Title: Navigating the Challenges of High-Speed Device Operation: Maintenance and Handling Imperatives
Introduction:
In the era of technological acceleration, high-output speed devices are becoming ubiquitously integral to myriad sectors, from manufacturing and automation to computing and transportation. The marvels of modern engineering have pushed the boundaries of how fast machines can operate, but with great velocity comes a heightened responsibility for maintenance and handling. Operating at such rapid rates, these devices can encounter a unique set of challenges that, if unaddressed, may lead to decreased efficiency, premature wear, or even catastrophic failure. This article delves into the critical considerations that must be accounted for to ensure the longevity, reliability, and safety of devices functioning at high-speed regimes.
To begin with, the advent of high-speed operation necessitates a meticulous examination of the device’s design and construction material choices. These foundational aspects will significantly influence the wear characteristics and thermal dynamics underpinning the system’s operation. It is imperative to understand the role of lubrication, which becomes ever more crucial and complex at higher velocities. Selecting the appropriate lubricant, applying it correctly, and maintaining its integrity can substantially extend the life of high-speed components.
The thermal implications of high-speed operation cannot be overstressed. As the device’s moving parts accelerate, friction inevitably rises, leading to increased temperatures that can degrade materials and impact structural integrity. Such thermal stress mandates rigorous monitoring and robust cooling systems to dissipate excessive heat build-up. Additionally, the high inertial forces experienced at fast speeds accentuate the need for precise alignment and balance of the moving parts. Imbalances, even at a minute scale, can manifest as significant vibrations and noise, which over time can lead to wear or failure of components and substantial performance degradation.
Another facet to consider is the effect of high speeds on control systems and feedback mechanisms. Ensuring that control systems are responsive enough to handle the rapid pace and can make adjustments in real-time is pivotal for maintaining the device’s performance. This article will explore these and other maintenance and handling considerations, offering insights into best practices for operating devices at high output speeds securely and sustainably. Through thoughtful analysis and strategic planning, it is possible to harness the benefits of high-velocity operation without sacrificing the equipment’s lifespan or operator safety.
Heat Management and Dissipation
Heat management and dissipation is a critical challenge in the operation of any device that functions at high output speeds. High output speeds typically generate significant amounts of heat due to increased friction and resistance experienced within the moving components of the device. This can lead to a variety of issues, including a reduction in the efficiency of the device, potential damage to its components, and in extreme cases, failure of the device itself.
One of the main considerations for maintaining a device at high output speeds is ensuring that the heat generated is dissipated effectively. This often requires an integrated approach to cooling, which could involve passive methods, like heat sinks and thermal pads, or active methods, such as forced air or liquid cooling systems. The design of these systems must consider not only the amount of heat produced but also how quickly it needs to be removed to maintain optimal operating temperatures.
Components within the device, such as bearings, spindles, and motors, must be able to operate under the stress of high temperatures. Materials with high thermal resistance are often used, and components may be designed to have increased surface area to facilitate heat transfer. In some cases, materials that change phase (such as certain gels or compounds that melt) can absorb substantial amounts of heat in a controlled fashion.
Regular maintenance is essential for effective heat management and dissipation. This includes checking and replacing thermal interface materials, cleaning heat sinks and cooling channels to ensure they are not blocked by debris, and monitoring cooling systems for proper function. Additionally, thermal sensors can play a crucial role in maintaining safe operating temperatures by providing real-time data and enabling an automated shutdown if critical temperatures are exceeded, preventing damage to the device.
In summary, heat management and dissipation are key considerations when operating devices at high output speeds. Maintaining efficiency and longevity of the device requires attention to cooling system design, regular maintenance, and the use of appropriate materials and sensors to manage the thermal load. Failure to properly manage heat can significantly impact the functionality and service life of high-speed devices.
Lubrication and Wear Prevention
Lubrication plays a critical role in the maintenance and longevity of machinery, especially when devices operate at high output speeds. Proper lubrication is essential to prevent wear and tear on moving parts. At high speeds, metal components can come into contact with each other, and without a lubricant to provide a protective barrier, friction can cause significant wear. This can lead to deterioration of parts, increased energy consumption, overheat, and ultimately, machine failure.
