Title: The Impact of Print Speed on the Vinyl Printing Process in Large Format Printers
Introduction:
In the dynamic world of large format printing, where precision and efficiency are paramount, the speed at which a printer operates can significantly influence the overall quality and productivity of the printing process. Vinyl, a popular material choice for its durability and versatility, is widely used for banners, signs, vehicle wraps, and wall graphics. However, the intricacies of printing on vinyl with a large format printer are subject to the inherent trade-offs between speed, print quality, and operational effectiveness.
Print speed in large format printing refers to the rate at which a printer can produce printed material, usually measured in square feet or meters per hour. This measure, while crucial for meeting deadlines and optimizing workflow, has profound implications on several aspects of the vinyl printing process. It affects not just the turnaround time for print jobs but also factors such as ink adhesion, color fidelity, media compatibility, and ultimately, the longevity and visual impact of the finished product.
This article will delve into the complexities of print speed and explore how it affects the vinyl printing process in large format printers. We will examine the balancing act required to maintain high-quality prints without sacrificing speed, the technical considerations printer operators must navigate, and the innovations in printing technology aimed at optimizing this delicate equilibrium. Understanding the interplay between speed and other elements of the vinyl printing process is essential for professionals in the field to produce vibrant, high-quality graphics that meet the demands of today’s fast-paced market.
Impact on Production Throughput
The influence of print speed on the vinyl printing process in a large format printer is substantial, particularly when it comes to Impact on Production Throughput. Production throughput refers to the amount of work or the number of items that can be produced over a given period. When it comes to large format vinyl printing, several factors are affected by the print speed.
Firstly, with higher print speeds, a large format printer can produce more prints in a shorter period, which increases the overall production output. This is crucial for businesses that need to meet tight deadlines or handle a large volume of print jobs. Quick production rates are often associated with higher workplace efficiency and the ability to take on additional projects, leading to increased revenue and growth potential for print service providers.
However, the print speed must be balanced with quality considerations. If the speed is maximized without regard to quality, it can lead to suboptimal results, such as banding or inaccurate color reproduction, which could ultimately hurt the reputation of the printing service. Faster printing can also cause additional strain on the printer’s mechanical components, potentially leading to more frequent maintenance or even breakdowns, which can interrupt the production process.
Furthermore, high-speed printing typically requires the ink to dry or cure more rapidly to prevent smudging or bleeding as it moves through the printer. This necessity can influence the type of inks and drying systems used in the printer, as some may be better suited to quicker drying times than others. In the case of vinyl, which is a non-absorbent material, selecting the right combination of ink and drying technology is essential to maintain high production speeds without sacrificing quality.
In conclusion, print speed plays a pivotal role in determining the production throughput of a large format printer printing on vinyl. Fast printing can increase the number of jobs that can be completed, which is advantageous for meeting high demand. Nonetheless, a careful balance must be struck to ensure that the output quality remains high and that the equipment is used within its operational limits to avoid excessive wear and tear. All these factors must be considered to optimize the vinyl printing process for both productivity and longevity.
Print Quality and Resolution
Print quality and resolution are crucial aspects of the vinyl printing process, particularly in large format printing. The resolution of a print in large format printing is typically measured in dots per inch (DPI), and it represents the number of individual dots of ink that a printer can produce within a linear inch. Higher-resolution prints have more dots per inch, resulting in a more detailed and clearer image that is essential for large format prints, which are often viewed from a closer distance and thus require a higher level of detail.
When considering the print speed, the correlation between speed and quality must be acknowledged. Faster printing speeds often come at the expense of print quality. This is primarily because high-speed printing doesn’t allow for the same level of detail as slower printing speeds. When the printer operates faster, there tends to be less ink application precision, potential misalignment of the print heads, and inadequate time for the ink to settle on the substrate before the next pass occurs. These factors can lead to a drop in the sharpness of the image, color fidelity, and overall aesthetic appeal of the final product.
Moreover, the print speed can also influence the drying time of the ink. Faster print speeds can result in a requirement for quicker drying inks, which might not be as vibrant or durable as those that dry slower. If the ink does not have enough time to properly cure or adhere to the vinyl, it can cause issues like smudging, which would significantly affect the quality of the final print.
In high-quality large format printing, it’s essential to strike a balance between speed and resolution. While faster production is beneficial for meeting tight deadlines and increasing throughput, it should not come at the cost of the final print’s quality, which is paramount for customer satisfaction. Therefore, print service providers often have to find a middle ground that allows for efficient printing without compromising on the sharpness, clarity, and overall quality that clients expect from large format prints.
It’s also important to consider that different large format printers are optimized for different speed and quality settings. Some modern printers are capable of maintaining high-quality prints at faster speeds due to advanced print head technology, better ink formulations, and precision control systems. Companies should carefully evaluate their printer’s capabilities and optimize their printing processes according to the specific demands of their projects to ensure the best possible outcome.
