Title: Understanding the Cool-Down Time of a Paper Shredder: Contributing Factors and Mechanisms
In the modern office environment, paper shredders serve as a crucial line of defense against information breaches, ensuring sensitive documents are securely destroyed to safeguard personal and corporate data. However, like any piece of machinery, paper shredders have operational limits that dictate how long they can run before needing a period of inactivity to cool down. The cool-down time of a paper shredder is a vital concern for businesses that require frequent shredding services to maintain productivity and extend the lifespan of their shredding equipment. This cool-down period is influenced by a myriad of factors, from the technical specifications of the shredder itself to the usage habits in the office. Understanding these factors can help users optimize shredder performance while preventing overheating, which could lead to machine failure or even pose safety risks.
To dissect the cool-down time for paper shredders, one must consider the shredder’s design, such as the motor’s power, the cutting mechanism, and its duty cycle. The motor type plays a critical role; shredders with heavy-duty motors designed for longer running times will have different cool-down requirements compared to those with less powerful motors suitable for lighter tasks. Furthermore, the type of cutting mechanism—be it strip-cut, cross-cut, or micro-cut—can also impact the amount of heat generated during shredding. Additionally, user practices, such as the volume of paper fed into the shredder, the type of material being shredded, and adherence to recommended usage patterns, significantly affect how quickly a shredder reaches its maximum operating temperature and, subsequently, how long it must rest before it can safely resume operation.
In this comprehensive exploration, we will delve into the complexities surrounding the cool-down time of the paper shredder. We’ll examine the engineering principles that underpin shredder design, the user behaviors that influence shredder performance, and the environmental conditions that affect heat dissipation. Our goal is to provide a clear understanding of why paper shredders require a cool-down period and the variables that determine the length of this downtime, ultimately offering guidance for maximizing the efficiency and longevity of your paper shredding equipment.
Motor Power and Thermal Protection
Motor power and thermal protection are crucial factors that determine the performance and longevity of a paper shredder. The motor is the heart of a paper shredder; it converts electrical energy into mechanical energy, which drives the cutting blades that shred the paper. The power of the motor is typically measured in horsepower (HP) or watts (W), and it dictates the shredder’s capability to handle loads. A more powerful motor can shred thicker stacks of paper, handle tougher materials, and generally endure longer shredding tasks without overheating.
Thermal protection plays a vital role in managing the heat generated during the shredding process. Shredders come with built-in thermal sensors that monitor the temperature of the motor. When the shredding process generates excessive heat, these sensors trigger a thermal protection mechanism that shuts off the motor to prevent damage. This safety feature is essential because it prolongs the life of the shredder and prevents potential fire hazards.
The cool down time of a paper shredder, which is the period that the shredder must rest to allow the motor to cool down after a continuous run, is affected by several factors:
1. **Motor Power**: A shredder with a high-powered motor will generally have a shorter cool down time compared to one with a less powerful motor because the former can handle more intensive work without reaching critical heat levels.
2. **Thermal Protection**: The sensitivity and quality of the thermal protection technology influence how soon and how often the shredder will require a cool down period. Advanced thermal protection systems can manage heat more effectively, reducing the need for frequent breaks.
3. **Shredding Capacity and Continuous Run Time**: Shredders designed for heavy-duty use or with a longer continuous run time have mechanisms in place to handle heat buildup and could therefore have shorter cool down periods. However, consistently pushing a shredder to its max capacity can lead to longer cool down requirements to ensure the motor doesn’t overheat.
4. **Type and Thickness of Material Shredded**: The tougher the material or the thicker the stack of papers being shredded, the more strain is placed on the motor, resulting in more heat generated and potentially longer cool down times.
5. **Ambient Operating Temperature**: The environment where the shredder operates also affects the cool down time. A warmer room will contribute to the motor retaining heat for longer periods, whereas a cooler environment aids in dissipating heat faster.
6. **Maintenance and Lubrication Practices**: Properly maintained and regularly lubricated shredders will generally experience smoother operation and less friction. Reduced friction leads to less heat generation and, consequently, shorter cool down times.
