Title: Deciphering the Maintenance Imperatives for Shredders with Shorter Cool-Down Times
Introduction:
In the contemporary realm of high-paced professional environments, shredding equipment has emerged as a fundamental asset for safeguarding sensitive information and ensuring compliance with data protection laws. Among the myriad of features that modern shredders boast, the cool-down time has drawn significant attention. Shredders with shorter cool-down times tend to cater to the demands for efficiency and continuous operation within busy offices and industry settings. These advanced machines allow users to carry out extensive shredding tasks without the interruptions that often accompany thermal thresholds being exceeded.
However, short cool-down periods can also imply a greater concentration of wear and tear over a smaller time frame, necessitating a comprehensive understanding of maintenance considerations to prolong the operational life of the equipment. This article provides a deep dive into the maintenance strategies and practices that should be adopted for shredders with shorter cool-down times. We will explore the importance of timely cleaning, the selection of suitable lubricants, the management of shredder capacity, and the adherence to manufacturer guidelines. Moreover, we will delve into the critical role that user awareness and training play in preventing mishaps that could lead to unnecessary downtime or damage.
By giving due consideration to these maintenance aspects, businesses and individuals alike can ensure that their shredding apparatuses remain functional, reliable, and ready to perform at a moment’s notice. These considerations not only enhance the longevity of the shredders but also contribute to a seamless document destruction process that upholds both efficiency and security. Join us as we unravel the intricacies of maintaining shredders with shorter cool-down times and explore how such diligence can lead to a significant return on investment for any entity that relies on these crucial devices.
Understanding Cool Down Times and Overheating Risk
Understanding cool down times and overheating risk is crucial when it comes to operating mechanical shredders. These machines are designed to cut through materials—ranging from paper to more robust items such as credit cards or CDs—but the motor within generates heat through friction and mechanical work. Cool down time is the period that a shredder requires to rest so that its internal temperature can return to a safe operational level. Overheating arises when a shredder is used continuously beyond its rated capacity, leading to potential malfunction, reduced lifespan of the machine, or even fire hazards if left unattended.
The risk of overheating is a primary concern because shredders contain parts such as motors and cutting blades that can become excessively hot. Continuous operation without adequate rest can cause these components to fail, triggering a breakdown. Therefore, users should adhere to the maximum run time specified by the manufacturer and allow for cool down time as recommended. It varies among different models and is typically longer for basic, low-volume shredders, while commercial or heavy-duty shredders are engineered to withstand longer periods of usage.
Maintaining a shredder properly to cater to its cool down needs involves understanding the machine’s capabilities and handling it accordingly. For shredders with shorter cool down times, it’s essential not only to respect those rest periods but also to anticipate maintenance needs more frequently. The shorter the cool down time required, the more resilient the machine usually is to heat, but this does not mean it’s immune to the gradual wear and tear caused by heat stress.
A key maintenance consideration is the lubrication of the shredder’s cutting blades. Shorter cool down times often mean more intense usage is expected, and thus regular lubrication becomes imperative to ensure smooth operation. Usually, this involves applying the manufacturer-recommended oil across the entry width of the shredder, and then running the machine in reverse for a short period to spread the oil evenly.
Monitoring and replacing worn or damaged parts promptly is another critical practice. Users should pay attention to any unusual noises, vibrations, or a noticeable reduction in performance, as these may indicate that certain components are struggling due to insufficient cooling periods.
Lastly, environmental factors can also affect the overall efficiency of the cool down process. Shredders with shorter cool down times should be placed in well-ventilated areas to aid in the dispersion of heat. This also means avoiding cramped or enclosed spaces where hot air can become trapped around the machine, preventing it from cooling effectively.
In summary, while shredders with shorter cool down times offer convenience and higher workloads, they require diligent maintenance and mindful operation to maintain safety and extend the life of the machine.
Frequency of Lubrication and Types of Lubricants
The maintenance of a paper shredder is vital to ensure its longevity and optimal performance. Among the critical maintenance considerations, frequency of lubrication and the types of lubricants used are of significant importance. Lubrication is essential for shredders because it reduces friction between the cutting blades, which can help prevent the unit from overheating and keep it running smoothly. Generally, the more frequently a shredder is used, the more often it should be lubricated. For shredders that are used infrequently, lubricating the blades once a month may be sufficient. However, for shredders used daily, lubrication might be necessary after each use or at least weekly.
