The printing process in a wide format printer is a complex and intricate one. The substrate, or material, that is printed on plays a major role in the success of this process. Substrate thickness affects the printing process in a wide format printer in a variety of ways.
When considering how substrate thickness affects the printing process, it is important to consider the type of printer being used. Different printers have vastly different capabilities when it comes to processing different thicknesses of substrate. Some printers are better suited for thinner materials, while others are designed to handle thicker substrates.
Substrate thickness also affects the speed of the printing process. Thicker substrates require more time to be printed on, as they require more heat to be applied. This can slow down the overall printing process. Additionally, thicker substrates require more ink to be applied, which can cause the ink to dry more slowly.
The printing resolution of a wide format printer is also affected by substrate thickness. Thicker substrates can cause the ink to spread more, resulting in a lower printing resolution. Additionally, the material can also cause the ink to fade more rapidly, resulting in a shorter lifespan for the printed product.
Finally, substrate thickness affects the cost of the printing process. Thicker substrates require more ink and more time to be printed on, resulting in a higher cost for the printed product.
In conclusion, substrate thickness plays an important role in the printing process in a wide format printer. It affects the speed, resolution, and cost of the printing process, and should be carefully considered when selecting a substrate for the job.
Impact of Substrate Thickness on Printer Adjustments and Settings
Substrate thickness is an important factor to consider when printing with a wide format printer. The thicker the substrate, the more adjustments must be made to the printer’s settings in order to achieve a quality print. If the substrate is too thick, it may not feed through the printer correctly, or it may cause jams due to the extra pressure needed to move the substrate through the printer’s rollers. Additionally, the printer settings must be adjusted to accommodate for the extra thickness of the substrate. This includes changing the print speed, resolution, and ink density to ensure that the quality of the print is not compromised.
The relationship between substrate thickness and print quality is also important to consider when printing with a wide format printer. Thicker substrates require more ink to create a saturated print. As a result, the ink consumption of a printer increases when printing with thicker substrates. This can be especially noticeable when printing with large format printers, as they tend to require higher volumes of ink for each print. Additionally, if the substrate is too thick, the printer may not be able to achieve the print quality desired, as the extra thickness of the substrate can cause the ink to spread unevenly.
Thicker substrates also have an impact on the paper handling and feeding process. Feeding thicker substrates into a printer can be difficult, as the extra thickness can cause the substrate to jam or not feed properly. Additionally, thicker substrates require more pressure to feed through the rollers, and this can cause the substrate to experience damage or wear and tear. To avoid this, it is important to ensure that the printer is properly adjusted to accommodate for the extra thickness of the substrate.
The effect of substrate thickness on printer maintenance and longevity is also an important factor to consider when printing with a wide format printer. Thicker substrates require more pressure to be fed through the printer, and this can cause wear and tear on printer components. This can lead to decreased printer performance and the need for more frequent maintenance and repairs. Additionally, the extra pressure needed to feed thicker substrates through the printer can cause jams more frequently, which can lead to additional maintenance costs.
Overall, substrate thickness is an important factor to consider when printing with a wide format printer. The thicker the substrate, the more adjustments must be made to the printer’s settings, and the more ink must be used to achieve a quality print. Additionally, thicker substrates can cause jams and damage to the printer, and they require more pressure to feed through the printer, which can lead to decreased printer performance and increased maintenance costs.
Relationship between Substrate Thickness and Print Quality
Substrate thickness plays an important role in the printing process when using a wide format printer. It affects the quality of the finished print, as different thicknesses require different printing settings. Thicker substrates require increased pressure on the print head, and an increase in the number of passes over the material in order to ensure an even spread of ink. If the pressure is too low, the resulting print may appear streaky or smudged. Conversely, if the pressure is too high, it can cause the substrate to buckle or warp, resulting in a poor quality print.
In addition, substrate thickness can have an effect on the color accuracy of a print. Thicker substrates absorb more ink, meaning that the colors will appear darker. Thinner substrates will require lighter ink settings in order to achieve the desired color. This is important to consider when printing on different types of materials, as the wrong settings can result in a final product that does not match the desired color.
