In any industry reliant on machinery for operations, understanding the impact of cool down time on efficiency and throughput is crucial. This is no different in the world of shredding operations, where the balance between maintaining high performance levels and safeguarding equipment longevity is a constant act. The cool-down time of shredding equipment significantly influences not only the operating capacity of the machines but also their lifespan and overall performance. Cool down time, often overlooked or undervalued, plays a pivotal role in achieving operational excellence. This article aims to dissect the relation and impact of cool down time on the efficiency and throughput of a shredding operation.
Shredding operations, regardless of the materials being processed, inherently involve a lot of friction, and consequently, heat generation. This, if not controlled, can lead to equipment damage, decreased efficiency, and ultimately a reduction in throughput. It is here that cool down periods step into play, allowing the machinery to recover, resume optimal functioning, and enhance overall productivity.
The critical influence of cool down time on the shredded end-product quality, the wear and tear of blades, and energy consumption patterns are paramount aspects that guide the operation schedules in a shredding plant. A comprehensive understanding of these factors can empower organizations to plan their shredding operations more efficiently, concurrently achieving high production rates and long-term equipment sustainability.
However, the mapping out and application of these cool down periods within the operational schedule is not a straightforward process. It necessitates an in-depth awareness of the specific needs of the machinery, the materials being shredded, and the operational objectives at play. This article will provide an in-depth exploration of how cool down time affects the efficiency and throughput of shredding operations, presenting insights backed by industry experience and technical knowledge.
By throwing light on this subject, we hope to highlight the importance of optimal machinery utilization in shredding operations, with a special focus on the role and implications of effective cool-down practices. By the end of this article, you will have a greater understanding of the complex dynamics that define the efficiency and throughput of a shredding operation.
The Role of Cool Down Time in Prolonging Shredder Lifespan
The role of cool down time in preserving the lifespan of a shredder cannot be over-emphasized. A shredder, like any other mechanical or electronic device, produces a significant amount of heat when running. Combined with the friction created by the shredding process, this heat causes strain upon the machine’s internal components. Over time, continual heat and friction can degrade these parts, leading to decreased performance, more frequent breakdowns, and ultimately, a shorter lifespan for the shredder.
Cool down periods provide a necessary opportunity for the shredder to reduce these thermal stresses, sparing its sensitive parts from heat-related damages. Without regularly timed breaks, the machine cannot recover from the accumulated stress, resulting in premature wear and tear.
In terms of efficiency and throughput for a shredding operation, cool down time plays a critical role. When a shredder overheats, it automatically shuts down for protection. This can lead to unexpected delays in operations. By incorporating cool down periods into the operation schedule, the shredder will not reach this overheat threshold and shut down, leading to more consistent and predictable production times.
However, cool down time should be strategically timed. It is a trade-off between preserving the machine’s health and optimizing operational productivity. Extensive cool down times can decrease the throughput by leaving the machine idle for extended periods. Therefore, achieving a balance between adequate cool down time and maximizing shredding productivity is crucial. Cool down times ideally should be scheduled during non-peak hours or can coincide with other necessary operational tasks. This strategy not only prolongs the shredder’s lifespan but also maintains a peak operational efficiency.
Impact of Cool Down Time on Shredding Speed and Efficiency
The impact of cool down time on shredding speed and efficiency is significant and should not be underestimated. In the context of a shredding operation, cool down time essentially refers to the operational pauses needed to allow the shredding equipment to stabilize its internal temperature following periods of intense or prolonged activity. The necessity for these breaks is typically prompted by the heat generated during the shredding process. Overheating is a common issue in shredding operations and is known to contribute to the depreciation of machine operation, leading to less efficient performance and a shortened lifespan.
The rate of shredding, thus the throughput, is directly influenced by the duration of these cool down intervals. The more frequent or longer these pauses, the fewer materials can be processed in a given timeframe, resulting in reduced shredding speed and output. For instance, if a shredder requires a 15-minute cool down after every 45 minutes of operation, up to 25% of its operational timeframe is non-productive, affecting the overall efficiency.
The cool down time can also impact the overall energy efficiency of the shredding operation. When the shredding equipment is required to restart after each pause, it can lead to higher energy consumption. Increased energy use not only inflates operational costs but may also contribute to a larger carbon footprint, making the process less environmentally friendly.
