Shredders with overheat protection are vital tools in both office and home environments, providing security in discarding sensitive documents and helping to manage waste. While they are designed to be durable and user-friendly, regular maintenance is crucial to ensure they operate effectively and have a long service life. The purpose of overheat protection is to prevent the shredding device from reaching temperatures that could damage its internal components or pose a safety hazard. However, relying solely on built-in protection is not enough. Owners must be proactive in understanding and carrying out proper maintenance procedures.
In this article, we will delve into the various maintenance considerations for shredders with overheat protection. We’ll discuss the importance of understanding the shredder’s operating limits and the overheat protection mechanism to ensure it functions as intended. We will examine why regular cleaning and oiling are essential to maintaining the integrity of the shredding blades and internal gears. Additionally, we’ll look at the need for proper feeding techniques to avoid overburdening the machine, which not only can trigger the overheat protection but can also reduce the shredder’s lifespan.
It’s also worth noting the role of a well-ventilated environment for the shredder to maintain optimal operating temperatures. Furthermore, we’ll explore how the selection of shredded materials can impact maintenance schedules and the importance of adhering to the manufacturer’s guidelines for paper thickness and the type of materials that can be shredded without causing harm to the machine. From recognizing signs of potential issues to a breakdown of the most common maintenance tasks, this article aims to provide a thorough overview of keeping your shredder with overheat protection running smoothly for years to come.
Understanding Overheat Protection Mechanism
Overheat protection in shredders is a crucial feature that helps prevent damage to the motor and internal components caused by excessive heat. When a shredder operates, it generates heat due to the mechanical work of cutting through materials such as paper, plastic cards, and sometimes even small metal objects like staples or paper clips. The amount of heat generated can become excessive, particularly during extended periods of use or when shredding materials that are tough to break down.
The overheat protection mechanism is typically a thermal sensor or a thermal fuse wired within the shredder’s circuitry. These sensors monitor the temperature inside the shredder and either trigger a shutdown or a cooldown process if the temperature crosses a pre-set threshold. This threshold is usually set at a level that is considered to be safe for both the machine and the surrounding environment.
When a shredder with overheat protection begins to get too hot, the mechanism will effectively halt the shredding process, thereby preventing potential damage or even fire hazards. After it has shut down, the shredder will require a cooldown period before it can safely be used again. During this time, the heat dissipates, and the risk of overheating is significantly reduced. This is a crucial feature for prolonging the life of the shredder and ensuring the safety of its operation.
For maintenance considerations with regards to the overheat protection feature in shredders, several factors should be taken into account:
1. **Regular Cleaning**: Over time, shredders can accumulate dust and debris, which can insulate heat and contribute to overheating. Regular cleaning of the shredder can help to maintain proper airflow and prevent the build-up of materials that can trap heat inside the machine.
2. **Proper Lubrication**: Lubrication is important for the smooth operation of the cutting blades, which in turn, reduces the effort required by the motor and the generated heat. There are usually specific instructions from the manufacturer on how and how often to lubricate the shredder.
3. **Appropriate Usage**: It’s important to adhere to the manufacturer specifications for what can and can’t be shredded, as well as how much material can be fed into the shredder at once. Overloading the shredder can cause it to overheat more quickly.
4. **Adequate Ventilation**: Ensuring that your shredder is in a well-ventilated space can help to prevent overheating. Heat can accumulate around the shredder if it is in a confined space or if it’s surrounded by other heat-generating devices.
5. **Periodic Inspections**: Regular inspections of the overheat protection mechanism itself can ensure it is functioning correctly. If a thermal sensor fails, it might not detect an overheat condition, which could lead to damage.
By understanding how the overheat protection mechanism functions and adhering to these maintenance considerations, you can help guarantee that your shredder operates safely and effectively for as long as possible. Regular adherence to maintenance protocols ensures both operator safety and the longevity of the shredder.
Scheduled Cleaning and Lubrication
Scheduled cleaning and lubrication are critical aspects of maintaining a shredder with overheat protection. Overheat protection in a shredder typically involves a thermal cutoff feature that is designed to shut off the power to the motor when it reaches a temperature that is too high, preventing potential damage to the shredder’s internal components or even a fire hazard. Regularly cleaning and lubricating a shredder can significantly contribute to preventing such overheating situations and extending the life of the shredder.
