Maintenance tasks are a routine part of any business or organization, and keeping them up-to-date and in good condition is essential for efficiency and safety. However, a common question is, how frequently should these maintenance tasks, such as cleaning or calibration, be performed? This is an important factor to consider when setting up a maintenance plan, as too little maintenance can lead to unexpected breakdowns or malfunctions, while too much can be inefficient and costly. It is therefore important to determine how often maintenance should be undertaken to maximize both efficiency and safety.
This article will explore the various factors to consider when determining how often maintenance tasks should be performed. Firstly, the type of maintenance task will be examined, followed by the environment and usage of the equipment or facility. Additionally, the importance of regularly reviewing the maintenance plan and the potential cost savings will also be discussed. Finally, a conclusion will be drawn on the optimal frequency of maintenance tasks.
By the end of this article, readers should have a better understanding of how frequently maintenance tasks should be performed in order to ensure the best possible results for their organization. With this information, readers can develop an effective maintenance plan that maximizes efficiency and safety while minimizing costs, ensuring their organization runs as smoothly and safely as possible.
Identifying Critical Maintenance Tasks
Identifying critical maintenance tasks is a critical step in any successful equipment maintenance plan. It is important to determine which tasks are essential for proper functioning of the equipment and which tasks can be safely omitted or reduced in frequency. To identify the necessary tasks, the user manual and manufacturer recommendations should be consulted, as well as any industry standards. Additionally, the current condition of the equipment should be assessed, as well as the environment in which it is being used. Once the necessary tasks have been identified, they should be documented for future reference.
Determining the appropriate frequency of maintenance tasks is a key part of any successful equipment maintenance plan. Generally, maintenance tasks should be performed according to the manufacturer’s recommendations, as well as any applicable industry standards. Additionally, the environment in which the equipment is being used should be taken into account when determining the appropriate frequency. For example, an equipment operating in a dusty environment may require more frequent cleaning than one operating in a clean environment.
The impact of regular maintenance on equipment efficiency is significant. Regular maintenance can keep equipment running at peak efficiency, extending its lifespan and reducing the need for costly repairs. Additionally, regularly scheduled maintenance can help identify potential problems before they become serious, allowing for timely repairs and avoiding costly downtime.
How frequently should maintenance tasks, such as cleaning or calibration, be performed? Maintenance tasks should generally be performed according to the manufacturer’s recommendations and industry standards. Additionally, the environment in which the equipment is being used should be taken into account when determining the appropriate frequency. Factors such as the amount of dust or debris in the environment, or the amount of wear and tear on the equipment should be considered when determining the frequency of maintenance tasks.
Determining the Appropriate Frequency of Maintenance Tasks
Maintenance tasks such as cleaning or calibration must be performed regularly in order to ensure that equipment is operating efficiently. The appropriate frequency of these tasks will depend on a variety of factors, including the type of equipment, its operating environment, and the manufacturer’s recommendations.
When determining the frequency of maintenance tasks, it is important to consider both the short-term and long-term effects of the maintenance schedule. For example, if the maintenance schedule is too frequent it can increase the cost of labor and materials, while if it is too infrequent it can lead to equipment malfunctions and decreased efficiency. It is therefore important to consider the specific needs of each piece of equipment when determining the appropriate maintenance schedule.
Manufacturer recommendations are an important factor in determining the frequency of maintenance tasks. Many manufacturers provide detailed instructions for maintenance and repair tasks in their user manuals, and it is important to follow these instructions to ensure the safety and efficiency of the equipment. For example, if the manufacturer recommends a specific type of lubricant for a certain type of machine, it is important to use this lubricant to ensure that the machine is operating efficiently and safely.
The frequency of maintenance tasks should also be adjusted over time to reflect the changing needs of the equipment and its operating environment. As the equipment ages and its operating environment changes, the frequency of maintenance tasks may need to be adjusted. Regular monitoring and adaptation of the maintenance schedule is important in order to ensure that the equipment is functioning properly and efficiently.