The relationship between substrate thickness and print quality is an important one to consider when using a wide format printer. It is important to ensure that the correct settings are used to achieve the desired results, and that the substrate is able to handle the pressure from the print head. If the substrate is too thin, it may buckle or warp under the pressure, resulting in a poor quality print. If the substrate is too thick, it may require increased pressure, which can lead to smudging or streaking. Taking the time to adjust the settings and ensure the correct substrate thickness is the best way to achieve the highest quality prints.
Influence of Substrate Thickness on Ink Consumption
Substrate thickness plays a pivotal role in the amount of ink a wide format printer uses during the printing process. The thicker the substrate, the more ink is needed to achieve the desired outcome. This is because thicker ink layers are required to penetrate the substrate more deeply. As a result, thicker substrates require more ink to achieve the same level of coverage and vibrancy as thinner substrates. This can lead to higher ink costs over time. Additionally, thicker substrates can cause the printer to clog and require more frequent cleaning and maintenance.
Inkjet printers are designed to jet ink onto a substrate at a specific speed and with a specific amount of pressure. When a thicker substrate is used, the printer must work harder to penetrate the substrate. This requires more ink to achieve the same results as with a thinner substrate. In some cases, the printer may even require an adjustment of its settings in order to accommodate the thicker substrate.
The relationship between substrate thickness and ink consumption can also be seen in the drying time of the printed image. Thicker substrates take longer to dry, as the ink layers need more time to penetrate the substrate and adhere to it. This can lead to longer production times, which can be costly in terms of time and money.
Overall, substrate thickness can have a major impact on ink consumption in a wide format printer. Thicker substrates require more ink to achieve the same results as thinner substrates, and can also lead to longer production times. It is important to consider substrate thickness when selecting a printer and adjusting its settings in order to ensure the best results.
Role of Substrate Thickness in Paper Handling and Feeding
Substrate thickness plays an important role in paper handling and feeding when using a wide format printer. Substrate thickness is determined by the type and weight of the paper being used. For example, thicker substrates, such as cardboard, require more force to feed and handle than lighter weight papers. This can be problematic for wide format printers, as they need to be able to handle a wide range of substrate thicknesses in order to print quality images. The substrate thickness can also affect the speed of the printer, as thicker substrates require more force to feed and handle.
In terms of paper handling and feeding, substrate thickness can also affect the way the paper is loaded into the printer. Thicker substrates, such as cardboard, can be difficult to feed into the printer, as they require more force to be loaded properly. This can lead to jams, misfeeds, and other printer errors. To reduce these issues, the printer must be adjusted to the proper substrate thickness before beginning the printing process.
The substrate thickness can also affect the way the ink is applied to the paper. Thicker substrates require more ink to print properly, as they require more coverage. This can lead to increased ink consumption, as more ink must be used to achieve a higher quality print. To reduce ink consumption, the printer must be adjusted to the proper substrate thickness.
Overall, substrate thickness can have a significant effect on the paper handling and feeding process when using a wide format printer. Thicker substrates require more force to be loaded and handled properly, as well as more ink to be applied to the paper. To ensure quality prints, the printer must be adjusted to the proper substrate thickness before beginning the printing process.