From a maintenance perspective, shredders need to be kept clear of paper dust and debris that can accumulate over time. Paper particles and other materials can clog the shredder’s cutting blades, which requires the motor to work harder to push materials through, potentially leading to overheating. Scheduled cleaning should involve removing any bits of paper or other debris caught in the blades or mechanisms, which is often best done with a can of compressed air or a specialized vacuum attachment designed for electronic equipment to ensure thorough removal of such particles.
Lubrication is equally crucial for maintaining the smooth operation of the shredders’ cutting components. Proper lubrication helps reduce friction between moving parts, which can lead to heat build-up and wear. For shredders, specifically, manufacturers often recommend the use of specific shredder oil. This oil is applied directly to the cutting blades to ensure they continue to move freely and prevent papers from jamming, which is a common cause of overheating. The frequency of lubrication will depend on the shredder’s use – heavy usage would naturally call for more frequent lubrication compared to light use.
Other considerations for maintaining a shredder with overheat protection include operating the shredder within its recommended capacity to avoid strain on the motor and ensuring that the correct types of materials are being shredded – as foreign objects or non-recommended materials can cause jams or stress the motor. Moreover, ensuring good ventilation around the shredder can prevent an ambient temperature rise that could contribute to overheating.
Routine maintenance aligned with the manufacturer’s recommendations can prevent downtime due to repairs, avoid unexpected costs, and ensure that the shredder with overheat protection operates reliably and safely for years to come. Neglecting these simple maintenance steps can lead to larger issues, which could not only damage the shredder but also pose safety risks to users.
Proper Usage and Material Load Specifications
Proper usage and adherence to material load specifications are essential for optimizing the performance and lifespan of a shredder. A shredder designed to operate within certain parameters will perform best when used as intended. Overloading a shredder with too many sheets of paper, feeding in materials that are too tough, or attempting to shred items not recommended by the manufacturer can lead to a variety of problems. These issues can include paper jams, wear and tear on the shredding blades, motor strain, and ultimately, overheating, which despite having overheat protection, can still diminish the efficacy and longevity of the shredder.
Understanding the specifications of a shredder means recognizing the maximum number of sheets it can shred simultaneously, the types of materials it can handle (e.g., paper, credit cards, CDs), and any maximum duty cycle that represents how long the shredder can operate before needing a cool-down period. By respecting these guidelines, users can ensure their shredder functions smoothly and benefits from the full protective capabilities of features like overheat protection—systems typically involving sensors and thermal cutoff mechanisms to prevent damage from excessive heat buildup.
Maintenance considerations for a shredder with overheat protection incorporate a number of proactive and reactive measures. Regular cleaning is vital, as accumulated dust and debris can insulate heat within the shredder’s components, making the overheat protection more likely to engage. It’s also important to allow the shredder time to cool down after long uses, even if it has not yet triggered its overheat protection, to prevent stress on the motor and other internal parts. By allowing the machine to operate within regular intervals, issues related to excessive temperature rise can be minimized.
Lubrication is another key maintenance task, as it ensures the blades operate smoothly and reduces the effort the motor must exert, subsequently lessening the heat generated during shredding. Most shredders benefit from specialized shredder oil applied directly to the blades or sheets of lubricant paper run through the device. This also aids in maintaining a cleaner cutting mechanism, which aligns with the standard maintenance practice of cleaning.
Lastly, it’s imperative to be responsive to the warnings or automatic shutdowns initiated by overheat protections. When a shredder indicates it has reached its heat limit, users should allow an ample cool-down period before resuming operation. Additionally, regular checks for signs of wear and tear that may impact the shredder’s ability to manage heat should be conducted in conjunction with the manufacturer’s recommended inspection schedule. This proactive approach not only prolongs the shredder’s life but also ensures it remains safe to use.
Ventilation and Environment Control
Ventilation and environment control are critical aspects of maintaining a shredder with overheat protection. This item 4 from the numbered list emphasizes the importance of ensuring that the shredder operates in an environment that facilitates its ability to maintain a proper temperature during operation.
