to a preset temperature before printing can start. This process can take some time, with warm-up times ranging from a few seconds to several minutes, depending on the printer model and ambient temperature conditions. Brands or models that utilize this type of fuser are more likely to experience longer warm-up times.
On the other hand, instant-on fusers, named for their ability to heat up more quickly, use a thin film or a ceramic element that can reach operating temperature much more rapidly. Printers equipped with such fuser technology tend to have shorter warm-up times, allowing them to begin printing after a few seconds of being powered on or woken from a sleep mode.
The difference in warm-up times can greatly influence the speed and efficiency of a commercial digital laser printer or MFP. A shorter warm-up time means a faster first page out time (FPOT), which is critical during high-demand use cases. When a copier or an MFP has a longer warm-up time, the initial job start can be delayed, possibly leading to a bottleneck in print production, especially in environments with high printing demands.
Printers and MFPs from different brands and technologies that are designed with energy-saving features may also affect warm-up times. Some devices are equipped with sleep modes to conserve energy when not in use. However, when they are brought out of sleep mode, they may require a warm-up period that could impact overall productivity.
In addition, the speed and efficiency of devices during their warm-up phase can be influenced by advancements in technology. As manufacturers continue to innovate, newer models are featuring enhanced warm-up routines that aim to reduce wait times drastically, thus improving operational efficiency and productivity.
Overall, the warm-up time of a commercial digital laser copier or MFP is an essential factor that can affect the speed and efficiency of office workflows. When considering the purchase of a new machine, it is important for buyers to review the warm-up time specifications and balance them with the needs of their workplace. Selecting a device with the ideal warm-up characteristics could result in improved productivity and reduced disruption in printing tasks.