Operating a device at or near its duty cycle can have a significant impact on its performance and maintenance needs. The duty cycle of a device is an important parameter for any industrial operation, as it determines how long the device can be operated in a given period of time. Too much operation can cause the device to overheat, leading to poor performance and the need for more frequent maintenance. On the other hand, too little operation can cause the device to become inefficient, leading to decreased performance and increased maintenance needs. It is important to understand the impact that regularly operating a device at or near its duty cycle can have on its performance and maintenance needs, in order to ensure that the device is running optimally and efficiently.
In this article, we will explore the impact that regularly operating a device at or near its duty cycle can have on its performance and maintenance needs. We will look at how operating a device at or near its duty cycle can affect the device’s temperature, its power consumption, and its lifespan. We will also examine how operating a device at or near its duty cycle can impact its maintenance needs, as well as discuss some strategies for managing the device’s duty cycle. Finally, we will provide some tips for ensuring that the device is operating at its optimal performance level.
Potential Performance Impact
Operating a device at or near its Duty Cycle can have a variety of potential performance impacts. This could include a decrease in the device’s overall efficiency, a decrease in its accuracy or precision, or an increase in the amount of time it takes to complete a task. Additionally, it could result in an increase in the amount of energy the device consumes or a decrease in the quality of its output. For example, if a machine is running at or near its Duty Cycle, it may take longer to complete a task or produce an inferior product, both of which could result in lost time and money.
In addition, regularly operating a device at or near its Duty Cycle can cause wear and tear on the device’s parts and components. This can lead to a decrease in the device’s reliability or an increase in the number of maintenance issues that need to be addressed. Over time, this can result in a decrease in the device’s performance, as well as an increase in the number of repairs and replacements that need to be done.
Finally, if a device is operated at or near its Duty Cycle, it may be more prone to failure. This could be due to the stress placed on the device’s parts and components, as well as an increase in the amount of energy consumed. This could result in costly downtime and expensive repairs.
How might regularly operating a device at or near its Duty Cycle impact its performance and maintenance needs? Operating a device at or near its Duty Cycle can have a variety of negative impacts on its performance and maintenance needs. This includes a decrease in the device’s overall efficiency, a decrease in its accuracy or precision, an increase in the amount of energy consumed, an increase in the number of repairs and replacements, and an increase in the likelihood of failure. All of these factors can lead to increased operating costs and decreased productivity, which could ultimately result in a loss of time and money.
Potential Maintenance Impact
Operating a device at or near its Duty Cycle could result in a higher maintenance requirement. This is because the physical components of the device are put under more strain as they are used more frequently. In some cases, components may wear out faster due to increased usage and need to be replaced more often. Operating a device at or near its Duty Cycle could also mean that more frequent servicing is required to ensure that the device is running optimally. This could lead to increased maintenance costs in the long run. Additionally, if a device is not maintained properly, it could lead to further problems which may require more expensive repairs.
It is important to note that regularly operating a device at or near its Duty Cycle could also lead to an increase in the number of maintenance checks required to ensure that the device is running correctly. This is because the device may experience more wear and tear, meaning that it needs to be checked for any potential issues more often. This could be an additional expense that needs to be factored into the overall cost of running the device.
Finally, operating a device at or near its Duty Cycle could also lead to an increase in energy consumption. This is because the device is being used more frequently, meaning that it needs more energy to run. This could lead to higher energy bills in the long run.
Overall, regularly operating a device at or near its Duty Cycle can have an impact on its performance and maintenance needs. It could mean that components wear out more quickly, additional servicing is required more often, and more maintenance checks are necessary to ensure that the device is running optimally. It could also lead to an increase in energy consumption and higher energy bills. Therefore, it is important to weigh the potential costs and benefits of running a device at or near its Duty Cycle when making a decision.
Impact on Parts and Components
The impact on parts and components as a result of regularly operating a device at or near its Duty Cycle is significant. In order to ensure that the device continues to operate at peak performance, it is important to keep the parts and components in good condition. This includes replacing worn or damaged parts, lubricating moving parts, and ensuring that all connections are secure. Additionally, it is important to regularly inspect the device so any potential issues can be identified and addressed before they become more serious.
If a device is regularly operated at or near its Duty Cycle, it may require frequent replacement of parts and components due to wear and tear. Additionally, the device may require more frequent lubrication in order to maintain its performance. Additionally, any connections may need to be inspected and tightened to ensure that the device is operating at peak performance. All of these additional maintenance needs can result in an increase in operating costs over time.
Finally, it is important to note that operating a device at or near its Duty Cycle can also increase the likelihood of parts and components failing. This can be due to the increased wear and tear on the parts and components, as well as the increased strain on the device itself. If this occurs, it can lead to costly repairs or even the need to replace the entire device, which can significantly increase operating costs.
Preventive Maintenance and Monitoring
Preventive maintenance is the practice of scheduling and performing necessary maintenance to ensure that a device can continue to operate at its optimum performance. Regular maintenance helps detect and address potential problems before they become costly and irreversible. By regularly monitoring and maintaining a device, it is possible to extend its lifespan and reduce the number of repairs and replacements.
How might regularly operating a device at or near its Duty Cycle impact its performance and maintenance needs? Operating a device at or near its Duty Cycle can put additional strain on the device, reducing its overall performance. Additional strain can also cause the device to require more frequent maintenance and repairs, as parts and components may be more likely to become worn or damaged due to the increased use and stress. It is important to consider the Duty Cycle of a device when determining the frequency of preventive maintenance and monitoring. This will help to ensure that the device is able to perform at its optimum level and that any potential issues are addressed quickly and effectively.