Most shredders are designed with an internal cooling system that can include fans and heat sinks to dissipate heat effectively. Overheat protection is an additional feature that monitors the temperature of the machine, typically through sensors. When the internal components reach a threshold temperature that risks damaging the motor or the electronic parts, this feature triggers a shutdown to prevent overheating. This mechanism ensures the longevity of the shredder and promotes safety.
For the overheat protection to function correctly, the ambient environment must be conducive to cooling. This means that the shredder should be placed in a well-ventilated area where airflow can freely circulate around it. This prevents hot air from being trapped around the machine, which could lead to increasing internal temperatures despite the active cooling mechanisms.
Additionally, there should be no blockages around the ventilation slots of the shredder. These are typically designed to allow hot air to escape and cooler air to enter. Placing objects too close to these vents or obstructing them with paperwork or other materials can significantly reduce their effectiveness.
Environmental control also refers to the temperature and humidity of the room where the shredder is located. The shredder should be in a cool and dry area, as high humidity can exacerbate the potential for overheating and condensation inside the machine, leading to oxidation or electronic failures. It’s also advised to avoid placing shredders in direct sunlight or near heating sources, such as radiators or heaters, which can contribute to increased operating temperatures.
It is important to consider few maintenance considerations for a shredder with overheat protection:
1. **Monitor Ambient Temperature**: Ensure the room where the shredder is being operated is not too hot. Electronic equipment typically works best in cooler temperatures.
2. **Allow for Adequate Airflow**: Do not place the shredder in a confined space. Leave enough room around it for efficient heat dissipation.
3. **Regularly Check and Clean Vents**: Dust and debris can easily clog ventilation ports. This can be mitigated with regular inspection and cleaning to ensure unobstructed airflow.
4. **Consider Humidity Levels**: Too much moisture in the air can be harmful. Use dehumidifiers if necessary to maintain an ideal humidity level in the shredder’s operating environment.
5. **Keep the Shredder Away from Heat Sources**: Position the shredder away from direct sunlight and other heat-generating devices which could exacerbate heat build-up.
Maintaining the environment around a shredder is an integral part of its upkeep and performance, ensuring the overheat protection mechanism functions optimally and the device delivers sustained operation over time.