Understanding and managing these factors are key to ensuring the shredder operates efficiently and enjoys a long service life. Regular maintenance and careful operation according to the manufacturer’s guidelines can help minimize the need for cool down periods and maintain optimal shredder performance.
Shredding Capacity and Continuous Run Time
Shredding capacity and continuous run time are two crucial factors to consider for the performance and endurance of a paper shredder. Shredding capacity refers to the maximum number of sheets of paper that a shredder can process simultaneously without jamming or overloading the system. A higher shredding capacity usually implies that a shredder is designed for more intensive use and can handle larger volumes of paper at once, enhancing productivity in environments with heavy shredding requirements.
Continuous run time, on the other hand, denotes the duration a paper shredder is designed to operate without needing a cool-down period to prevent overheating. This can vary significantly among different shredder models. For example, some shredders may only operate for a few minutes at a time, while others can run continuously for an hour or more before needing a break. The continuous run time is often dictated by the shredder’s motor capabilities, cooling systems, and overall build quality.
The factors that determine the cool-down time of a paper shredder include:
1. **Motor Power and Thermal Protection**: A more powerful motor might generate more heat but also typically come fortified with better thermal protection and cooling mechanisms. Shredders with this feature can run for longer periods before requiring a cool-down period.
2. **Shredding Capacity and Continuous Run Time**: Shredders designed for high shredding capacities and with long continuous run times have components that can handle higher temperatures and have designed heat dissipation strategies to cope with the produced heat.
3. **Type and Thickness of Material Shredded**: The tougher the material or the thicker the bunch of papers, the more the motor has to work and the more heat it generates. Consequently, shredders used for more robust materials may need longer cool down periods.
4. **Ambient Operating Temperature**: The environment in which a shredder operates also influences its cool down time. A machine operating in a hot environment will take longer to cool down compared to one in a cooler setting.
5. **Maintenance and Lubrication Practices**: Regular maintenance and proper lubrication can extend the continuous run time of a shredder and reduce cool down periods. An inadequately maintained or lubricated shredder may overheat more quickly and thus have a longer cool-down period.
Considering these factors can help in choosing the correct shredder for your needs, or optimizing the performance and lifespan of your existing machine by ensuring adequate cool down periods and maintenance practices.
Type and Thickness of Material Shredded
The type and thickness of the material being shredded are critical factors that influence the cool down time of a paper shredder. Different shredders are designed to handle varying materials, from standard office paper to credit cards and compact discs. The thicker and more robust the material, the more strain is put on the shredder’s motor and blades, resulting in more heat generation. For instance, shredding a few sheets of thin printer paper will generate less heat compared to shredding the same number of thick cardboard sheets or multiple folded documents.
The cool down time of a paper shredder largely depends on its thermal protection system. When the shredder handles materials that are thicker or harder to cut, the motor works harder and heats up faster. This intense operation could trigger the thermal protection feature sooner, necessitating a longer cool down period to prevent overheating and potential damage to the shredder. Conversely, a shredder fed with materials within its comfortable processing range will generate less heat, reducing the need for frequent or lengthy cool down periods.
In addition to type and thickness, the material’s composition can also affect the amount of heat generated. For example, paper with adhesive labels or laminated documents may create more friction and heat compared to plain paper. Materials that are outside the recommended specifications for a shredder can not only increase the cool down time but also risk damaging the shredding blades or clogging the machine, leading to maintenance issues which can impact long-term performance and durability.
Proper understanding and adherence to the shredder manufacturer’s guidelines on acceptable materials for shredding are therefore essential. Users should also be aware that the rated thickness (like the number of sheets a shredder can handle at once) is typically based on a standard weight of paper, and adjusting the load to account for thicker or sturdier materials can help manage heat generation and optimize cool down times.
Ambient Operating Temperature
The ambient operating temperature refers to the surrounding environmental temperature within which a paper shredder is utilized. This factor significantly influences the cool down time of paper shredders since these devices are affected by the external temperature conditions.
The cool down time of a paper shredder is determined by how long it takes for the machine to return to a safe operating temperature after a period of use. The duration of the cooling process is crucial for the prevention of overheating, which can cause damage to internal components and potentially lead to a malfunction or reduce the lifespan of the shredder.
