UV-curable inks are a unique type of ink used for large format printing. They are a specialized ink that allow for very vibrant, long-lasting prints that require little maintenance. With this type of ink, the printer does not need to use a heat press or other processes to cure the ink. Instead, it cures when exposed to UV light.
Large format printing is used for many different applications, such as wall graphics, vehicle wraps, trade show displays, and even banners. For these applications, the substrate or material used to print on is as important as the ink itself. For UV-curable inks, the substrate is an especially important factor, as the proper substrate can improve the quality and durability of the print.
Due to the nature of UV-curable inks, certain substrates are more suitable than others. This article will explore what types of materials are best suited for UV-curable ink in large format printing. By understanding what substrates work best with UV-curable inks, you can ensure that you get the highest quality prints possible. We will look at the different types of substrates, how they affect the printing process, and the benefits of using them with UV-curable ink.
Compatibility of Different Material Types with UV-Curable Ink
UV-curable ink is a type of ink used in large format printing that cures almost immediately upon exposure to ultraviolet (UV) light. This type of ink is ideal for printing on various substrates, as it dries quickly and produces sharp images with a high level of detail. However, it is important to note that the compatibility of different materials with UV-curable ink can vary greatly depending on the type of substrate and the properties of the ink. In general, materials such as plastics, metals, wood, composites, and textiles are all suitable for UV-curable ink.
When it comes to plastic substrates, polystyrene, polycarbonate, and acrylic are all suitable for UV-curable ink. These materials are especially good for outdoor applications as they are resistant to UV radiation and are highly durable. Additionally, PVC and PETG are both compatible with UV-curable ink, however they are not recommended for outdoor applications due to their poor weather resistance.
When it comes to metal substrates, aluminum and stainless steel are both suitable for UV-curable ink. Aluminum is the preferred choice due to its low cost and excellent UV resistance, while stainless steel is better suited for applications where durability is required. Additionally, other metals such as brass and copper can also be printed with UV-curable ink, however they must be treated with a primer before application.
Wood is another suitable substrate for UV-curable ink, however it is important to note that wood is a porous material and therefore requires pre-treatment before application. Additionally, textiles such as cotton, polyester, and nylon are also suitable for UV-curable ink, however they must be pre-treated with a primer to ensure adhesion.
In general, UV-curable ink is a versatile and reliable ink for large format printing, with many different materials and substrates being suitable for use. However, it is important to note that the compatibility of different materials with UV-curable ink can vary greatly depending on the properties of the ink and the type of substrate. Therefore, it is important to test the compatibility of the ink and the substrate prior to application.
Influence of Material Surface Texture on UV-Curable Ink Adhesion
When using UV-curable ink on a variety of substrates, the surface texture of the substrate can have a significant impact on the adhesion of the ink. The surface texture of the substrate affects the amount of surface area that the ink has to adhere to, as well as the amount of surface tension that the ink has to overcome. For example, a substrate with a smooth surface texture will not provide as much surface area for the ink to adhere to as a substrate with a rough surface texture. Additionally, a substrate with a rough surface texture will create more tension for the ink to overcome, making it more difficult for the ink to adhere.
The best way to ensure a successful adhesion when using UV-curable ink on a variety of substrates is to match the surface texture of the substrate to the type of UV-curable ink being used. If the substrate has a smooth surface, a lower viscosity ink should be used. Similarly, if the substrate has a rough surface, a higher viscosity ink should be used. By taking the time to match the surface texture of the substrate to the viscosity of the ink, the adhesion of the ink will be greatly improved.
What types of materials or substrates are best suited for UV-Curable ink in large format printing? UV-Curable ink is best suited for substrates that are rigid, flat, and durable. Examples of such substrates include acrylic, aluminum, glass, polycarbonate, and PVC. The surface texture of the substrate will also impact the adhesion of the ink, so it is important to choose a substrate with a surface texture that is suited to the type of UV-curable ink being used. For substrates with a smooth surface, a lower viscosity ink should be used, and for substrates with a rough surface, a higher viscosity ink should be used.
UV-Curable Ink Performance on Various Plastic Substrates
UV-curable inks are a type of ink that require exposure to ultraviolet light to cure and form a strong bond with the substrate. This type of ink is often used in large format printing on a variety of surfaces, including plastic substrates. UV-curable inks are capable of printing on a wide range of plastic surfaces, including PVC, PET, polycarbonate, acrylic, and more. The performance of UV-curable inks on these plastic substrates varies depending on the specific material.
When printing on plastic substrates, it is important to consider the material’s surface texture. UV-curable inks perform best on smooth surfaces, as the ink can more easily adhere to the substrate. If the plastic surface is textured, the ink can become trapped in the ridges and crevices, resulting in an uneven finish. Additionally, the material’s color and opacity can affect the performance of the ink, as darker and more opaque colors can absorb UV light and slow down the curing process.
Overall, UV-curable inks are a great choice for large format printing on various plastic substrates. It is important to consider the material’s surface texture, color, and opacity to ensure the best results. Additionally, it is essential to follow best practices for using UV-curable ink on metal substrates, as the ink can be more difficult to adhere to this type of material.
Impact of Material Color and Opacity on UV-Curable Ink Performance
Material color and opacity can have a significant impact on the performance of UV-curable ink in large format printing. Darker colors, such as black, absorb more light energy, and therefore require more UV light exposure to cure the ink. On the other hand, lighter colors, such as white, reflect more light and require less UV light exposure to cure the ink. Additionally, the opacity of the material can also affect the curing time of the ink. A more opaque material can block UV light from reaching the ink and will require more time to cure.
