In the modern office setting, a shredder is an essential tool for keeping sensitive information safe. With the rise of digital documents, data security is of paramount importance. As such, shredders have become necessary for preventing unauthorized access to confidential documents. However, the inclusion of safety sensors may significantly increase the cost of a shredder. This article will explore the cost implications of adding safety sensors to a shredder, and the advantages and disadvantages of doing so.
The addition of safety sensors to a shredder can provide several benefits, from ensuring the paper is shredded properly to preventing accidental injury. Safety sensors are designed to detect when paper is inserted and to stop the shredding process when hands or fingers are too close to the opening. This can reduce the risk of injury or paper jams caused by incorrect paper insertion. Additionally, the sensors can detect when the shredder is overloaded and shut off the motor to protect it from damage.
However, the inclusion of safety sensors does come with a cost. Shredders with safety sensors are usually more expensive than those without them, as the sensors require additional components and labor to install. Furthermore, the sensors may also require regular maintenance and upkeep, resulting in further costs. Lastly, the inclusion of safety sensors may also reduce the shredding speed and efficiency, potentially resulting in longer shredding times and higher operational costs.
Overall, while the inclusion of safety sensors may result in higher upfront and operational costs, the potential benefits may outweigh the costs. By understanding the cost implications of adding safety sensors to a shredder, businesses can make an informed decision as to whether or not this is a worthwhile investment.
The Cost of Safety Sensors in the Market
The cost of safety sensors in the market can vary greatly, depending on the type of sensor, its size, and its intended application. Common types of safety sensors include motion, light, temperature, pressure, and proximity sensors. Depending on the application, the cost of these sensors could range from a few dollars to several hundred dollars. Additionally, the cost of safety sensors can also vary depending on the type of technology used in the manufacturing process. For example, some sensors may use more expensive components or require more advanced manufacturing techniques than others, resulting in higher costs.
When it comes to the cost of safety sensors for shredders, many manufacturers opt to use motion sensors. Motion sensors are designed to detect any movement within a defined area and are often used to trigger the shredder when a hand or object is placed too close to the blades. The cost of motion sensors will depend on the size and type of sensor, but they are typically relatively inexpensive and can be bought for a few dollars each.
The inclusion of safety sensors in shredders does significantly increase the cost of the machine. This is because the sensors need to be integrated into the machine’s design and the manufacturer will need to use more expensive components and materials. Additionally, the manufacturer will need to devote more time and resources to testing and ensuring that the sensors are working properly. All of these factors can significantly increase the cost of a shredder, but it is often a worthwhile investment since it can help prevent serious injuries or damage to the machine.
In conclusion, the inclusion of safety sensors in shredders does significantly increase the cost of the machine. This is because manufacturers need to use more expensive components, devote more time to testing, and integrate the sensors into the machine’s design. However, this cost can be a worthwhile investment since it can help protect users from injury or damage to the machine.
The Impact of Safety Sensors on Shredder Manufacturing Costs
The inclusion of safety sensors in shredders can have an impact on the manufacturing costs that shredder producers need to consider. Safety sensors are designed to prevent accidents, such as when a person’s hand is too close to the machine. There are several types of safety sensors available in the market, with different levels of complexity and cost. As such, the cost of incorporating safety sensors into shredders can vary greatly depending on the type and number of sensors chosen. Additionally, shredder manufacturers must also factor in the cost of researching and installing the sensors.
The impact of safety sensors on the cost of a shredder can also depend on the particular shredder model. For example, higher-end shredders may include more features and safety sensors than basic shredders. This means that the cost of production for the more advanced shredders may be higher than for the simpler models, even with the inclusion of safety sensors. As such, the cost of producing shredders with safety sensors may vary significantly from model to model.
Overall, the inclusion of safety sensors does significantly increase the cost of a shredder. However, this cost can be offset by the benefits of increased safety and reliability, as well as the potential reduction in the cost of repairs and maintenance. Therefore, it is important for shredder manufacturers to consider the cost-benefit tradeoff when determining whether or not to include safety sensors in their shredders.