There are different types of lubricants available for paper shredders. The most common is shredder oil, which is specifically designed to be used with shredders and is available from most office supply stores or the manufacturer of your shredder. This specialized oil is formulated to be heat-resistant and maintain its viscosity when applied to the high-friction areas within the shredder. Some manufacturers also offer lubricant sheets, which are paper sheets treated with a precise amount of lubricant. These sheets can be run through the shredder to ensure an even distribution of the lubricant over the blades.
When considering maintenance for shredders with shorter cooldown times, it is essential to monitor the level of use closely. Shredders with shorter cooldown times may be designed for more intense usage, but they can still benefit from regular lubrication, as it ensures the shedding mechanism operates without unnecessary strain. These shredders might warm up at a faster rate due to their more frequent use, which makes lubrication even more critical to maintain the shredder’s health. Not adhering to proper lubrication schedules might lead to increased wear and tear on the blades, and potentially, the motor.
Furthermore, regular lubrication can help prevent paper jams, which are often the result of the accumulation of paper dust and other debris between the cutting blades. By keeping the blades well-lubricated, this debris can be minimized, reducing the frequency of jams and thus, the need for cooldown periods. However, it’s essential to use the correct type of lubricant and to apply it according to the manufacturer’s recommendations – using an improper lubricant or too much can be just as detrimental as not lubricating the shredder at all.
Therefore, proper maintenance through consistent lubrication is a key factor in managing shredders with shorter cooldown times. Notably, this maintenance regime contributes to the shredder’s efficient operation, reduces potential downtimes due to jams or mechanical wear, and prolongs the life of the machine. Regular attention to lubrication details aligns with an overall maintenance strategy that includes operating the shredder within its capabilities, avoiding overfeeding, and adhering to the recommended cooldown periods, all of which support the performance and durability of the shredding device.
Shredder Usage Patterns and Impact on Motor Health
Understanding the usage patterns of a shredder is critical for maintaining its health, particularly the motor, as it’s the heart of the device. Paper shredders are employed in various settings, from home offices to large corporate environments, and each scenario presents a different pattern of use. The intensity and duration of shredding activity can substantially impact the motor’s health over time.
Frequent start-stop cycles, as often seen in a typical office setting where shredding is done intermittently throughout the day, can induce varying loads on the motor. This can lead to heat generation, which, if not managed properly, may result in premature wear and tear. Conversely, continuous use over prolonged periods, which might occur in more industrial settings, pushes the motor to operate under a constant load, leading to a steady build-up of heat. If the heat is not dissipated effectively, it can cause the motor to overheat and, eventually, fail.
It’s important to note that different shredders are designed with motors that have varying tolerances for heat and workload. Regularly pushing a shredder beyond its designed capacity can drastically reduce its life expectancy. To preserve motor health, end users should be mindful of the rated capacity and recommended duty cycle of their shredders, refraining from pushing the equipment to its limits.
In relation to maintenance considerations for shredders with shorter cooldown times, it’s essential to recognize that while a shorter cooldown period indicates a more efficient heat dissipation system, it doesn’t negate the necessity for proper care. Here are several maintenance considerations:
– Even with shorter cooldown times, users should avoid continuous operation up to the point of triggering a cooldown period, as frequent encounters with the thermal threshold can degrade motor performance over time.
– Routine maintenance should include not only lubrication but also checking for signs of overheating, such as discoloration of motor parts or a burning smell. This can catch issues before they lead to bigger problems.
– Users of shredders with shorter cooldown times might become complacent, thinking the machine is less prone to overheating. However, it remains vital to operate within the recommended parameters and provide the shredder with breaks during extended shredding tasks.
– The quality and viscosity of the lubricant used may also affect the shredder’s thermal management. It’s important to adhere to the manufacturer’s recommendations for lubrication frequency and type, as proper lubrication will reduce friction, assisting in heat reduction.
– Lastly, it is advisable to monitor the waste container of the shredder because an overfilled waste bin can obstruct the ventilation and cooling system, leading to unnecessary heat buildup.
By adhering to these suggestions, users can maximize the lifespan and performance of shredders, even those designed with features that promote shorter cool-down times.
