Contour cutting, a critical process in large format printing, allows for the precise trimming of printed graphics according to their custom shapes and sizes. It is a technique employed to add versatility and visual appeal to advertising materials, decals, stickers, and various types of signage. While this capability has revolutionized the custom graphics and signage industry, it is not without its challenges. Addressing these potential issues is essential to maintaining the quality and efficiency of production.
One of the primary challenges in contour cutting arises from the alignment and registration of the printed graphic with the cutting machine. Accurate print-to-cut registration is essential for ensuring that the cut lines match the printed image perfectly. Any misalignment can result in a poor-quality product, with potential errors such as incomplete cuts or undesired borders around the design. This precision becomes even more critical with intricate designs and smaller details that are common in large format graphics.
Another significant challenge is material handling. Large format prints often involve heavy, unwieldy rolls of material that can be difficult to manage. Ensuring that these materials feed correctly through the printer and cutter without shifting is paramount to achieving a clean cut. Variations in material behavior due to environmental factors like temperature and humidity can further complicate this process.
Further complexities arise from the diversity of materials used in large format printing. Each medium—be it vinyl, fabric, paper, or other specialty substrates—has its own properties and requires specific cutting tools and settings. Identifying the optimal cutting force, speed, and blade type is crucial to prevent issues such as tearing, dragging, or incomplete cuts. Moreover, the longevity and wear of cutting blades present an ongoing challenge, as dull blades can compromise cut quality and lead to material wastage.
Moreover, technological advancements and software integration play a vital role in streamlining the contour cutting process. Keeping pace with software updates, understanding the intricacies of file preparation, and managing the digital aspects of the workflow can present steep learning curves for operators. Technical difficulties, equipment failures, or software glitches can all result in costly delays and rework.
In a comprehensive article, each of these challenges demands closer inspection. By understanding the various obstacles faced during the contour cutting process in large format printing, industry professionals can better anticipate problems and implement effective strategies to overcome them, ensuring the delivery of high-quality products that meet the exacting standards of clients. The article would delve deeper into these issues, providing insights into the technologies and best practices that can help mitigate the risks associated with contour cutting, ultimately contributing to a more efficient and reliable production process.
Material Handling and Alignment
Material Handling and Alignment are crucial factors in the contour cutting process in large format printing. Contour cutting is used to cut shapes or outlines around a printed design, which can range from simple circles to more complex custom shapes. The material handling aspect of this process involves the loading and feeding of the print material into the cutting machine. For large format prints, this often means handling very large and unwieldy sheets or rolls of printed material, which requires careful coordination and physical strength.
Once the material is loaded, proper alignment is essential. Aligning the material correctly ensures that the cuts are made in the right place relative to the printed image. This usually involves aligning reference points or edges of the material with corresponding alignment mechanisms or marks on the cutter. Poor alignment can result in the cuts not matching the printed image, leading to waste of both time and materials.
Challenges in material handling and alignment can arise due to various factors. One significant challenge is the nature of the material itself. Flexible materials such as vinyl can be difficult to keep flat and taut, causing unwanted shifts that misalign the print with the cutting path. Stiffer materials may not easily conform to the feed mechanism of the cutter or may cause jams. Additionally, the weight and size of large format materials might require multiple persons or specialized equipment to handle without causing damage or disruption.
Another challenge is ensuring consistent alignment throughout the cutting process. As the material moves through the cutter, any slippage or feeding error can skew the alignment and compromise the precision of the cut. This problem is compounded in longer run jobs where a slight misalignment can be magnified over the length of the material.
Moreover, the type of cutter used can also impact the ease of material handling and alignment. Some advanced cutters have automated optical recognition systems that can detect registration marks and auto-align the material, but these systems can be expensive and may not always work perfectly with all materials and print configurations.
Overall, effectively managing material handling and alignment requires meticulous attention to detail, thorough knowledge of the equipment and materials, and sometimes, creative problem-solving to adapt to the unique challenges posed by each cutting job. Investing in proper staff training and maintaining the equipment can help overcome many of these issues and lead to a smoother, more efficient contour cutting process.