Material and Ink Usage Efficiency
Material and ink usage efficiency is a critical factor in the vinyl printing process, particularly when using large format printers. Efficiency in this context refers to the optimal use of resources—specifically materials such as vinyl substrate and the inks used to print designs and images. This efficiency is crucial, both from a cost perspective and an environmental standpoint.
When it comes to large format printing, the cost of materials can be one of the most significant expenses incurred by a printing business. Efficient usage of materials means minimizing waste, which can be accomplished by precise print job setup and accurate alignment of the printer. This helps ensure that each piece of vinyl is used to its maximum potential, reducing the need for reprints or excess trimmings that cannot be used.
Likewise, the efficiency of ink usage is of great importance. Inks for large format printers can be expensive, and their cost figures into the final price of printed materials. Ensuring that the printer is correctly calibrated and maintaining high operating standards are essential to avoid overuse of ink, which can occur through over-saturation or the need to reprint due to errors. Modern printers often come with advanced ink management systems designed to reduce ink consumption while maintaining high-quality output.
Furthermore, efficient use of materials and ink is beneficial for the environment. Reducing waste means less material is sent to landfill, and precise ink usage lowers the risk of releasing volatile organic compounds (VOCs) into the atmosphere.
Now, when considering the print speed, its impact on material and ink usage efficiency for large format printers is quite significant. Faster print speeds can mean higher throughput, allowing more work to be done in less time. However, when a printer operates at very high speeds, there may be a trade-off in terms of the precision of ink placement and the overall control over material feed, potentially leading to higher ink consumption and material wastage. For instance, high-speed printing might cause ink to bleed or spray, affecting not just the usage of inks but also the quality of the final print.
Balancing print speed with efficiency requires finely-tuned equipment and expert operation. Printers need to be calibrated carefully for the specific type of vinyl and ink being used. This calibration must consider the drying time of the ink and the correct feed rate of the material through the printer to ensure that the ink is applied consistently and allowed to set properly.
In summary, while faster print speeds in large format vinyl printing can increase production throughput, they must be managed carefully to maintain efficiency in materials and ink usage. Unchecked speed can lead to overuse and wastage of resources, cutting into profitability and potentially diminishing the sustainability of the printing process. Understanding the interplay between speed and efficiency is key for any printing business that aims to produce high-quality outputs in a cost-effective and environmentally conscious manner.
Maintenance and Wear on Printer Components
Maintenance and wear on printer components are critical aspects that significantly influence the operational efficiency and longevity of large format vinyl printers. These impacts stem from how frequently the printer is used, the type of materials processed, environmental conditions, and the print speed settings employed during operations.
Print speed is a substantial factor in determining the rate of wear and the required maintenance of printer components. When a large format printer operates at high speeds, the mechanical components, such as the print head carriage, rollers, and belts, are subjected to greater stress. This stress can lead to accelerated wear and, subsequently, more frequent maintenance or replacement of parts. High-speed printing often involves faster movement of the print heads across the material, leading to quicker degradation through mechanical wear and tear.
Furthermore, the higher the speed, the shorter the contact time between the print heads and the substrate. This can sometimes compromise the precision of ink drop placement, leading to potential quality issues that may necessitate additional maintenance to recalibrate the print heads or adjust the printer’s settings.
Slower print speeds, on the other hand, can result in less mechanical strain on the printer components, potentially reducing the printer’s overall wear and extending the time between needed maintenance intervals. However, operating at lower speeds may also lead to a decrease in production throughput, so businesses must find a balance between maintaining printer longevity and meeting production demands.
In addition to mechanical considerations, the thermal management of the printer is also affected by print speed. High-speed printing can generate more heat, which, if not adequately dissipated, can lead to overheating of the print head nozzles, impacting their performance and lifespan.
Ultimately, understanding the relationship between print speed and the maintenance and wear on printer components is essential for optimizing the performance and durability of a large format vinyl printer. Regularly scheduled maintenance, proper handling, and the use of high-quality components can help mitigate the adverse effects of high-speed printing, ensuring that the printer operates efficiently and consistently produces high-quality prints.