Ventilation and Environmental Factors Affecting Cool Down
Ventilation and environmental factors play a critical role in determining the cool down times of shredders. These elements directly impact how quickly a shredder can dissipate the heat generated during its operation. Efficient cooling is vital to maintain the performance and longevity of the shredding machine.
In any setting where a shredder is used, proper airflow is essential. Adequate ventilation ensures that hot air generated by the shredder’s motor is replaced with cooler ambient air, aiding in the cool down process. A poorly ventilated environment will trap heat around the shredder, keeping the temperature of the device elevated and possibly leading to overheating. To mitigate this, shredders should be placed in well-ventilated areas or rooms with air conditioning or fan systems that can facilitate air movement.
The ambient temperature of the environment where the shredder is located also affects the shredder’s ability to cool down efficiently. Shredders operating in hot climates or in areas exposed to direct sunlight will have higher base temperatures and thus, take longer to cool down. To avoid this issue, it’s best to place shredders away from heat sources and in temperature-controlled environments.
Maintenance considerations for shredders with shorter cool down times include ensuring the shredder does not operate continuously beyond its rated capacity. Continuous use beyond intended limits can overstress the motor, necessitating more frequent maintenance or even repairs. It is also crucial to adhere to the manufacturer’s recommended cool down periods. If a shredder has a shorter cool down time, it may be designed for more intermittent use, so understanding and respecting this limitation is necessary to prevent premature wear.
For these high-efficiency shredders, performing regular check-ups on ventilation efficiency is important. The vents or fans within the shredder should be kept clean and unobstructed to maintain optimal airflow. Dust and debris accumulation can hinder proper air circulation, reducing the effectiveness of the cooling systems.
Lastly, the environment itself must be maintained to support the shredder’s cooling needs. Regularly monitoring and adjusting the room temperature, ensuring that the shredder is not placed near heating vents, and avoiding direct sunlight can help to maintain shorter cool down times. By considering these environmental and ventilation factors, you can maximize the operational efficiency and lifespan of your shredder.
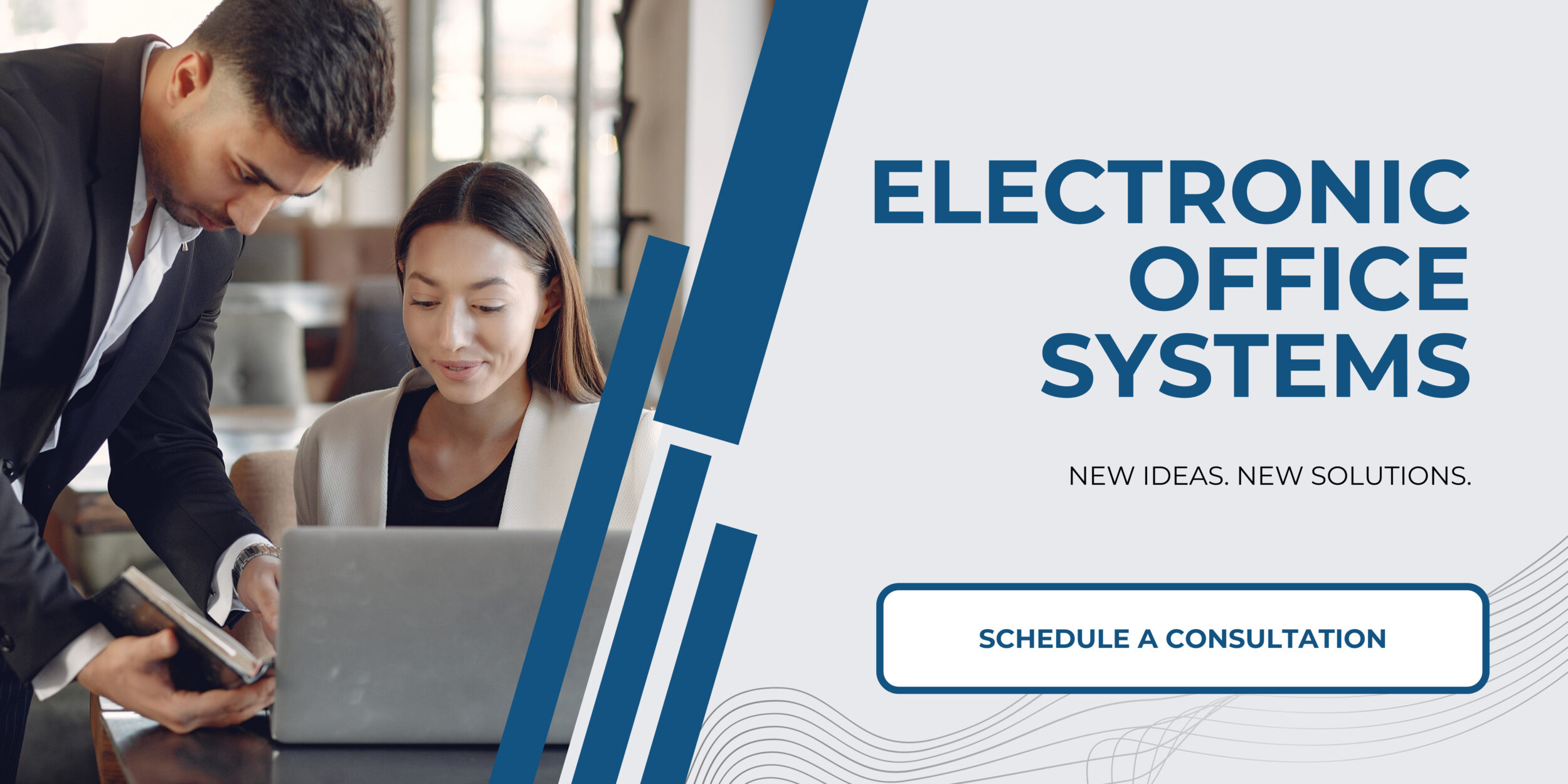
Regular Cleaning and Waste Management Procedures
Regular cleaning and waste management procedures are crucial aspects of maintaining a paper shredder and ensuring its longevity. These procedures go beyond simply emptying the waste bin when it is full; they involve thorough cleaning of the shredder’s blades, the removal of paper dust and other debris that might accumulate inside the machine, and proper disposal of shredded materials compliant with environmental regulations or organizational guidelines for sensitive information.