Accuracy and Precision Issues
Accuracy and precision are critical factors when it comes to contour cutting in large format printing. The contour cutting process involves cutting shapes precisely along the edges of printed graphics, which requires the cutter to follow a predefined path accurately. This operation relies heavily on the coordination between the printer and cutter to ensure that the cut lines match the printed image exactly.
One of the primary challenges of achieving high accuracy and precision in contour cutting is the potential for misalignment. This may occur if the printed graphics have shifted during the printing process or if the material has been loaded incorrectly into the cutter. Even slight misalignments can cause the cuts to be off, leading to wasted materials and print jobs that do not meet quality standards.
Another challenge is related to the cutter’s mechanical precision. Mechanical play or backlash in the cutter’s hardware can lead to imprecise cuts. This is particularly challenging when cutting complex shapes or when working with very large prints where small errors can be magnified over the length of the material.
Moreover, different materials may behave differently under the cutter’s blade. For example, some materials may stretch, compress, or distort during the cutting process, which can throw off the accuracy of the cut. Selecting the right blade type, adjusting the blade force, and ensuring the material is taut can mitigate these issues, but this often requires a trial and error process to determine the correct settings for each material type.
The precision of the cutting process also depends on the accuracy of the registration marks that are printed along with the graphics. These marks are used by optical sensors on the cutter to align the cutting path with the printed image. If the registration marks are not printed precisely or if the cutter’s sensors do not accurately read them, this can lead to issues with the contour cutting accuracy.
Lastly, wear and tear on the cutting blades and the maintenance of the cutting machinery can impact the precision of cuts. Dull blades can cause dragging or incomplete cuts, and poorly maintained machines can introduce additional errors.
In summary, achieving the required level of accuracy and precision in contour cutting involves overcoming the challenges posed by material handling, the mechanical precision of the cutter, the effects of different materials, the accuracy of registration marks, and the maintenance of the cutting machinery. Each of these factors must be carefully managed to ensure that the final print product meets the specified quality standards.
Calibration and Cutting Force Adjustments
Calibration and cutting force adjustments are critical aspects of the contour cutting process in large format printing. These factors directly influence the quality of the final printed material. Calibration refers to the alignment and synchronization of the cutting tool with the printed graphics to ensure precise and accurate cuts. Accurate calibration guarantees that the contour cuts follow the intended paths as designed in the digital files. This process usually involves fine-tuning the cutter’s blade position, the alignment of the printing and cutting media, and ensuring that the blade precisely follows the contour lines of the printed images or designs.
Cutting force, on the other hand, pertains to the pressure exerted by the cutting blade on the material. Adjusting the cutting force is crucial since different materials require varying levels of force to achieve a clean cut. A cutting force that is too low may result in incomplete cuts, requiring a second pass or manual trimming, which affects productivity and material waste. Conversely, excessive force can damage the material, leading to unusable graphics and excessive wear on the cutting blade and machinery.
The challenges that might arise during the contour cutting process are numerous. The primary obstacle is ensuring consistent calibration during long print-and-cut jobs. Material feed and tracking issues can cause misalignment over time, which is particularly problematic for long contour cuts. Large format printers and cutters must maintain precision over the entire length and breadth of the material to prevent discrepancies that can render the entire piece unusable.
Moreover, variations in material thickness, texture, and rigidity require constant monitoring and adjustments to the cutting force. Users need to be familiar with the characteristics of various materials to determine the optimal cutting force for each. This can be challenging when working with new or mixed media types, leading to trial and error in finding the right settings, potentially resulting in material waste and increased costs.
Another challenge involves maintaining the sharpness and condition of the cutting blade. A dull blade can cause drag, incomplete cuts, or the blade to deviate from the intended cut path. Regular maintenance and timely replacement of blades are therefore essential to prevent quality issues.
