The proper maintenance and operation of industrial shredders are crucial for ensuring their longevity and performance. One aspect of shredder operation that often generates discussion among users and manufacturers is the impact of the cooling down period on the machine’s propensity for overheating. Generally, shredders are equipped with built-in cooling systems designed to manage heat generation during the shredding process. However, the cool down time—defined as the interval during which the machine is allowed to rest and return to a lower temperature before being restarted or subjected to further strain—plays a significant role in preventing thermal stress and potential overheating.
In a comprehensive exploration of the relationship between cool down times and shredder overheating, several key factors must be taken into consideration. First, the design and efficiency of the shredder’s cooling system are paramount; systems that dissipate heat effectively may allow for shorter cool down periods without compromising the machine’s integrity. Second, the intensity and duration of shredding tasks prior to the cool down directly influence the heat load that must be managed. Higher volumes of material or denser items can cause greater heat buildup, thereby requiring longer cool down times to ensure safe temperatures are reached before resumption.
Furthermore, the ambient temperature and the operating environment can also affect a shredder’s cooling efficiency. A shredder operating in a hot, poorly-ventilated space may retain heat longer and thus may be at a higher risk of overheating without a sufficient cooling period. Finally, the mechanical condition of the shredder itself, particularly the wear and tear on critical components like motors, bearings, and cutting blades, can have an impact on heat generation and the associated risks of short cooldown intervals leading to overheating.
Understanding the nuanced interplay of these elements is essential for developing best practices for shredder operation and maintenance. In the following article, we aim to dissect the question at hand: Does a shorter cool down time correlate with a higher risk of the shredder overheating? We will delve into scientific principles, examine industry standards, and review empirical data, all with the objective of illuminating the complexities surrounding this topic. The insights gained will be valuable for users seeking to optimize their shredder’s performance while safeguarding against the costly and potentially dangerous outcome of an overheated machine.
Cool Down Time and Overheating Mechanics
The concept of cool down time in relation to shredders is an important aspect of the device’s operational management. Cool down time refers to the period that a shredder requires to dissipate heat after it has been in use before it can safely be used again. The mechanics of cooling down involve the cessation of activity in order to allow the heat generated by the motor and shredding mechanisms to transfer into the surrounding environment, thereby preventing the device from reaching a temperature that might harm its components.
When it comes to the relationship between cool down time and the risk of overheating, it is generally understood that a direct correlation exists. The cooler a shredder’s motor and mechanical parts are allowed to become between usage sessions, the lower the risk of overheating. This is because the temperature rise within the machine is cumulative; with each successive use without adequate cooling, the shredder’s internal temperature can climb to dangerous levels.
A shredder that is operated continuously without adhering to the recommended cool down periods is far more likely to overheat. Overheating can lead to various problems, such as the breakdown of lubricants that keep mechanical parts running smoothly, damage to sensitive electronic components, and deterioration of the motor itself. Moreover, overheating may also prompt safety mechanisms to activate, shutting down the shredder to prevent further damage or, in worst-case scenarios, causing a fire hazard.
Therefore, it is crucial to allow shredders to cool down properly, respecting the manufacturer’s guidelines for cool down time. This can vary depending on the make and model of the shredder, the ambient temperature in its operating environment, and the intensity of its usage (e.g., shredding heavy-duty materials or large volumes of paper). While a shorter cool down period might seem convenient for those who wish for continuous operation, it significantly increases the risk of overheating and might result in decreased performance and a shorter overall lifespan of the shredder.
Regularly scheduled cool down periods will ensure that a shredder functions safely and efficiently, preserving its operational integrity over time. By acknowledging the importance of cool down time, users can maintain optimal performance and prevent potential hazards associated with shredder overheating.
Factors Influencing Shredder Heat Dissipation
Shredders are designed to destroy documents by cutting them into small pieces. As with any mechanical equipment, shredders have moving parts that generate heat during operation. The heat dissipation of a shredder depends on several factors.