Several key factors affect the cool down time of a paper shredder, one of which is the ambient operating temperature:
1. **Motor Power and Thermal Protection:** High-powered motors can generate more heat, but they might also be equipped with better thermal protection that efficiently manages heat buildup. Thermal protection, such as automatic shut-offs or thermal overload switches, halts the shredding process if the machine reaches a certain temperature, helping to ensure it cools down properly.
2. **Shredding Capacity and Continuous Run Time:** A shredder that can handle more sheets of paper at once or can run continuously for a longer period will produce more heat. It may need a longer cool down period before it can safely operate again.
3. **Type and Thickness of Material Shredded:** Thicker materials or credit cards can cause more strain on the shredder’s motor, increasing the temperature. Consequently, the cool down will be extended when shredding these tougher materials frequently.
4. **Ambient Operating Temperature:** When a paper shredder is used in a warmer environment, it has a higher starting temperature, thus potentially reaching critical heat levels quicker than when used in a cooler environment. The cool down time is elongated in warm conditions due to the lesser efficiency in dissipating heat back into the already warm surroundings.
5. **Maintenance and Lubrication Practices:** Proper maintenance and regular lubrication ensure the smooth operation of the shredder’s cutting blades. This reduces the friction heating of components. A well-maintained shredder can cool down more rapidly because less heat is generated during operation compared to a poorly maintained machine.
Ensuring that your paper shredder is placed in a favorable environment where the ambient temperature is not excessively high can aid in maintaining an optimal operating condition. This reduces the risk of overheating and thus preserves the functionality and longevity of the shredder. By paying attention to the ambient operating temperature and other factors, users can ensure more efficient cooling periods and safe operation for their shredding equipment.
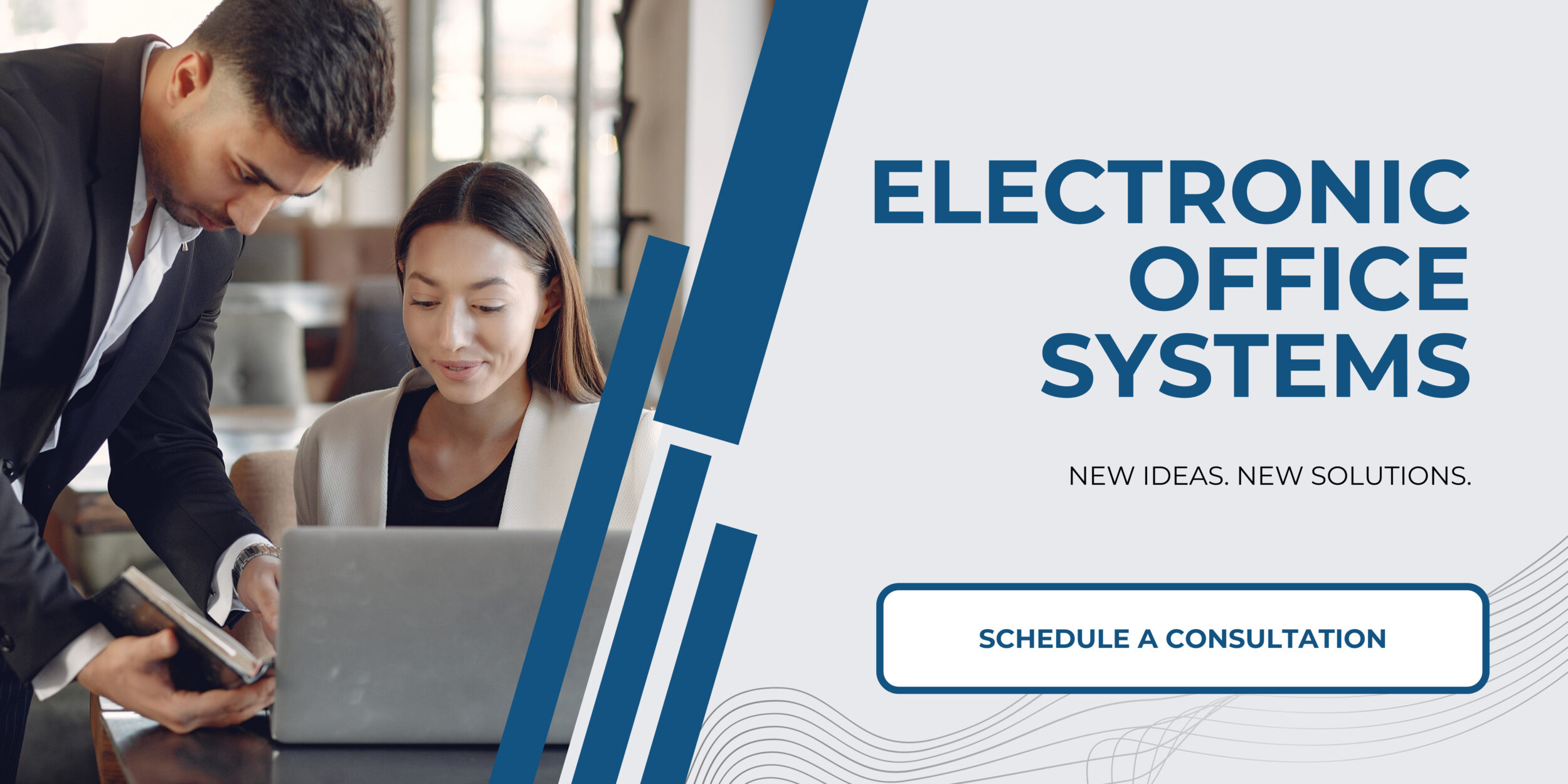
Maintenance and Lubrication Practices
Maintenance and Lubrication Practices are vital for the optimal operation and longevity of a paper shredder. Regular maintenance ensures that the shredder functions smoothly, safely, and effectively. Lubrication, in particular, plays a key role in the performance and durability of the shredding blades.