Environmental factors, such as temperature and humidity, can also affect the materials and cutting process. These conditions may alter the material dimensions slightly, leading to faults in the calibration. Operators must be aware of these potential variations and adjust the equipment accordingly.
To manage these challenges, large format printing businesses invest in high-quality equipment with sophisticated calibration systems and precise force control mechanisms. Skilled operators who understand the intricacies of the printing materials and equipment are also essential to navigate the complexities of precise contour cutting. Training and experience are invaluable in preventing errors and ensuring high-quality results in large format printing projects.
Software and File Preparation
Software and file preparation is a crucial aspect of the contour cutting process in large format printing, as it lays the groundwork for the production of precise and high-quality graphics. This step involves using specialized graphics software to design and layout the images or shapes that will be printed and then cut. The files must be properly formatted, with vectors and cut lines clearly established so that the cutting equipment can interpret and execute the cut accurately.
One primary challenge associated with software and file preparation is ensuring that the files are compatible with both the printing and cutting machinery. Compatibility issues may lead to the breakdown of the workflow, causing delays and increasing the potential for errors. Having software that can seamlessly integrate the design and cutting process is essential for efficiency.
Moreover, setting up the correct cut lines, also known as ‘contour lines,’ is essential. The software must be accurate to define these lines, so the cutter knows precisely where to cut around the printed graphics. Inconsistencies or inaccuracies in cut lines can lead to wasted material and unsellable products due to misalignment or incomplete cuts.
Another potential challenge is the complexity of the artwork. Complex designs with intricate cuts require meticulous file preparation to ensure that the cutter can accurately follow the contours. More complicated designs increase the risk of errors, which may not only waste materials but also time, as the setup and troubleshooting become more time-consuming.
Finally, the operator’s expertise with the software is also a significant factor. Skilled technicians need to manage the software settings, adjust the cut paths, and correct potential issues within the file before sending it to cut. A lack of adequate training or experience can increase the likelihood of mistakes during the file preparation stage, adding to the complexity of contour cutting in large format printing.