High output speeds can exacerbate components’ wear due to the increased frequency of contact interactions between moving parts. When devices are running at such speeds, there is a heightened possibility of lubricant breakdown, caused by the heat generated from the friction. This degradation can reduce the effectiveness of the lubricant, leading to metal-on-metal contact, which increases the risk of premature wear and failure.
Regularly checking and replenishing lubricants, as well as using the correct type of lubricant for the specific machinery and operating conditions, are fundamental practices to ensure smooth operation. In high-speed applications, the selection of lubricants with appropriate viscosity and thermal stability is particularly important to ensure they do not degrade quickly under the operation’s stress.
Maintenance personnel must be vigilant in monitoring the condition of the lubricant, looking for signs of contamination, such as the presence of metal particles or changes in color or consistency. This might indicate that the lubricant is no longer providing adequate protection and needs to be replaced. Implementing a scheduled maintenance program that includes regular lubrication intervals can help maintain machinery efficiency, prolong equipment life, and prevent costly unplanned downtime.
Furthermore, from a handling perspective, proper lubrication ensures that high-speed machinery operates within its specified parameters, reducing the risk of overloading or overheating. The use of automated lubrication systems can provide continuous and consistent lubrication, which is particularly beneficial for equipment that operates 24/7 or in environments where manual lubrication is challenging.
High output speeds also necessitate that machines are well-aligned and balanced since even minor misalignments can introduce additional stresses that can also lead to more rapid wear. Therefore, precision alignment and balancing are integral alongside diligent lubrication practices to ensure that machinery can operate at high speeds without compromising performance or longevity.
Vibration Control and Damping
Vibration control and damping are critical factors in the design and operation of any mechanical system that operates at high output speeds. Efficient vibration control ensures the longevity of a device, preserves its structural integrity, and enhances performance. Damping, which is the process of reducing or otherwise controlling vibrations, plays a significant role in minimizing the transmission of unwanted vibrations to critical parts which could lead to a decrease in performance or even system failure.
When a device operates at high output speeds, the rotational or reciprocating components can generate considerable vibration due to dynamic forces. If these vibrations are not adequately controlled, they can cause mechanical stress, leading to premature wear and potential failure of components. It is not only the moving parts of the device that are affected; vibration can also be transferred through the device to its mountings or supporting structure, which could lead to noise issues, and in worst-case scenarios, structural damage.
The maintenance and handling considerations for devices at high output speeds start even before actual operation, with the design and installation phase requiring precise engineering to ensure proper balance and alignment of components. Regular maintenance checks are essential for identifying wear and any changes in vibration patterns that might indicate an underlying problem.
Balancing of rotating parts and alignment correction of components can reduce vibration levels significantly. In some instances, installing vibration isolators or dampers to absorb and reduce transmitted forces can improve the system’s lifespan and performance. These isolators could be made of various materials like rubber, springs or specialized polymers that are chosen based on the frequency and amplitude of the vibrations to be dampened.
Predictive maintenance techniques, such as vibration analysis, can be employed to monitor the condition of the machinery in real-time. By using sensors and advanced analytical software, it is possible to detect changes in vibration patterns and address potential issues before they become significant problems.
In summary, efficient vibration control and damping are indispensable in high-speed devices to avoid negative impacts on performance and longevity. Ongoing efforts in maintenance, such as regular inspection, balancing, correct installation, and the use of predictive analytics, are vital in handling these systems to ensure their continued reliable operation.
Structural Integrity and Material Fatigue
Structural integrity and material fatigue are crucial considerations for the design and maintenance of machines and structures that operate at high output speeds. The repeated application of loads and the resulting stress cycles can lead to material fatigue, which occurs when materials begin to fail after prolonged periods of stress and strain. High-speed operation accelerates this process due to the increased number of cycles a component experiences over a given period.