In summary, determining the appropriate frequency of maintenance tasks is an important part of ensuring the efficiency and safety of equipment. It is important to consider the type of equipment, its operating environment, manufacturer recommendations and the changing needs of the equipment when determining the frequency of maintenance tasks. Regular monitoring and adaptation of the maintenance schedule is also important in order to ensure that the equipment is functioning properly and efficiently.
The Impact of Regular Maintenance on Equipment Efficiency
Regular maintenance of equipment is essential for preserving its efficiency and functionality. Without regular maintenance, machines can start to break down, become less efficient, and require costly repairs. This is especially true if the equipment is used in a demanding environment or is exposed to harsh conditions. For example, a machine used in a factory may require regular cleaning and lubrication, while outdoor equipment may need better protection from the elements. By performing regular maintenance, a company can ensure that their equipment remains in top condition and continues to operate at peak efficiency.
How frequently should maintenance tasks, such as cleaning or calibration, be performed? The frequency of maintenance tasks depends on several factors, including the type of equipment, how often it is used, and the environment in which it is used. Generally speaking, regular inspections and maintenance should be conducted on a monthly, quarterly, or semi-annual basis. In some cases, such as with highly sensitive equipment, daily maintenance may be required. User manuals and manufacturer recommendations can also provide more detailed guidance on the regular maintenance required for specific types of equipment.
The Role of User Manuals and Manufacturer Recommendations
The role of user manuals and manufacturer recommendations can be an important factor in determining how frequently maintenance tasks should be performed. User manuals provide useful information on how frequently maintenance tasks should be done, as well as on the type of maintenance needed. Manufacturer recommendations are also important because they will often provide additional information on the best practices for maintenance. This can be useful in helping to ensure that the maintenance tasks are done properly and in a timely manner. For example, a manufacturer may recommend that certain components of a machine be cleaned every three months, or that the oil in an engine be changed every six months. This type of information can be helpful in ensuring that the maintenance tasks are done correctly and in a timely manner.