Firstly, the build quality and materials used in the construction of the shredder can significantly impact how effectively it dissipates heat. A well-designed shredder that uses high-quality materials and components will generally be more efficient at heat dissipation, reducing the risk of overheating. For instance, shredders made with metal components are typically better at conducting heat away from the motor and cutting blades compared to those with plastic parts.
Secondly, the power and capability of the shredder play a role in heat dissipation. High-performance shredders designed to handle a heavier workload will typically have more powerful motors and more robust cooling systems to cope with the extra heat generated during prolonged use.
Another critical factor is the environmental conditions where the shredder is used. A well-ventilated space allows heat to disperse more effectively and minimize the buildup of high temperatures within the shredder’s components.
Lastly, the operating cycle of the shredder affects its heat dissipation. This refers to how long the shredder is run and how frequently it is used. Continuous usage without adequate breaks increases the temperature of the device, particularly if it exceeds the recommended run time specified by the manufacturer.
When it comes to the correlation between a shorter cool down time and the risk of a shredder overheating, it is essential to understand that a shredder needs to cool down to prevent the heat from accumulating to a level that could cause damage or degrade the performance of the machine. If a shredder is not given sufficient time to cool down, the heat will not dissipate effectively, causing the temperature of the machine to rise progressively with each use.
An inadequate cool down period can have several consequences, including an increased risk of overheating, which is detrimental to the shredder’s internal components. Continuously running the shredder without allowing for proper cooling can lead to the overheating of the motor, which may eventually result in a thermal shutdown to prevent damage, or worst-case scenario, a complete motor burnout. Moreover, the cutting blades can become dull more rapidly when subjected to high temperatures, affecting the shredder’s efficiency and leading to more frequent maintenance or replacement.
In summary, shredder cooling periods are essential to maintain the longevity and functionality of the device. A shorter cool down time could lead to a greater risk of overheating and subsequent damage or reduced performance. It is vital for users to adhere to the manufacturer’s guidelines regarding the operation and maintenance of their shredder to ensure safe and efficient use.
Effects of Overheating on Shredder Performance and Lifespan
The impacts of overheating on a shredder’s performance and lifespan are significant and multifaceted. When a shredder operates beyond its temperature threshold, the excess heat can result in various mechanical and electrical issues.
From a mechanical standpoint, overheating can lead to the breakdown of lubricants that keep the shredder’s moving parts functioning smoothly. As these lubricants degrade, friction increases, which in turn generates more heat and exacerbates the problem. Over time, the increased wear and tear on the components can cause them to fail prematurely. This is particularly true for the cutting blades, which can lose their sharpness more quickly when exposed to high temperatures, resulting in less efficient operation and more frequent jamming incidents.
In terms of electrical components, the heat can damage the insulation of the wiring and contribute to short circuits or failures of capacitors and other electronic parts. This damage not only affects performance — resulting in decreased throughput and the potential for increased operational pauses — but can also pose safety risks, such as a potential for fires.
Furthermore, consistent overheating can literally warp the metal and plastic parts of a shredder, leading to misalignment and ultimately failure of the machine. Therefore, overheating has dire consequences for a shredder’s overall performance, potentially requiring more frequent repairs and replacements than would otherwise be necessary, and hence, reducing its expected lifespan.
Now, regarding the correlation between shorter cool down times and the risk of a shredder overheating, it is typically observed that allowing a shredder to cool down properly between usage sessions can significantly reduce the likelihood of overheating. Cool down times are designed based on the shredder model’s power, use-case, and built-in thermal protection mechanisms. The period allows the machine to return to a safe operating temperature, preventing the cumulative effects of heat build-up. If a user bypasses the recommended cool down period and continues to operate the shredder, the machine does not have the necessary time to dissipate the heat, increasing the chance of overheating. Consequently, strict adherence to prescribed cool down periods is essential to maintaining optimal performance and extending the shredder’s service life.
Recommended Cool Down Periods for Different Shredder Models
The recommended cool down periods for different shredder models are an essential aspect of managing shredder performance and longevity. Different shredder models can tolerate varying amounts of continuous usage before needing to rest to dissipate heat. The cool down period is specifically the time during which a shredder is left to rest and so as not to be used, ensuring the motor and other critical components have time to cool off and thereby reduce the likelihood of overheating. Manufacturers generally provide guidelines for the maximum run time and necessary cool down period in their product manuals, as these are calculated based on the shredder’s design, power, and built-in thermal protection features.