Structural integrity refers to the ability of a component or structure to withstand the intended loads without failure. This includes coping with the static loads, the occasional unexpected overloads, and the dynamic loads associated with high-speed operations. A systematic approach to ensure structural integrity involves selecting appropriate materials and designs that take into account the fatigue life of the components. Engineers use various methods, such as finite element analysis, to predict how structures will respond to these stresses and to optimize designs.
To mitigate these issues, regular inspections and maintenance are critical. Non-destructive testing techniques, like ultrasonic testing, radiography, and magnetic particle inspections, help in detecting early signs of fatigue and structural weakness without causing damage. Additionally, employing high-quality materials, utilizing appropriate heat-treating processes to enhance strength, and avoiding sharp corners in design to reduce stress concentrations can also improve fatigue life.
Furthermore, the introduction of high output speeds means that small imperfections or defects in materials can propagate more quickly into critical failures. Therefore, manufacturers often implement conservative design margins and robust quality control measures to prevent defects from occurring in the initial stages of production.
Considering these aspects is essential to maintain a high level of reliability and safety in any high-speed operational environment, such as in aerospace, automotive, and industrial machinery sectors. As technology continues to push the limits of material capabilities, ongoing research in material sciences and fatigue analysis remains paramount to advancing the durability and lifespan of high-performance components and machines.
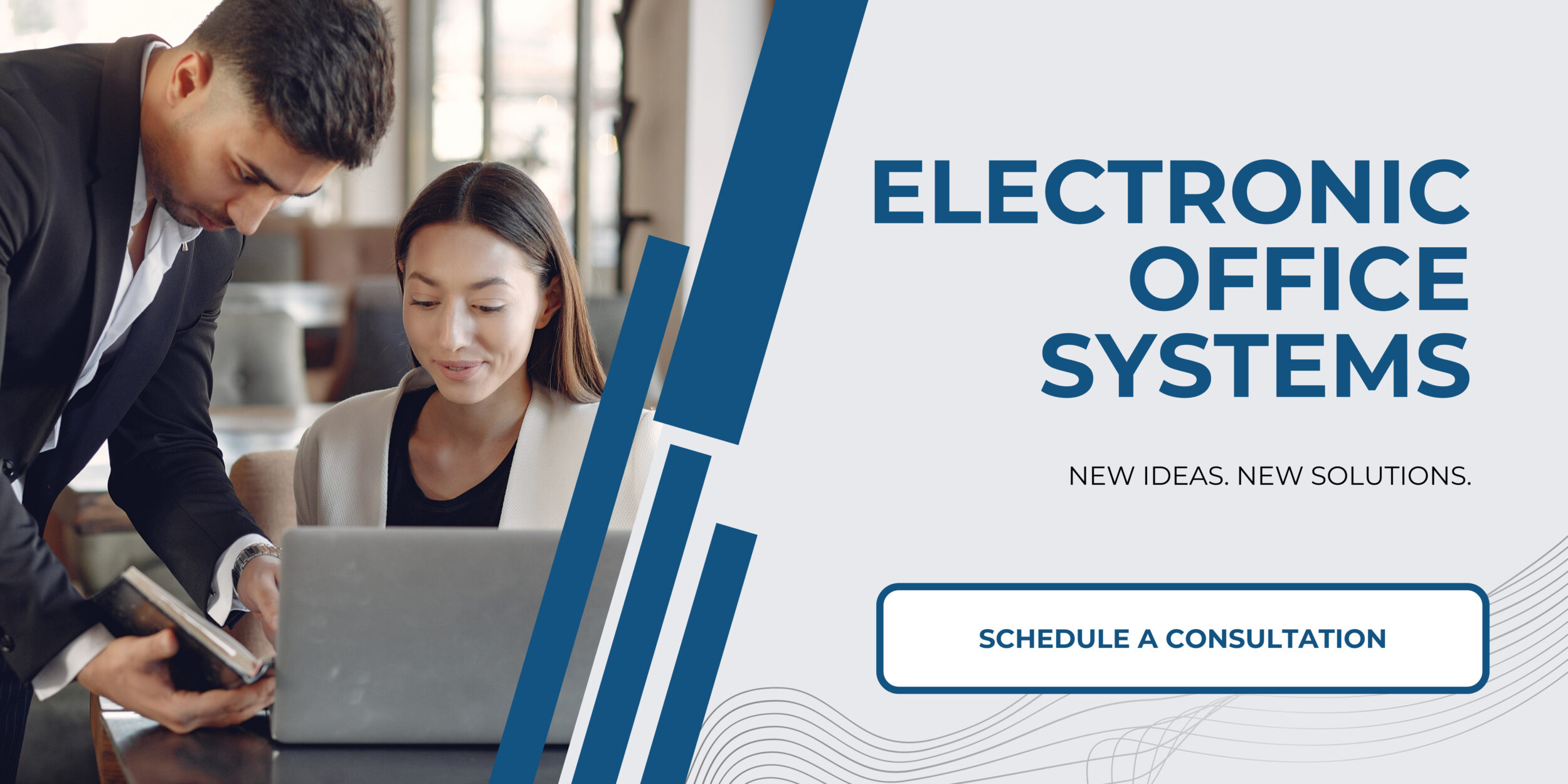
Calibration and Precision Alignment
Calibration and precision alignment are crucial aspects of maintaining and operating any high-performance device or machinery. When equipment operates at high output speeds, these factors become even more significant due to the increased risk of deviation from specified performance parameters, which can affect the quality of output and longevity of the device.
**Calibration** refers to the process of configuring a device to provide a result for a sample within an acceptable range. Ensuring that equipment is properly calibrated is essential because even minor discrepancies can lead to significant deviations over time or when the device is operated continuously at high speeds. Calibration involves adjusting the precision of the equipment to match a known standard or measurement. For instance, a high-speed printer must frequently be calibrated to ensure accurate color representation and print alignment, especially when producing large volumes of high-resolution images.