In addition, user manuals and manufacturer recommendations can also provide information on the best practices for calibrating equipment. Calibrating equipment is important for ensuring that the equipment is working correctly and that it is providing accurate readings. The user manuals and manufacturer recommendations can provide information on the best practices for calibrating the equipment, such as what type of calibration is required and how often it should be done. This can help to ensure that the calibration is done properly and in a timely manner.
Overall, user manuals and manufacturer recommendations can be very useful in determining how frequently maintenance tasks should be performed. They can provide important information on the best practices for performing maintenance tasks and on the best practices for calibrating equipment. This can help to ensure that the maintenance tasks are done properly and in a timely manner.
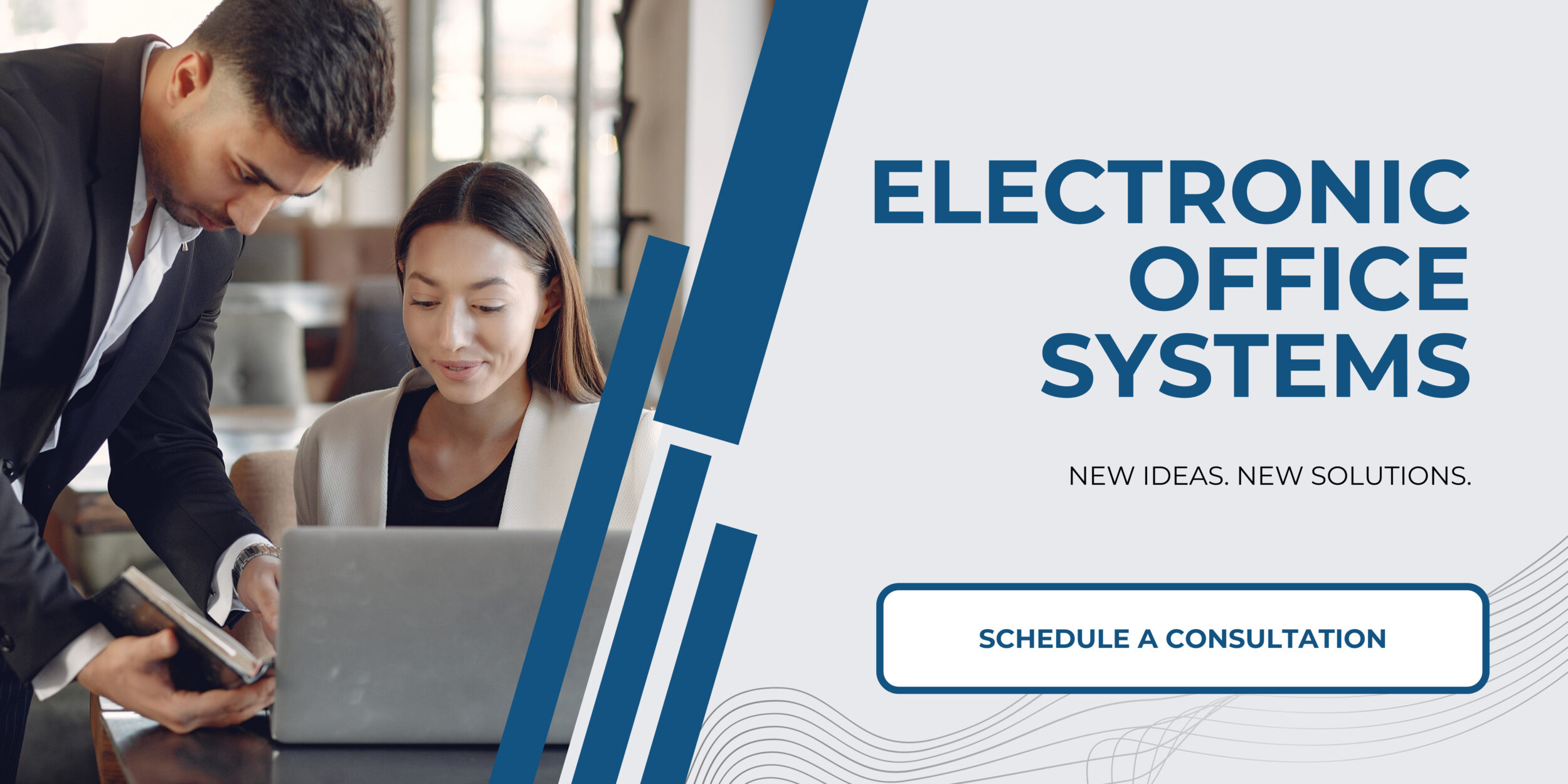
Monitoring and Adapting Maintenance Schedules
Monitoring and adapting maintenance schedules is an important part of any successful maintenance program. It is essential to track and document the performance of the equipment to ensure that it is running properly and that any potential issues are identified quickly and addressed. Monitoring the maintenance schedule also allows for a more accurate assessment of the performance of the equipment and can help to identify areas of potential improvement.
The frequency of maintenance tasks needs to be determined based on the type of equipment, its usage, and the conditions it is being used in. Different pieces of equipment may require different levels of maintenance and it is important to monitor the schedules to ensure that all maintenance tasks are completed as required. Regular maintenance will help to ensure that the equipment runs as efficiently as possible and that any potential problems are identified and addressed quickly.
When it comes to determining the frequency of maintenance tasks, it is important to consider the manufacturer’s recommendations as well as the user manual for the equipment. These documents will provide information on the recommended frequency of maintenance tasks and can help to ensure that the equipment is kept in optimum condition. In addition, it is important to monitor the performance of the equipment and adjust the maintenance schedule accordingly. If the equipment is being used more frequently, it may require more frequent maintenance tasks. Similarly, if the equipment is not being used as often, it may require less frequent maintenance tasks.
In conclusion, monitoring and adapting maintenance schedules is essential for any successful maintenance program. It is important to consider the manufacturer’s recommendations as well as the user manual for the equipment when determining the frequency of maintenance tasks. Additionally, it is important to monitor the performance of the equipment and adjust the maintenance schedule accordingly to ensure that the equipment is kept in optimum condition.