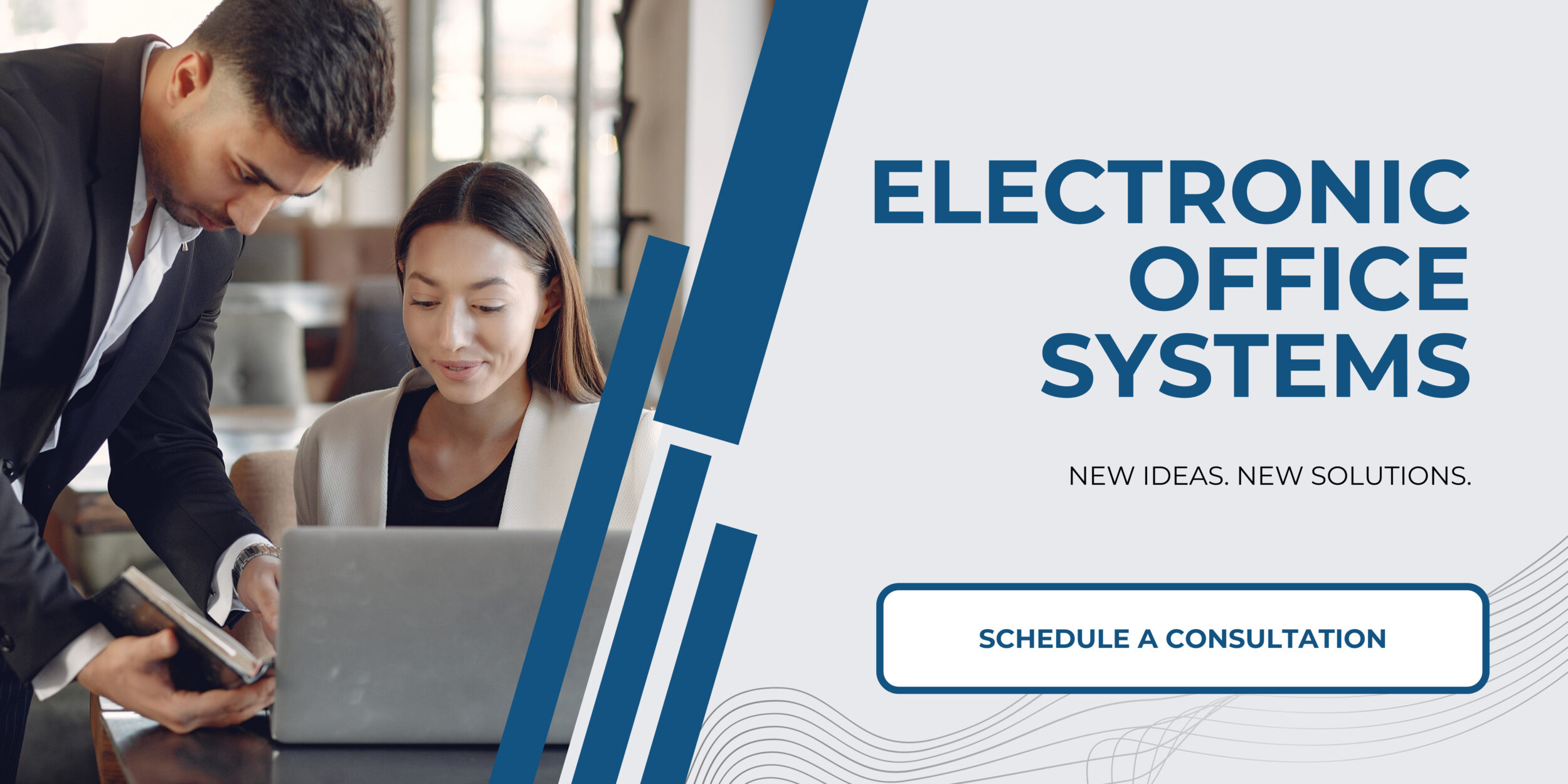
Regular Inspection and Part Replacement Schedule
A crucial aspect of maintaining a shredder with overheat protection is the implementation of a regular inspection and part replacement schedule. This routine maintenance is especially important for ensuring the long-term functionality and safety of the shredding machine. Overheat protection in shredders is typically a feature that prevents the motor from reaching temperatures that could cause damage or pose a fire hazard. However, ensuring that this protection continues to work correctly requires regular checks and servicing.
Regular inspections should include examining the shredder’s blades for dullness or damage. Dull blades can cause the machine to work harder and longer to shred the same amount of material, which can contribute to overheating. Replacing or sharpening the blades as necessary will maintain shredding efficiency and help to prevent overloading the motor. Operators should also check for worn bearings, misalignments, or any other mechanical issues that could increase friction and heat generation within the shredder.
Maintenance of a shredder also involves checking the sensors and safety systems that contribute to the overheat protection mechanism. These might include thermal sensors that trigger an automatic shutdown if temperatures climb too high. Such sensors must be kept in good working order to ensure they can effectively monitor and respond to potential overheating.
Beyond monitoring the shredder’s operational components, maintenance personnel should replace worn parts before they fail. This preemptive approach not only prevents mechanical failures that could lead to overheating but also minimizes the risk of unexpected downtime. Regularly reviewing and adhering to the manufacturer’s guidelines for part replacement intervals is key.
Frequent cleaning is another aspect of operating a shredder with overheat protection. Dust and debris can accumulate in the machine, which may block airflows essential for cooling. Ensuring that the machine’s ventilation pathways are clear supports the overheat protection system in keeping the shredder at a safe operating temperature.
Lastly, it is also wise to keep a stock of critical replacement parts on hand to ensure that routine maintenance or unexpected repairs can be conducted promptly, reducing downtime and preserving the efficiency and longevity of the shredder. Remember that good maintenance practices, including a regular inspection and part replacement schedule, increase safety, lower the risk of breakdowns, and extend the life of the machine.