For instance, basic home office shredders might only handle a few minutes of continuous shredding before requiring a longer cool down period, which can range from 15 minutes to an hour, depending on the specific model and its quality. On the other hand, high-end or commercial shredders might run for 30 minutes or more and require similarly proportional cool down times. When manufacturers determine these periods, they consider various factors, such as the shredder’s cutting capacity, motor size, heat dissipation efficiency, and the materials from which the shredder is constructed.
The correlation between a shorter cool down time and the risk of a shredder overheating is quite strong. Generally, the shorter the cool down period relative to the operating time, the higher the chance of the shredder overheating. This is because the shredder does not have adequate time to release the built-up heat. Continuous operation without proper cooling can strain the motor and other components, which in extreme cases can lead to motor burnout or the breakdown of other parts. It is important to remember that overheating not only jeopardizes the shredder’s immediate functionality but can also shorten its overall lifespan by causing wear and tear on the components.
Moreover, the cool down time should never be disregarded because it is a safety mechanism designed to protect both the machine and the user. Overheating can create a fire hazard or cause the shredder to malfunction in a way that poses a risk to the operator. Therefore, adhering to the manufacturer’s recommended cool down periods is critical for the safe and effective use of a shredder. It’s worth noting that some modern shredders come equipped with technologies designed to manage overheating, such as advanced cooling systems or thermal overload protection, but even these cannot completely eliminate the need for proper cool down times. It’s always best practice to follow the guidelines provided with your specific shredder model to ensure its longevity and safe operation.
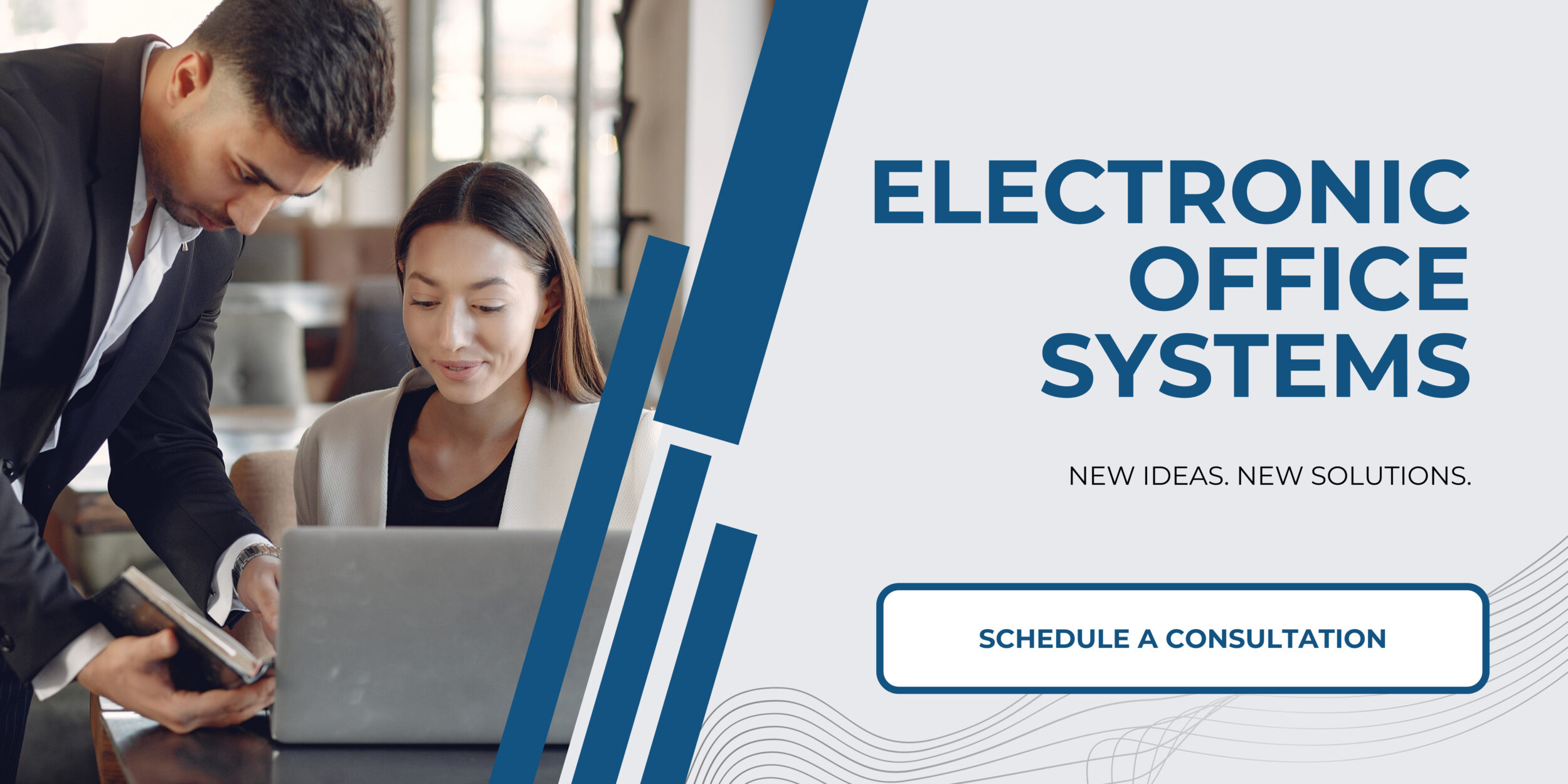
Preventative Measures and Best Practices for Shredder Maintenance
Preventative measures and best practices for shredder maintenance are essential to ensuring your shredder operates efficiently and has a long lifespan. One key aspect of maintaining a shredder is to prevent overheating, which can occur when the device is used for prolonged periods without adequate breaks. Overheating can not only temporarily halt the operation of the shredder due to built-in safety mechanisms but can also cause permanent damage to vital components of the machine over time, reducing its operational life.