The frequency of cleaning a shredder can vary based on its usage. In a heavy-use environment such as an office, cleaning may be required more frequently than in a home setting. To clean a shredder, you should start by unplugging the device for safety. Then you can use a can of compressed air to blow out paper particles from the cutting heads and the internal mechanism. For thorough cleaning, use a shredder oil sheet or apply shredder oil to a piece of paper to run through the machine, lubricating the cutting blades and picking up residual particles. This not only cleans but also maintains the sharpness and efficiency of the blades.
As part of waste management, you should ensure that shredded materials are disposed of properly. If the shredder is used for sensitive documents, the waste should be handled according to data protection laws, which often require cross-cut or micro-cut shredders that make the documents unrecoverable. For the environmentally conscious, recycling shredded paper is generally possible, but it’s important to check local recycling guidelines since some facilities may not accept shredded paper or might require it to be bagged separately.
Regarding maintenance considerations for shredders with shorter cool down times, it’s essential to understand that shredders with short cool down periods are typically designed to handle more frequent use. However, with more usage comes the likelihood of increased wear and tear, meaning maintenance tasks become more critical. For instance, lubricating the shredder is necessary to ensure that the cutting blades continue to operate smoothly and without causing strain on the motor, which helps prevent overheating.
Moreover, shorter cool down periods mean that the machine’s components are exposed to heat more regularly, possibly leading to a quicker accumulation of dust and debris, which can have an insulating effect, retaining unwanted heat within the shredder. Keeping the shredder clean is, therefore, even more imperative. Regularly scheduled maintenance checks can preemptively identify any wear on the cutting blades or motor before major issues arise. Ensuring that the shredder is in a well-ventilated area also helps dissipate heat more efficiently after each use, which contributes to the reduced risk of overheating, irrespective of the cool down period.
In summary, maintenance for shredders with shorter cool down periods should focus on regular lubrication, thorough cleaning to avoid dust build-up, and adequate attention to shredding only the quantity of paper that the machine is rated for, to prevent stressing the components unnecessarily. Keeping these factors in mind will help mitigate the chances of malfunction or the need for more significant repairs down the line.