From these points, it should be apparent that managing cool down time is an integral aspect of optimizing shredding operations. Proper maintenance, appropriate scheduling, and using quality equipment whose thermal management is efficient, can significantly decrease the frequency and duration of necessary cool down periods, aiding to maintain shredding speed, increase throughput, and potentially decrease operational costs.
The Relationship Between Cool Down Time and Shredder Maintenance
The relationship between cool down time and shredder maintenance can be seen as reciprocal. Cool down periods are vital in maintaining the efficiency of shredders, especially in prolonged shredding operations. Overheating can cause a variety of issues to shredding machines, including mechanical failures, reduced effectiveness, and in some cases, the complete breakdown of the shredder.
Cool down times, typically recommended in the shredder’s operation manual, allow for both the engine and blades of the shredder to rest. This rest period protects the machine from overheating, avoids unnecessary wear and tear of the shredding components, and prolongs the life of the shredder. Regularly following the advised cool down time can help reduce the frequency and extent of required maintenance services, leading to a decrease in maintenance-related costs and a boost in the shredder’s overall durability and performance over time.
However, the implementation of these cool down periods can hamper the throughput of a shredding operation. A shredding operation’s efficiency is gauged by the number of items it can shred in a given amount of time. When a shredder is forced to pause for cool down, it interrupts the process, leading to a decrease in the operation’s total output.
That said, while a cool down period may reduce the shredder’s immediate throughput temporarily, it significantly augments the shredder’s longevity and serviceable life. An understanding and proper management of cool down times can, therefore, result in higher throughput over the shredder’s overall operational lifespan. Thus, regular maintenance and adhering to recommended cool down times can strike a balance between maintaining operational efficiency and ensuring the long-term health and productivity of the shredder.
Effect of Cool Down Time on Energy Consumption in Shredding Operations
Cool down time, a crucial aspect to consider in shredding operations, is directly related to energy consumption. The concept might seem counterintuitive at first: why should a machine at rest consume more energy? The answer lies in the nuances of machine operation and performance efficiency.
Shredding operations generate substantial heat, especially during continuous operation. To prevent damage to machine parts and maintain efficient functioning, a built-in cool down period is essential. It’s during this downtime, the shredder is allowed to cool down, protecting components from heat-induced wear and breakdown.
However, there is an energy cost involved. If a shredder is in constant high-heat operation, followed by cool down periods, this sudden temperature fluctuation syndrome can lead to inefficient usage of energy. In other words, when the shredder restarts operation after a cool down period, it will have to reach a certain operational temperature, consuming more energy than if the temperature had remained steady at a lower level.
