Title: Unveiling the Heart of Copying: The Role and Mechanics of the Fuser Unit in Copiers
In the intricate ecosystem of a copier, the fuser unit stands as a pivotal component, yet it often operates unnoticed amidst the symphonic whir of gears and rollers. This unsung hero is responsible for one of the final and most crucial stages in the photocopying process—the fusing of toner onto paper. Understanding how a fuser unit works not only demystifies the inner workings of copiers but also highlights the sophisticated blend of physics and engineering that allows for the reproduction of documents with precision and durability.
Fundamentally, a fuser unit is tasked with a transformative process: it must take the loose powder known as toner and turn it into a permanent, smudge-resistant image affixed to paper. It does this through a carefully calibrated combination of heat and pressure. The role of the fuser unit becomes apparent at the end of the copying cycle, after the toner has been electrostatically attracted to the correct areas on the paper to recreate the desired image or text.
This intricate dance begins with the two main components of the fuser: the heated roller (or fuser roll) and the pressure roller. Together, they create an environment where controlled heat melts the toner particles without damaging the underlying paper, while simultaneous pressure ensures that the now-viscous toner firmly adheres to the paper fibers. The engineering behind the fuser unit is a marvel of thermal management, as it must consistently reach the right temperature—usually between 180 and 200 degrees Celsius (356 to 392 degrees Fahrenheit)—to achieve optimal adhesion without risking a fire hazard or paper degradation.
In addition to its primary function, the fuser unit has evolved to incorporate various features that enhance its efficiency and longevity, such as energy-saving modes and user-replaceable components. Its performance is also a crucial determinant in print quality, affecting both the sharpness of the final output and the longevity of the document. As we delve further into the operational intricacies and the importance of the fuser unit in copiers, we gain a deeper appreciation for the delicate balance of forces that must be maintained and the technological advancements that continue to push the boundaries of document reproduction. This article will take you on a journey through the scorching corridors of the fuser unit, where the alchemy of heat, pressure, and precision brings the static world of toner to life on the page.
Heat Generation and Transfer
Heat generation and transfer is an integral part of the printing process within a laser printer or copier. The fuser unit, which is the component responsible for this task, plays an essential role in creating permanent images or text on paper. The way this works is both fascinating and elegant.
A fuser unit functions through a process of heating and pressurizing the toner—the powdered ink used in laser printers—to create a durable bond between the toner particles and the fibers of the paper. The heat is crucial because the toner used in laser printers is made of plastic, which needs to melt slightly to adhere firmly to the paper’s surface.
The fuser unit itself typically consists of two rollers: the heat roller (or fuser roller) and the pressure roller. As the paper passes between these rollers, the heat roller applies the necessary temperature to soften the toner. It’s designed to reach, and maintain, a specific temperature threshold that is optimal for the toner to melt without damaging the paper.
Inside the heat roller, there’s often a halogen lamp, a quartz tube filled with halogen gas that emits infrared radiation when electricity passes through it. This infrared radiation heats the roller’s surface. Alternatively, some fuser units may use a ceramic heating element that coats the heat roller to provide an even, consistent heat.
The transfer of this heat is critical. It must be applied evenly and at the precise moment when the toner is in contact with the paper. If the heat is too low, the toner won’t fuse properly, leading to smudging. If it’s too high, it could cause the paper to burn or the toner to degrade.
To ensure that heat generation and transfer happen efficiently, fuser units are designed with temperature control mechanisms, such as thermostats and thermistors. These components constantly monitor and adjust the temperature to the correct levels. The ‘warm-up’ period, which refers to the time taken for the fuser to reach the necessary temperature from being switched on, is crucial for the first print of the day or if the printer has been in standby mode. Once warmed up, however, modern fuser units can maintain their temperature with minimal energy expenditure, ready to fuse the toner onto any page that is sent through the printer.
In this way, the heat generation and transfer step provided by the fuser unit is vital not just for the immediacy of print jobs but for the long-term permanence and professionalism of the documents laser printers produce. Without such a mechanism, the crisp, smudge-free finish that we expect from modern laser printers and copiers simply wouldn’t be possible.