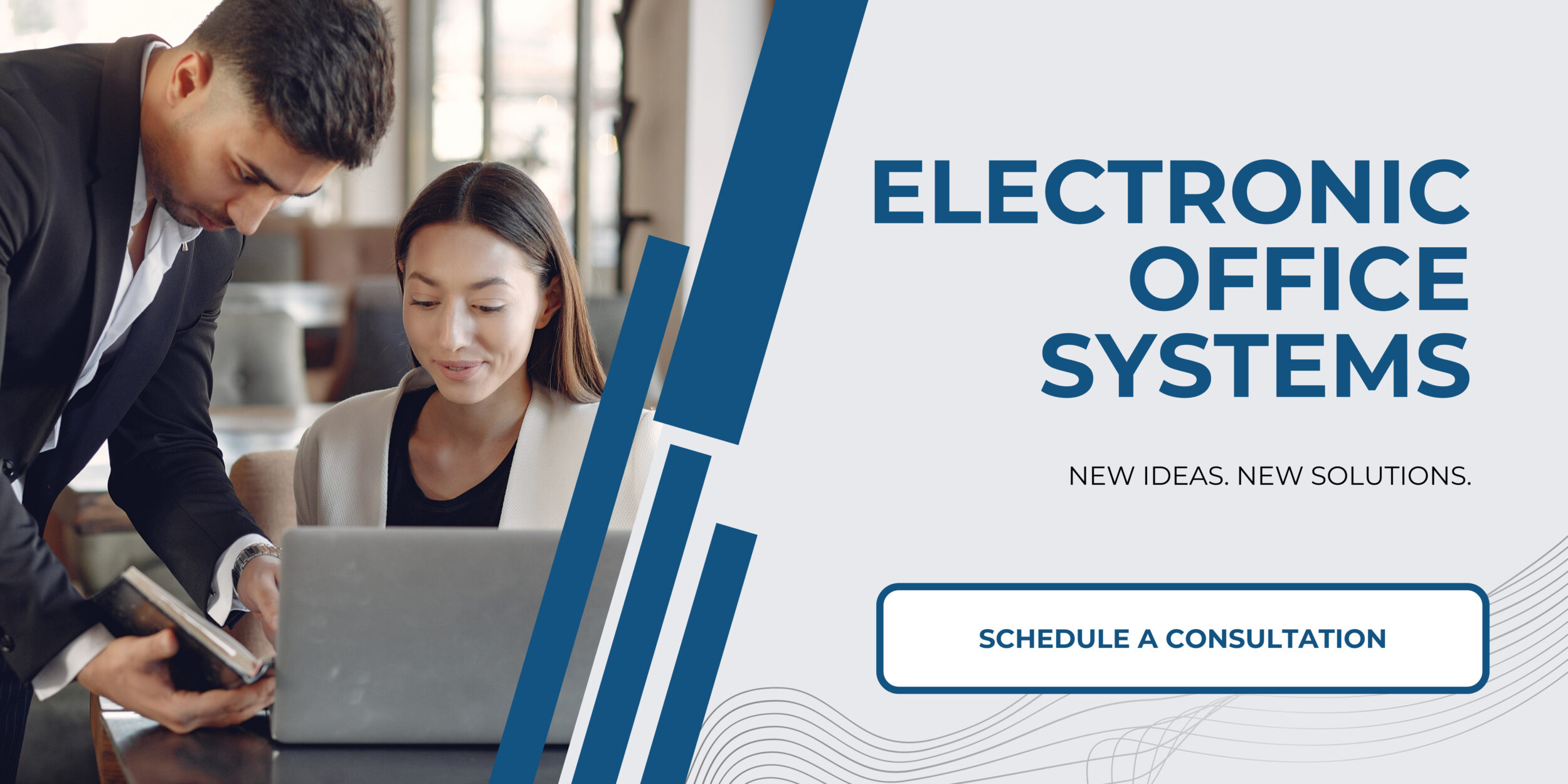
“`html
Drying and Curing Times
“`
Drying and curing times are an essential aspect of the vinyl printing process, particularly when using large format printers. These terms are not synonymous, although they’re often used interchangeably. Drying generally refers to the process where solvents (or water in the case of latex inks) evaporate from the printed ink, leaving the pigment on the substrate. Curing, on the other hand, is where the ink undergoes a chemical reaction to set or harden fully.
Print speed can significantly affect both drying and curing times. When a printer operates at higher speeds, each section of the printed material has less time under the heaters or curing units, which can lead to insufficient drying or curing. This can be particularly problematic with heavy ink loads where more solvent or carrier needs to evaporate to prevent issues like smudging or scratching. Inadequate curing can also lead to the ink not adhering well to the substrate, which compromises the print’s durability and appearance.
Moreover, fast print speeds can sometimes result in the printed material passing through the machine before the inks dry, causing prints to stick to themselves or transfer ink to other parts of the printer, such as rollers or other prints. This can be a significant problem when printing on materials that are rolled up immediately after printing, as is common with large format printers.
Manufacturers often try to mitigate these problems by improving the ink formulas to dry or cure faster, and by enhancing the hardware of the printers with more powerful drying systems or with UV lights for curing. However, these improvements also have their own limitations and can drive up the cost of the printing process.
In summary, while faster print speeds can enhance production throughput, they can also present challenges for drying and curing times in vinyl printing, especially with large format printers. Providing sufficient time for inks to dry and cure is crucial to ensure high-quality, durable prints and to avoid operational issues like ink transfer and material spoilage. As such, striking the right balance between print speed and drying/curing time is essential for a successful printing operation.