Cool down periods can be optimized to enhance shredding operation efficiency and reduce energy consumption. For instance, implementing a strategy of timed breaks between operations, rather than continuous shredding followed by an abrupt cool down can promote balanced energy usage. It reduces the intensity of fluctuation in operational temperatures, maintaining the machinery at a more stable, and efficient, level.
The optimization of cool down time can then have a significant impact on energy consumption in shredding operations. It encompasses not only reduction in energy usage but also increases the overall productivity and lifespan of the equipment. Understanding the effect of cool down time on energy consumption is thus critical to enhancing the overall efficiency and throughput of a shredding operation.
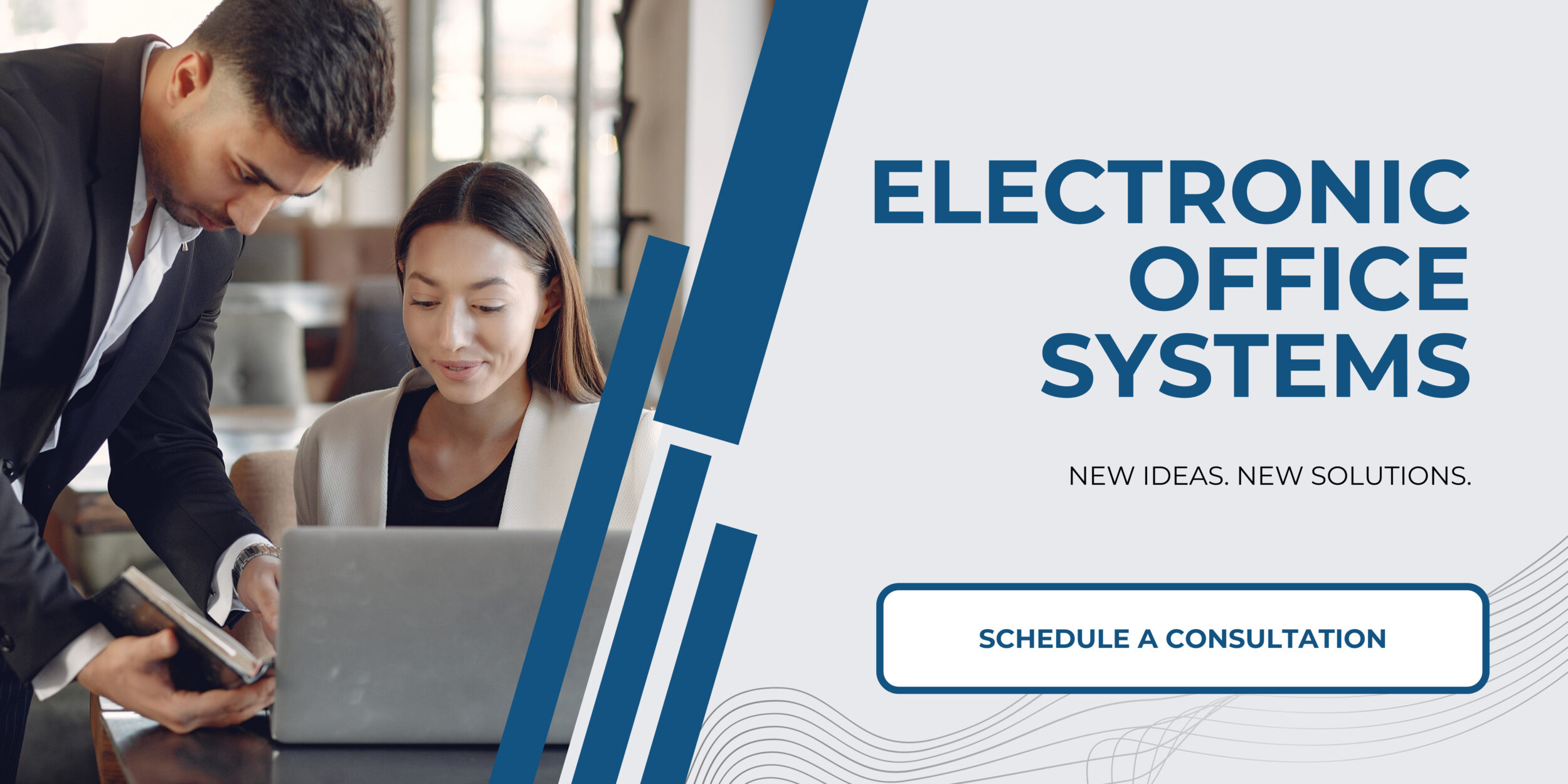
Analysis of Downtime Productivity Loss due to Shredder Cool Down Periods
The study of downtime productivity loss due to shredder cool down periods is an essential aspect of understanding the dynamics of any shredding operation. This involves understanding the intricate process of how shredders function, the necessity for cooling down periods and the impact of these periods on the overall productivity of a shredding operation.
Shredders, particularly industrial ones, are designed to handle mass shredding duties which generate heat due to consistent friction. This, over time, raises the machine’s internal temperature, leading to a point where a cool down period is necessary to prevent overheating which could potentially damage the machine and decrease its lifespan. However, these cool down periods inevitably lead to downtime, which in turn impacts productivity levels.
When considering the impact that cool down time has on the efficiency and throughput of a shredding operation, it is important to remember a few key points. Firstly, the cool down time may result in interruptions to the workflow, affecting the rate at which materials can be processed. This is particularly crucial in high-demand settings where the requirement for shredded materials is constant. Extended cool down periods can significantly limit the amount of material that a shredder can process in a given time frame, thereby reducing its throughput.
Secondly, cool down periods can impact the efficiency of a shredding operation in terms of energy usage. Longer periods of inactive time during operations mean that the shredder is using power without actually processing material. This can lead to higher energy costs in relation to the volume of material processed, thus reducing the operational efficiency.
It’s noteworthy to mention that strategic scheduling of cool down periods can mitigate some of these negative impacts. If planned correctly, these periods can coincide with naturally occurring lulls in the workflow, minimizing disruption and productivity loss. As a result, while the cool down period does indeed contribute to downtime productivity loss, it is not entirely detrimental when properly managed.
In conclusion, cool down periods are a necessary part of any shredding operation to ensure the longevity of the machinery. However, their impact on efficiency and throughput must be carefully considered and managed to minimize productivity loss.