Pressure Application
In the context of copier machines, the Pressure Application refers to the stage in the printing process where the paper is pressed against the fuser’s heated rollers to permanently affix the toner to the paper. This step is crucial for ensuring that the print is durable and resistant to smudging or fading.
The fuser unit itself is an essential component of laser printers and copiers. It operates by using a combination of heat and pressure to fuse the toner powder onto the paper, creating a permanent bond. The unit typically consists of two main rollers: the fuser roller, or hot roller, and the pressure roller. The fuser roller is heated to the necessary temperature to melt the toner, while the pressure roller applies force against the fuser roller to press the toner into the paper fibers.
When a printed page reaches the fuser unit, the pressure roller pushes the paper against the heated fuser roller. As the paper passes through these rollers, the toner, which is initially a powder, melts due to the heat. Simultaneously, the pressure applied by the rollers ensures that the melted toner seeps into the fibers of the paper. This combination of heat and pressure is critical for creating a crisp, smudge-free image or text on the printed page.
The effectiveness of the pressure application can be affected by several factors, including the type and thickness of the paper, the quality of the toner, and the condition of the fuser unit. Most modern fuser units are designed to adjust to various paper types and printing demands to maintain optimal quality.
It’s important to note that the pressure must be precise. Too little pressure may result in poor toner adhesion, leading to prints that can easily smudge or fade. Conversely, too much pressure can cause the paper to wrinkle or damage the fuser rollers, leading to maintenance issues and reduced printer lifespan.
Overall, the Pressure Application is a fundamental step in achieving the final, high-quality printed document. It works in concert with the other listed components, including Heat Generation and Transfer, Toner Particle Melting and Bonding, Fuser Roller and Pressure Roller Mechanics, and is also a significant consideration in Fuser Unit Maintenance and Lifespan.
Toner Particle Melting and Bonding
The fuser unit in copiers is a critical component responsible for the final stage of the printing process, which involves toner particle melting and bonding. This stage is essential for transforming the toner from a powder form into a durable and permanent image or text on the paper. How does this part of the process work seamlessly within the complicated machinery of a copier?
To understand the role of a fuser unit, we must first consider the composition of the toner used in copiers. Toner is a fine powder that contains plastic particles which are specifically designed to melt under high temperatures. When a document is sent to the copier, the machine uses static electricity to arrange the negatively charged toner particles on the positively charged areas of a drum or belt within the copier. The image on the drum correlates to the document to be printed, and the toner adheres in the pattern of this image.
Once the toner has been applied to the paper, the sheet passes through the fuser unit. The fuser unit typically consists of two rollers: the hot roller (or fuser roller) and the pressure roller. The hot roller is heated by an internal lamp, and as the paper with the loosely attached toner particles passes between these two rollers, several things happen simultaneously.
Firstly, the heat from the fuser roller begins to melt the plastic components of the toner particles. The fuser must reach a specific temperature that is high enough to melt the toner but low enough to not scorch the paper – this balance is critical to the copier’s operation.
Secondly, the pressure applied by the pressure roller ensures that the melted toner is pressed into the paper fibers. This pressure must be substantial to ensure strong adhesion but must also be controlled so as not to damage the paper or the quality of the printed image.
During the toner particle melting and bonding process, the fuser unit works to create a permanent bond between the toner and the paper. As the heated toner particles are pressed into the paper, they cool down and solidify, resulting in a crisp and smudge-free image that won’t rub off the paper.
Proper maintenance and handling of the fuser unit are important because it directly affects the quality of the printed documents. Over time, the fuser unit can wear down and may require replacement to maintain the efficiency and quality of the printing process. The lifespan of a fuser unit varies depending on the model of the copier, usage patterns, and the quality of the maintenance performed on the machine.
In summary, the fuser unit is integral to the copier’s function, with the toner particle melting and bonding stage being crucial for producing final printed documents that are touchable and durable. Understanding the fuser unit’s operation helps in managing the copier effectively and ensuring consistent print quality.