**Precision alignment** is similarly critical, as it ensures that all parts of a machine are aligned and work in conjunction with one another efficiently and effectively. In high-speed operations, misalignment can lead to increased wear and tear, which can cause premature failure of components. It may also result in product defects, reduced accuracy, and a decrease in overall system performance. Precision alignment is particularly important in sectors like manufacturing, where robotic arms or conveyor belts must synchronize perfectly to maintain a seamless production line.
When considering the maintenance and handling of devices operating at high speeds, one must take into account several factors:
1. **Regular Inspections:** Frequent and thorough inspections help identify calibration or alignment issues before they lead to significant problems. Regular checks enable maintenance personnel to make minor adjustments in time.
2. **Use of High-Quality Components:** Higher-quality parts often have better tolerances and are manufactured to stand up to the stress of continuous high-speed operation, which is essential for maintaining calibration and alignment over longer periods.
3. **Environmental Stability:** The operating environment can significantly affect calibration and alignment. Temperature fluctuations, humidity, and dust can interfere with sensitive components. Therefore, maintaining a controlled environment can help in reducing the need for recalibration and realignment.
4. **Skilled Personnel:** Properly calibrating and aligning high-speed machinery requires skilled technicians who understand the intricacies of the equipment. Their expertise ensures that adjustments are made accurately and that the equipment operates at its best.
5. **Routine Maintenance Schedule:** Implementing a maintenance schedule is vital. Regular maintenance not only ensures calibration and alignment are consistently checked and corrected if necessary, but also that other factors impacting these aspects, such as wear and tear or lubrication, are addressed.
6. **Monitoring Systems:** Advanced monitoring systems and sensors can provide real-time data on the performance of high-speed devices, making it easier to determine when recalibration or realignment is needed.
Operating equipment at high output speeds demands a proactive approach to maintenance, and meticulous attention to calibration and precision alignment is a significant part of this. Those responsible for the operation of such devices must understand the importance of these processes and be vigilant in maintaining them to avoid operational inefficiencies, downtime, and the costs associated with repairs or substandard products.