Understanding and overcoming these challenges can lead to more efficient production processes, less material waste, and higher-quality finished products in large format printing projects.
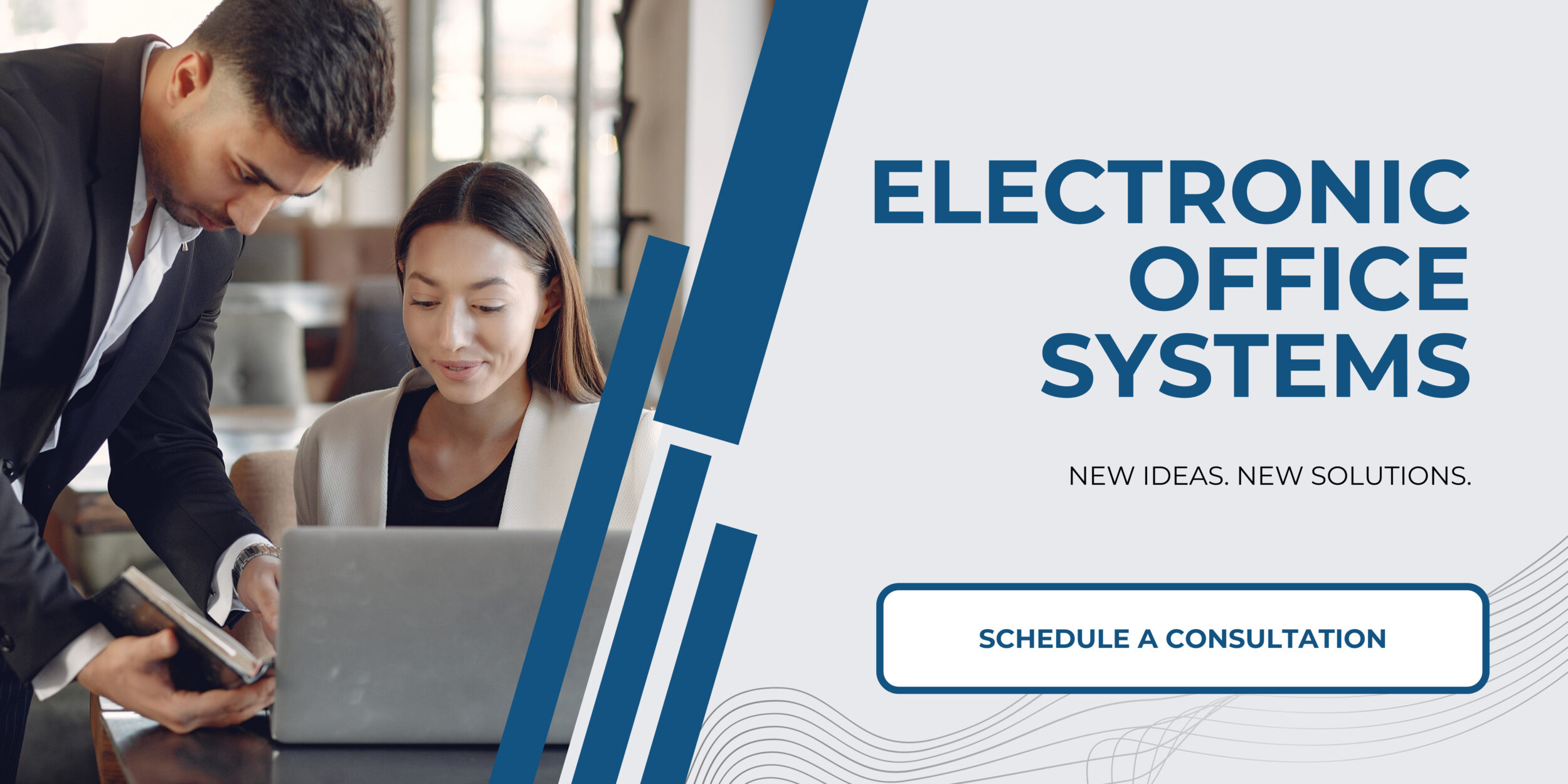
Environmental Factors and Machine Maintenance
Environmental factors and machine maintenance play a critical role in the contour cutting process within the realm of large format printing. When considering environmental factors, we must account for the workspace’s temperature, humidity, and cleanliness. For instance, fluctuations in temperature and humidity can cause materials to expand or contract, leading to inaccuracies in the cutting process. Materials like vinyl or laminate can be particularly sensitive to these changes, which can result in unwanted distortions or misalignments during cutting.
Moreover, dust and debris in the working environment can accumulate on both the printing materials and the cutting machinery. Such particles can interfere with the cutter’s optical sensors, which are paramount for detecting contour lines. Cleaning protocols must be established to ensure that sensors and the cutting path remain unobstructed. Additionally, static electricity, often overlooked, can attract dust and even cause the media to feed incorrectly, which further complicates the cutting process.
Machine maintenance is another area that requires constant attention. Regular preventive maintenance is vital to ensure the longevity and consistent performance of cutting machines. Failing to maintain the cutter can lead to various issues, including the blunting of the blade, which results in poor cut quality and can damage the material. Worn or malfunctioning parts, such as belts, gears, or bearings, can also cause imprecision in cutting.
The challenges arising from inadequate machine maintenance include diminished accuracy, increased waste due to errors, and potential downtime that interrupts production schedules. It’s crucial for businesses to establish a regular maintenance schedule that covers the inspection and replacement of crucial components, blade sharpening or replacement, and software updates to enhance performance and reduce downtimes.
Lastly, experienced personnel must be available to troubleshoot and adjust the machinery as needed. The expertise of the operator matters significantly; they must be able to interpret signs of mechanical wear or environmental impact and adjust the machine settings accordingly to achieve the best possible cutting results.
In conclusion, awareness of environmental factors and a strict adherence to machine maintenance are paramount in mitigating challenges in contour cutting within large format printing. By controlling these variables, businesses can maintain high-quality output, prolong their equipment’s service life, and ensure client satisfaction.