Comparison of Shredder Prices: With and Without Safety Sensors
The cost of safety sensors in the market affects the price of shredders that include safety sensors. Depending on the manufacturer, the cost of shredders with safety sensors can be significantly higher than shredders without them. As safety sensors become more commonplace, the cost of including them in shredders has decreased, but they can still be a more expensive option than shredders without them. When comparing prices of shredders with and without safety sensors, it is important to consider the long-term cost savings associated with having the safety sensors included in the product.
Safety sensors can be a cost-effective solution for shredder manufacturers, as they can help reduce potential repair and maintenance costs in the long run. By detecting potential safety hazards, such as paper jams or overheating, the safety sensors can alert the user and prevent further damage to the shredder. In addition, the safety sensors can help shredder manufacturers meet current safety requirements, which can reduce the risk of liability costs associated with potential accidents or injuries.
When considering the cost of safety sensors, it is important to weigh the initial cost with the potential benefits. While safety sensors may initially increase the cost of a shredder, they can provide long-term cost savings in the form of reduced repair and maintenance costs, as well as help shredder manufacturers meet current safety standards. With careful consideration of the cost of safety sensors and the potential benefits, shredder manufacturers can make an informed decision about whether or not to include safety sensors in their products.
Cost-benefit Analysis: Safety Sensors vs Shredder Repair and Maintenance
Cost-benefit analysis is an important part of any decision making process, especially when it comes to safety-related decisions. An analysis of the cost-benefit of installing safety sensors in shredders versus repair and maintenance costs can help manufacturers and consumers make a more informed decision. The cost of safety sensors in the market can vary widely, depending on the type and quality of the sensors. The impact on shredder manufacturing costs depends on the complexity of the safety sensors, as well as the budget of the manufacturer.
When comparing shredder prices with and without safety sensors, it is important to consider the long-term savings associated with the safety sensors, such as reduced repair and maintenance costs. Safety sensors can help to prevent costly repairs and downtime, as well as avoid potential hazards and injuries. In addition, the cost of safety sensors is often much less than the cost of potential damages associated with an incident or accident. A cost-benefit analysis can help to identify the best value for the money in terms of safety sensors versus repair and maintenance.