For any mechanical device, friction is a constant concern as it leads to wear and tear. Paper shredders are no different; the cutting blades used to slice through paper generate friction each time the machine is used. Over time, the blades can become dull if not properly maintained, which can lead to more strain on the motor, reduced efficiency, increased noise, and the potential for paper jams.
Proper lubrication mitigates the adverse effects of friction. Most shredder manufacturers will recommend a specific type of lubricant, often in the form of oil or specialized sheets that are shredded like paper. This oil helps to keep the blades sharp and reduces the amount of heat produced by the cutting action. Applying lubricant to a paper shredder usually involves pouring the oil across a sheet of paper in an ‘S’ pattern or directly into the feed entry in modest amounts, depending on the design of the shredder and the manufacturer’s guidance.
It is also important to consider the cleanliness of the blades and mechanisms. Dust and small paper remnants can build up within the shredder, increasing the risk of jamming and overheating. Regular cleaning can prevent such build-up. High-security shredders, which produce very fine particles, can be especially prone to such problems without regular maintenance.
The cool down time of a paper shredder – the interval required for the shredder to rest and cool off after a period of operation – is affected by several factors:
1. **Motor Power and Thermal Protection**: Shredders with more powerful motors and better thermal protection can run for longer periods before needing to cool down.
2. **Shredding Capacity and Continuous Run Time**: Machines designed for higher volumes of shredding will generally have longer continuous run times and shorter cool down periods.
3. **Type and Thickness of Material Shredded**: Thicker materials and non-paper items increase the stress on the shredder’s motor, potentially calling for longer cool down times.
4. **Ambient Operating Temperature**: A warmer operating environment can cause the shredder to overheat more quickly, shortening the continuous run time.
5. **Maintenance and Lubrication Practices**: Proper maintenance, as mentioned above, includes keeping the blades lubricated, which helps keep the machine cool during operation. A well-maintained shredder will usually have a more efficient cooling cycle and thus, shorter cool down times.
In summary, regular and correct lubrication in conjunction with overall maintenance practices plays a significant role in the cooling cycle of a paper shredder. Properly cared for, a shredder will have peak performance with minimal downtime, while neglect can lead to longer cool down periods and a shorter life span for the machine.