Preventative maintenance primarily consists of following the manufacturer’s recommended usage guidelines. This typically includes adhering to the maximum number of continuous operating minutes and respecting the required cool down time. The cool down time is designed to allow the motor and other components to return to a safe temperature, preventing damage from excessive heat build-up.
Shredders typically have a thermal protection feature to shut down the device automatically in case it reaches a dangerous operating temperature, but relying solely on this feature is not advisable. To help maintain a consistent operational temperature and avoid reaching these critical limits, users can perform smaller shredding jobs with breaks in between rather than large, continuous shredding tasks.
Another preventative measure is regular cleaning of the shredder’s blades. Over time, dust and paper debris can accumulate on the blades, which can insulate heat and contribute to overheating. Cleaning the blades not only helps with heat dissipation but also ensures the smooth operation of the cutting mechanism.
Lubricating the shredder is another important maintenance step. Special shredder oil or lubricant sheets are available to keep the cutting mechanism functioning smoothly, which reduces friction and helps prevent overexertion of the motor, leading to less heat generation.
Furthermore, operators should be aware of the shredder’s sheet capacity and avoid feeding more sheets than recommended at one time, as this can cause the motor to work harder and potentially overheat. It’s also advisable to remove staples and paper clips that can cause jams, forcing the motor to work more strenuously than necessary.
In terms of the second query, whether a shorter cool down time correlates with a higher risk of the shredder overheating, it’s important to understand that the cool down time is not just about correlation but causation. A cool down period allows the heat generated by the motor and blades during shredding to dissipate. If a shredder does not cool down sufficiently, subsequent usage will start at a higher temperature, reducing the time it takes to reach critical temperature limits. Consistently ignoring cool down recommendations increases the risk of overheating, which can result in thermal cut-out engages, diminished performance, or damage that can be expensive or impossible to repair. Therefore, recognizing and adhering to the shredder’s cool-down periods is vital in preventing overheating and maintaining the shredder’s longevity.