Fuser Roller and Pressure Roller Mechanics
The fuser roller and pressure roller mechanics within a copier are integral components of the printing process. In a typical laser printer or copier, these rollers work harmoniously to form the final image on the paper.
The fuser unit, which contains the fuser roller (often called the “hot roller”) and the pressure roller (also known as the “backup roller” or “nip roller”), is responsible for permanently binding toner to paper. The mechanics of this system are critical for ensuring high-quality printouts.
The fuser roller is coated with a heat-resistant, non-stick material such as Teflon, which helps in preventing toner from sticking to the roller. Inside this roller is a halogen heating lamp or a similar heating element that enables it to reach the required temperature, often around 180 to 200 degrees Celsius (356 to 392 degrees Fahrenheit), although this can vary depending on the printer model and toner formulation.
Once the paper, with loosely adhered toner in the shape of the intended image, reaches the fuser unit, it passes between the fuser roller and the pressure roller. The fuser roller transfers heat to the toner particles, while the pressure roller applies force. This dual action causes the toner particles to melt and fuse into the paper fibers.
The pressure roller complements the fuser roller by providing a consistent pressure against the fuser roller as the paper makes its pass between them. This pressure ensures that every part of the toner receives equal heat and is pressed uniformly into the paper, which is important for achieving a smooth and even print.
The fuser unit’s design is crucial for its proper function. For example, there needs to be a precise balance in the temperature of the fuser roller to efficiently melt the toner without damaging the paper or causing it to jam. Similarly, the pressure roller must exert just enough pressure to fuse the toner to the paper without crushing it.
In modern copiers, the fuser unit is designed to warm up rapidly and maintain a consistent temperature to optimize energy usage and improve print speed. Some copiers also feature a “sleep mode,” wherein the fuser unit drops to a lower temperature when not in use, conserving energy and extending the life of the components.
Overall, fuser roller and pressure roller mechanics are fascinating examples of the synergy between thermal energy and mechanical pressure in creating lasting images on paper. The meticulous design and operation of fuser units within copiers ensure that the reproduced documents are crisp, professional and durable.