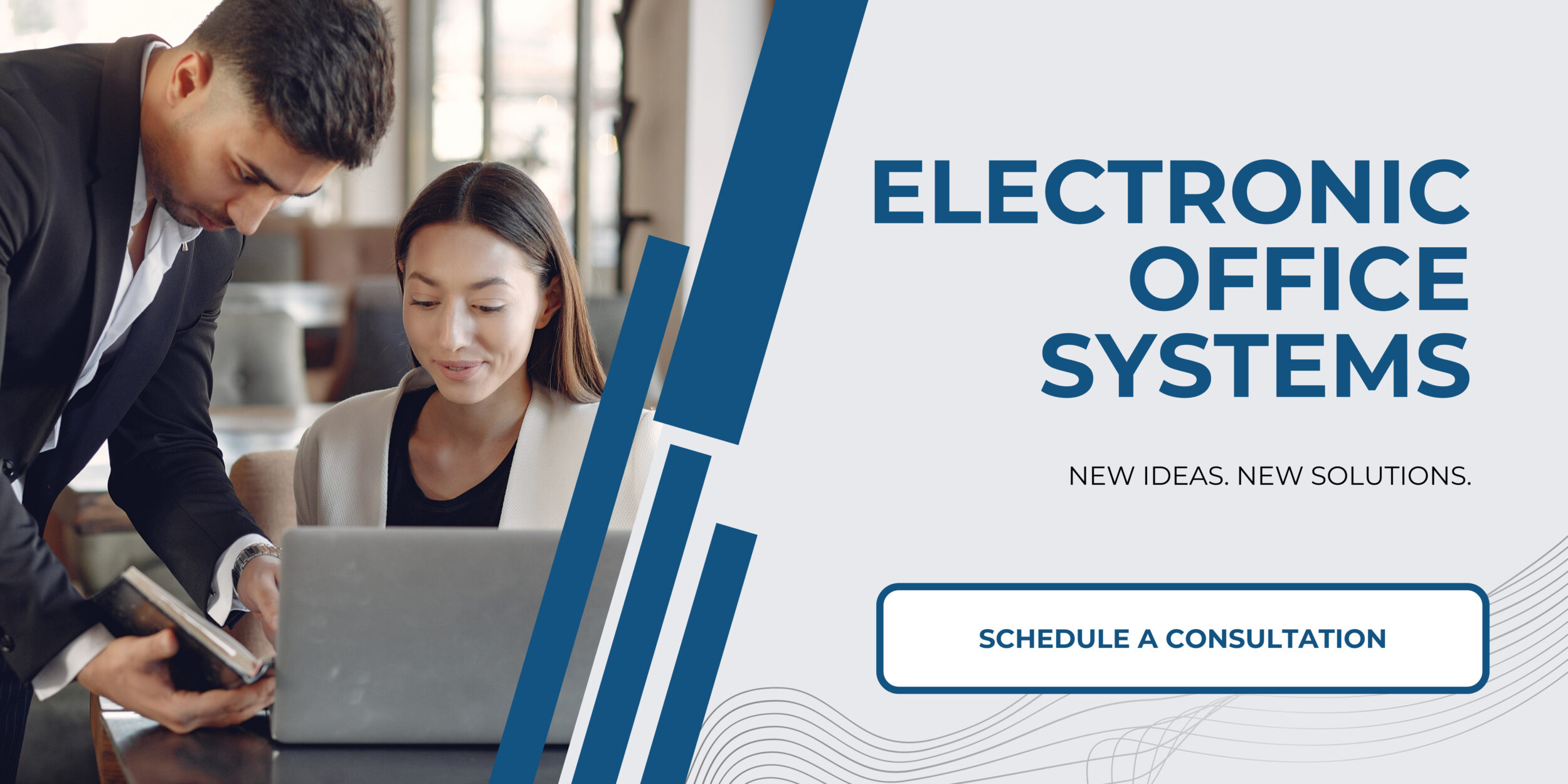
The Effect of Substrate Thickness on Printer Maintenance and Longevity
The substrate thickness of a wide format printer can have a significant impact on its maintenance and longevity. The thickness of the substrate affects the amount of pressure needed for the printer to properly feed and handle the paper. If the substrate is too thick, the pressure needed to feed the paper can be too great and cause damage to the printer. On the other hand, if the substrate is too thin, the printer may not be able to feed the paper properly. This can lead to jams and other issues. In addition, if the substrate is too thick it can cause wear and tear on the printer’s components over time, leading to decreased longevity.
The substrate thickness can also affect the maintenance of the printer. If the substrate is too thick, it can cause wear and tear on the printer’s components more quickly, leading to the need for more frequent maintenance. Printer maintenance can involve replacing parts and other adjustments, all of which can be expensive. If the substrate is too thin, the printer may not function properly, and again, require more frequent maintenance.
In conclusion, the substrate thickness of a wide format printer affects both its maintenance and longevity. If the substrate is too thick or too thin, it can cause wear and tear on the printer’s components, resulting in the need for more frequent maintenance. This can be costly and decrease the printer’s longevity. Therefore, it is important to select the correct substrate thickness to ensure the printer is as efficient and reliable as possible.