Overall, the inclusion of safety sensors in shredders does increase the cost of the shredder, but the cost-benefit analysis should be done to determine if the additional cost is worth it. The long-term savings associated with safety sensors can more than make up for the initial cost. Ultimately, the decision of whether or not to include safety sensors depends on the individual shredder manufacturer’s budget and risk tolerance.
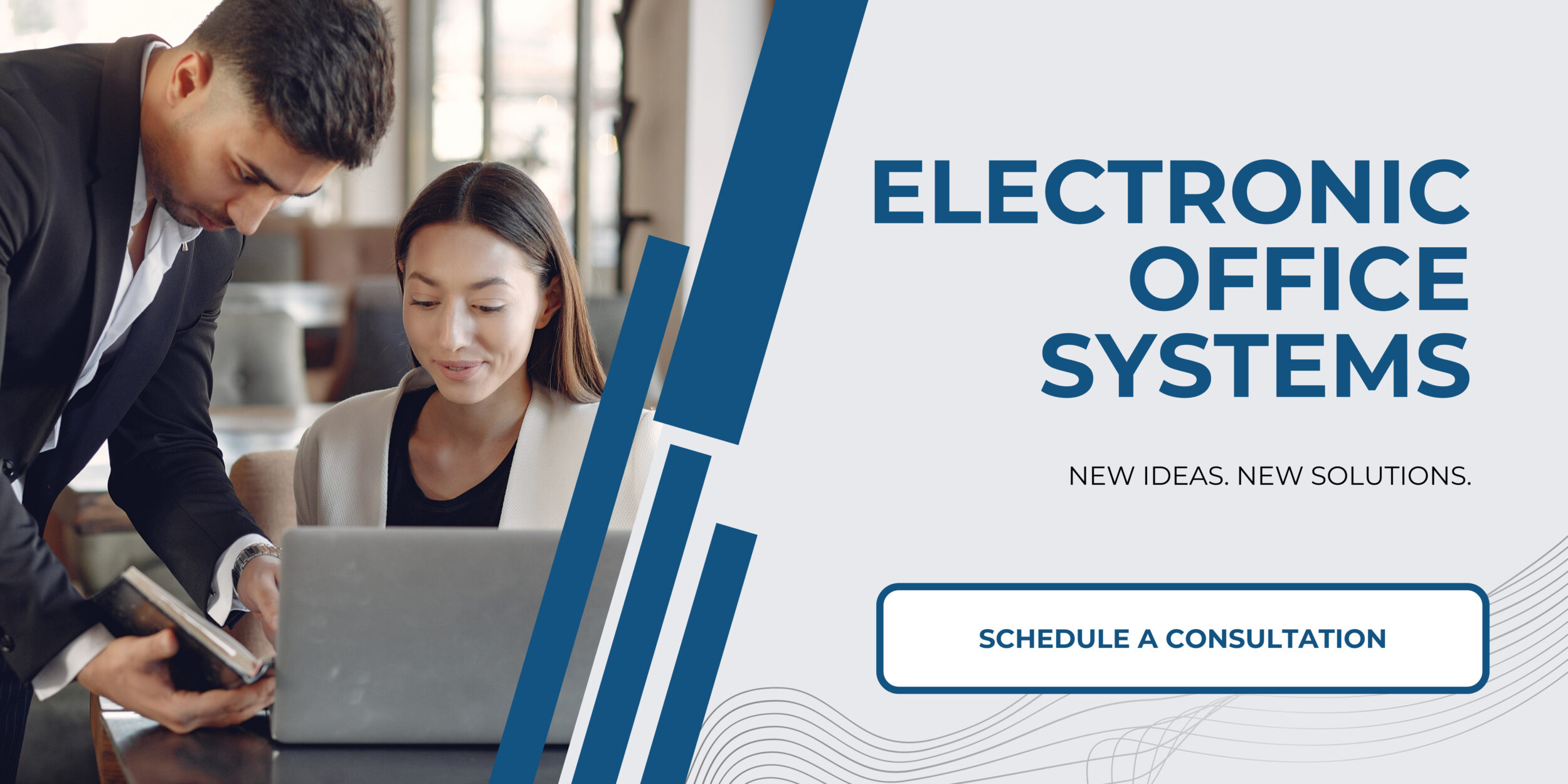
Cost Strategies for Shredder Manufacturers Implementing Safety Sensors
The inclusion of safety sensors in shredders is an important safety feature that all shredder manufacturers should consider. For shredder manufacturers, the cost of safety sensors can be significant, depending on the type and quantity of sensors used in the shredder. As such, cost strategies must be implemented to ensure that the inclusion of safety sensors does not significantly increase the cost of the shredder. One way to reduce the cost of safety sensors is to purchase them in bulk from a reliable supplier. Additionally, shredder manufacturers can take advantage of new technologies such as machine learning and automation to reduce the cost of safety sensors. This can be done by using data from existing shredders to create a predictive model that can be used to identify potential safety hazards.
Another cost strategy is to explore alternative safety sensor technologies that may be more cost-effective than traditional safety sensors. For example, some shredder manufacturers have begun to explore the use of pressure-sensing technology to detect potential safety hazards. This technology is often more cost-effective than traditional safety sensors and can be used to detect a wide variety of safety hazards.
Finally, shredder manufacturers can also explore alternative methods of integrating safety sensors into their shredders. For example, some shredder manufacturers have begun to explore the use of 3D printing to integrate safety sensors directly into the shredder’s design. This can result in a more cost-effective solution and can also reduce the cost of safety sensors.
Overall, the inclusion of safety sensors in shredders can significantly increase the cost of the shredder. However, with the right strategies in place, shredder manufacturers can reduce the cost of safety sensors and ensure that the inclusion of safety sensors does not significantly increase the cost of the shredder.