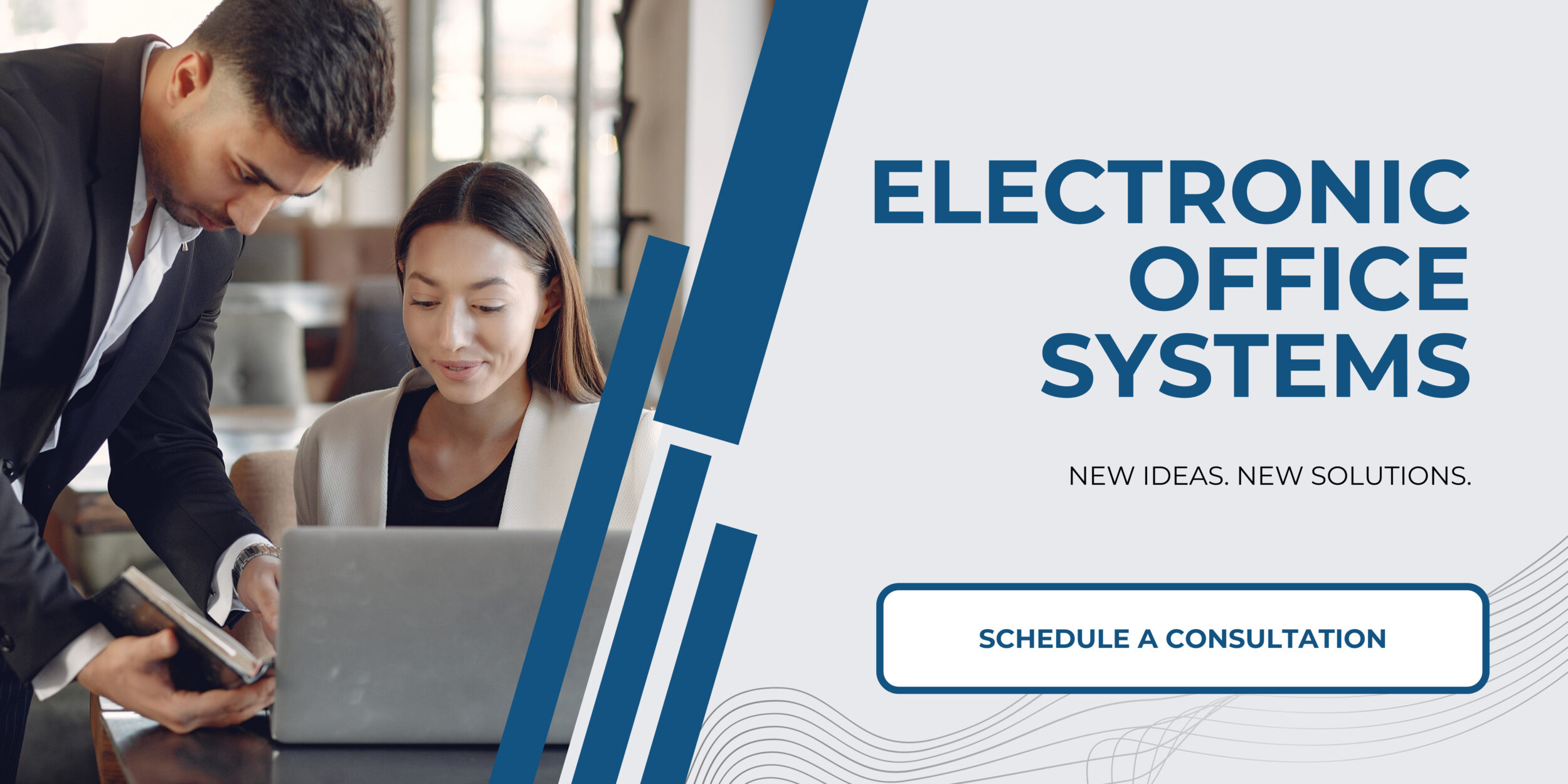
Fuser Unit Maintenance and Lifespan
Maintaining the fuser unit is crucial in ensuring the longevity and proper functioning of a copier. Over time, the fuser unit undergoes wear and tear due to the high temperatures and constant pressure it needs to exert during the printing process. A typical fuser unit can last anywhere from 50,000 to 200,000 pages, although this lifespan can vary drastically based on the model of the copier, the type of use it undergoes, and how well it is maintained.
Regular maintenance of the fuser unit includes cleaning, inspection, and occasionally replacing the fuser roller or films that come into direct contact with paper. Dirt, residual toner, and paper particles can accumulate on these components, leading to image defects, paper jams, or even reduced fuser life. Some copiers might alert users with a maintenance message when it’s time to check or replace the fuser unit—this helps ensure timely intervention before print quality diminishes or the unit fails.
To properly take care of a fuser unit, the user should follow the manufacturer’s recommendations for operating temperature and paper type. Using inappropriate print media or operating the copier in an environment that’s too hot or cold can put undue stress on the fuser unit, shortening its expected lifespan. Moreover, fusers are typically designed to be replaced after a certain amount of use, and many modern copiers have fuser units that are user-replaceable, simplifying the maintenance process.
In relation to how a fuser unit works in the context of copiers, the fuser unit’s main job is to bond the toner to the paper securely, creating a durable and smudge-resistant image or text. To do so, the fuser unit must reach a high enough temperature to melt the toner particles without damaging the paper. This is achieved through a precise balance of heat, pressure, and timing.
Inside the fuser unit, there are two main rollers: the heat roller (or fuser roller) and the pressure roller. The heat roller is heated internally, often by quartz tube lamps or ceramic heating elements. It works in conjunction with the pressure roller, which applies force to ensure the toner particles penetrate the paper fibers. As the paper passes through these rollers, the heat from the fuser roller melts the toner, and the pressure from the pressure roller helps it adhere firmly to the paper. After passing through the rollers, the paper is cooled quickly, allowing the toner to solidify in its final, fixed position on the paper. This results in a crisp, permanent print.