When it comes to UV-curable ink, it is important to consider the color and opacity of the material in order to ensure that the ink is properly cured. This is especially true when printing on materials with darker colors or higher opacity. The best materials for UV-curable ink in large format printing are those that are light in color and have low opacity. This will allow the UV light to penetrate the material more easily and ensure that the ink is properly cured.
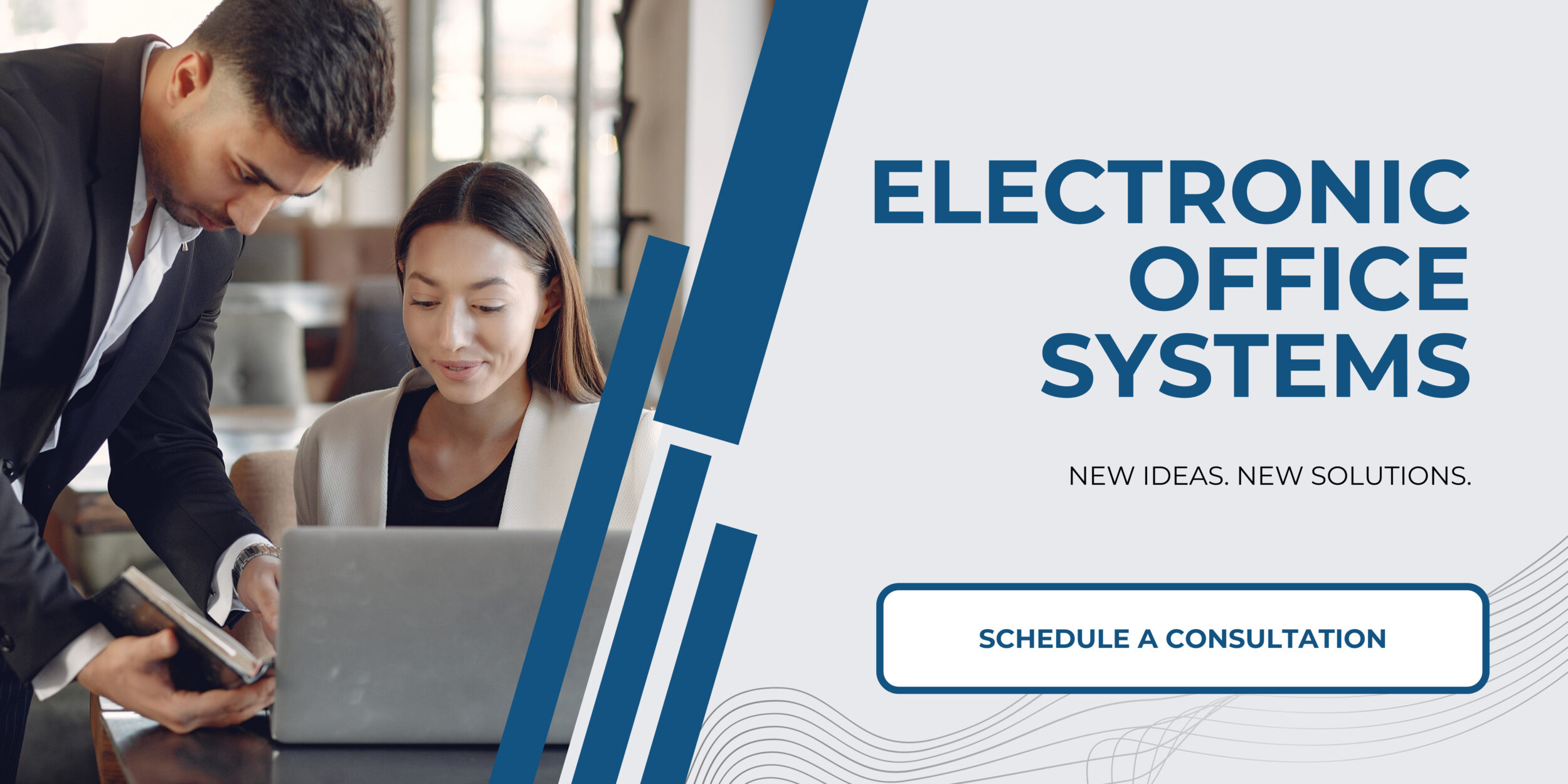
Best Practices for Using UV-Curable Ink on Metal Substrates
UV-curable ink is a popular choice for large format printing due to its ability to quickly produce high-quality prints. However, when using UV-curable ink on metal substrates, there are certain best practices to follow in order to ensure the best results. First and foremost, it is important to ensure that the substrate is properly prepped before printing. This includes cleaning the surface of any dirt and debris, as well as using a primer or other specialty coating to ensure proper adhesion. Additionally, it is important to use a low-tack adhesive tape or masking tape to secure the substrate to the printer bed.
When it comes to the types of metal substrates best suited for UV-curable ink, aluminum is one of the most popular options. This is because aluminum is lightweight, durable, and can provide excellent results when printed with UV-curable ink. Other metals such as stainless steel, brass, and copper can also be used, though it is important to note that different types of metals may require different types of coatings and adhesives to ensure proper adhesion.
Finally, it is important to note that the type of UV-curable ink used on a metal substrate will also have an impact on the quality of the printed image. In general, high-solids inks provide the best results on metal substrates, as they are designed to adhere well and provide excellent image quality. Additionally, it is important to use a UV-curable ink specifically designed for metal surfaces, as other types of UV-curable inks may not adhere properly or provide the desired results.