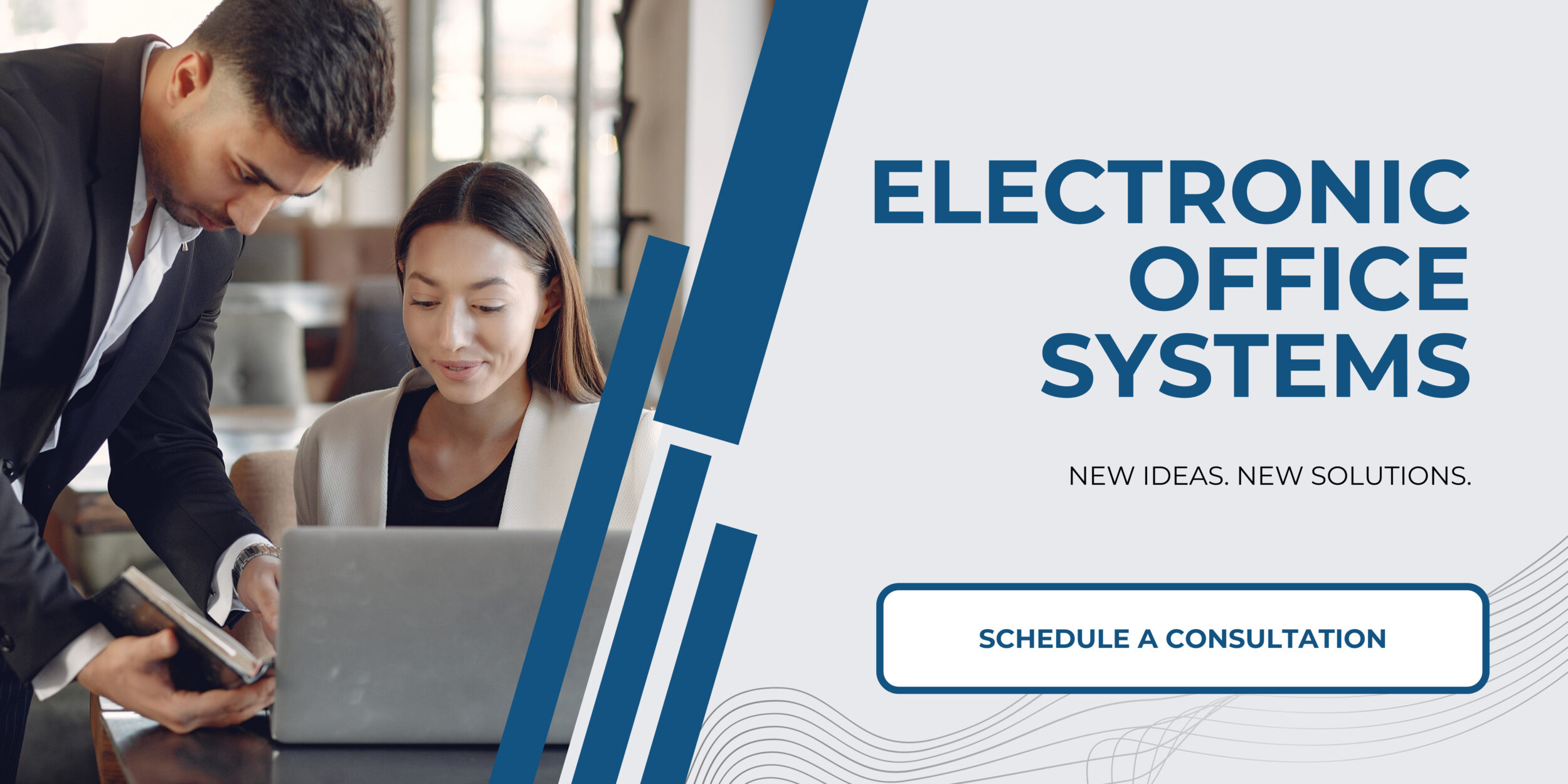
Impact on Operating Costs
Operating costs are an important factor to consider when evaluating the performance and maintenance needs of a device. Operating costs can be impacted by a device’s duty cycle, which is the amount of time the device is in use as a percentage of the total time available. If a device is regularly operating at or near its duty cycle, it can result in increased wear and tear on the device, leading to higher operating costs. For example, if a device is regularly operating at 80% of its duty cycle, it will need to be replaced or repaired more often, leading to additional costs. Additionally, if a device is regularly operating at or near its duty cycle, it may require additional energy to keep the device running, resulting in increased operating costs.
Furthermore, operating at or near a device’s duty cycle can lead to decreased efficiency and increased downtime, as the device is being used more frequently than it was designed for. This can lead to decreased productivity, as well as increased costs associated with repairs, replacement parts, and service calls. Additionally, if a device is not properly maintained, it can lead to additional costs related to both performance and maintenance, as the device will need to be serviced or replaced more often.
Overall, operating a device at or near its duty cycle can have a significant impact on a device’s operating costs, as increased wear and tear, as well as additional energy and maintenance costs, can add up quickly. To minimize the impact of operating at or near a device’s duty cycle, it is important to ensure that the device is regularly maintained and serviced to keep it running at peak performance. Additionally, operating a device at or near its duty cycle should be used as a last resort, as it can lead to costly repairs and replacements.